President
- FMA
- The Fabricator
- FABTECH
- Canadian Metalworking
Categories
- Additive Manufacturing
- Aluminum Welding
- Arc Welding
- Assembly and Joining
- Automation and Robotics
- Bending and Forming
- Consumables
- Cutting and Weld Prep
- Electric Vehicles
- En Español
- Finishing
- Hydroforming
- Laser Cutting
- Laser Welding
- Machining
- Manufacturing Software
- Materials Handling
- Metals/Materials
- Oxyfuel Cutting
- Plasma Cutting
- Power Tools
- Punching and Other Holemaking
- Roll Forming
- Safety
- Sawing
- Shearing
- Shop Management
- Testing and Measuring
- Tube and Pipe Fabrication
- Tube and Pipe Production
- Waterjet Cutting
Industry Directory
Webcasts
Podcasts
FAB 40
Advertise
Subscribe
Account Login
Search
Bending tube without marring the surface
Plastic tooling prevents abrasions, markings, and scratches on metal tubing
- By Mike Thomas
- May 4, 2021
- Article
- Tube and Pipe Fabrication
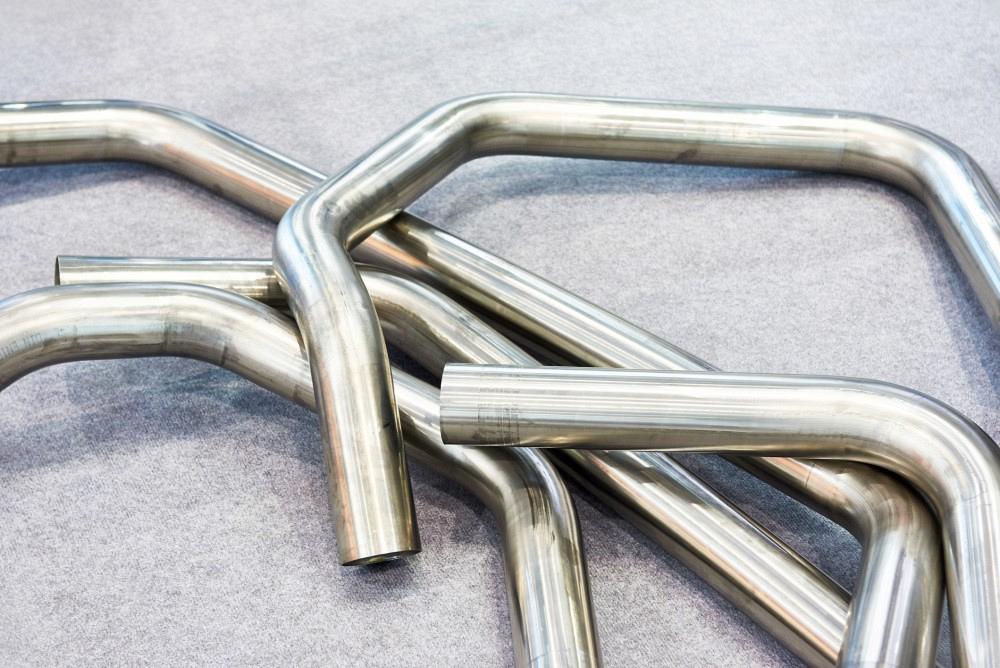
Some challenging bending applications can result in marring the tube’s surface. The tooling is metal, the tubing is metal, and in some cases abrasions or scratches are unavoidable. Getty Images
For many tube fabrication applications, making a successful bend is straightforward, especially when using one of the latest rotary draw benders. A full set of tooling—bend die, wiper die, clamp die, pressure die, and mandrel—surrounds and restricts the tube along the inner and outer surfaces, so that during the bending process, the metal flows where it is intended to flow. This, combined with a modern control system, can provide excellent results for simple to moderately difficult bends. It’s not foolproof, in that success also requires proper setup and lubrication, but in many cases, the result is a good bend, time after time, shift after shift, day after day.
When presented with a challenging bend, fabricators have a few options. Some rotary draw machines have a carriage boost feature, providing a pushing force to assist the drawing force. Beyond this, toolmakers usually have a strategy or two for handling difficult bends, for example by increasing the length of the clamp die or machining a series of serrations into the clamp die’s contact surface. A longer clamp die develops more friction; serrations bite into the tube’s surface. Both provide additional grip to prevent the tube from slipping during the bending process.
Regardless of the specifics, the goal is to produce a component that meets the customer’s requirements. For the most part, this means a component that has little distortion and a smooth surface. However, this isn’t ironclad. For a tube that will be hidden from view, the customer might tolerate quite a bit of ovality on a round tube, substantial flattening of a square or rectangular tube, slight to moderate wrinkling along the inside of the bend, or tooling marks. Most of these can be quantified as a percentage of deviation from an ideal bend, so it’s a matter of finding out what the customer really wants. Some are willing to pay quite a bit for a pristine bend, while others prefer a much less expensive bend with notable imperfections.
