- FMA
- The Fabricator
- FABTECH
- Canadian Metalworking
Categories
- Additive Manufacturing
- Aluminum Welding
- Arc Welding
- Assembly and Joining
- Automation and Robotics
- Bending and Forming
- Consumables
- Cutting and Weld Prep
- Electric Vehicles
- En Español
- Finishing
- Hydroforming
- Laser Cutting
- Laser Welding
- Machining
- Manufacturing Software
- Materials Handling
- Metals/Materials
- Oxyfuel Cutting
- Plasma Cutting
- Power Tools
- Punching and Other Holemaking
- Roll Forming
- Safety
- Sawing
- Shearing
- Shop Management
- Testing and Measuring
- Tube and Pipe Fabrication
- Tube and Pipe Production
- Waterjet Cutting
Industry Directory
Webcasts
Podcasts
FAB 40
Advertise
Subscribe
Account Login
Search
Pressure-testing pipe on a small scale to 60,000 PSI
Hand-held peripherals provide portability, versatility for challenging testing situations
- By Eric Lundin
- December 21, 2021
- Article
- Tube and Pipe Fabrication
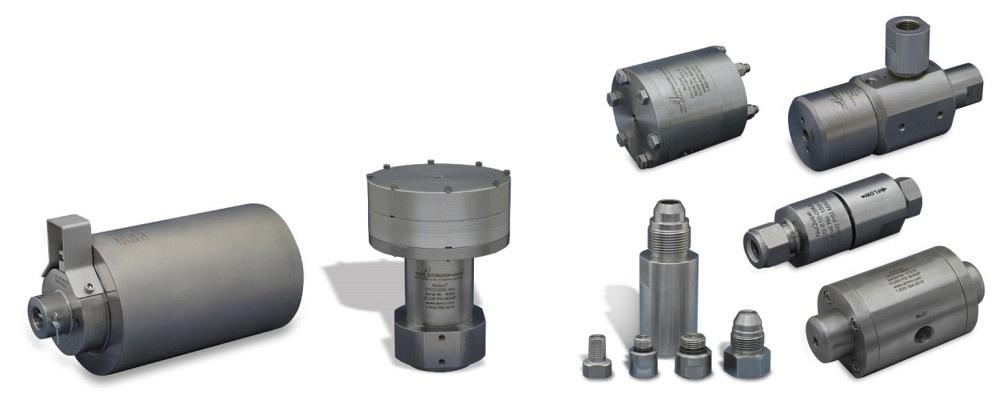
Airmo augments its line of quick disconnects with an extensive line of valves (shown here), swivels, and accumulators. Images: Airmo
Imagine three military pilots flying deep behind enemy lines on a ground attack mission. The target is a warehouse known for storing weapons and munitions. The pilots aren’t flying the fastest, flashiest, or stealthiest of aircraft, but they’re up to the task. The combat range is more than 400 miles, they cruise at nearly Mach 1, and they can jam enemy radar effectively, allowing them to get in and out undetected. They have laser-guided bombs for the mission, air-to-air missiles for defense, and each has a rotary cannon that fires 20-mm shells in case they run low on missiles.
Suddenly, one of the pilots drops out of the formation and follows at a distance. Maintaining radio silence, he doesn’t make the bombing run, but he does follow the others back to the base, and only then does he reveal what went wrong: Although the aircraft checked out in preflight and most of the flight went well, a warning light indicating an electrical fault came on as they approached the target.
Later, during a careful once-over of the electrical system, the crew finds a sheared wire and a short length of scrap tubing in one of the wings. It appears that the tube had been rolling around inside the plane and had gotten wedged against a wiring harness, and the repeated stresses of takeoffs, landings, and flight maneuvers had provided just enough motion between the pipe’s cut end and the wires to shear one of them, causing a short circuit.
One of the members of the maintenance team replaced a hydraulic line a few weeks back. Did the technician cut the tube to length before pressure-testing the line, and could this repair action be the source of the rogue length of tube?
Stress-free Pressure and Leak Testing
Tube and pipe products can be evaluated for fitness of service in a variety of ways, both destructive and nondestructive. A tensile test measures strength, tests such as Brinell or Rockwell determine hardness, a crushing process verifies the weld’s integrity, a pressure test checks for leaks or strength.
