- FMA
- The Fabricator
- FABTECH
- Canadian Metalworking
Categories
- Additive Manufacturing
- Aluminum Welding
- Arc Welding
- Assembly and Joining
- Automation and Robotics
- Bending and Forming
- Consumables
- Cutting and Weld Prep
- Electric Vehicles
- En Español
- Finishing
- Hydroforming
- Laser Cutting
- Laser Welding
- Machining
- Manufacturing Software
- Materials Handling
- Metals/Materials
- Oxyfuel Cutting
- Plasma Cutting
- Power Tools
- Punching and Other Holemaking
- Roll Forming
- Safety
- Sawing
- Shearing
- Shop Management
- Testing and Measuring
- Tube and Pipe Fabrication
- Tube and Pipe Production
- Waterjet Cutting
Industry Directory
Webcasts
Podcasts
FAB 40
Advertise
Subscribe
Account Login
Search
Mechanical contractor invests in laser cutting equipment to support new business structure
Company’s new business model sparks growth, new business opportunities with tube and pipe
- By Eric Lundin
- February 8, 2022
- Article
- Tube and Pipe Fabrication
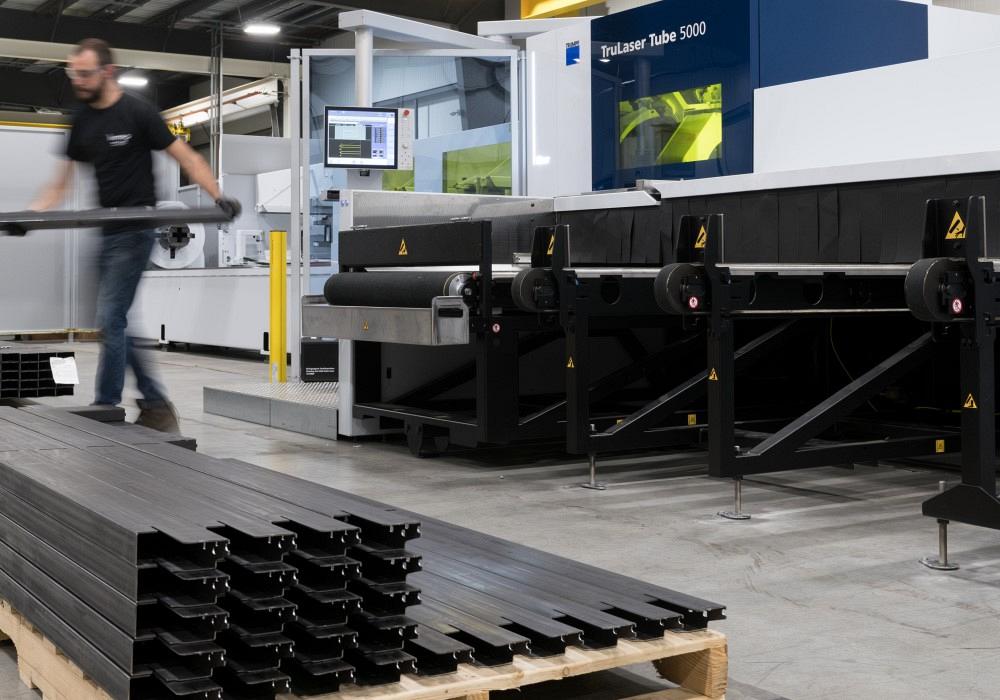
After decades of success and growth, mechanical contractor H&S Industrial had outgrown its facility and was primed for a move. When it moved to a new location, the executive team created a new business model to incorporate contract manufacturing. H&S Industrial
To the uninitiated, the phrase metal fabrication sounds like it describes just one thing, but of course it’s far more than that. A large stamping company has little in common with a two-person outfit that focuses on railings and gates. A fabricator that can turn a profit on order volumes less than 10 is at one end of the volume spectrum, whereas manufacturers in the automotive tier structure are at the other end. Making a pipe product for offshore oil extraction is much more stringent than making tube for lawn mower handles and chair legs.
And that’s just among manufacturers. Metal fabrication has a big presence among mechanical contractors too. This is the territory occupied by H&S Industrial, Manheim, Pa. Founded as Herr & Sacco Inc. in 1949, the company excels in industrial and structural fabrications such as ASME code-compliant pressure vessels, process/utility piping systems; conveyors, hoppers, and similar material-moving machines and systems; platforms, mezzanines, catwalks, and structural supports; and other large-scale items that support construction projects.
