- FMA
- The Fabricator
- FABTECH
- Canadian Metalworking
Categories
- Additive Manufacturing
- Aluminum Welding
- Arc Welding
- Assembly and Joining
- Automation and Robotics
- Bending and Forming
- Consumables
- Cutting and Weld Prep
- Electric Vehicles
- En Español
- Finishing
- Hydroforming
- Laser Cutting
- Laser Welding
- Machining
- Manufacturing Software
- Materials Handling
- Metals/Materials
- Oxyfuel Cutting
- Plasma Cutting
- Power Tools
- Punching and Other Holemaking
- Roll Forming
- Safety
- Sawing
- Shearing
- Shop Management
- Testing and Measuring
- Tube and Pipe Fabrication
- Tube and Pipe Production
- Waterjet Cutting
Industry Directory
Webcasts
Podcasts
FAB 40
Advertise
Subscribe
Account Login
Search
Refueling, repairing, refurbishing, redeploying a supercarrier
Navy contractor Newport News Shipbuilding overhauls the USS Abraham Lincoln for second half of its life cycle
- By Eric Lundin
- February 10, 2016
- Article
- Tube and Pipe Fabrication
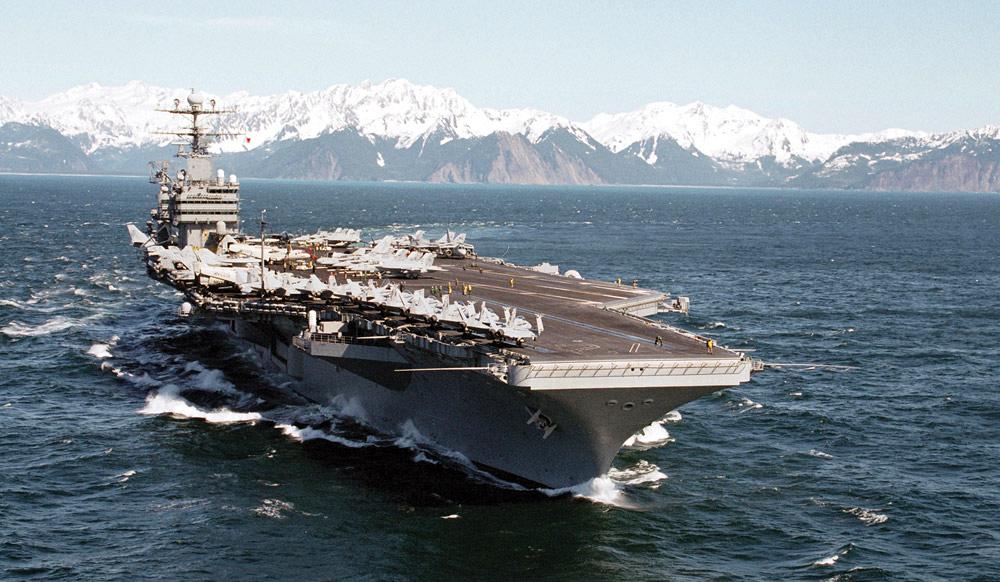
USS Abraham Lincoln prepares for flight operations in the Gulf of Alaska as part of a joint training exercise, Northern Edge. U.S. Navy photo by Photographer’s Mate 3rd Class Kittie VandenBosch.
A modern aircraft carrier is nothing short of immense. The current fleet of U.S. carriers, the 10 ships in the Nimitz class, measure slightly more than 1,000 feet long and 250 ft. wide. Two Westinghouse A4W nuclear reactors generate 550 megawatts of electricity—enough to run all of the onboard systems, fire the steam-powered catapults to launch the aircraft, and provide 260,000 shaft horsepower. Propulsion is provided by four screws that measure 21 ft. across and weigh 30 tons each. Two rudders that measure 29 by 22 ft. steer the ship. Despite its vast size, a Nimitz-class boat moves quickly, achieving a top speed of 30 knots (35 miles per hour).
At the same time, a supercarrier makes efficient use of space. Pilots manage takeoffs and landings that are incredibly abrupt, using about 20 percent of the distance they would use on land. Also, the staff is packed in pretty tight. Major cities like Chicago and Boston have 13,000 residents per square mile, but an aircraft carrier is off the chart with an equivalent of 600,000 people per sq. mile. Granted, the ship isn’t the permanent home to the 5,000 sailors who staff it, but after seven or eight months at sea, it probably feels like it’s a permanent home.
