- FMA
- The Fabricator
- FABTECH
- Canadian Metalworking
Categories
- Additive Manufacturing
- Aluminum Welding
- Arc Welding
- Assembly and Joining
- Automation and Robotics
- Bending and Forming
- Consumables
- Cutting and Weld Prep
- Electric Vehicles
- En Español
- Finishing
- Hydroforming
- Laser Cutting
- Laser Welding
- Machining
- Manufacturing Software
- Materials Handling
- Metals/Materials
- Oxyfuel Cutting
- Plasma Cutting
- Power Tools
- Punching and Other Holemaking
- Roll Forming
- Safety
- Sawing
- Shearing
- Shop Management
- Testing and Measuring
- Tube and Pipe Fabrication
- Tube and Pipe Production
- Waterjet Cutting
Industry Directory
Webcasts
Podcasts
FAB 40
Advertise
Subscribe
Account Login
Search
Hydroformer proves that two tubes are better than one
Tier 1 supplier uses expertise to replace conventional load beam assembly, improves vehicle’s safety rating
- By Eric Lundin
- July 23, 2018
- Article
- Tube and Pipe Fabrication
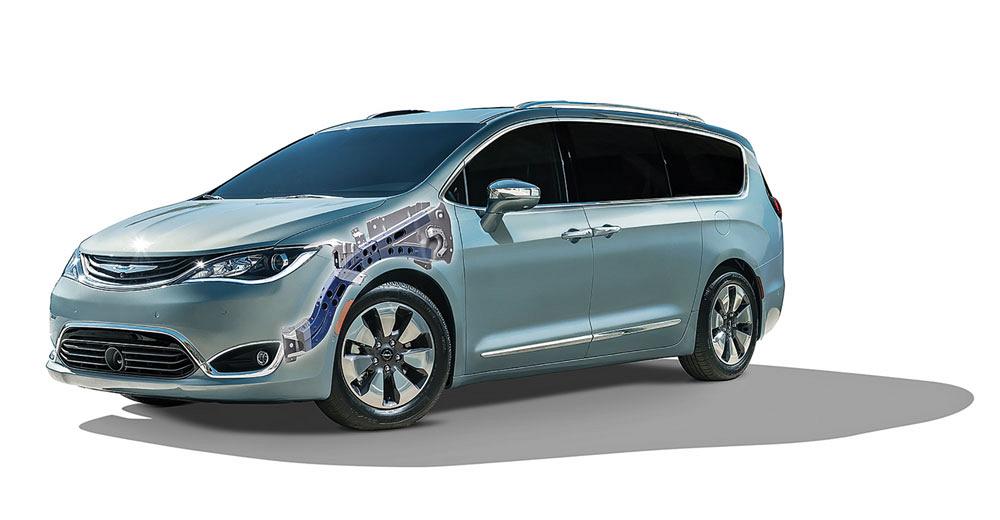
In 2017, Fiat Chrysler Automobiles USA introduced a new minivan design, the Pacifica. It won several awards and, regarding safety, it earned the Insurance Institute for Highway Safety’s highest possible ratings for every category in which it was tested.
Build-to-print may have been enough capability for many companies in the automotive supply chain in the past, but these days Tier 1 suppliers often have to be engineering consultants as well manufacturers. To be a viable partner, a Tier 1 supplier has to know as much about the industry—processes, materials, design trends, safety regulations, corporate average fuel economy, and consumer preferences—as the automobile manufacturers do. In the past, “Yes, we can build this part” was enough. These days, “Yes, we can improve this part” is necessary to thrive in this relentlessly competitive marketplace.
A structural component developed by Tier 1 supplier Vari-Form® for Fiat Chrysler Automobiles US LLC (FCA) is an example of this sort of expertise used in a collaborative effort (see Lead Image). The part is a front load beam that was incorporated into the Chrysler Pacifica®, a flagship minivan that won a slew of awards when it was introduced in 2017.
