- FMA
- The Fabricator
- FABTECH
- Canadian Metalworking
Categories
- Additive Manufacturing
- Aluminum Welding
- Arc Welding
- Assembly and Joining
- Automation and Robotics
- Bending and Forming
- Consumables
- Cutting and Weld Prep
- Electric Vehicles
- En Español
- Finishing
- Hydroforming
- Laser Cutting
- Laser Welding
- Machining
- Manufacturing Software
- Materials Handling
- Metals/Materials
- Oxyfuel Cutting
- Plasma Cutting
- Power Tools
- Punching and Other Holemaking
- Roll Forming
- Safety
- Sawing
- Shearing
- Shop Management
- Testing and Measuring
- Tube and Pipe Fabrication
- Tube and Pipe Production
- Waterjet Cutting
Industry Directory
Webcasts
Podcasts
FAB 40
Advertise
Subscribe
Account Login
Search
Distillery fabricator makes collars to speed manifold-making process
T-making tool eases tube-to-tube alignment, cutting, welding processes
- By Eric Lundin
- January 12, 2021
- Article
- Tube and Pipe Fabrication
Since the process of distillation was first developed, mankind has had more than 3,000 years to update and refine it. At its simplest, it uses a vessel such as a copper pot, a heat source, and a condenser that captures and cools the vapor that escapes from the pot. Called batch distillation, this process separates the contents of the pot based on their specific boiling points. When the process is finished, the distiller empties and cleans the pot, rinses the condenser, and starts over.
Initially used for making perfume, the process has been used for distilling water for at least 2,000 years and was critical in the practice of alchemy, the foundation of modern chemistry. Of course it’s also used for distilling alcohol (specifically, ethanol) from fermented sugars to increase its purity.
Closely related is continuous distillation, which is carried out in column stills rather than pot stills. Entrepreneur Steve Marasco used the continuous distillation concept to develop a column still design he markets under the brand name “Hillbilly Stills” in Kentucky. The staff in his shop recently came across a way to cut down the time needed to fabricate them.
Traditional Distilling
For traditional batch distilling, the distillery comprises a pot or a kettle, usually custom-made for this purpose, outfitted with a top. Protruding from the top is a pipe that runs straight up, then pitches slightly downward to a second vessel used for collection. As the evaporate cools in the pipe, it condenses and turns into a liquid. Gravity causes it to flow out of the condenser into a collection vessel.
Creating alcohol revolves around yeasts, approximately 1,500 species that belong to the fungus family. The yeast devours sugar and secretes two waste products: carbon dioxide and alcohol. The fermenting process starts when the distiller fills a container with a food that has quite a bit of sugar or starch content (fruit, potatoes, rye, and so on) and adds yeast. The yeast begins to feast on the sugar content; as time goes on, alcohol builds up, thereby making the environment in the container progressively more toxic. When the yeast is overcome, it dies, and the process comes to a halt.
“Bread yeast can tolerate alcohol until the concentration gets up to about 8%,” Marasco said. Other species can tolerate much higher concentrations. “Some yeasts can live in an environment of about 20% alcohol.”
The distiller puts the mash into the pot and fires up the burner. When the temperature gets to 173.1 degrees F, the alcohol begins to boil, condense, and drain into the collection vessel.
As the name implies, a column still is a vertical pipe. The setup is quite a bit different from that of a pot still in that heating, evaporation, and condensing take place in a single vessel—it doesn’t have a separate condenser. It contains a series of plates arranged vertically and is laid out for a continuous input of the feedstock. This input takes place through a port about halfway up the column, and as the mash flows downward from plate to plate, it cools as it goes. The mash encounters steam traveling upward, which causes the alcohol to evaporate.
Marasco’s design is a water-cooled setup that uses two tubes, one inside the other, with a jacket between the two.
