- FMA
- The Fabricator
- FABTECH
- Canadian Metalworking
Categories
- Additive Manufacturing
- Aluminum Welding
- Arc Welding
- Assembly and Joining
- Automation and Robotics
- Bending and Forming
- Consumables
- Cutting and Weld Prep
- Electric Vehicles
- En Español
- Finishing
- Hydroforming
- Laser Cutting
- Laser Welding
- Machining
- Manufacturing Software
- Materials Handling
- Metals/Materials
- Oxyfuel Cutting
- Plasma Cutting
- Power Tools
- Punching and Other Holemaking
- Roll Forming
- Safety
- Sawing
- Shearing
- Shop Management
- Testing and Measuring
- Tube and Pipe Fabrication
- Tube and Pipe Production
- Waterjet Cutting
Industry Directory
Webcasts
Podcasts
FAB 40
Advertise
Subscribe
Account Login
Search
Hand-held pressing tool provides quick, convenient pipe installation and maintenance as an alternative to traditional methods
Dreading the next piping repair? Don’t sweat it.
- By Eric Lundin
- May 17, 2018
- Article
- Tube and Pipe Fabrication
Regardless of the industry you’re in, working against the clock is a universal and continuous challenge. Time always seems to be in short supply, and if you don’t have time to do the job right the first time, you certainly won’t have enough time to do it over. Whether you’re running a one-person operation or part of a large contracting firm, making the most of your time is critical, every day, on every job.
It can be especially difficult in a dynamic environment. All the normal day-to-day demands are challenging enough without scheduling changes, interruptions, and hot jobs that wreak havoc on well-organized plans. The search is always on for ways to complete more jobs faster, compete against all the other contractors out there, serve your customers without sacrificing quality, and generate more revenue.
In the mechanical trades, installing, retrofitting, and repairing tube and pipe is a common job, and traditional methods for joining tubes, such as soldering, can be time-consuming. It might be worthwhile to consider other processes, depending on the job.
Join the Pressing Trend
Soldering is a common method of joining two copper tube ends. Informally known as sweating, the soldering process puts quite a bit of heat into the joint of the fitting and copper tube. When all goes as planned, the metals coalesce to form a bond that is mechanically strong and leakproof. Soldering and its cousins, brazing and welding, are used on copper, steel, and stainless steel pipe for applications as varied as fresh and wastewater lines, natural gas lines, sprinkler systems, air conditioner lines, and heat exchanger piping for boiler systems. However, these thermal processes aren’t the only way to make such a joint. A complementary process, pressing, also creates a bond that is both mechanically strong and leakproof.
Tool manufacturer Greenlee Textron manufactures two such pressing tools, one inline and one pistol grip, both trade named Gorilla™ Press.
“Pressing, which is short for the phrase compression pressing, implies and imparts an even pressure exerted 360 degrees around the circumference,” said Dale Speggen, product manager for Greenlee’s mechanical division. The pressing process is far simpler than soldering, brazing, or welding. The user slides a press-style fitting over the two ends of the pipes, places the appropriate press jaw or ring over the fitting, and pulls the trigger. In less than 5 seconds, the pressing cycle produces a strong, leakproof connection. The process to operate the tool is similar to using a power tool to drill a hole or tighten a screw.
“It also brings convenience and versatility to the work site,” Speggen said.
“Conventional methods use an open flame, which has an element of risk and requires a hot-work permit,” Speggen said. “They also require quite a few tools and supplies—a cutting tool, an emery pad, and a wire brush to do the prep work and a torch, flux, fittings, and solder to do the installation. Why not exchange all that for a cutting tool, a pressing tool, a jaw set, and some compression fittings?” he said.
Also, pressing doesn’t require draining the water out of the system, a convenience when working on a system that has been in service.
“Pressing often is used for repairs, maintenance, or retrofitting, and in these cases, water is present in the system,” Speggen said.
The inline model Gorilla, which develops 4,275 pounds of pressing force, has jaw sets that handle pipes from 1⁄2 to 11⁄4 inch in copper and stainless steel and 3⁄8 to 11⁄2 in. in cross-linked polyethylene (PEX). The tool runs on an 18-volt, 2-amp-hour (AH) battery that charges in 15 minutes and runs 150 cycles per charge, according to the manufacturer.
