Director Market Development
- FMA
- The Fabricator
- FABTECH
- Canadian Metalworking
Categories
- Additive Manufacturing
- Aluminum Welding
- Arc Welding
- Assembly and Joining
- Automation and Robotics
- Bending and Forming
- Consumables
- Cutting and Weld Prep
- Electric Vehicles
- En Español
- Finishing
- Hydroforming
- Laser Cutting
- Laser Welding
- Machining
- Manufacturing Software
- Materials Handling
- Metals/Materials
- Oxyfuel Cutting
- Plasma Cutting
- Power Tools
- Punching and Other Holemaking
- Roll Forming
- Safety
- Sawing
- Shearing
- Shop Management
- Testing and Measuring
- Tube and Pipe Fabrication
- Tube and Pipe Production
- Waterjet Cutting
Industry Directory
Webcasts
Podcasts
FAB 40
Advertise
Subscribe
Account Login
Search
Overcoming bottlenecks on either side of Industry 4.0 automation
A holistic view is necessary for manufacturers to get the most out of a digital process upgrade
- By Bill Kelly
- June 2, 2020
- Article
- Tube and Pipe Fabrication
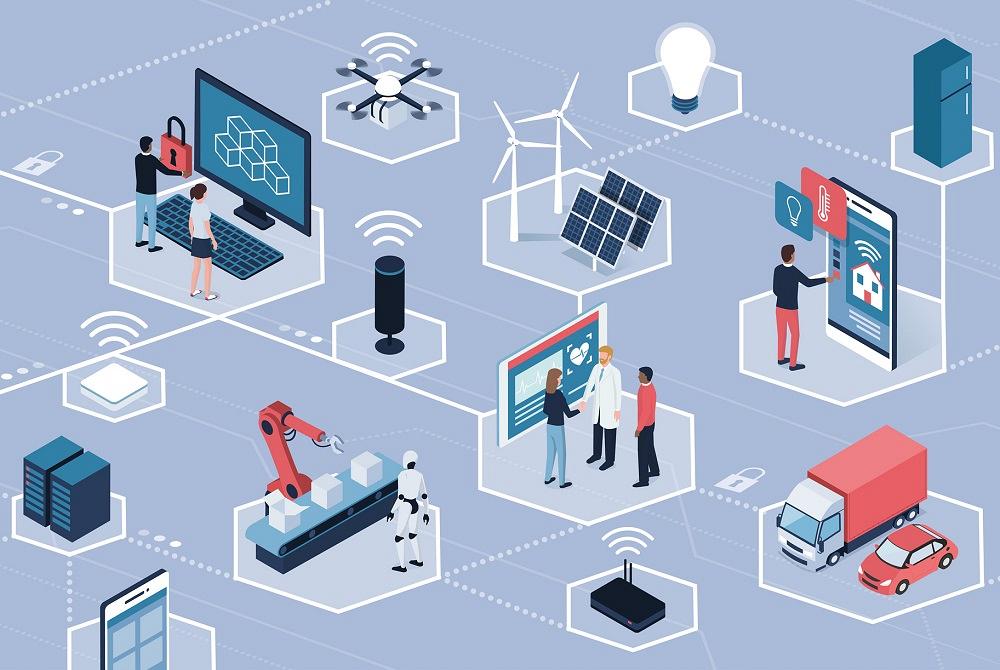
Implementing Industry 4.0? Digitization, connectivity, and transparency can revolutionize a process or even an entire business, but successful implementation requires a holistic analysis. Getty Images
Manufacturers around the world are facing growing pressure to deliver products more efficiently and affordably than ever before while maintaining quality standards. In such an environment, organic growth isn’t enough. Surviving and thriving is a matter of achieving growth through innovating.
Modern technologies are transforming nearly every industry and sector, including manufacturing, creating opportunity for improvements in productivity, efficiency, and agility, as well as worker safety and satisfaction.
Industry 4.0 presents one such opportunity for companies looking to innovate and achieve competitive advantage. The term Industry 4.0 essentially describes the fourth (and current) industrial revolution, a result of combining a variety of modern technologies. The key elements are digitization and connectivity. Using sensors that measure inputs and outputs, creating subsystems that turn those inputs and outputs into a digital information stream, and making that stream of information available and accessible in a connected system is the basis of Industry 4.0.