Of course, these are just the details. An aircraft carrier’s mission is to project military power anywhere, anytime. It carries 85 to 90 aircraft and is equipped with dozens of systems and subsystems that make up its offensive and defensive capabilities. A half-dozen radar systems support the air wing’s mission by providing air search capability, target acquisition, air traffic control, and landing assistance. A trio of systems for shooting down hostile aircraft and missiles provide the necessary defensive capacity. It would have some vulnerability if it deployed alone, but it travels with a small armada of vessels that support, supply, and defend it, which boost and expand its role. It also carries quite a bit of machinery for repairs and fabricating systems or assemblies as needed (see Figure 1).
Despite their many capabilities, modern aircraft carriers need a midlife overhaul. Technologies change rapidly, so the original equipment—radars, weapons, catapults, antisubmarine warfare systems, and so on—needs attention after 25 years or so. A maintenance action known as refueling and complex overhaul (RCOH), which lasts about four years, is a mix of repairs and replacements, bringing the ship’s capabilities up-to-date and preparing it for the second half of its operational life. In March 2013 the USS Abraham Lincoln, hull designation CVN 72, reported to Newport News Shipbuilding in Newport News, Va., for its midlife RCOH.
How much has technology changed since CVN 72 first went to sea? The digital revolution wasn’t anything new at that time, but it was still growing rapidly. A typical integrated circuit (IC) chip in that year, 1988, had about 1 million transistors; today’s ICs have 2.6 billion. Many items that are digital today were analog then—film cameras and corded telephones, for example—and in 1988 the World Wide Web hadn’t yet been developed. If you can imagine a world without cell phones, laptop computers, and Wi-Fi, you can imagine the technology used in building CVN 72.
A specific upgrade is the Navy’s Consolidated Afloat Networks and Enterprise Services (CANES), a communication system that consolidates five legacy networks into one. Its focus is enhanced connectivity for command, control, communications, computers, and intelligence (C4I) network systems, an improvement in both capability and affordability across the fleet. In addition to increasing the Navy’s operational effectiveness, it provides better quality of life for deployed sailors. Nobody would expect a sailor to disconnect from friends and family during a deployment; CANES allows Internet access via satellite.
Another upgrade concerns the aircraft assigned to the carrier. The USS Abraham Lincoln is undergoing upgrades to be the first Nimitz-class carrier to service the Lockheed Martin F-35 Lightning II, also known as the Joint Strike Fighter.
In other words, the word complex doesn’t really do this process justice. The process is akin to disassembling a 100,000-piece jigsaw puzzle, throwing away half of the pieces, making 50,000 new pieces, and fitting the new ones to the old ones to make a half-new, half-old puzzle. When the process is finished, nearly every component on every system inside the ship will have been inspected and repaired, refurbished, or replaced. CVN 72 will look the same on the outside, but it will be completely new on the inside.
A Strong Legacy in Newport News
Newport News Shipbuilding (NNS), owned by Huntington Ingalls Industries, is guided by the words of founder Collis Potter Huntington: “We shall build good ships here. At a profit if we can, at a loss if we must, but always good ships.” A railroad magnate who, with three partners, planned and built the first transcontinental railroad, Huntington wasn’t intimidated by the scope of operations involved in running a shipyard. NNS’s lengthy experience includes building and repairing commercial and Navy ships, focusing these days solely on nuclear-powered aircraft carriers and submarines.
Almost as old as the shipyard is NNS’s Apprentice School, which provides the shipyard a steady stream of craftsmen and leaders in 19 trades and eight optional programs. The programs, which run from four to eight years, consist of both classroom instruction and on-the-job training, and culminate in a certificate, an associate degree, or an engineering degree. All apprentices are employed from their first day of school, and for many, it turns into a longstanding career. However, after students graduate, continuing their employment at NNS is a choice, not a requirement.
