- FMA
- The Fabricator
- FABTECH
- Canadian Metalworking
Categories
- Additive Manufacturing
- Aluminum Welding
- Arc Welding
- Assembly and Joining
- Automation and Robotics
- Bending and Forming
- Consumables
- Cutting and Weld Prep
- Electric Vehicles
- En Español
- Finishing
- Hydroforming
- Laser Cutting
- Laser Welding
- Machining
- Manufacturing Software
- Materials Handling
- Metals/Materials
- Oxyfuel Cutting
- Plasma Cutting
- Power Tools
- Punching and Other Holemaking
- Roll Forming
- Safety
- Sawing
- Shearing
- Shop Management
- Testing and Measuring
- Tube and Pipe Fabrication
- Tube and Pipe Production
- Waterjet Cutting
Industry Directory
Webcasts
Podcasts
FAB 40
Advertise
Subscribe
Account Login
Search
Looking for an alternative to conventional swaging?
Internal elastomeric swaging handles some niche applications
- By Eric Lundin and Trish Harbaugh
- July 2, 2012
- Article
- Tube and Pipe Fabrication
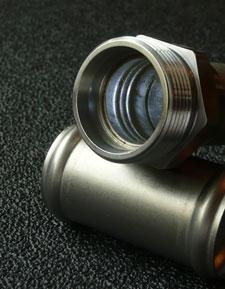
Elastomeric swaging is suitable for applications such as a three-groove swaged fitting (top) and beads (bottom).
If you’re familiar with internal swaging, you know you have a couple of choices to perform the operation. Conventional processes use a hard tool that expands or rotates inside the tube to make a predetermined form. A little-known process, elastomeric swaging, is another choice. It uses a flexible tool to bulge-form the tube or pipe. Depending on your application, elastomeric swaging can be a good fit.
Patented for military aircraft use in the late 1970s, internal elastomeric swaging is a cold-forming process. The linear travel of a high-strength drawbolt compresses an elastomeric expander against a static split ring that surrounds the drawbolt (see Figure 1 and Figure 2).
The process has two distinct uses. First, it can expand the tube or pipe into a fitting. During the swaging cycle, the tooling develops a high radial force that displaces the tube wall, expanding it into the grooves of the external connector. When complete, this process creates a work-hardened double layer of material. Second, it can be used to create forms such as beads (see Lead Image).
The internal elastomeric swaging process uses constant pressure, so it doesn’t cause local stress concentrations; because of this, it doesn’t result in distortion, wall thinning, and strength loss of the tube or fitting. Regarding inspection, an elastomerically swaged assembly needs only visual and dimensional inspection, externally and internally. Because the process simply moves the metal, it doesn’t introduce subsurface inclusions or other flaws, and therefore doesn’t require radiographic or ultrasonic inspection.
It is useful for swaging tube and pipe made from the manufacturing industry’s most common material—steel—and it’s also suitable for stainless steels, aluminum, titanium, and INCONEL® alloys.
Which Niche?
Conventional end forming may be the best choice for many applications; in other cases, welding or brazing a connector onto a length of tubing is the best option. However, elastomeric swaging can fill a niche in which conventional methods produce less-than-satisfactory results. While it can be used for low-pressure applications up to about 3 in. diameter, such as ductwork, its characteristics make it a strong contender for small-diameter, high-pressure applications.
- Diameter. Welding and brazing are difficult on small diameters. Elastomeric swaging is often used on tube or pipe from ¼ to 1 ½ in. dia.
- Pressure. Because the tube is formed to fit the connector, rather than attached to the connector, the elastomeric swaging doesn’t provide a leak path. This is critical for high-pressure applications; elastomeric swaging handles pressures up to 5,000 pounds per square inch.
- Vibration. The vibrations and shocks on lines and systems used in transportation equipment eventually weaken the bonds that join parts in an assembly. A formed end with the correct fitting type provides a durable joint that withstands vibrations and minor shock loads.
- Hardness. Some materials are so hard that they are prone to cracking when worked with hard tooling. Elastomeric tooling can be a good option for several reasons. Elastomeric tooling is soft, so it doesn’t disturb the surface of the workpiece; it expands slowly, which gives the tubing material time to react to the radial force; and it distributes the force evenly, so the material forms evenly.
- Radius. In some cases, a tube is designed with a radius that is too tight to be swaged economically. Rather than resort to an expensive option, such as swaging it progressively with several sets of tools, elastomeric swaging can handle a tight radius readily and inexpensively.
- Dissimilar Metals. The welding industry continues to make progress in joining dissimilar metals, but doing so successfully usually requires specialized training, great care, and some compromises. Elastomeric swaging works on dissimilar metals without concern for metal bonding.