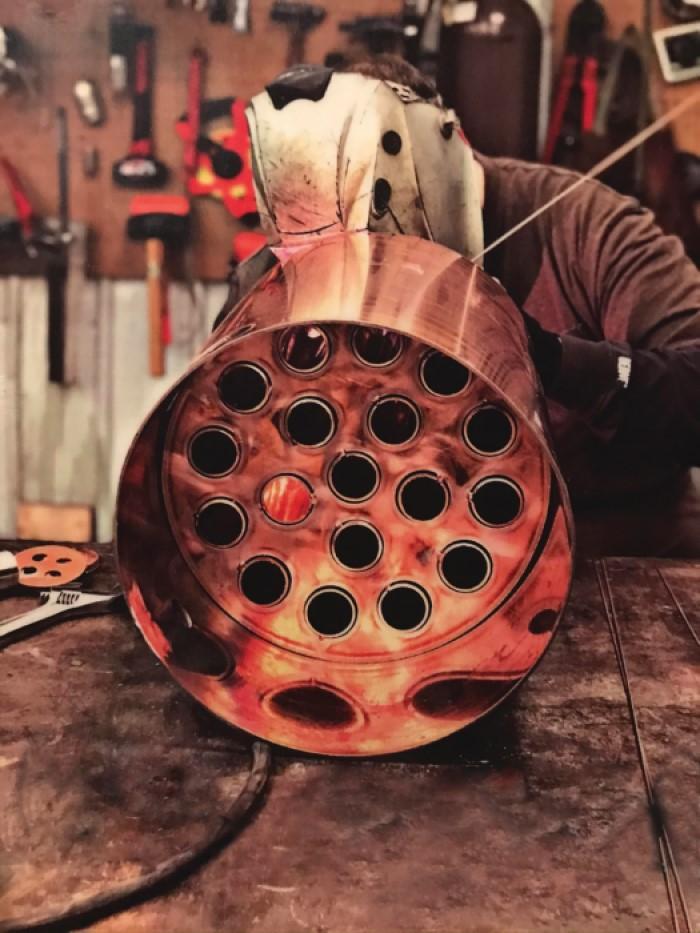
Building a column still relies on a lot of gas tungsten arc welding. The two main processes are making ports for sight glasses and tube-to-tubesheet welding.
Traditional Manifold Construction
Anyone who has ever built more than a couple of manifolds using common shop tools can tell you that it’s absolutely the most time-consuming and frustrating task in all of metal fabrication. No good way exists for making a series of 90-degree intersections to join a main pipe to a succession of laterals. A well-executed joint is actually 90 degrees on two axes, both vertical and horizontal, and just a bit of an offset is easy to spot. Even when the fitter gets the pipes aligned properly, the joint rarely has a constant gap, so the welder has to compensate for a varying gap width.
Many concepts have been tried, and many are reasonably helpful. Browsing a web site or two (especially YouTube) for just a few minutes yields a few strategies involving templates and homemade jigs, demonstrating how to mark and cope the pipe and how to fixture the main to the lateral. Browsing through the booths at an industrial tradeshow such as FABTECH can be a better option for finding purpose-built jigs, considering that it’s rich in welding technology. However, many fitters don’t have a purpose-built jig, so they’re left with intuition, shop tools, and a bit of trial-and-error on each joint they make.
Like other fabricators, pipefitters, and welders, Marasco’s team struggled with this. On a column still, a conventional design feature is a series of pilot glasses or sight glasses, windows that run along the length of the column. Drilling, cutting, coping, grinding, and fitting the tubes for the sight glasses was a vexing problem.
“It was difficult to be precise,” Marasco said.
One of T-Drill’s applications engineers, Dylan Howell, learned about Marasco’s application and suggested creating a series of outlets along the column for affixing the tubes for the pilot glasses. T-Drill’s forte is a process by which a rotating tool drills through the wall of a copper pipe and creates a collar. After drilling the pilot hole and allowing the tool to stop, the operator rotates the tool’s chuck counterclockwise to deploy two pins that extend from the bit; the operator starts the tool again and slowly retracts it; as the tool retracts, it performs a spinning and pulling process, forcing some of the copper to flow from the pipe’s wall to form a T joint. Marasco thought it would work.
“Not only did Dylan know his business, but he knew mine,” Marasco said.
Marasco took delivery of a T-drill model T-65b, a battery-powered hand-held tool, showed it to his employees, and went about running his several other businesses. Only some time later, when Howell called to check in, did Marasco learn that his employees hadn’t yet started to use it. They had thought that the unit had come with the wrong tooling sizes.
“It took Dylan about a minute to explain how to use it,” Marasco said.