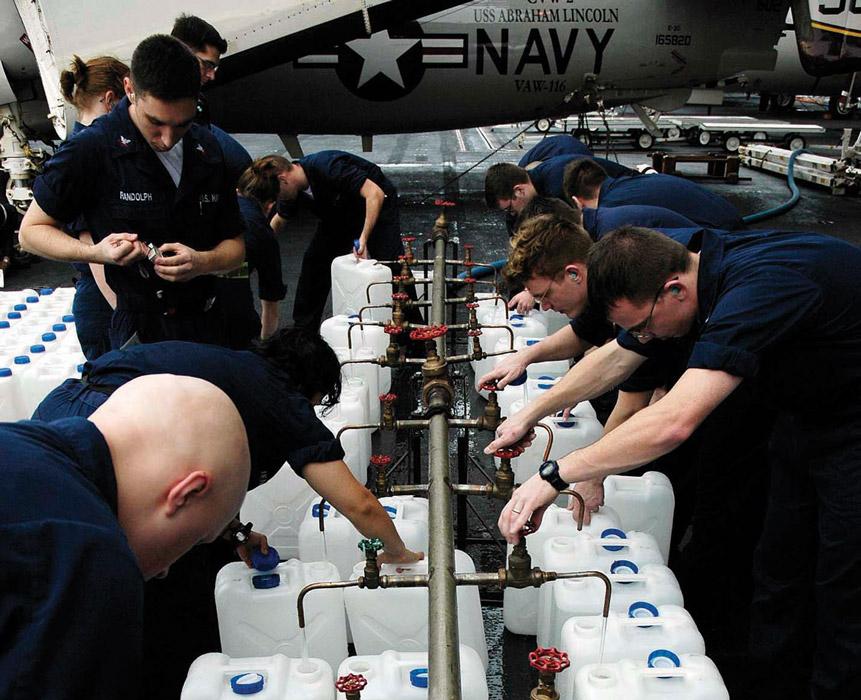
Figure 1
Sailors onboard the USS Abraham Lincoln fill jugs with purified water to support relief efforts
in the wake of the tsunami that struck Southeast Asia in 2005. The Lincoln’s Repair Division
constructed the manifold in eight hours. U.S. Navy photo by Photographer’s Mate Airman
Jordon R. Beesley.
“Our perspective is that we don’t want to keep a graduate here if the graduate doesn’t want to be here,” said NNS Communications Manager of Media Relations Christie Miller. If a student comes to realize that a shipyard career isn’t to his or her liking, the graduate is free to pursue a job elsewhere with no obligation to NNS. Most make a career at the shipyard. A decade after graduation, the retention rate at NNS is more than 80 percent.
“Some leave, but most stay, and a good portion of Apprentice School graduates move into leadership positions in the company,” said NNS Vice President of Manufacturing and Supply Chain Management Robert Hogan, himself an AS graduate.
Having a pipeline in which AS graduates work as mentors to AS students sounds like a great way to keep tribal knowledge alive, but it’s much more than that. Because many NNS executives, managers, and supervisors once worked on the shop floor, they know where the good ideas come from—the shop floor. NNS puts those ideas to good use, incorporating them into the company’s written procedures and processes, a sustained effort that keeps the company moving forward.
The same goes for new equipment. The company is known for being frugal, in some cases keeping equipment running well past its prime. When repair parts get too hard to find and the downtimes become so lengthy that they jeopardize delivery schedules, the NNS management team doesn’t start by arranging a meeting with equipment vendors. NNS calls a meeting with its craftspeople to learn about the machine’s specific capabilities and how well they do, or don’t, match up to NNS processes. After selecting a vendor, this team meets with the machine builder to determine what it needs in terms of off-the-shelf features and options or, if need be, a custom-made machine.
Manufacturing
Most fabricators would be at home in the fabrication and machine shops at NNS. The various departments use machines for cutting, bending, welding, turning, and machining that are no different than you’d find in any other fabrication shop anywhere in the U.S. You might see a machine that requires manual setup once in a while, but nearly everything at NNS has CNC.
Much more striking, of course, is how nearly everything at NNS is different from a fabrication shop. A key differentiator is the sheer scale of operations.
While many fabricated items are made from light-gauge material, much of the work at NNS is extremely heavy-duty. Something like a toolbox or a storage locker doesn’t need much extra durability, but a hatch that separates two compartments on a boat weighs far more than a door that separates two rooms in a building. The ship’s structure has to endure the stresses caused by the ship’s movements—pitch, roll, heave, surge, and sway—and damage incurred during hostilities, so strength is the key. Most of the materials are high-yield-strength ballistic steels often several inches thick (NNS staff is understandably tight-lipped about specifics).
Nearly every assembly has a handful of gussets, brackets, braces, or reinforcements of some sort. The strength and weight of the components is mind-boggling when compared to items used in off-road automotive or even heavy machinery, as is all the work that goes into the components, but considering the application, it’s easy to understand why. An aircraft carrier’s mission is risky at best. The staff’s goal to make good ships has another motivation, a personal one. NNS staff members walk past the ship and have face-to-face contact with sailors every day. Their ship, their customers. Every day.
