- FMA
- The Fabricator
- FABTECH
- Canadian Metalworking
Categories
- Additive Manufacturing
- Aluminum Welding
- Arc Welding
- Assembly and Joining
- Automation and Robotics
- Bending and Forming
- Consumables
- Cutting and Weld Prep
- Electric Vehicles
- En Español
- Finishing
- Hydroforming
- Laser Cutting
- Laser Welding
- Machining
- Manufacturing Software
- Materials Handling
- Metals/Materials
- Oxyfuel Cutting
- Plasma Cutting
- Power Tools
- Punching and Other Holemaking
- Roll Forming
- Safety
- Sawing
- Shearing
- Shop Management
- Testing and Measuring
- Tube and Pipe Fabrication
- Tube and Pipe Production
- Waterjet Cutting
Industry Directory
Webcasts
Podcasts
FAB 40
Advertise
Subscribe
Account Login
Search
Fabricating system achieves one-piece flow for exhaust manifolds
Robotic system handles two manifold styles using sophisticated forming processes
- November 17, 2020
- Article
- Tube and Pipe Fabrication
Situation
An exhaust manifold manufacturer looked for a way to make exhaust systems in an uninterrupted flow. An assembly of parts made from stainless steel, the manifold would require bending, forming, and end calibration. More than performing bending, end forming, and cutting, the production system would provide parts for two styles of manifold, made from either four or six unique tube lengths. Furthermore, if a single tube would fail at the welding stage, the cell would generate a signal to cue the system to produce a replacement tube. Finally, the system would reduce the cutting and trimming operations by forming up to 20 units from a single length of tube, separating each component from the mother tube after forming.
In other words, the customer wanted a versatile system that would provide true one-piece flow, including replacement parts, if necessary.
Resolution
Equipment manufacturer transfluid Maschinenbau GmbH developed a workcell that relies on a central robot for transferring each tube from station to station.
After retrieving a single tube from the magazine, the system uses an eddy current system to find the weld seam so the tube can be oriented properly. A linear handling system feeds the tube to a bending machine, which uses one of four bending tools, then cuts the tube with a carbide cutter for a deformation-free end. The first end of each component then is sized internally and externally at the same time with a finger expansion. After the second end is deburred, the robot takes the component to a combination forming machine for an axial forming process that makes an asymmetrical geometry at the remaining end, and the last step is a final cut to length made by a chipless orbital cutting system.
At this point the robot deposits the component into the appropriate container.
The workcell has one more step to go, one involving an exhaust gas recirculation tube bent by a separate process. Making a 1.75-in. flange on this tube, which has been formed with a bend near the end of the tube and which has a longitudinal weld seam, takes some finesse. The bend’s location limits the clamping length, and the weld seam is more brittle than the parent material, so splitting the tube at the seam is a risk. The process uses a progressive rolling technique that successfully flares the tube despite these challenges.
About the Publication
subscribe now
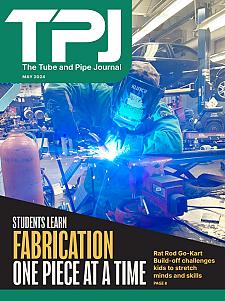
The Tube and Pipe Journal became the first magazine dedicated to serving the metal tube and pipe industry in 1990. Today, it remains the only North American publication devoted to this industry, and it has become the most trusted source of information for tube and pipe professionals.
start your free subscription- Stay connected from anywhere
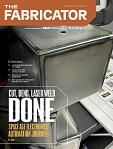
Easily access valuable industry resources now with full access to the digital edition of The Fabricator.
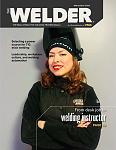
Easily access valuable industry resources now with full access to the digital edition of The Welder.
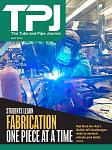
Easily access valuable industry resources now with full access to the digital edition of The Tube and Pipe Journal.
- Podcasting
- Podcast:
- The Fabricator Podcast
- Published:
- 04/16/2024
- Running Time:
- 63:29
In this episode of The Fabricator Podcast, Caleb Chamberlain, co-founder and CEO of OSH Cut, discusses his company’s...
- Trending Articles
Zekelman Industries to invest $120 million in Arkansas expansion
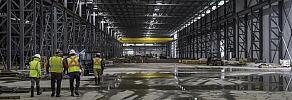
3D laser tube cutting system available in 3, 4, or 5 kW
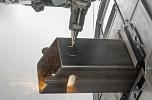
Corrosion-inhibiting coating can be peeled off after use
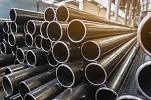
Brushless copper tubing cutter adjusts to ODs up to 2-1/8 in.
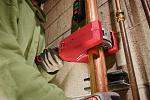
HGG Profiling Equipment names area sales manager
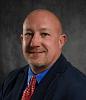
- Industry Events
16th Annual Safety Conference
- April 30 - May 1, 2024
- Elgin,
Pipe and Tube Conference
- May 21 - 22, 2024
- Omaha, NE
World-Class Roll Forming Workshop
- June 5 - 6, 2024
- Louisville, KY
Advanced Laser Application Workshop
- June 25 - 27, 2024
- Novi, MI