Among metal fabricators, those that have long-term contracts for parts produced in high-speed processes like stamping tend to have the lowest mix and the highest volume. That’s not H&S. Its business model is the definition of high mix/low volume, often making quantities of one. That said, it has many things in common with companies that fabricate manufactured components and assemblies. Metal fabricators of all sorts seek growth but can find themselves hemmed in for a variety of reasons. When a fabricator has gotten all it can out of its building, its equipment, or its markets, it needs to shake things up to move forward.
Several years back, H&S Industrial’s president found a way to move the company forward in one vast step, getting past several of the factors that were restraining its growth.
A Company in Transition
In 2006 Chris Miller found himself suddenly at the helm of H&S Industrial. Formerly a project manager for the firm, he had received the shocking news that his father, the company’s president, was ill and hospitalized. He died just over a week later, and a few months afterward, Chris demonstrated that he was prepared for his new role when he unveiled a bold plan to start a new chapter in the company’s story. He envisioned more space, a new layout, and a pathway to enter new markets.
The immediate concern was that company had outgrown its facility in Landisville, Pa. The building was too small, the loading docks were too small, and Landisville was too small. The city’s compact streets weren’t built to carry giant pressure vessels and other large, industrial fabrications that were H&S’s focus. So the executive team found land in nearby Manheim and got to work in planning a new location. This was more than an opportunity for more space; it was a chance to use its new space in a more efficient way than before.
The executives didn’t want a series of work bays. A work bay is suitable for building each project in place, but efficiency depends on the scope of the projects. As the projects grow in complexity, moving the projects through the facility from one station to another makes more sense. However, a traditional assembly line wouldn’t work. A large, slow-moving project could get in the way of a small, fast-moving project.
The executive team developed a layout based on four assembly lanes. With a little guesstimating, it’s not too difficult to separate and segregate projects so each can move along without impeding the progress of those that come behind. This layout has something more, though: a feature that takes into consideration a slowdown caused by unforeseen circumstances. It’s a broad aisle that runs perpendicular to the four lanes, providing a passing lane. If a project in one lane slows down, projects behind it aren’t held up.
A second component to Miller’s strategy was far more impactful. He envisioned a company made up of several separate divisions united by a hub that provides common resources for the various divisions, such as executive guidance, strategic planning, human resources support, a unified safety program, accounting, and business development efforts. Breaking out each of the company’s activities into separate units would call attention to each of the core functions provided by the company, now named Viocity Group. Each unit would support the other divisions and pursue its own customer base.
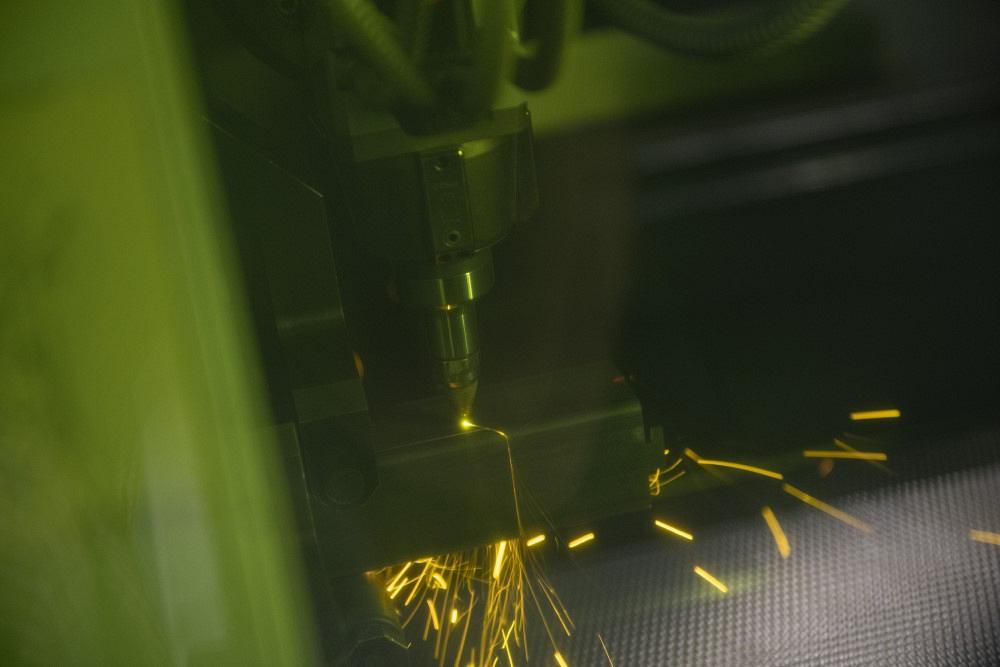
A mechanical contractor's volumes usually aren't enough to justify an investment in a laser cutting machine. H&S made the investment with the intention of entering the metal fabrication market, a gamble that paid off.