These sound simple enough, and for some applications, the tests indeed might be fairly straightforward. However, as the pipe’s integrity becomes more critical, the tests and the equipment used to carry them out become increasingly sophisticated. And, as the pipes grow in length and diameter, the testing apparatus for each sort of test grows as well.
In many cases, the tube or pipe is tested where it’s made or where it’s fabricated—in a manufacturing facility. That’s usually not difficult, the available space is adequate, the steps are clearly defined, and any preparation steps such as material handling, squaring the ends, and deburring are worked out in advance.
In other cases, it’s not so simple. Tube and pipe often are tested in the field, where they are put to use. This can be anywhere. The heat-transfer tubing in an air-conditioning system at a residence or a business has to be tested after a repair or a replacement. Pipes and tubes used in oil exploration and extraction have to be tested at the rig (land-based and offshore). A newly installed hydraulic line deep inside an aircraft has to be tested in place.
For many such testing situations, especially in which space is limited, the power source has to be mobile and all of the accessories—swivels, connectors, valves, accumulators, and regulators—have to be as compact as possible.
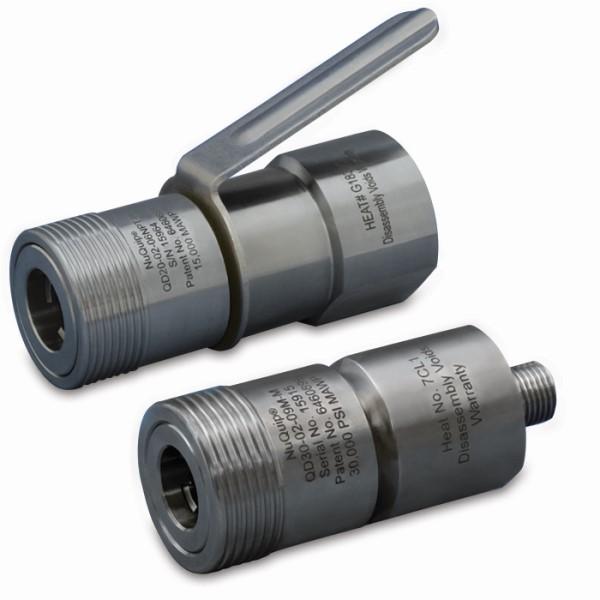
Airmo’s NuQuip product line includes quick disconnects rated up to 60,000 PSI. Despite establishing enough grip to withstand this much pressure, they are engineered to preserve the tube’s integrity.
Other uses for tubular components have much more demanding criteria. In many industries, the tube or pipe has to be first-rate; a failure is simply unacceptable. This goes for the automotive industry, oil and gas exploration, and aerospace manufacturing.
In these industries, the suppliers usually do everything they can to prevent the tube or pipe from leaking or rupturing, so every action must maintain the materials’ integrity. Using a common connector, one tightened with a wrench, is likely to change the tube’s diameter where the connector contacts the tube’s surface, which is the end of the tube’s integrity. Any abrupt change in diameter, even a small one, implies a stress riser. Stress risers are defects that can allow a crack to develop. A cracked pipe conveying a fluid at tens of thousands of pounds of pressure per square inch doesn’t last long.
“Every time you use a wrench to tighten a connector, you risk marking the tube,” said Harry Morán, CEO of Airmo Pressure Technologies Inc. Avoiding the use of this sort of connector is especially critical in aircraft, aerospace, and other industries that use light-wall products.
“The quick disconnect has to grip the tube, withstand the test pressure, and leave no discernable mark on the surface,” Morán said. “We’ve had the impression on steel tube measured with a scanning electron microscope, and the displacement was 4 microns from a test pressure of 40,000 PSI.”
The company makes pressure systems, check valves, relief valves, and quick disconnects for pressure tests up to 60,000 pounds per square inch. That’s an impressive amount of pressure, considering that many hydraulic systems work on 5,000 PSI. More impressive still is that the company’s quick disconnects can withstand that much pressure and remain in place despite having a very short grip length.
“In some cases, we have less than an inch of pipe to work with,” Morán said. The entire grip length might be 0.75 in.
