- FMA
- The Fabricator
- FABTECH
- Canadian Metalworking
Categories
- Additive Manufacturing
- Aluminum Welding
- Arc Welding
- Assembly and Joining
- Automation and Robotics
- Bending and Forming
- Consumables
- Cutting and Weld Prep
- Electric Vehicles
- En Español
- Finishing
- Hydroforming
- Laser Cutting
- Laser Welding
- Machining
- Manufacturing Software
- Materials Handling
- Metals/Materials
- Oxyfuel Cutting
- Plasma Cutting
- Power Tools
- Punching and Other Holemaking
- Roll Forming
- Safety
- Sawing
- Shearing
- Shop Management
- Testing and Measuring
- Tube and Pipe Fabrication
- Tube and Pipe Production
- Waterjet Cutting
Industry Directory
Webcasts
Podcasts
FAB 40
Advertise
Subscribe
Account Login
Search
Fabricator invests in CNC rolling capability to honor military contract
System hardware, software help fabricator meet accuracy, repeatability requirements for structural member
- By Eric Lundin
- June 1, 2021
- Article
- Tube and Pipe Fabrication
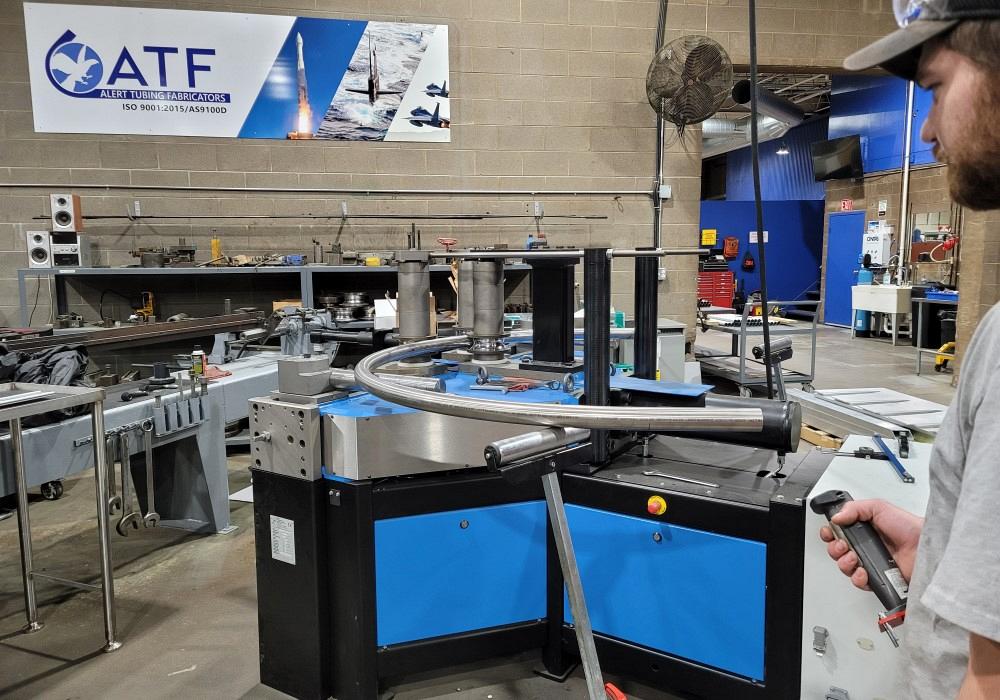
Although Alert Tubing Fabricators, Loves Park, Ill., has been rolling tube for years, its technology advanced substantially when it invested in a CNC machine to augment its manual capability. Images: Alert Tubing Fabricators
It’s an article of faith that U.S. soldiers, sailors, and airmen should never be sent off to engage in a fair fight. Maintaining distinct, clear advantages in combat capabilities and troop readiness and are crucial in keeping any engagements as lopsided as possible.
Whether the latest hardware is something simple, like an upgraded rifle, or something strategic, like a new class of submarine or a newly designed bomber, the latest equipment is always more sophisticated, more capable, or more connected than it predecessor, reflecting the progress of technology. And whether the latest exercise is as rigorous as the previous one, or even worse, soldiers always complain although they know that if they ever see combat, they’ll be glad they were prepared.
These upgraded capabilities and a respectable state of readiness depend on military spending. The federal military budget averaged around $300 billion annually throughout the 1990s, which was about double that of the 1970s. Growth in the military budget changed substantially after Sept. 11, 2001, and it peaked 10 years later at $752 billion. While some of the increase is for more equipment, there is little doubt that much of the additional expenditure covers improved equipment.
Alert Tubing Fabricators, Loves Park, Ill., is no stranger to bidding on military contracts and providing components that go into such programs. The company has been a subcontractor to many government contractors for several years and is aerospace certified. Furthermore, the owner and chief estimator, Kevin Coffey, is a former USAF pilot, so he has some insights from the other side of the fence, knows the jargon, and is familiar with the workings of the bidding and procurement processes.