The Expanding Role of Elastomeric Swaging
“This process is most commonly used on sizes smaller than 1½ inch,” said Joe Fortin, an aircraft industry veteran. A retired machine rebuild specialist at The Boeing Co. for 28 years, Fortin has specialized in tube forming processes for many years.
“When applied to two- and three-groove fittings, this double-walled construction provides a strong, leakproof mechanical attachment for fluidtight connections,” he said. “It makes a robust connection that stands up to vibration, which makes it suitable for many aircraft applications. Aircraft use many tubing connections that are 3/8 to ½ in. in diameter and have pressures from 3,000 to 5,000 pounds per square inch, and this process works well for these applications.”
Elastomeric swaging also eliminates some of the risks associated with other methods. For example, welding requires great care to prevent tungsten inclusions and hydrogen embrittlement. Likewise, roller swaging tooling must be cleaned thoroughly when switching from one material to another to prevent contamination. If the tooling picks up tiny particles of steel during one production run, some of this material might get transferred to aluminum workpieces during a subsequent run, potentially contaminating the entire lot.
The key to the elastomeric swaging process is the tooling. Elastomers are dense and don’t compress much. When the drawbolt squeezes the material laterally, it reacts by expanding radially with substantial force.
“For one aircraft project, I tested elastomeric swaging on some lengths of small-diameter tubing with 0.070 wall thickness,” Fortin said. “This material was so thick that it couldn’t be orbital welded because the heat didn’t penetrate the wall thoroughly, resulting in partial welds. However, after the evaluation, we recognized the potential of elastomeric swaging.”
The characteristics that make it work well for aircraft make it a good option for nearly any application that uses fluids under pressure, such as transportation, heavy equipment, military, marine, and refrigeration. This process can be used for air lines, low-pressure water lines, electrical conduit, and wastewater handling systems.
About the Authors
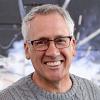
Eric Lundin
2135 Point Blvd
Elgin, IL 60123
815-227-8262
Eric Lundin worked on The Tube & Pipe Journal from 2000 to 2022.
Trish Harbaugh
Vice President
6010 S. 39th Place
Rogers, AR 72758
479-202-0039
About the Publication
subscribe now
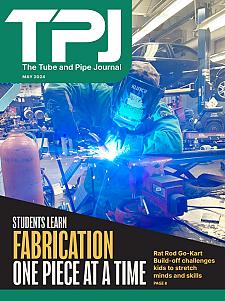
The Tube and Pipe Journal became the first magazine dedicated to serving the metal tube and pipe industry in 1990. Today, it remains the only North American publication devoted to this industry, and it has become the most trusted source of information for tube and pipe professionals.
start your free subscription- Stay connected from anywhere
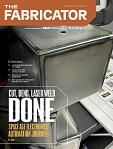
Easily access valuable industry resources now with full access to the digital edition of The Fabricator.
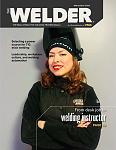
Easily access valuable industry resources now with full access to the digital edition of The Welder.
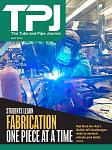
Easily access valuable industry resources now with full access to the digital edition of The Tube and Pipe Journal.
- Podcasting
- Podcast:
- The Fabricator Podcast
- Published:
- 04/16/2024
- Running Time:
- 63:29
In this episode of The Fabricator Podcast, Caleb Chamberlain, co-founder and CEO of OSH Cut, discusses his company’s...
- Trending Articles
Zekelman Industries to invest $120 million in Arkansas expansion
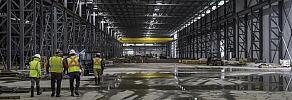
3D laser tube cutting system available in 3, 4, or 5 kW
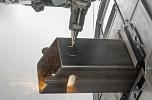
Corrosion-inhibiting coating can be peeled off after use
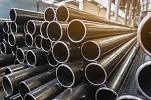
Brushless copper tubing cutter adjusts to ODs up to 2-1/8 in.
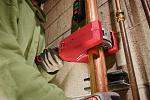
HGG Profiling Equipment names area sales manager
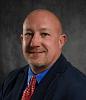
- Industry Events
16th Annual Safety Conference
- April 30 - May 1, 2024
- Elgin,
Pipe and Tube Conference
- May 21 - 22, 2024
- Omaha, NE
World-Class Roll Forming Workshop
- June 5 - 6, 2024
- Louisville, KY
Advanced Laser Application Workshop
- June 25 - 27, 2024
- Novi, MI