Testing Anything and Everything
Pressure testing is carried out on nearly every pipe application imaginable, Morán said. Depending on the industry, it might be spot testing or it might be 100% testing.
Plumbing is a good example. In many cases, a plumbing leak would be little more than an inconvenience. A length of pipe or a faucet that springs a leak, if caught soon enough, wouldn’t cause a lot of damage, and the remedy wouldn’t be too expensive. Still, no plumber wants to replace a length of pipe in a new home—especially if the dry wall crew has already come through—so a common practice in the plumbing industry is to test nearly everything, Morán said.
In heating and cooling equipment, a leak can be much more expensive, so pressure testing is thorough.
“In the heating, ventilation, and air-conditioning industry, 100% testing is the standard,” Morán said. “After installing the tubing in a heat exchanger, the tube is pressurized and its diameter increases so the tube makes contact with the fins,” he said. After that, a pressure test is necessary to ensure that the tube didn’t burst. Such systems often are tested after every repair as well.
Automotive applications? Anything leaking from an automobile is likely to contribute to a wreck or a fire. Power steering fluid, brake fluid, fuel—even a small, slow leak in any of these systems can lead to a disaster. A leak in an automotive air-conditioning system isn’t as critical, but the repair is likely to be expensive. For vehicles powered by hydrogen fuel cells, testing goes beyond individual components. The entire fuel cell system is sealed and tested under pressure to check for leaks.
In the energy industry, the cost of a remedy for a leaking tube or pipe is exponentially greater than for other industries, especially if it’s offshore.
“In the energy industry, tubes used in oil and gas exploration have to be tested before they are installed and then during installation,” Morán said. “The industry uses more testing than most others because of the risks involving poor weld integrity. The industry has zero tolerance for any disruption to the flow of gas or oil. Disruptions have huge consequences.”
For offshore oil and gas exploration and extraction, the tubing is tested after it is unspooled, and it’s tested again after it is butt-welded to the previous length of tubing. The tube has to endure substantial pressure at low temperatures, and it has to resist an unending corrosion attack. The tubing often is made from a superduplex alloy, a high-strength material that is notch-sensitive.
The company’s components are designed for the testing protocols used for all of these applications, Morán said. For example, while water is a common medium for pressure testing, the company can’t rely solely on water. If the intended environment is too cold, any residual water will freeze and damage the equipment. Helium is another good medium, considering the size of the molecule and the fact that it’s inert. After pressurizing the system, the technician uses a helium sniffer to check for leaks.
“We have specialized tool models that are rated for both helium and fluids,” Morán said.
They’re also rated for use with the hydraulic fluid commonly used in the aerospace industry, which is particularly caustic, he said. The company also designs its peripherals for a somewhat extensive temperature range. They have to withstand temperatures typically encountered by aircraft at 50,000 ft. above sea level (-70 degrees F) and very hot industrial environments, which can exceed 400 degrees F.
Eliminating FOD
Considering the potential loss of life when things go wrong, the aerospace industry is probably the most thorough in its testing. A pressure tester like this can help to prevent foreign object damage (FOD). The term refers to damage caused by any debris, tool, or piece of hardware left in an aircraft or a spacecraft by accident, or anything sucked into an engine. FOD isn’t taken lightly by anyone in aviation or aerospace. Airfield and aircraft carrier personnel regularly walk the flight lines and flight decks, looking for debris. Despite every crew chief’s efforts to keep every craft airworthy 100% of the time, fasteners occasionally fall off ,and parts are known to break off, a hazard to the next aircraft that comes along. It doesn’t take a large piece of debris to tear up the inside of an engine and force an emergency landing or, worse, cause a crash.
“On an aircraft, the pressure test on a hydraulic line often takes place in the empennage, where the technician has very little room to work,” Morán said, referring to the tail section of an aircraft. After replacing a hydraulic line that controls the rudder or an elevator, the technician has to do a pressure test to verify that the line is leakproof.
“Usually there’s no room for installing a safety cage, and the quick-disconnect might be mere inches away from the technician.” At 30,000 PSI, a quick-disconnect that slips off the tube turns into a quick missile, so it has to stay put.