Another difference is how NNS saves money for the Navy. Fabricators always look for ways to cut costs, but a Navy contractor has a rule of thumb that governs everything it does: 1-3-8. For every dollar spent on a weldment, assembly, or repair done in a shop, the equivalent work done dockside would cost about $3, and if performed on the ship would cost $8. When NNS does more on land, it costs taxpayers less. An RCOH also relies on work done by sailors at the Light Industrial Facility (see Figure 2).
“We’re moving to digital shipbuilding,” said Manufacturing Superintendent Steve Cataldo, who brought 15 years of automobile manufacturing experience to the shipyard. “We don’t use paper drawings. We download the drawings right to the machines and start making parts,” he said.
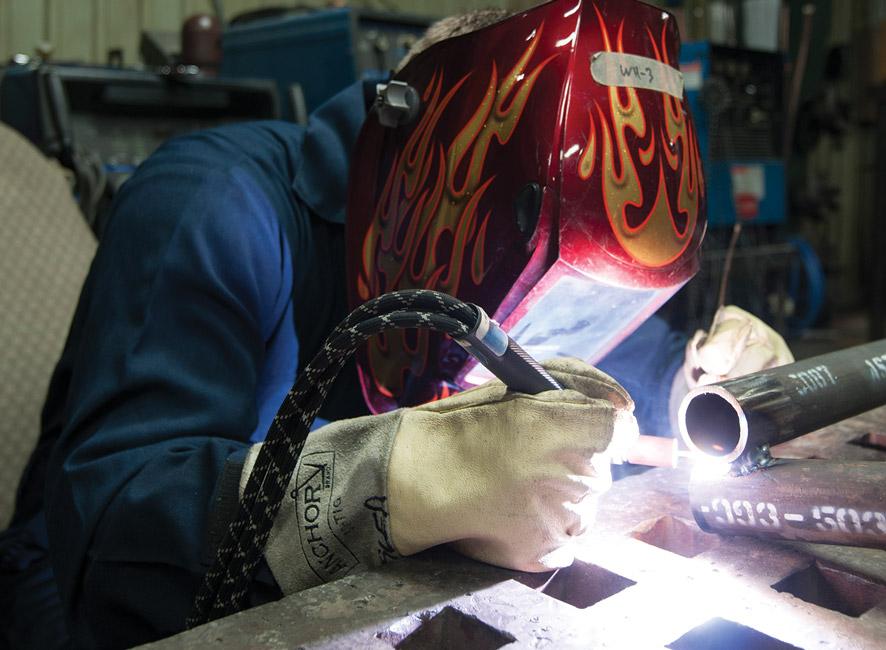
Figure 2
Hull Technician Fireman Cody Hosler, assigned to the aircraft carrier USS Abraham Lincoln
(CVN 72), welds a pipe assembly at the Light Industrial Facility. Welding in port keeps sailors’
skills sharp and is an integral part of the 23 million man-hour effort that goes into an
RCOH. U.S. Navy photo by Mass Communication Specialist Seaman Ashley Raine Northen.
Because an aircraft carrier doesn’t have symmetry in any direction, port to starboard or bow to stern, many of the components and assemblies are one of a kind. In days gone by, a contractor used blueprints to determine the dimensions of an assembly and the locations of all the features, but making a complex assembly in the shipyard always came with a risk that they wouldn’t fit precisely.
These days CAD software and CNC have removed any doubt about the dimensional integrity of every component that goes into an assembly. If the distortion caused by the heat from welding were to cast any doubt on the assembly’s dimensions, verification with a coordinate measuring machine is a simple matter. Finally, when tolerances are extremely tight, the contractor can use recent photogrammetry data from the ship, rather than blueprints, to verify the fit-up before taking the assembly aboard for installation.
These technologies support NNS’s efforts to drive costs down by making sure that assemblies need no rework—they fit the first time, every time—and they also help in the 1-3-8 guideline.
Adding another layer of complexity is that, even within a class of aircraft carriers, the ships aren’t identical. Lessons learned during the build process can lead to design changes from one ship to the next. Additionally, length of deployment, mission, and environmental factors are different for every ship and play a role in the ship’s condition at the time of its RCOH.
Structural Fabrication. Just as no single aspect of an aircraft carrier is more important than any other—the catapult is just as important as the arresting gear, and the newest recruit’s duties are just as necessary as the captain’s—no single department at NNS is any more important than any other. That said, quite a bit of the activity revolves around the Structural Fabrication and Assembly Division (SFA). The SFA cuts and forms plates and structural parts for new construction, repair, and RCOHs. When starting a project, the SFA’s first activity is “flame on steel,” referring to the first burst of plasma that sets the project into motion.
