Founder
- FMA
- The Fabricator
- FABTECH
- Canadian Metalworking
Categories
- Additive Manufacturing
- Aluminum Welding
- Arc Welding
- Assembly and Joining
- Automation and Robotics
- Bending and Forming
- Consumables
- Cutting and Weld Prep
- Electric Vehicles
- En Español
- Finishing
- Hydroforming
- Laser Cutting
- Laser Welding
- Machining
- Manufacturing Software
- Materials Handling
- Metals/Materials
- Oxyfuel Cutting
- Plasma Cutting
- Power Tools
- Punching and Other Holemaking
- Roll Forming
- Safety
- Sawing
- Shearing
- Shop Management
- Testing and Measuring
- Tube and Pipe Fabrication
- Tube and Pipe Production
- Waterjet Cutting
Industry Directory
Webcasts
Podcasts
FAB 40
Advertise
Subscribe
Account Login
Search
Improving part consistency with CNC tube benders
Focus on a few key areas to pinpoint your issues
- By Jay Robinson
- November 11, 2023
- Article
- Tube and Pipe Fabrication
When production parts coming off CNC tube benders show variations, the natural reaction is to think there are problems with the machine or bend tooling.
While this sometimes is the case, variations just as often are caused by other factors. Following are a few common problems and things to check if you are not getting consistently good bends.
Length Variations
Length varies on the first straight, but all the other legs and the last straight length are consistent. Make sure your cut lengths are consistent. While this seems obvious, tube fabricators often struggle to get parts consistently within tolerance in their gauges because the variation in cut length exceeds the allowable variation in leg length.
Length varies in the first and last straight. Ensure that your load position is consistent and straight. A tube that is loaded into the collet at an angle (usually sagging down) typically will be lifted into a straight position when the collet closes so that it looks fine before bending starts.
However, imagine how the edge of the tube abuts the stops in the collet if it is sagging down: The bottom edge of the tube may contact the stop, but the top edge will not. When the collet closes and the tube is lifted, either the top has to move back some while the tube is lifting, or the bottom will have to come forward.
There’s an equal chance that the bottom will move forward, the top will move back, or a little of both. Because the relative position of the tube is moving forward and backward but the machine is moving to the same positions, both the first and last legs are affected but the lengths between bends are not.
Last leg length varies, but all other lengths are consistent. Watch to see if the clamp slips on the tube as bending starts and progresses. While clamp slip can cause all sorts of issues, it is entirely possible for the clamp to slip a little during the bend and cause no obvious issues with the quality of the bend.
However, when the clamp slips on the tube, less of the straight length is consumed. After bending, the carriage still correctly positions the tube between the two tangent points, which means that the change will show up in the last straight length. Because the amount the clamp slips will not be consistent, the last straight length also will not be consistent.
Leg lengths are inconsistent through the part. Watch if the tube slips in the collet. If the tube is being pulled slightly forward out of the collet during bending, it may get pushed back into the collet when the carriage pushes the tube out of the bend die. Similar to clamp slip, collet slip may not be very consistent, so it will seem like the leg lengths are constantly changing.
Rotation Variations
Rotations are consistent on the first couple of bends but vary on later bends. Watch for the tube to spin in the collet. As a part progresses through bending, it often gets farther and farther from the centerline of the tube. The farther away the first end of the tube gets away from center, the more leverage it has against the collet. As the rotation starts, more and more inertia must be overcome both to start and stop the rotation.
Rotations are inconsistent on a single bend. Look for interference from the part catching some part of the tooling or machine.
Bend Quality Issues
The outside of the bend is flattening. If using a mandrel, check the mandrel’s nose-to-tangent position. Depending on the type of mandrel, the nose should almost always be slightly in front of the tangent line of the bend die. This rounds the outside radius of the tube, though it naturally wants to flatten.
Check the pressure die assist (PDA) speed. If the PDA speed is set too low, it will add drag along the outside radius of the bend and may cause the tube to flatten.
The outside radius of the bend has a hump. Check the position of the mandrel. It is likely too far forward.
Wrinkles are forming inconsistently. Clamp slippage is the most common cause of inconsistent wrinkles. Because the amount that the clamp slips generally won’t be consistent, you may find that while several parts will be OK, a couple will have one or two bends that wrinkle a little. Or, you might have one bend that suddenly wrinkles a lot, but every other bend is OK.