Once in a while a customer specifies a bend that doesn’t seem too difficult to produce, one made from a moderately soft material with just enough wall thickness to stretch along the outside of the bend without splitting, but not so much that it bunches up along the inside of the bend. Initially it looks like an easy bend, but then the customer reveals one last criteria: no marking. The application is aesthetic so the customer won’t tolerate any marring from the tooling at all.
If a test bend results in tooling marks, the fabricator has two options. One is to employ an extra step to polish the finished piece to remove all tooling marks. Certainly polishing can be carried out successfully, but it means additional handling and more work, so it’s not necessarily an inexpensive option.
A second option is to use no-mar tooling.
Materials and Construction for No-mar Tooling
Eliminating marring is a matter of eliminating steel tooling surfaces. This is done by making tooling entirely from a heavy-duty synthetic polymer or by making tooling inserts from these materials.
Both strategies depart from convention; bender tooling usually is made from a metal alloy only. Few other materials can withstand the bending forces and form the tube or pipe, and the ones that can usually aren’t very durable. However, two of these plastics have emerged as commonly used materials for this application: Derlin and Nylatron. While these materials have excellent compressive strength, they aren’t nearly as hard as tool steel, which is why they leave no marks. They also have some natural lubricity. Because of these two factors, no-mar tooling is rarely a direct replacement for standard tooling.
Because polymer tooling doesn’t develop as much friction as steel tooling, the part being formed usually needs a more generous bend radius and a design that supports a longer clamp die than components designed for metal tooling. A lubricant still is necessary, although usually in small quantities. A water-based lubricant is the best bet to prevent a chemical reaction between the lubricant and the tooling.
While all tooling has a finite service life, no-mar tooling has a shorter service life than conventional tooling. This is a critical consideration when quoting such a job because the tooling must be replaced more frequently. This frequency can be reduced by using polymer inserts attached to steel tooling bodies with mechanical fasteners, which often last longer than tooling made entirely from polymers.
Applications for No-mar Tooling
No-mar tooling is suitable for forming steel, stainless steel, aluminum, and copper, and the typical applications are as varied as the materials. Food and beverage applications are ideal for no-mar tooling. Pipe destined for food or beverage processing ideally is perfectly smooth. Any scratches, dents, or scrapes left on the tube or pipe’s surface can collect debris and become a breeding ground for bacteria.
Other common applications include coated or plated parts. A common misconception is that the coating or plating process fills in or covers up imperfections. Coating and plating layers are extremely thin, and often the goal is a highly reflective, glossy finish. This sort of surface accentuates, rather than obscures, surface blemishes, so a preventive measure is necessary.
About the Author
Mike Thomas
435 Roske Drive
Elkhart, IN, 46516
574-295-5041
About the Publication
Related Companies
subscribe now
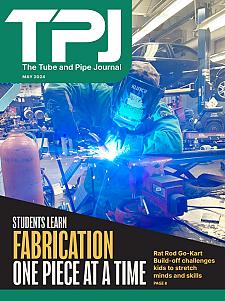
The Tube and Pipe Journal became the first magazine dedicated to serving the metal tube and pipe industry in 1990. Today, it remains the only North American publication devoted to this industry, and it has become the most trusted source of information for tube and pipe professionals.
start your free subscription- Stay connected from anywhere
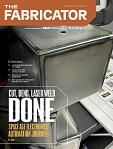
Easily access valuable industry resources now with full access to the digital edition of The Fabricator.
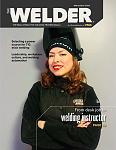
Easily access valuable industry resources now with full access to the digital edition of The Welder.
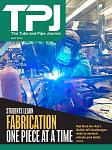
Easily access valuable industry resources now with full access to the digital edition of The Tube and Pipe Journal.
- Podcasting
- Podcast:
- The Fabricator Podcast
- Published:
- 04/16/2024
- Running Time:
- 63:29
In this episode of The Fabricator Podcast, Caleb Chamberlain, co-founder and CEO of OSH Cut, discusses his company’s...
- Trending Articles
Zekelman Industries to invest $120 million in Arkansas expansion
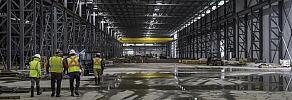
3D laser tube cutting system available in 3, 4, or 5 kW
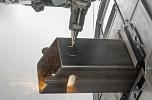
Corrosion-inhibiting coating can be peeled off after use
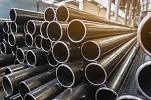
Brushless copper tubing cutter adjusts to ODs up to 2-1/8 in.
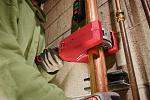
HGG Profiling Equipment names area sales manager
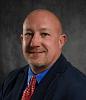
- Industry Events
16th Annual Safety Conference
- April 30 - May 1, 2024
- Elgin,
Pipe and Tube Conference
- May 21 - 22, 2024
- Omaha, NE
World-Class Roll Forming Workshop
- June 5 - 6, 2024
- Louisville, KY
Advanced Laser Application Workshop
- June 25 - 27, 2024
- Novi, MI