“This industry simply cannot tolerate a leak,” Morán said. “A leak can injure personnel and wreak havoc on the aircraft. It damages wire, motors, and nearly everything else in its path,” he said.
This is why a quick-disconnect that leaves no trace of its presence is necessary. Tightening a fitting with a wrench on an aircraft tubing system can be especially problematic. Every unnecessary pound added to an aircraft or a space vehicle is one less pound that can be dedicated to something necessary—say, fuel, cargo, or ammunition—so the tubes usually have the lightest walls possible.
Could the technician use another pressure-testing system, perhaps one that crimps the end a bit, and merely cut the end off after the test is complete? In a word, no. This is where FOD comes in.
First, the technician would have to account for the cut-off end when the job was finished. If he didn’t, meaning that the cut-off end was left behind in the aircraft, FOD could result. Even the simplest of aircraft have countless moving parts, so aircraft technicians must be scrupulous in keeping track of everything they bring into, and remove from, every aircraft. Every tool, every part they replace, and every fastener must be accounted for. While a short length of pipe clipping a wire isn’t the most likely scenario, it’s not out of the question.
Second is a much more problematic issue. The technician would have to deburr the cut end, and burrs tend to go everywhere. He’d have to remove all the stray bits of metal, both inside the pipe and elsewhere in the aircraft.
So in the case of an aircraft application, a quick-disconnect is the way to go. Without cutting and deburring, the risk of FOD from pressure-testing a hydraulic line is zero, and the subsequent flights are much more likely to go without a hitch, whether they are delivering passengers, cargo, or ordnance.
About the Author
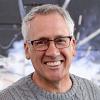
Eric Lundin
2135 Point Blvd
Elgin, IL 60123
815-227-8262
Eric Lundin worked on The Tube & Pipe Journal from 2000 to 2022.
About the Publication
Related Companies
subscribe now
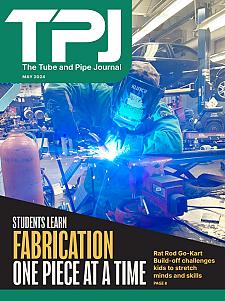
The Tube and Pipe Journal became the first magazine dedicated to serving the metal tube and pipe industry in 1990. Today, it remains the only North American publication devoted to this industry, and it has become the most trusted source of information for tube and pipe professionals.
start your free subscription- Stay connected from anywhere
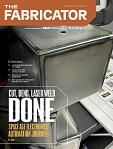
Easily access valuable industry resources now with full access to the digital edition of The Fabricator.
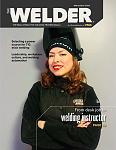
Easily access valuable industry resources now with full access to the digital edition of The Welder.
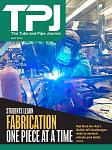
Easily access valuable industry resources now with full access to the digital edition of The Tube and Pipe Journal.
- Podcasting
- Podcast:
- The Fabricator Podcast
- Published:
- 04/16/2024
- Running Time:
- 63:29
In this episode of The Fabricator Podcast, Caleb Chamberlain, co-founder and CEO of OSH Cut, discusses his company’s...
- Trending Articles
Zekelman Industries to invest $120 million in Arkansas expansion
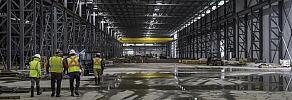
3D laser tube cutting system available in 3, 4, or 5 kW
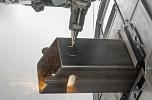
Corrosion-inhibiting coating can be peeled off after use
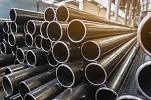
Brushless copper tubing cutter adjusts to ODs up to 2-1/8 in.
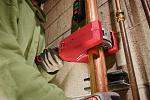
HGG Profiling Equipment names area sales manager
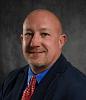
- Industry Events
16th Annual Safety Conference
- April 30 - May 1, 2024
- Elgin,
Pipe and Tube Conference
- May 21 - 22, 2024
- Omaha, NE
World-Class Roll Forming Workshop
- June 5 - 6, 2024
- Louisville, KY
Advanced Laser Application Workshop
- June 25 - 27, 2024
- Novi, MI