The pistol-grip version is beefier, developing 7,200 lbs. of force and handling pipe sizes from 1⁄2 to 2 in. in copper, stainless steel, and carbon steel. The tool runs on an 18-V 3-AH battery that charges in 22 minutes and delivers 300 cycles per charge, according to Greenlee. Both have heads that swivel 350 degrees for maneuvering the tool into tight spaces and holding the tool comfortably at any angle.
In addition to being easy to use, the tools have self-monitoring capabilities and a memory that makes it easy to track usage for maintenance purposes.
“It tracks the total number of cycles, and the user can set a maximum number, which serves as a reminder to do an inspection, change the oil, or perform some other routine maintenance,” Speggen said. When the tool goes back to the manufacturer for maintenance or repair, the press cycle count since the last maintenance point is reset to zero, but the memory isn’t cleared.
“In addition, the Gorilla tools include a pressure monitoring feature that ensures the fitting is pressed properly,” Speggen said. “In the event optimal pressure is not reached, the tool will notify the operator in real time via audio and visual cues,” he said. The pressing cycle history also is stored and can be retrieved from the tool for documentation.
An Assistant, Not a Replacement
Speggen acknowledges that this sort of tool isn’t going to replace pipe traditional pipe-joining methods. It’s not intended to be a process used instead of soldering, but in addition to soldering. Many factors, like job size, type, and scope, play into deciding to incorporate pressing. While the time to press is significantly faster than soldering, the decision to use pressing comes with two costs that bear consideration: the initial investment and the price of each fitting, which is higher than the price of a conventional fitting. “Investing in a pressing tool is a matter of balancing these costs against time,” Speggen said.
A final benefit to pressing is the consistency in the results. Press tools provide uniformity in pressure, creating water-tight seals from one fitting to the next, from one operator to the next, from the beginning of the shift until the end of the shift.
Greenlee Textron, www.greenlee.com
About the Author
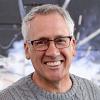
Eric Lundin
2135 Point Blvd
Elgin, IL 60123
815-227-8262
Eric Lundin worked on The Tube & Pipe Journal from 2000 to 2022.
About the Publication
subscribe now
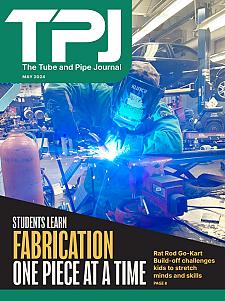
The Tube and Pipe Journal became the first magazine dedicated to serving the metal tube and pipe industry in 1990. Today, it remains the only North American publication devoted to this industry, and it has become the most trusted source of information for tube and pipe professionals.
start your free subscription- Stay connected from anywhere
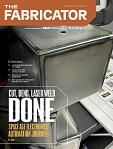
Easily access valuable industry resources now with full access to the digital edition of The Fabricator.
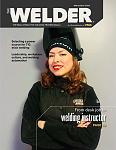
Easily access valuable industry resources now with full access to the digital edition of The Welder.
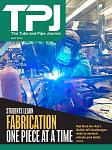
Easily access valuable industry resources now with full access to the digital edition of The Tube and Pipe Journal.
- Podcasting
- Podcast:
- The Fabricator Podcast
- Published:
- 04/16/2024
- Running Time:
- 63:29
In this episode of The Fabricator Podcast, Caleb Chamberlain, co-founder and CEO of OSH Cut, discusses his company’s...
- Trending Articles
Zekelman Industries to invest $120 million in Arkansas expansion
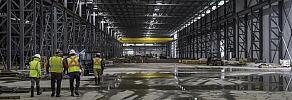
3D laser tube cutting system available in 3, 4, or 5 kW
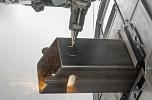
Corrosion-inhibiting coating can be peeled off after use
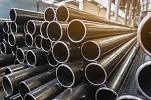
Brushless copper tubing cutter adjusts to ODs up to 2-1/8 in.
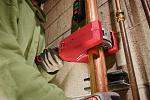
HGG Profiling Equipment names area sales manager
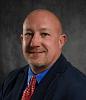
- Industry Events
16th Annual Safety Conference
- April 30 - May 1, 2024
- Elgin,
Pipe and Tube Conference
- May 21 - 22, 2024
- Omaha, NE
World-Class Roll Forming Workshop
- June 5 - 6, 2024
- Louisville, KY
Advanced Laser Application Workshop
- June 25 - 27, 2024
- Novi, MI