Although the van concept isn’t new—early vans were available in the 1930s—the modern inception, the minivan, is a relatively recent development. Introduced to the market by Chrysler in 1990 when it rolled out the Town & Country®, it immediately became a force to be reckoned with. “The original annual sales target for the first minivan exceeded all expectations when Chrysler sold 700,000 in the first year,” said Terry Nardone, the company’s director of sales and marketing.The Town & Country also is noteworthy because the 1991 model had the first production hydroformed part—also supplied by Vari-Form—and in the ensuing decades, the partnership between the two companies has deepened, as the Pacifica project shows.
A Man, a Plan, a Van
In 2015 Sergio Marchionne, FCA’s CEO, announced that the company would invest $2 billion to develop a new minivan and overhaul the Windsor Assembly Plant, Windsor, Ont., to produce it. At the time the company was still producing the Town & Country, and the model name Pacifica referred to a crossover vehicle. For the 2017 model year, the Town & Country minivan would be replaced by the newly designed Pacifica minivan.A few years before that, FCA had approached Vari-Form about updating the aforementioned component, which runs from the motor mount to the A pillar.
“About five years ago, engineers at FCA approached us about front load beam,” said Dean Gericke, director of engineering and program management at Vari-Form. “It’s similar to the load beam used in the Dodge Ram truck, which once was a stamped and welded assembly that we replaced with an assembly based on hydroformed tubes.”
Vari-Form’s development of hydroformed components—a program it calls hydroform intensive body structures (HIBS)—is in its third phase. HIBS I dealt with cost and weight reduction. HIBS II involved designs that used specific materials, such as boron steel and variable-thickness tubes. HIBS III takes hydroforming further, focusing on the structural efficiency relative to conventional (stamped) assemblies.
For the Pacifica program, Vari-Form devised an assembly based on two hydroformed tubes with square cross sections. They abut each other along most of their lengths, then go separate ways as they approach the A pillar (see Figure 1).
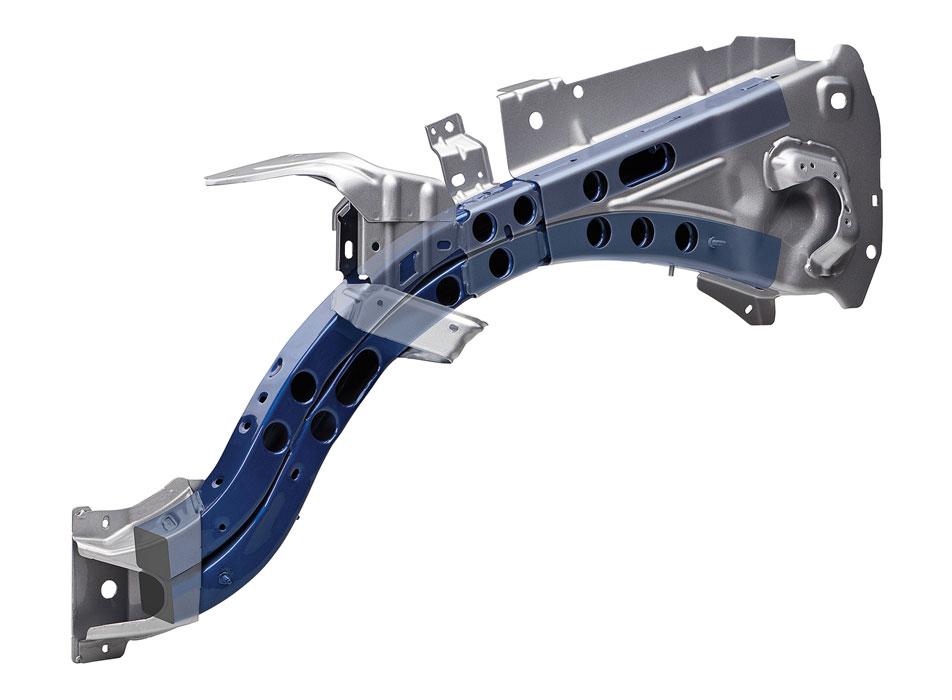
Figure 1
The structural integrity of the Pacifica’s front load beam is based on factors such as the material, design, and processes used for forming and joining the two main components, the square tubes. Tier 1 supplier Vari-Form used its decades of experience and research it dubbed HIBS III, which focuses on structural strength, to design and manufacture a front load beam that helped the vehicle achieve high marks for crashworthiness.