“The SFA is three times the size of an average Home Depot,” said Director of Structural Fabrication and Assembly Barry Fallon. It’s called a fabrication shop, but like much else in shipbuilding, that’s an understatement. It employs 200 craftspeople that cut and form the steel to make the bows, sterns, hulls, and bulkheads. CNC robotic systems up to 110 ft. long use high-definition plasma and oxyfuel to cut steel up to 8 in. thick. After cutting, the steel then is formed on vast hydraulic presses, the largest of which develops 5,000 tons of force.
The parts then are transported to the other shops to become subassemblies, large panels, and then units. The Steel Production Facility is the largest of the other shops, at more than 500,000 sq. ft., and is equipped with four production lines that produce panels up to 65 ft. wide. These units then are finished out with machinery and the electrical, pneumatic, and hydraulic support systems.
Welding. Welders at the shipyard have an extensive library of welding certifications in a variety of processes in low- and medium-carbon steel, chrome-moly steel, nickel-molybdenum-chromium alloys, and titanium-based alloys for the many shipboard applications—structural elements, pipe, pressure vessels, castings, and machinery.
Fabricating a bulkhead is a typical welding application at NNS. Like an ambitious homeowner thinking about tearing down a wall to change a home’s floor plan, an RCOH often includes removing bulkheads to accommodate the ship’s midlife updates. Fabricating new bulkheads is an extraordinary undertaking.
“When you build a wall for a house, you put up the framing, then fasten the drywall to the studs,” Hogan said. “Our process is the opposite. We lay out the plate, then set the reinforcements in place.”
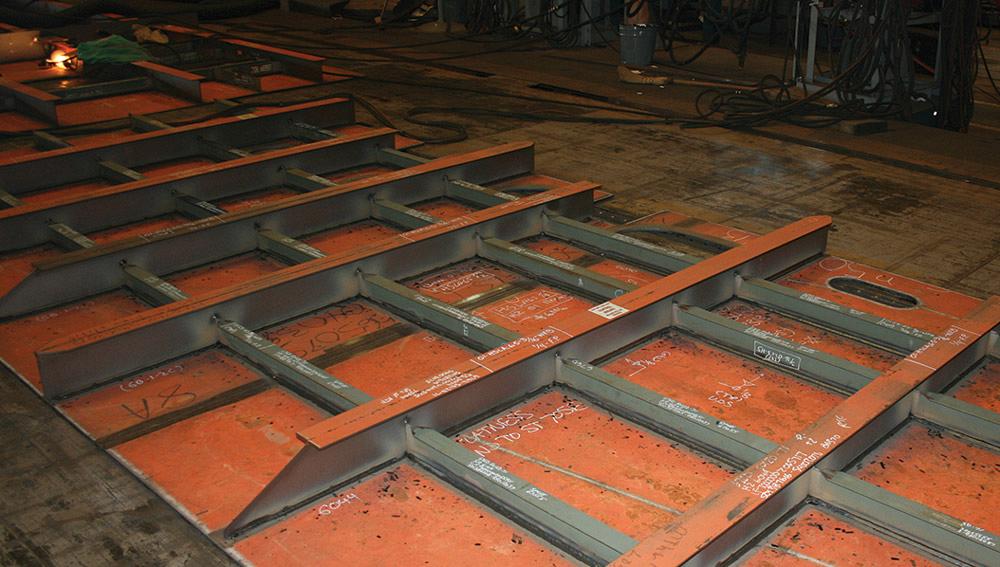
Figure 3
For welding bulkhead stiffeners, NNS relies on robots. “A robot can be programmed for
precisely the right amount of heat input, travel speed, and the specific weld sequence to
keep distortion to a minimum,” said NNS Director of Structural Fabrication and Assembly
Barry Fallon. In addition to removing the drudgery from this task, the result is a betterquality
bulkhead. Photo by Eric Lundin.
On the surface it seems simple, but in reality, making bulkheads is difficult. It’s extremely monotonous; welding straight lines all day long lacks variety, putting it beyond the concentration of most welders (see Figure 3). NNS uses two welding robots for this task.
NNS does a lot of welding to join plates before robots weld the stiffeners in place. NNS uses three processes, depending on the plate thickness. All three are examples of a process crossing from one area to another.