The explanation was a revelation, as the new process has almost nothing in common with the old process. Planning and marking the locations of the holes for the sight glass tubes was painstaking at best; it could take an entire day to get everything planned, marked, cut, coped, located, and fixtured so that the sight glass tubes were evenly spaced and properly aligned to prevent interference with the plates inside the main tube.
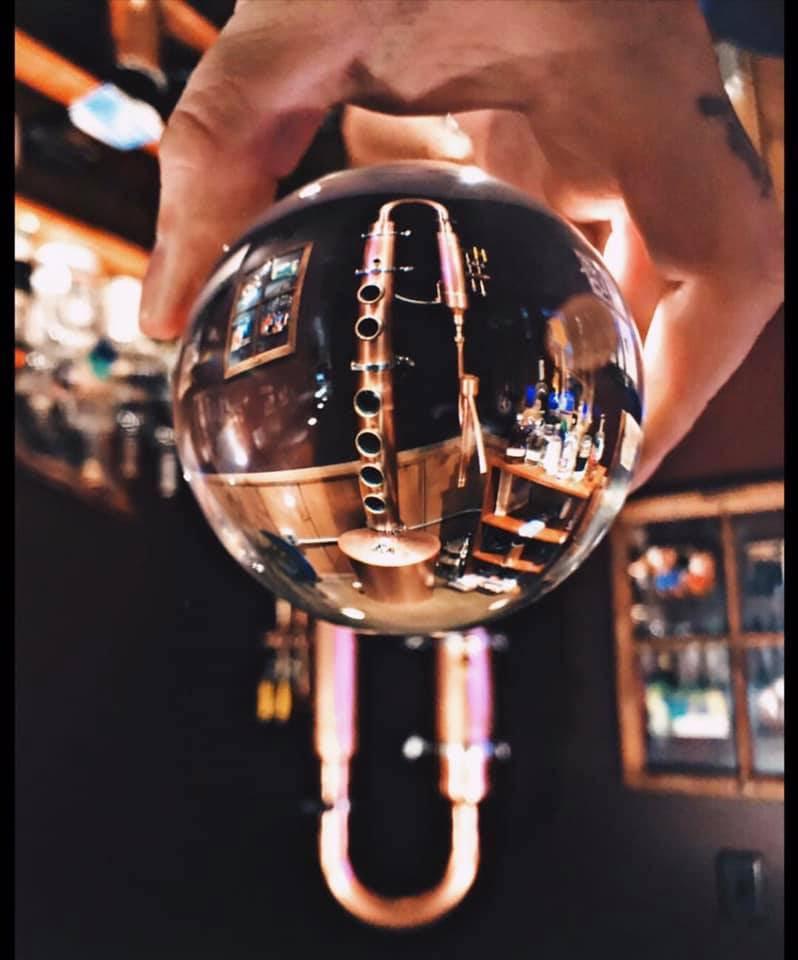
A perfectly aligned row of sight glasses, as seen through a sight glass, highlights the accuracy of using a collar-pulling unit to make a manifold from copper tube.
Using the new process, marking all of the collar locations takes just a few seconds; making each collar takes just a minute or two; and rework is nonexistent because every collar protrudes from the main tube as it should, at a 90-degree angle whether viewed from the top or the side. Using the old method, the stills looked good, but now they look better. Assembly is not only faster, but easier.
“The components go together like snapping Legos together,” Marasco said.
Furthermore, using the collaring method to build the still provides a cleaner environment for distilling.
“The stills have fewer nooks and crannies where material can accumulate and bacteria can grow,” Marasco said. This wasn’t necessarily a problem with the old stills—any dedicated distiller can clean a unit—but with fewer hiding places for debris, the new units can be cleaned much faster.
Ready to Join the Separating Community?
Brewing at home can be a good way to make an authentic, quality beverage. To hear Marasco tell it, some “authentic’ and “quality” beverages are available at every price point, but so are many less-than-authentic, average-quality beverages. In his opinion, the market is saturated overpriced beverages hawked with marketing tactics that are slightly ridiculous at best and downright underhanded at worst.