“When two square tubes are in contact back-to-back, they act as a system,” Gericke said. “Two squares can handle a lot more compression than a rectangle that has the same cross section.” Gericke demonstrated the concept by standing a business card on its end and pressing down on it with little force, causing it to flex. The same card, with a fold along its length, has significant column strength and resists substantially more compressive force.
However, developing this component assembly wasn’t nearly as simple as joining two contoured tubes.
From the Pacific to the Atlantic. While the component is a load beam for the Pacifica, this isn’t the only vehicle it is to be used in. It’s no secret that automobile manufacturers strive for standardization whenever they can, often using a single chassis and a handful of drivetrains for several models over several years. The exteriors are different, meaning the hoods, fenders, and other sheet metal components vary in their dimensions, so often a structural component needs a geometry that works with several models in any given year and often several models over several years.
Design for Repairability. Nearly every manufacturer is familiar with designing for ease of assembly. If a part is nearly symmetrical, why not make it perfectly symmetrical, if possible? This prevents an assembler from installing it incorrectly—rotated 180 degrees, upside down, or backward. Designers also need to pay close attention to dimensions, so as a subassembly grows to incorporate additional parts, the dimensions don’t change so much that the part becomes difficult to install (or remove, if it needs to be replaced).
In the automotive world, a related concept is design for repairability. Automobiles need repair from time to time, and a common joining practice in this industry is spot welding. Unlike many welding techniques, which rely on access to just one side of the workpiece, spot welding requires access to two sides. Vari-Form had to take this into account when developing the load beam.
How Safe Is It? Last, because these components are situated near the front tires, they’re far from the center of the vehicle. They sit near the driver-side and passenger-side edges of the vehicle, so they have to bear the load of an offset crash test.
Offset tests are a departure from the more familiar head-on, side-impact, and rollover tests introduced by the National Highway Traffic Safety Administration (NHTSA) in the 1970s. Introduced by the Insurance Institute for Highway Safety (IIHS), offset tests were first carried out in 1995. Rather than using a barrier that contacts the center of the vehicle, offset (or overlap) testing involves a barrier that makes contact with just a portion of the front end of the vehicle, simulating a car hitting a post or two cars colliding, just barely, on a two-lane highway with no central median.
In the original overlap test, which has a moderate amount of offset, a specimen vehicle traveling 40 miles per hour hits a deformable barrier that covers about 40 percent of the vehicle’s width, offset to the drivers’ side. When the test was introduced, just three of the 11 cars tested were rated as good in the IIHS system (which has four rankings: good, acceptable, marginal, and poor). Since that time, the rankings have improved dramatically across the board. In the words of the IIHS: “Today, all vehicles earn good ratings. Occupant compartments are much stronger than they used to be. They hold up in a crash and allow safety belts and airbags to do their jobs. Most modern cars have safety cages encapsulating the occupant compartment and built to withstand head-on collisions and moderate overlap frontal crashes with little deformation. At the same time, crush zones help manage crash energy to reduce forces on the occupant compartment. The main crush-zone structures are concentrated in the middle 50 percent of the front end. When a crash involves these structures, the occupant compartment is protected from intrusion, and front airbags and safety belts can effectively restrain and protect occupants.”
The other two tests, introduced by the IIHS in 2012, are much more demanding. Known as small overlap impact tests, they concentrate all the impact force across just 25 percent of the front of the vehicle. As rendered in the dry prose of the IIHS: “Small overlap frontal crashes primarily affect a vehicle’s outer edges, which aren’t well protected by the crush-zone structures. Crash forces go directly into the front wheel, suspension system and firewall. It is not uncommon for the wheel to be forced rearward into the footwell, contributing to even more intrusion in the occupant compartment and resulting in serious leg and foot injuries.”
Gericke’s description is bolder, describing another result altogether: “The small overlap test simulates a shearing force that tries to peel off the side of the vehicle.” While safety is a universal concern, an image like this strikes a chord because minivans are made for families. Nobody wants to imagine a vehicle full of children opened up like a sardine can. Safety is a critical selling point.