In 2016 the company started to roll out the new structure. With this arrangement, H&S Industrial’s role is essentially the same as it was, providing large-scale metal fabrication projects, blasting, painting, and rigging. Staffed by more than 80 employees, it occupies 80,000 sq. ft. for cutting, fabricating, welding, and finishing.
The second division, Nitro Cutting, was launched the same year, featuring a fully automated TRUMPF TruLaser 3030 fiber laser for cutting sheet. H&S had taken a leap of faith a year earlier when it invested in this system. It was a substantial risk, considering that the company had no previous exposure to laser cutting and no customers that were interested in laser cutting services. Miller considered laser cutting to be an opportunity for growth and was looking ahead to enhance the capabilities of H&S, and in 2016 he transferred this machine to Nitro. The 15,000-sq.-ft. cutting division is now fully staffed and providing automated laser cutting and forming services.
RSR Electric was established in 2018. Formerly known as RS Reidenbaugh, it provides expertise in developing power supply and control systems, with an emphasis on data and communication infrastructure. A fourth unit added in 2020, Keystruct Construction, is a general contracting company. It provides project management for every step of a commercial or industrial construction project, from preconstruction planning to the design and build phases. It also handles renovations.
This new mode of doing business goes far beyond a rebranding, and it’s more than a new organization. It highlights and deploys the decades of accumulated expertise of each business unit, effectively making all of it available to every customer. It also provides a way to cross-sell the other services. Miller’s intention is to turn bids for portions of projects into bids for turnkey projects.
Cutting Tube with a Laser Machine
When Miller’s strategic vision came to fruition, the company had already invested in its first fully automated laser. As Miller’s vision developed, the executives realized that a tube laser would likely be a good fit for Nitro. Tube and pipe work had been prominent at H&S for decades, but it was just one piece of a vast puzzle. As such, the company’s tube and pipe cutting had never come under any particular scrutiny until the 2015 timeframe.
“The company is engaged in many types of industrial projects,” Miller said. “Hoppers, conveyors, tanks, guarding systems, and platforms are typical projects, and even if they’re not heavy in tube or pipe, many of these sorts of things need tube for mechanical or structural reasons.”
It invested in a TRUMPF TruLaser Tube 7000 fiber laser which, like the sheet laser, is fully automated. It’s a large-format machine capable of cutting rounds up to 10 in. dia. and squares up to 7 by 7 in. Its infeed system handles raw material lengths up to 30 ft. long, while the outfeed can handle finished parts up to 24 ft. long. It’s one of the largest tube lasers available, and the only one in the local area, according to Miller.
It would be a stretch to say that the company’s investment in a tube laser brought the entire plan together, but the investment is a scaled-down version of the company’s business model, demonstrating how Nitro supports itself and the other divisions.
“Switching to laser cutting really improved the accuracy of the parts,” Miller said. “We get better assemblies, but just as importantly, it leverages our other resources, notably our welders.” Nobody wants a skilled welder struggling with poor fit-ups. Figuring out a workaround takes time and effort that would be best spent welding.
“The outcome is better fitment, better assemblies, and less time spent welding,” he said. Laser cutting also helps alleviate the need to find welders with deep expertise. If the fit-up is right on the money, a welder with less experience can handle the assembly with ease.
“Using tabs and slots also helps in improving efficiency,” he said. “A tab-and-slot approach allows us to eliminate fixturing and eliminate assembly mistakes. Once in a while, a welder puts an assembly together wrong and has to cut it apart and rebuild it. Placing the tabs and slots strategically can make it impossible to assemble a project incorrectly, and we can offer this as a service to our customers,” he said. The machine can drill and tap holes, and it’s exceptional for the myriad miscellaneous items the company needs, such as brackets, hangers, and gussets.
It didn’t end there. The new organization, combined with the tube laser and other key investments, allowed the company to go even further, working outside the realm of mechanical contracting. The staff at Nitro Cutting now thinks and works like the staff at a contract manufacturer.
“We have quite a bit of steady, high-volume work using the new technologies,” Miller said, referring to its laser machines. “We’ve gone from a 100% job shop approach, where we do one project at a time, to high-volume work on six- to 12-month contracts,” he said.
But it wasn’t an easy transition. It was new and different, and some employees weren’t ready for it. Projects undertaken by a mechanical contractor provide something different every day, and much of the work is hands-on and labor-intensive. Tending a machine that makes high volumes of parts around the clock for the manufacturing industry was a foreign concept in the early days of Nitro Cutting.
“This was quite a shock to some of the veteran employees, one or two of whom have been with us for 50 years,” Miller said.