“Look at the shapes of the bottles and the price tags,” he said. “Fancier bottles and higher price tags go hand in hand.” In his opinion, sky-high prices have little, if anything, to do with the contents. “Some expensive bourbons are very good, but it’s hard to justify paying $500 for one bottle,” he said.
A popular trend in beer fares no better in his view. “If you’re going to be a success in selling India pale ale, you need a silly name,” he said.
One particularly unscrupulous spirits vendor, which Marasco doesn’t name, purchases wholesale quantities of grain alcohol, trucks it to a location deep in the heart of the Appalachian region—a traditional center of moonshining expertise—and pumps it through a still so it can label the product “Distilled in Appalachia.”
Marasco thinks that the industry will experience a big influx of new brand names in the next couple of years.
“Nearly everyone in the moonshine business has started barreling everything they have,” he said. “In two years, we’ll probably see thousands of new ones on the market.” Some will be bona fide products made by distillers that respect the heritage, and some will be so-so products marketed by companies interested in little more than profit, leaning hard on fancy labels, pretty pictures, and unjustifiable prices.
Does this mean you should buy a still and make your own moonshine? Marasco can’t recommend that because, when operated legally, an alcohol distilling operation is not economically viable.
“Beer is taxed at $18 a barrel,” he said. Traded in 31-gallon barrels, that works out to 58 cents per gallon. Not too bad. “Wine is taxed at $3.40 per gallon,” he continued. That’s bad, and it gets a lot worse. “Liquor is taxed at $13.50 a gallon.” Hence the only charge that stuck to one of the most famous black-market liquor distributors of all time, Al Capone: tax evasion.
Liquor aside, if you want to make your own perfumes or distill your own water, Marasco’s company can set you up with a beautiful vertical copper still.
About the Author
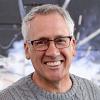
Eric Lundin
2135 Point Blvd
Elgin, IL 60123
815-227-8262
Eric Lundin worked on The Tube & Pipe Journal from 2000 to 2022.
About the Publication
subscribe now
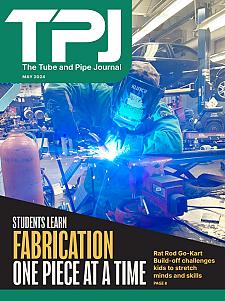
The Tube and Pipe Journal became the first magazine dedicated to serving the metal tube and pipe industry in 1990. Today, it remains the only North American publication devoted to this industry, and it has become the most trusted source of information for tube and pipe professionals.
start your free subscription- Stay connected from anywhere
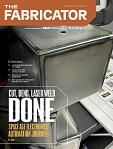
Easily access valuable industry resources now with full access to the digital edition of The Fabricator.
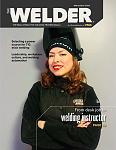
Easily access valuable industry resources now with full access to the digital edition of The Welder.
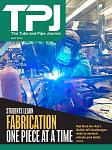
Easily access valuable industry resources now with full access to the digital edition of The Tube and Pipe Journal.
- Podcasting
- Podcast:
- The Fabricator Podcast
- Published:
- 04/16/2024
- Running Time:
- 63:29
In this episode of The Fabricator Podcast, Caleb Chamberlain, co-founder and CEO of OSH Cut, discusses his company’s...
- Trending Articles
Zekelman Industries to invest $120 million in Arkansas expansion
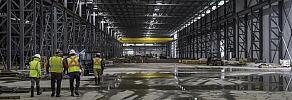
3D laser tube cutting system available in 3, 4, or 5 kW
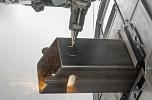
Corrosion-inhibiting coating can be peeled off after use
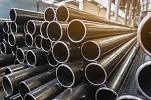
Brushless copper tubing cutter adjusts to ODs up to 2-1/8 in.
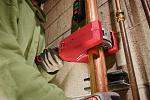
HGG Profiling Equipment names area sales manager
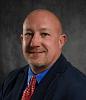
- Industry Events
16th Annual Safety Conference
- April 30 - May 1, 2024
- Elgin,
Pipe and Tube Conference
- May 21 - 22, 2024
- Omaha, NE
World-Class Roll Forming Workshop
- June 5 - 6, 2024
- Louisville, KY
Advanced Laser Application Workshop
- June 25 - 27, 2024
- Novi, MI