When the clamp starts to slip, eventually the action changes from a bend to more of a fold. That’s when wrinkles start to form.
Additional Factors to Check
Amount of mandrel lubricant. As the tube forms, excess oil or gel lubricant can get trapped and create inconsistent voids between the tube wall and mandrel that otherwise would not be there.
Collet slip/carriage speed when bending with carriage boost. If your part requires carriage boost but the carriage speed is set too low, it may pull the tube forward slightly at the end of a bend. On the next bend, as the tube is drawn around the die, the carriage is unable to help the tube around because the tube slips back momentarily to its original position against the stop.
Weld seam. Confirm that tube is always loaded with the weld seam in the same location.
Pressure die pressure. A lot of issues, including wrinkles, can often be masked by adding pressure die pressure. However, add too much pressure and the PDA may not be able to travel forward with the tube, which then causes clamps to slip, which in turn causes wrinkles.
Too much pressure also can harm the machine and wear out consumables prematurely. Insufficient pressure also can cause wrinkles.
PDA slippage during bending. PDA slippage can be hard to see. During bending, it looks like the PDA is traveling faster than the tube—because it is. It has a slightly longer path to travel along the outside radius, meaning that as bending occurs, the PDA (or even an unpowered follower) has to travel slightly faster than the centerline of the tube.
Also, as the tube stretches along the outside radius, the overall tube length generally gets longer. Both of these things (longer path and elongating tube) can cause the appearance, when viewed from the back, that the PDA is slipping forward.
However, when the PDA speed is set too high and there is a not enough pressure on the pressure die to stop it from slipping, the face of the PDA may hit the back of the clamp die. As the bend moves around and the clamp die moves out of the way at about 45 degrees, the PDA will jump forward as viewed from the front or above.
As soon as it starts slipping, its effectiveness in helping push more material to the outside of the bend is greatly reduced. With less help from the PDA, the clamps have to take up the additional load, and they will start to slip. This may cause wrinkles to appear where they didn’t on a previous part.
About the Author
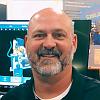
About the Publication
Related Companies
subscribe now
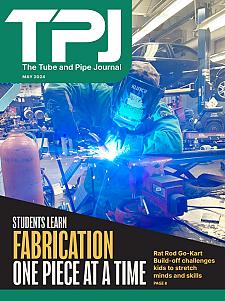
The Tube and Pipe Journal became the first magazine dedicated to serving the metal tube and pipe industry in 1990. Today, it remains the only North American publication devoted to this industry, and it has become the most trusted source of information for tube and pipe professionals.
start your free subscription- Stay connected from anywhere
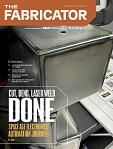
Easily access valuable industry resources now with full access to the digital edition of The Fabricator.
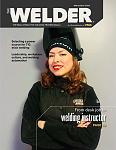
Easily access valuable industry resources now with full access to the digital edition of The Welder.
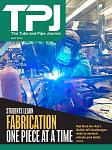
Easily access valuable industry resources now with full access to the digital edition of The Tube and Pipe Journal.
- Podcasting
- Podcast:
- The Fabricator Podcast
- Published:
- 04/16/2024
- Running Time:
- 63:29
In this episode of The Fabricator Podcast, Caleb Chamberlain, co-founder and CEO of OSH Cut, discusses his company’s...
- Trending Articles
Zekelman Industries to invest $120 million in Arkansas expansion
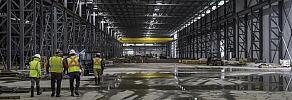
3D laser tube cutting system available in 3, 4, or 5 kW
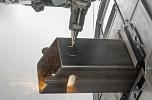
Corrosion-inhibiting coating can be peeled off after use
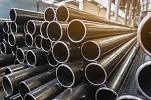
Brushless copper tubing cutter adjusts to ODs up to 2-1/8 in.
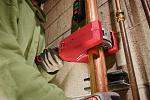
HGG Profiling Equipment names area sales manager
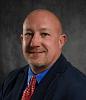
- Industry Events
16th Annual Safety Conference
- April 30 - May 1, 2024
- Elgin,
Pipe and Tube Conference
- May 21 - 22, 2024
- Omaha, NE
World-Class Roll Forming Workshop
- June 5 - 6, 2024
- Louisville, KY
Advanced Laser Application Workshop
- June 25 - 27, 2024
- Novi, MI