Miller understands it. On the shop floor, the change was in how parts would be made. In the executive suite, many other changes would play out. A contract manufacturer works in a business environment that is completely different from that of a mechanical contractor. The customers, the applications, the contracts, the bidding process, scheduling, the inspections, packing and shipping, and of course the opportunities and the challenges—everything is different.
These were high hurdles, but the executives at Viocity and the employees at Nitro cleared all of them.
Low- and High-volume Work
Creating Nitro brought in work from markets that are new to the company—exercise equipment, agricultural machines, conveyance, and bulk storage. The company also does some work in making components for low-volume, special-use transportation vehicles.
Like many fabricators that have quite a bit of manufacturing experience, Nitro doesn’t just make components and assemblies. It has substantial insights that can help streamline manufacturing, so it has a collaborative partnership with many of its clients, offering value analysis/value engineering to simplify components where possible. This creates a virtuous cycle of reducing costs for its customers, reinforcing its relationships with those customers, and bringing in more business.
Despite any setback caused by COVID-19, the machines were running full-tilt by the middle of 2021. The decision to make these investments paid off, but this doesn’t mean that the decision to bring laser cutting capability in-house was an easy one. Many fabricators make an investment in something like a laser cutting machine only after outsourcing laser work for years. They already havethe business and just need to bring it in-house. In the case of Nitro and its first laser cutting system, it didn’t start with a built-in customer base.
“We had new equipment, but no customers and no orders,” Miller said. “I spent a lot of sleepless nights wondering if I had made the right decision.”
It was the right decision, and the company is stronger for it. Nitro Cutting initially had no external customers, so 100% of its work was Viocity work. Just a few years later Nitro’s work for the other Viocity divisions is a mere 10% of its business.
And, since it invested in its first two laser cutting machines, Nitro Cutting has taken delivery of another tube laser system and it has another sheet laser scheduled for delivery early in 2022.
On the eastern seaboard, TRUMPF is represented by Mid Atlantic Machinery and Southern States Machinery
About the Author
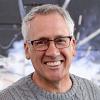
Eric Lundin
2135 Point Blvd
Elgin, IL 60123
815-227-8262
Eric Lundin worked on The Tube & Pipe Journal from 2000 to 2022.
About the Publication
Related Companies
subscribe now
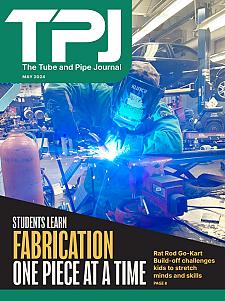
The Tube and Pipe Journal became the first magazine dedicated to serving the metal tube and pipe industry in 1990. Today, it remains the only North American publication devoted to this industry, and it has become the most trusted source of information for tube and pipe professionals.
start your free subscription- Stay connected from anywhere
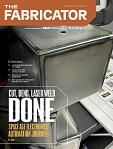
Easily access valuable industry resources now with full access to the digital edition of The Fabricator.
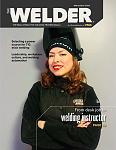
Easily access valuable industry resources now with full access to the digital edition of The Welder.
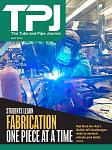
Easily access valuable industry resources now with full access to the digital edition of The Tube and Pipe Journal.
- Podcasting
- Podcast:
- The Fabricator Podcast
- Published:
- 04/16/2024
- Running Time:
- 63:29
In this episode of The Fabricator Podcast, Caleb Chamberlain, co-founder and CEO of OSH Cut, discusses his company’s...
- Trending Articles
Zekelman Industries to invest $120 million in Arkansas expansion
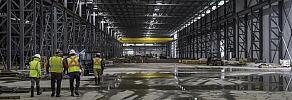
3D laser tube cutting system available in 3, 4, or 5 kW
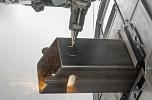
Corrosion-inhibiting coating can be peeled off after use
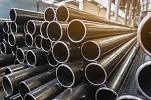
Brushless copper tubing cutter adjusts to ODs up to 2-1/8 in.
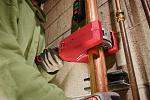
HGG Profiling Equipment names area sales manager
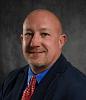
- Industry Events
16th Annual Safety Conference
- April 30 - May 1, 2024
- Elgin,
Pipe and Tube Conference
- May 21 - 22, 2024
- Omaha, NE
World-Class Roll Forming Workshop
- June 5 - 6, 2024
- Louisville, KY
Advanced Laser Application Workshop
- June 25 - 27, 2024
- Novi, MI