Despite the significant momentum gained by Industry 4.0 since 2011, its infancy means that little documentation of successful integrations exists. Without white papers, trade journal articles, and industry reports, manufacturers have no best practices to reference, so even today, implementations and integrations involve some trial and error.
Ramifications of Industry 4.0 on the Manufacturing Process
Regarding productivity, Industry 4.0 automation has the potential to make former manufacturing processes almost unrecognizable. Companies can significantly boost operational revenue by implementing connected automation within their facilities. Furthermore, revenue in the robotics market, which represents a key element in automation, is forecast to reach $87 billion by 2025. Now is an opportune time to explore and engage with automation and connective technologies to help to shape the manufacturing of the future.
Successful implementation of an automated process with Industry 4.0 data collection requires substantial planning, especially identifying potential bottlenecks. A bottleneck can have a significant impact on the efficiency of manufacturing processes and can markedly increase the time and expense of production, thus reducing profits. Given that manufacturing processes comprise a series of stages, process efficiency depends on each of these stages working in harmony. As such, the introduction of Industry 4.0 automation at any one stage can result in significant effects on upstream and downstream stages.
For example, if automation of a single stage of an eight-stage manufacturing process slashes production time at stage 4 from 268 hours to 14 hours, this change will bring significant improvement to productivity and profitability, but only if the organization is able to support necessary changes in the upstream and downstream processes. In this example, if stage 4 is the only stage that undergoes changes, stage 4 will overwhelm stage 5 and outpace stage 3, so stage 4 will come to a halt as it waits for stage 3 and stage 5 to catch up. This is an extreme example, but nevertheless it is derived from an industry case study, and it illustrates that upgrading one stage isn’t enough.
To identify bottlenecks, and thus generate major performance improvements, a thorough process review must include:
- Accumulations of work in process (WIP) – The largest amount of WIP identifies the process or stage that is the largest bottleneck.
- Wait times – Any that are much above average highlight additional bottlenecks.
- Throughput – Analyzing the output of each stage identifies that which has the greatest effect on the overall throughput.
Preventing Bottlenecks Before Automation
The plan must include a work flow based on the integration plan, and it must allocate ownership at each stage—maintaining current work flow while new equipment is installed; commissioning the equipment; and training the staff on how the new equipment works and its role in the process.
Map Out the Plan. Changes need plans, and plans depend on people. If key stakeholders aren’t engaged, change can quickly become detrimental. The first order of business is to create an environment of cooperation; the second is to divide responsibilities. Bear in mind that the plan for automation integration must be transparent, visible, actionable, comprehensive, and long-term. Automation projects are most often unsuccessful because they are too short-term in focus. Ensure the plan looks far enough ahead to consider how the integration of automation might impact upstream and downstream processes, including part validation or quality control.
Set Benchmarks. Industry 4.0 auto-mation is an investment. As such, measuring its effectiveness is a matter of determining the return on investment. This requires documenting benchmarks at each stage, before and after implementation. This helps the executive team determine productivity gains, and it casts light on new bottlenecks that result from flaws in the process or unexpected circumstances.
Overcoming Bottlenecks After Automation
Even with careful planning, unexpected circumstances and flaws in the process can arise that must be identified and corrected. Several strategies can be implemented to manage bottlenecks after automation:
- Redistribute resources - Automation provides the ability to transition personnel to other value-added roles and provides the foundation to expand product and service offerings. In addition, redistributing existing resources usually frees some human capital, making more employees available to engage in the analysis and decision-making needed to further refine the plan.
- Outsource - Review and consider the feasibility of having materials prefabricated off-site. If an outside supplier can comply with your quality control standards, outsourcing can alleviate bottlenecks by removing cumbersome stages of the manufacturing process and result in significant time savings.
- Review operation schedules - If a manual stage of the process consistently or continuously causes a bottleneck, rearrange the process so the stage in question can operate for longer periods, even running continuously, if possible. Using additional shifts or overtime may be necessary, and while such steps don’t reduce cycle time, they help to create a smoother flow.
- Continue to automate - Automation is not necessarily an isolated activity. Every initial automation integration causes disruptions in process and systems. A documented review and change- management process are the next steps to handle any additional changes required after an integration, which can include another integration at another stage.