The most arduous of the processes starts with a double bevel made by a plasma torch followed by a weld to fill in the beveled area. After flipping the plate and using carbon-arc gouging to get down to sound metal, the welder then welds the second side. One of the alternative processes starts with a U-groove milled along the faces to be joined. The plates have a tight fit-up, and after welding the first side, the welder doesn’t need to gouge the second side—it’s ready to weld. The third process relies on a precise weld joint and a copper backing bar. As the welder works along the top side of the plates, filling in the top side, molten weld metal fills in the bottom side. When finished, the top side is essentially indistinguishable from the bottom side. No flipping, no gouging, no second weld.
NNS used all three processes in the 1990s to build commercial ships. Since the processes received Navy approval, the company has put them to use in aircraft carriers and submarines.
Fabrication. NNS’s experience in laser cutting is similar to that of many fabrication shops: Just a few months after installation, the laser’s spare capacity shrunk rapidly.
In many cases, fabricators justify a laser purchase because the laser has a way of making complex parts simple. Often a component is too complicated to make with conventional machines, but a laser can do the trick; or a part requires many operations, and the laser eliminates material handling and turns out a part with better tolerances; or the laser speeds the component development cycle by eliminating the cost and time associated with ordering hard tooling. In some cases, a single part fits all of these descriptions. However, these complexities aren’t the limit of the laser’s usefulness.
As time goes on, other parts seem like good candidates for the laser. Small parts. Simple parts. Troublesome parts. It doesn’t take long until the laser operators find themselves programming a large and steadily growing number of components, and this is precisely what happened at NNS. Just a short time after investing in a CO2 laser, the company is researching a second machine, a fiber laser.
Machining. The machine shop is an apprentice’s dream come true. The mix of materials, component configuration, and part complexity provide enough variety to keep an apprentice on his toes, and eager for more, for years. The variety of alloys is endless: cold-rolled steel, INCONEL® alloys, nickel-copper alloys, Hastelloy® alloys, castings, overlays. Many parts have unique features and more gussets and reinforcements than seem possible. Finally, because everything on an aircraft carrier has an important role, many of the tolerances are critical.
“It’s not your typical machine shop,” Hogan said. “We don’t machine many individual parts. We subcontract a lot of that work.” NNS welders turn those components into welded assemblies, and this is when the shipyard’s machine shop gets involved.
“We take big, complex weldments and castings, and we do intricate and often close-tolerance machining,” said NNS Machine Shop Superintendent Joey Perry.
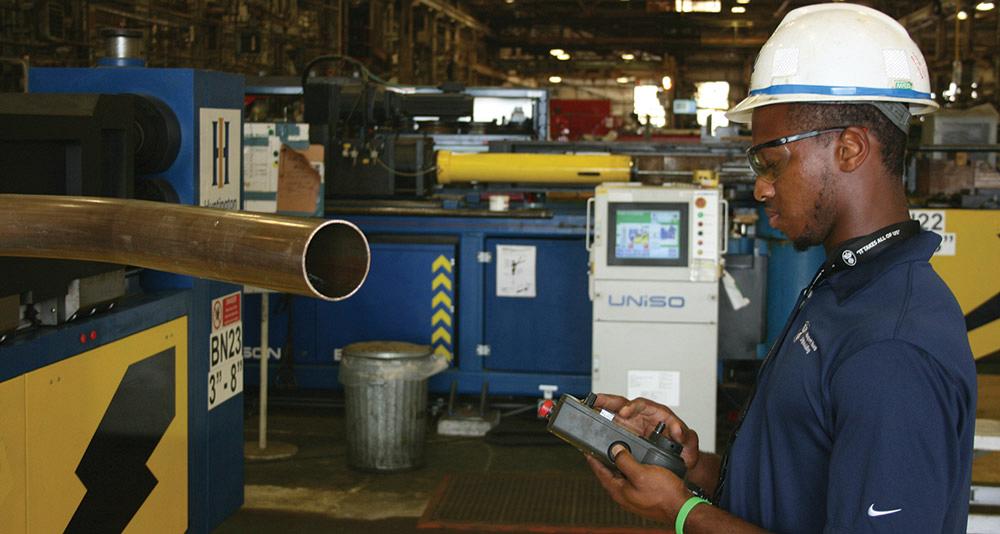
Figure 4
Jeromy Rich uses NNS’s latest pipe bender, an electric unit driven by servomotors. It has a
suite of modern features, including a laser measurement system for springback correction
and a remote pendant control. Photo by Eric Lundin.
- The sheer size of some of the assemblies is almost beyond belief. Each stern tube shaft, a 55-ton forging, arrives at NNS trepanned and ready for machining and balancing for bearing sleeves. The machine shop makes three bearing sleeves for each stern tube shaft and takes care of the heating and assembly. Each aircraft carrier needs four such shafts.
