- FMA
- The Fabricator
- FABTECH
- Canadian Metalworking
Categories
- Additive Manufacturing
- Aluminum Welding
- Arc Welding
- Assembly and Joining
- Automation and Robotics
- Bending and Forming
- Consumables
- Cutting and Weld Prep
- Electric Vehicles
- En Español
- Finishing
- Hydroforming
- Laser Cutting
- Laser Welding
- Machining
- Manufacturing Software
- Materials Handling
- Metals/Materials
- Oxyfuel Cutting
- Plasma Cutting
- Power Tools
- Punching and Other Holemaking
- Roll Forming
- Safety
- Sawing
- Shearing
- Shop Management
- Testing and Measuring
- Tube and Pipe Fabrication
- Tube and Pipe Production
- Waterjet Cutting
Industry Directory
Webcasts
Podcasts
FAB 40
Advertise
Subscribe
Account Login
Search
Electric bender cuts lead times, scrap rate
Stacked tooling, ease of programming improve manufacturing efficiencies
- By Eric Lundin
- March 12, 2015
- Article
- Tube and Pipe Fabrication
It’s an age-old rule that businesses must adapt to survive, and nowhere is this more evident than at Toolspec Manufacturing Co. Founded in 1961 as a tool-making company, Toolspec became a fabricator and assembler, specializing in bent tubular parts that require precision forming and welding. Its customers include several blue-chip companies serving world markets in luxury cars and construction machines. The company is a medium-volume manufacturer, typically producing about 16,000 product assemblies each week.
Continual investment in people and equipment has meant that over time Toolspec has built up a large and diverse base of automated production equipment supported by a staff of skilled machine operators. The equipment fleet includes three ring rolling machines, four end forming machines, seven power presses, and 16 robotic welding cells. The company also has a considerable number of tube benders, including 14 hydraulically powered CNC machines that have tube bending capability in sizes from 0.15 to 4.72 in. (4 mm to 120 mm) OD.
Although the company’s benders have served it well over the years, a disadvantage to conventional bending technology is the setup time. For some complex parts, the company’s equipment operators need more than an hour to set up a machine. The next step is a series of trial runs and adjustments, which requires additional time and generates quite a bit of scrap. The problem is compounded by process variables. The performance of some of its legacy equipment changes slightly as the machines warm up, making bend consistency a challenge to maintain throughout a production run.
Moving Forward
In its search for new bending machines, the company learned about electric bending technology. The company invested in two Unison Breeze 50 machines, all-electric models that bend diameters up to 1.97 in. (50 mm). Both are equipped with multistack tool heads to accommodate many diameters without tooling changeover. They also are fitted out with the company’s proprietary laser-controlled springback correction system, which measures bends as they are produced and automatically applies any necessary correction.
Both machines are networked to Toolspec’s CAD facilities and to a coordinate measuring machine (CMM) to ensure consistent production quality. The bending machines can be programmed manually; by importing data from CAD models that Toolspec creates; or by importing programs supplied by the customer. Data the CMM obtains from the first manufactured part is used to verify that the part meets the specifications. If necessary, data from the CMM is used to correct any errors and to adjust the bending machine so that the second and all subsequent parts are manufactured correctly.
According to Operations Director Howard Dean, the new technology doesn’t require advanced expertise. “The complex art of precision tube bending, known only to highly skilled operators, is replaced by a system that is easy to understand and use,” he said. “We took delivery of two [electric] machines less than eight months ago and by integrating them with our CAD and CMM we have implemented a much more efficient and flexible manufacturing system.”
Before this investment, Toolspec often needed weeks to prototype new parts, refine them, and ramp up production, especially if the part involved multiple complex bends followed by welding. After bending a prototype and obtaining customer feedback, the company implemented any necessary design changes, created new bending data, and manually reprogrammed the bending machine to produce a new trial part. This often needed to be repeated for several cycles before the company had a usable prototype, stretching the lead time and resulting in high development costs. The new closed-loop manufacturing strategy has shortened the time-to-first-good-part cycle.
“We are now able to produce prototype parts in a fraction of the time that it took with our old tube benders, with significantly reduced labor costs and much less scrap material,” Dean said.
Toolspec is now able to produce prototype parts to customer specification within about 30 minutes, and it can handle production runs with tolerances as tight as 0.04 in. (1 mm) based on bends that are accurate to within 0.25 degree. Also, because the new machines rely less on operator skill than its legacy machines, the company is positioned to hire additional personnel more easily than before when it needs to expand production capacity.
“Setup time for a new part is minimal, and tool changeover only takes us about 10 minutes, compared to hours with our [old] tube benders,” Dean said. “Now, the first part is usable and the second part is totally correct to drawing, to the point where we can immediately enter full production”.
One immediate result of this capability is that the company has secured a major new contract for export worth $785,000 per year. The company used the machine vendor’s Opt2Sim 3-D simulation software to demonstrate its new tube bending capability to the customer, and it recently delivered the first parts under this contract, all of which passed quality inspection.
About the Author
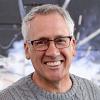
Eric Lundin
2135 Point Blvd
Elgin, IL 60123
815-227-8262
Eric Lundin worked on The Tube & Pipe Journal from 2000 to 2022.
About the Publication
subscribe now
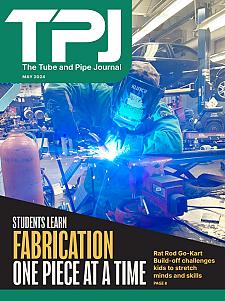
The Tube and Pipe Journal became the first magazine dedicated to serving the metal tube and pipe industry in 1990. Today, it remains the only North American publication devoted to this industry, and it has become the most trusted source of information for tube and pipe professionals.
start your free subscription- Stay connected from anywhere
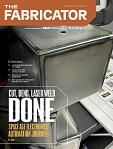
Easily access valuable industry resources now with full access to the digital edition of The Fabricator.
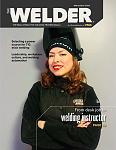
Easily access valuable industry resources now with full access to the digital edition of The Welder.
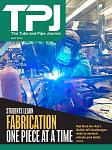
Easily access valuable industry resources now with full access to the digital edition of The Tube and Pipe Journal.
- Podcasting
- Podcast:
- The Fabricator Podcast
- Published:
- 04/16/2024
- Running Time:
- 63:29
In this episode of The Fabricator Podcast, Caleb Chamberlain, co-founder and CEO of OSH Cut, discusses his company’s...
- Trending Articles
Zekelman Industries to invest $120 million in Arkansas expansion
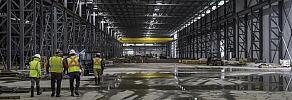
3D laser tube cutting system available in 3, 4, or 5 kW
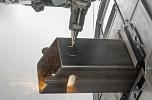
Corrosion-inhibiting coating can be peeled off after use
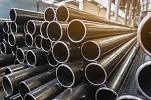
Brushless copper tubing cutter adjusts to ODs up to 2-1/8 in.
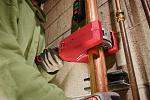
HGG Profiling Equipment names area sales manager
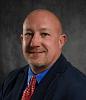
- Industry Events
16th Annual Safety Conference
- April 30 - May 1, 2024
- Elgin,
Pipe and Tube Conference
- May 21 - 22, 2024
- Omaha, NE
World-Class Roll Forming Workshop
- June 5 - 6, 2024
- Louisville, KY
Advanced Laser Application Workshop
- June 25 - 27, 2024
- Novi, MI