- Reduce downtime - While functional bottlenecks are problematic, downtime bottlenecks can be extremely detrimental to the bottom line. The potential cost of downtime is significant; research conducted in 2017 found that machine downtime cost manufacturers in the U.K. more than $2.67 billion every year. Having staff on-hand with the knowledge to conduct in-house repairs, an inventory of spare parts, and a solid working relationship with suppliers to ensure parts are ready when necessary are imperative in reducing downtime.
A Case Study in Automation
The K-TIG system uses gas tungsten arc welding technology and provides a variety of Industry 4.0 integration options from semiautomated to fully connected, with peripheral technologies having roles in either master or slave capacity. The system handles routine welds, freeing up welders to focus on specialized, custom, or unique welds that require dexterity, versatility, and judgment. Because it can force a keyhole through material up to ½ in. thick, it provides single-pass, full-penetration welds that don’t require weld preparation or postweld treatments.
A pipeline fabrication project in Argentina demonstrated the system’s benefits. The Acueducto Gran San Juan is a 30-mile pipeline built to transport drinking water to San Juan in Argentina. Of the 30 miles, approximately 9 miles involve stainless steel pipe 63 in. dia. and 3/8 in. thick.
The contractor handling the stainless steel portion, Industrias Metalurgicas Jaime s.r.l., developed a purpose-built facility in San Juan and planned the processes around K-TIG units for performing both the longitudinal and circumferential welds. Following the initial rolling and tacking of the material, the keyhole welding units performed the longitudinal welds. When several lengths were ready, they were joined by circumferential welds.
In its plan to use conventional welding technology, Industrias Metalurgicas Jaime estimated that it would weld the 1,300 pipes it needed for this project over 720 days. After reviewing the productivity of the keyhole welding system, it revised this estimate to 162 days. This represents a reduction of welding time by more than 75% and is an example of the importance of coordinating upstream and downstream activities around a newly automated processing stage.
About the Author
Bill Kelly
Building 5, 9 William Street Mile End
Adelaide, South Australia, 5031 Australia
+61 8 7324 6800
About the Publication
subscribe now
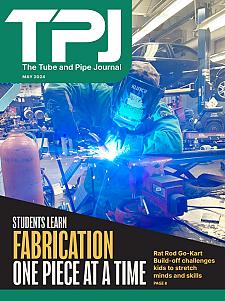
The Tube and Pipe Journal became the first magazine dedicated to serving the metal tube and pipe industry in 1990. Today, it remains the only North American publication devoted to this industry, and it has become the most trusted source of information for tube and pipe professionals.
start your free subscription- Stay connected from anywhere
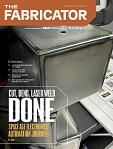
Easily access valuable industry resources now with full access to the digital edition of The Fabricator.
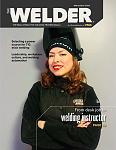
Easily access valuable industry resources now with full access to the digital edition of The Welder.
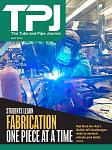
Easily access valuable industry resources now with full access to the digital edition of The Tube and Pipe Journal.
- Podcasting
- Podcast:
- The Fabricator Podcast
- Published:
- 04/16/2024
- Running Time:
- 63:29
In this episode of The Fabricator Podcast, Caleb Chamberlain, co-founder and CEO of OSH Cut, discusses his company’s...
- Trending Articles
Zekelman Industries to invest $120 million in Arkansas expansion
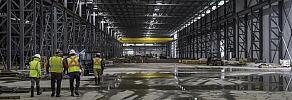
3D laser tube cutting system available in 3, 4, or 5 kW
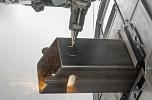
Corrosion-inhibiting coating can be peeled off after use
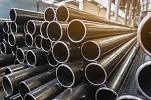
Brushless copper tubing cutter adjusts to ODs up to 2-1/8 in.
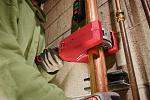
HGG Profiling Equipment names area sales manager
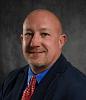
- Industry Events
16th Annual Safety Conference
- April 30 - May 1, 2024
- Elgin,
Pipe and Tube Conference
- May 21 - 22, 2024
- Omaha, NE
World-Class Roll Forming Workshop
- June 5 - 6, 2024
- Louisville, KY
Advanced Laser Application Workshop
- June 25 - 27, 2024
- Novi, MI