- The machine shop also manufactures the propeller shafts, which are more than 65 ft. long and weigh more than 53 tons. INCONEL alloy bearing sleeves are heated and installed on the shaft before final machining. The tapers of the ship’s propellers are trial-fit to the shafts in the shop to provide a tight fit before shipboard installation. The shop also manufactures four intermediate shafts, which are 34 ft. long and weigh more than 25 tons, providing the connection between the stern tube shafts and the propeller shafts. All shaft flanges are drilled and line reamed to the mating shaft in the shop with custom-made tapered bolts ground to fit each hole to make shipboard installation easier.
- “If you can get it through the doorway, we can machine it,” Perry said. This isn’t so much about the door but about the shop’s capabilities. It’s equipped with vertical machining centers, horizontal machining centers, and lathes, all with capacities that are much more than you’d find in most machine shops.
However, the door did actually become a limitation recently when the Navy introduced a new condenser design, a 100-ton monster that wouldn’t fit through the doorway, which measured 23 ft. tall by 37 ft. wide. This problem didn’t last long. NNS increased the doorway, making it 12 ft. taller, and the machine shop team developed a process to do the necessary machining. The boast still stands.
The machinists’ contributions didn’t start with the condenser and they didn’t end there, either.
“We’re doing work for 32 different contracts today, and we have a work package for every job in the shop,” Perry said. “The work package is the basis for our process and lessons learned. It also has target information for every work center so we have a reference for our performance and we can measure how well we’re doing, which helps us to be sure that we’re continually improving. We record new ideas that our craftsmen bring forward to improve the way we do it, and that information gets worked into the master plan for each one of these items, so we have a strong program for process control and process improvement.”
The lessons learned and best practices often cross from one contract to another. Everything that seems difficult or taxing to machine on an aircraft carrier becomes just a little easier when compared to the ultraclose-tolerance work needed on submarine components. Every hatch needs to be watertight and shafts must rotate in their bearings as quietly as possible, so mating surfaces are critical.
“We also do the fitting and test the assembly, and prepare everything as much as possible in the shop to ensure the shipboard installation crew doesn’t have to do much work at all,” Perry said.
Pipe Shop. The pipe shop has been transformed over the last few decades. To say it was an unsophisticated backwater department 30 years ago would be an understatement; today it’s a state-of-the-art work center.
A photo from 30 years ago shows that the pipe shop was equipped with two old bending machines, some simple layout tools, and welding equipment. That was it. Laying out pipe runs, taking measurements, and marking for cutting or welding was done on the floor. Pipe doesn’t stack well, so the material was scattered around. Workers moved through the area by way of makeshift pathways that ran between inventory, work-in-process, and machinery.
Compared to the photo, the pipe shop is unrecognizable. It’s neat, orderly, and shipshape. It even has some of the company’s most modern machinery, and the procurement process is an exemplary case of including perspectives and opinions from NNS craftsmen in working out the details. Tube bender manufacturer Unison consulted with NNS staff to come up with an electric bender that can handle pipe up to 8 in. dia. (see Figure 4). The shipyard wanted a compact machine, with a loading height of 60 in., which led the vendor to develop a new power transmission system, one that develops 265,500 lb.-ft. of torque. NNS also wanted the versatility of making intricate, small-diameter bends on the same bender, so the machine’s design incorporates quite a bit of free space around the bending head to prevent interferences.
Because the bender has programmable, closed-loop servomotors, setup is automatic and it delivers topnotch accuracy and repeatability. It’s also equipped with a laser measurement system that automatically makes the bend correction that is always necessary to compensate for springback and often necessary when changing from one batch of raw material to the next. This saves NNS money in reducing or, in many cases, eliminating scrap. This is critical in shipbuilding because as the pipe diameter increases, the value of the raw material increases exponentially.
The NNS staff has taken quite a few strides regarding safety in the pipe shop. First, the machine’s pneumatic and hydraulic lines, which normally run across the floor and pose a tripping hazard, run under the foundation. Second, an outfeed system lowers the pipe after it’s bent. In the old days, the operator would use a crane to lift the pipe from the bender and lower it to the floor, but misjudging the pipe’s center of gravity was always a concern. Third, NNS installed an air-powered lifting system for moving the die sets, some of which weigh thousands of pounds.
The new bender gets much more use than the pipe benders got a few decades back. In those days it was common to join two lengths of straight pipe with a fitting. As time has gone on and technologies have improved, the staff at NNS and the Navy have taken advantage of 3-D modeling software and CNC to replace welded fittings with bent pipe.