Because the front load beam goes over the wheel well and attaches to the A pillar, it has a lot of responsibility—in a collision, it soaks up some of the force that otherwise would force the wheel into the footwell, and at the same time it supports the doors, pillars, and other structures that run along the side of the vehicle, helping to keep them intact. Because it’s outboard of, and affixed to, the motor rail, the load beam doesn’t get a lot of support from the motor rail.
The front load beam must be tough—strong enough to withstand a sudden load and supple enough to absorb a substantial amount of impact energy.
Generating a Gen3 Subassembly
In past years, the material choices for automotive components included high-strength low-alloy, dual-phase, transformation-induced plasticity, and martensitic steels, referred to as Generation 1 (or Gen1) steels. Derived from mild steels, these were shown to have greater ultimate tensile strength (UTS) and lower ductility than mild steels.
Generation 2, which included twinning-induced plasticity steels and austenitic stainless steels, provided improvements in strength and ductility, but joining them to other materials was difficult at best.
The latest materials to make inroads into the automotive industry, Gen3, have the advantages of Gen2 in strength and ductility. They encompass materials that have ultimate tensile strength (UTS) from 116,000 to 232,000 pounds per square inch (PSI), or 800 to 1,600 megapascal MPa), and elongation approaching 40 percent. The big difference is that they don’t have the joining difficulties the Gen2 materials had.
“The latest materials include DP-1000,” said Gericke, referring to a material with 145,000-PSI UTS), which is substantially stronger than some of the common Gen1 materials, around 87,000 PSI. Vari-Form didn’t need the most capable of the Gen3 materials, opting for DP-780 at 113,000-PSI UTS.
While boron steels likewise have made big strides in the automotive marketplace, they are formed at elevated temperatures and quenched, often in the press, which complicates the process. Boron steels need additional energy for heating and water-cooled dies for quenching.Despite their strength, Gen3 materials are formed cold, so they don’t need to be heated beforehand.
The Size Is the Limit. Reduce, reduce, reduce! Decreasing the weight, size, and cost of every possible automotive component has been a three-part goal in the automotive industry for decades, and so it was for this front load beam.
“The engineers at FCA faced some severe packaging constraints in the Pacifica,” Gericke said. “It’s difficult to fit a load beam made of typical construction into the restricted space above the front tire,” he said, referring to stamped components welded together. Pound for pound, tubular structures tend to provide better integrity than many stamped shapes, standing up better to compression, tension, torsion, and shear forces. Because of this, a tubular assembly often takes up less space and provides more strength than a stamped and welded assembly that serves the same function.
Starting with a clean sheet of paper, relying on tube, and incorporating DP-780 set Vari-Form up for a successful replacement part. The team was able to make a smaller assembly and, because the material has tremendous strength, it’s a lightweight assembly. The wall thickness is just 1 millimeter.
The tubular portion doesn’t have to conform to the specific geometry of every vehicle in the program; it simply has to match the chassis, which is identical from one model to the next. To match the variations in geometry of the hoods, fenders, and other model-specific points, the Vari-Form team came up with brackets and other hardware—components that are unique to each model—to complete each assembly.
Cold Code Welding. To join the components to make the assembly, Vari-Form relies heavily on Cold Metal Transfer®, a welding process developed by welding equipment supplier Fronius International GmbH. According to Fronius, it’s a low-current, low-heat process that uses digital controls to feed the wire forward, then retract it as soon as the controller detects the short circuit. This keeps the arc-burning time, and the heat, to a minimum. The system monitors the arc length and adjusts it continuously, which provides a stable arc and spatter-free welds, according to the company.
It does really well in welding metals of dissimilar thicknesses, according to Gericke.
“It allows us to weld 1-mm-thick material to 2.5-mm-thick material,” he said. “Regarding the materials we weld and the speeds we achieve, I know of no other process that can do it.”
Expertise Unbridled. Understanding how each fabrication step influences downstream fabrication steps, and the part’s outcome, is the key to making a part that conforms to the intended dimensions.