Bending to Spec
The company recently got a chance to bid on a contract for the Department of Defense. The component was a somewhat challenging structural support made from square tubing, 4 by 4 by 0.375 in., to be bent to a long, sweeping radius. The caveat was that the Alert staff knew it would need a new machine.
The issue was the accuracy. Nearly everything that goes into a military program has to meet strict criteria concerning dimensional tolerances, strength, and durability, and rejects aren’t taken lightly. Although the component Alert bid on was not for critical use—in an offensive or defensive weapon or a propulsion system, for example—it had to meet strict dimensional criteria so fit-up wouldn’t be an issue.
On this component, the length tolerance was tight, specified at the stated length plus 0.030 to 0.060 in. Of course, a final trim cut could take care of that, but far more concerning was the bend tolerance, which was specified at the bend angle ± 0.5 degree. Alert is long on experience in bending and rolling tube and has three manual rolling machines, but the company knew that it would need something more advanced to make the component.
“Without a CNC machine, there wouldn’t be any way to make this part,” Coffey said.
Trial and Error Correction
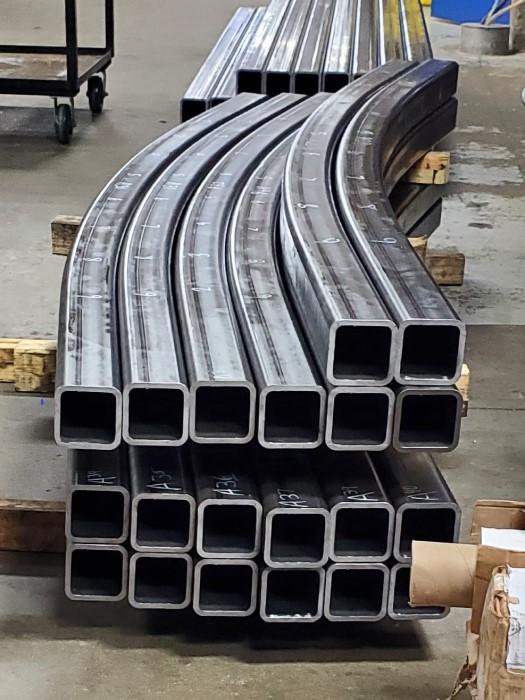
Alert Tubing Fabricators found that the accuracy and repeatability of its PBT 35 machine from Boschert, outfitted with a PC400 CNC, are outstanding. On a recent program for the U.S. military, using a new machine with custom-made tooling, the scrap amounted to less than 1% of the contracted quantity.
Everyone knows that keeping up with trends in bending tube means keeping up with trends in rotary draw benders. When fully outfitted with all of the tool types and machine features available these days, these benders—many of which have some rolling capability—are dazzling in their versatility: Bending can be in either the left-hand or right-hand direction; the machine can be equipped with a mandrel, pressure die, wiper die, and several tooling sets; and programming can be by CNC. This versatility allows the machine to take on ever more severe bending applications and make parts that are smooth (no wrinkles) and dimensionally accurate (no slipping) with a properly formed cross section (no flattening or crushing).
Also, for many years rotary tube benders have provided bend correction. After bending, the tube goes to a measuring station. If the tube is out of tolerance on any of the bends, the measurements are fed to the tube bender’s controller so that it can make slight adjustments to the bending program. In many cases, the next bend meets the dimensional requirements. This last capability is key in scrap reduction.
The Alert staff found a rolling machine that had CNC and a bend correction system when it discovered the PBT line of machines available from Boschert USA. Intended for rolling tube, bar, angle, beam, T profile, U profile, and custom-made shapes, the machines are available in five sizes with four control options (manual, teach-in, tablet CNC, and high-end pedestal CNC). Alert purchased a PBT 35 with the company’s most advanced control option, the PC400 CNC. It comes programmed with modules for creating ellipses, spirals, coils, S bends, and other complex shapes.
The machine typically can make bend corrections with zero scrap. After making the first bend, but before removing the component from the machine, the operator measures the tube’s bend radius (or radii). If any of the bends deviate from the print, the operator enters the measured dimensions into the controller. The machine then rebends the part so that it conforms to the specified dimensions. According to Boschert, the machine initially bends parts conservatively; it underbends slightly with the intention of making a correction later, which isn’t possible if the tube is overbent.
The machine also continually monitors the positions of the X and Y axes and tracks the springback values to build a database for automatic adjustments of future bends.
And it generates an image to represent the elasticities so the operator gains a full understanding of the data and how it is manipulated to bend dimensionally acceptable components.
These capabilities allow a less-experienced or even a newly hired employee to become proficient quickly, they save time, and they conserve material.