“To do this, it’s necessary to understand all of the characteristics of the tube and how it behaves,” Nardone said. “You bend it, and it springs back. You hydroform it, and it springs back. The weld draw also changes its shape. You have to go from the welding stage all the way back to the straight tube to get the right geometry.”
Dealing with the springback, work hardening, and thermal expansion would be difficult if the tubes were symmetric, but they’re not. A series of holes runs the length of both tubes on one side only—the side that faces away from the fender inners and other structures the load beam mounts to. These holes provide ease of repairability, allowing access by spot welding gear when replacing the load beam is necessary.
While the series of holes worked a little havoc on the anticipated springback, Vari-Form’s engineers persevered and ultimately developed a front load beam that meets all of FCA’s criteria.
Loading the Front Load Beam
If FCA’s goal was to change the vehicle’s safety rating, it seems to have worked. The predecessor vehicle, the 2016 Town & Country, had a very good record, having received four out of five stars in three NHTSA categories and five stars in one of its categories; it received top marks in four out of five categories tested by the IIHS. The main drawback was severe in that it received the lowest possible rating in the driver-side small overlap test.
The FCA design and the Vari-Form front load beam helped the Pacifica do better than the Town & Country, earning 19 out of 20 possible stars from the NHTSA and top rankings in five out of five IIHS evaluations, which included the driver-side small overlap test.
Vari-Form Corp., 17199 N. Laurel Park, Ste. 322, Livonia, MI 48152, 248-879-7656, www.vari-form.com
About the Author
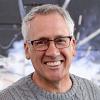
Eric Lundin
2135 Point Blvd
Elgin, IL 60123
815-227-8262
Eric Lundin worked on The Tube & Pipe Journal from 2000 to 2022.
About the Publication
Related Companies
subscribe now
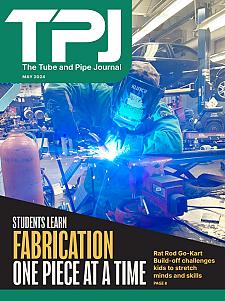
The Tube and Pipe Journal became the first magazine dedicated to serving the metal tube and pipe industry in 1990. Today, it remains the only North American publication devoted to this industry, and it has become the most trusted source of information for tube and pipe professionals.
start your free subscription- Stay connected from anywhere
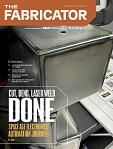
Easily access valuable industry resources now with full access to the digital edition of The Fabricator.
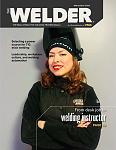
Easily access valuable industry resources now with full access to the digital edition of The Welder.
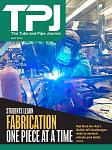
Easily access valuable industry resources now with full access to the digital edition of The Tube and Pipe Journal.
- Podcasting
- Podcast:
- The Fabricator Podcast
- Published:
- 04/16/2024
- Running Time:
- 63:29
In this episode of The Fabricator Podcast, Caleb Chamberlain, co-founder and CEO of OSH Cut, discusses his company’s...
- Trending Articles
Zekelman Industries to invest $120 million in Arkansas expansion
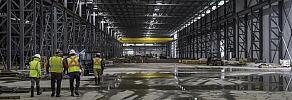
3D laser tube cutting system available in 3, 4, or 5 kW
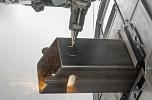
Corrosion-inhibiting coating can be peeled off after use
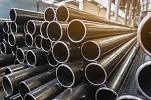
Brushless copper tubing cutter adjusts to ODs up to 2-1/8 in.
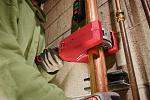
HGG Profiling Equipment names area sales manager
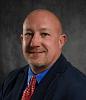
- Industry Events
16th Annual Safety Conference
- April 30 - May 1, 2024
- Elgin,
Pipe and Tube Conference
- May 21 - 22, 2024
- Omaha, NE
World-Class Roll Forming Workshop
- June 5 - 6, 2024
- Louisville, KY
Advanced Laser Application Workshop
- June 25 - 27, 2024
- Novi, MI