Exchanging Growing Pains for Revenue Gains
Because Alert is a veteran-owned company, Coffey has an edge in the bidding process, but that’s as far as that goes. Beyond the bid, Alert has no advantage over any other company. The parts have to meet all of the specifications, and the delivery times have to meet the OEM’s requirements. When the bid for this project was approved, the team got to work just as it always does, making accurate parts and delivering them on time. In fulfilling this contract, it had to do a little in-house work as part of its preparations.
“The machine comes with universal dies, but for this application, we had to make our own dies,” Coffey said. Alert gave the universal dies a try, but the die set’s corner radii and the tube’s corner radii didn’t quite match. The machine is so powerful that it essentially reshaped the tube, forcing some of the metal to flow into the corners of the die, which led to some distortion.

Making, checking, and shipping long parts requires some ingenuity. In addition to making custom radius-checking tools, the staff the staff at Alert Tubing Fabricators often adds supports to common pallets to prepare tube for shipment.
This wasn’t a big problem. Alert has a lot of expertise in machining and often makes its own tooling. Having in-house toolmaking capability isn’t as uncommon as it once was, but the availability and affordability of modern machine tools is a big help, and in this case, so is the tool design assistance that Boschert offers. Because most of the applications for these sorts of machines involve unusual shapes and custom extrusions, the Boschert staff and engineers at the PBT headquarters in Switzerland are accustomed to providing tooling design assistance, so in the end, Alert’s operations manager made a set of customized dies for the application.
Measuring the parts for a quality control check before shipping likewise took some home-grown ingenuity.
“The parts were too large to check on our coordinate measuring machine,” Coffey said.
The Alert staff relied on the part’s prints to laser-cut several steel plates to the contours of the tube, effectively making a set of simple check jigs. They bend the part, hold the plates up to the tube, and look for daylight. No daylight equates to a good bend.
Coffey found that the outcome was very good. The initial bends weren’t quite flawless, and the company had to scrap two parts. However, considering that it was a new part run on a new machine with custom-made tooling, this amount of scrap was negligible.
In addition to its accuracy, the machine also is fast. Another job at Alert highlights the speed of the new machine.
“We have a 1-1/2 in. by ½ rectangular tube that we used to run on one of our manual machines. An order would take us two weeks. Now we run it on the new machine, and it takes less than two days,” Coffey said. “Tubes bent on this machine don’t slip. It can’t be beat for its accuracy, repeatability, and speed.”
About the Author
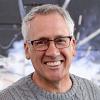
Eric Lundin
2135 Point Blvd
Elgin, IL 60123
815-227-8262
Eric Lundin worked on The Tube & Pipe Journal from 2000 to 2022.
About the Publication
Related Companies
subscribe now
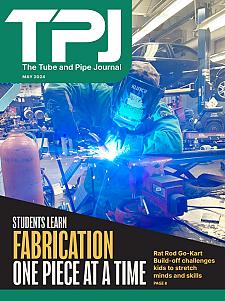
The Tube and Pipe Journal became the first magazine dedicated to serving the metal tube and pipe industry in 1990. Today, it remains the only North American publication devoted to this industry, and it has become the most trusted source of information for tube and pipe professionals.
start your free subscription- Stay connected from anywhere
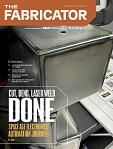
Easily access valuable industry resources now with full access to the digital edition of The Fabricator.
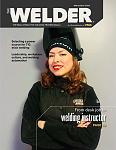
Easily access valuable industry resources now with full access to the digital edition of The Welder.
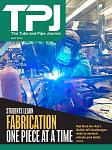
Easily access valuable industry resources now with full access to the digital edition of The Tube and Pipe Journal.
- Podcasting
- Podcast:
- The Fabricator Podcast
- Published:
- 04/16/2024
- Running Time:
- 63:29
In this episode of The Fabricator Podcast, Caleb Chamberlain, co-founder and CEO of OSH Cut, discusses his company’s...
- Trending Articles
Team Industries names director of advanced technology and manufacturing
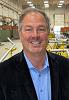
Orbital tube welding webinar to be held April 23
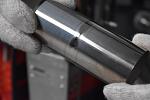
Zekelman Industries to invest $120 million in Arkansas expansion
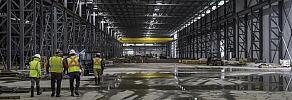
Push-feeding saw station cuts nonferrous metals
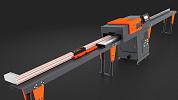
3D laser tube cutting system available in 3, 4, or 5 kW
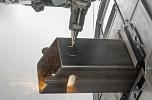
- Industry Events
16th Annual Safety Conference
- April 30 - May 1, 2024
- Elgin,
Pipe and Tube Conference
- May 21 - 22, 2024
- Omaha, NE
World-Class Roll Forming Workshop
- June 5 - 6, 2024
- Louisville, KY
Advanced Laser Application Workshop
- June 25 - 27, 2024
- Novi, MI