“This eliminated the time and materials for fabricating the fitting, and the welding, and the nondestructive testing,” said NNS General Foreman Kenny Quinn.
“A lot of the welding fittings were done on the ship,” Quinn said. “We’d make straight runs of pipe and fittings in the shop, and then send everything to the ship and they’d put everything in place on the ship.”
They’ll never eliminate flanges, but careful planning and bending allow uninterrupted pipe runs up to 30 ft. long.
By the Numbers
Every aircraft carrier has an air officer, also known as the air boss, whose responsibility encompasses all aircraft operations on the hangar deck, on flight deck, and in the air within a 5-mile radius of the ship. Overseeing the launches, landings, and nearby air traffic can be hair-raising when all goes well; occasionally the air boss has to focus all of his attention on a crisis as it unfolds in front of his eyes and has to make split-second, life-or-death decisions. It isn’t for everyone, and in many ways the job is probably more demanding than commanding the ship.
The closest NNS has to an air boss is a program director, the individual who bears the responsibility for the entire RCOH. For the USS Abraham Lincoln, the program director is Bruce Easterson and, like an air boss, his job involves managing the overall strategy of the project and an ability to dig into the details when necessary.
“An RCOH is the only time an aircraft carrier comes to the gas station,” Easterson said. “It’s a four-year process in which we recapitalize the entire carrier. We touch every space and it leaves as a brand-new ship.
“Nearly 5,000 people were working on the RCOH at the peak,” he said. “That’s a combination of sailors, Huntington Ingalls staff, and outside contractors.” The effort is about 23 million man-hours in the shipyard, 2 million on the ship, and 1 million in customer contractor teams.”
About 35 percent of all maintenance and modernization performed on the ship during its service life is carried out during the 42-month RCOH, Easterson said. The project is so vast that testing and troubleshooting the new systems take nearly a year. This isn’t to say that every maintenance task is planned to the last minute and to the last dollar. On CVN 72, NNS’s inspections revealed much more corrosion than expected in the catapult troughs.The USS Abraham Lincoln was the first carrier outfitted with a new catapult design, model C-13-2. Formally known as the Internal Combustion Catapult Aircraft Launch System (ICCALS), every catapult is examined during regularly scheduled maintenance inspections, and in the case of the Lincoln, some corrosion was evident, but the full extent wasn’t known until the catapults were torn down for refurbishment during the RCOH. The corrosion was so extensive that the remedy was much more than a repair. It required a comprehensive plan to reconstruct each catapult trough and to prevent corrosion in the future. The NNS staff engineered a plan, received Navy approval, implemented a complete rebuild, and never took its eyes off the calendar.
The corrosion affected the budget but it didn’t change the RCOH timetable.
“We realigned our resources and worked diligently to stay on schedule,” Easterson said.
Anchors Aweigh!
Nimitz-class ships go by many descriptions: 90,000 tons of diplomacy; 4.5 acres of sovereign and mobile U.S. territory; and a ship that possesses more firepower than the entire Navy had in 1945. The last one sounds like a stretch—this branch was 3 million strong in 1945—but considering the capabilities of several dozen jet-powered fighters armed with precision 21st-century weaponry, the modern state of anti-submarine warfare, the assistance of airborne command-and-control aircraft, the shield provided by electronic jamming aircraft, and all the defensive firepower the ship carries, it’s not very far from the truth.
Regardless of the description, the pride and experience of the employees at NNS are testimony that these are good boats, and the sailors deploy with confidence that they are onboard 10 of the most fearsome and durable fighting machines ever built. The NNS team includes 40 shipbuilders with more than 50 years’ experience, and every employee is guided by a second motto as powerful as Huntington’s words about building good ships: “It is my intention, and that of my fellow shipbuilders, to never send our sailors into a fair fight.”
About the Author
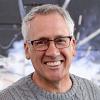
Eric Lundin
2135 Point Blvd
Elgin, IL 60123
815-227-8262
Eric Lundin worked on The Tube & Pipe Journal from 2000 to 2022.
About the Publication
subscribe now
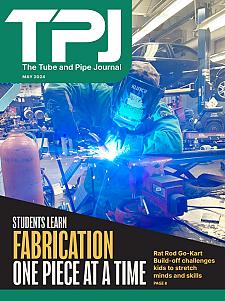
The Tube and Pipe Journal became the first magazine dedicated to serving the metal tube and pipe industry in 1990. Today, it remains the only North American publication devoted to this industry, and it has become the most trusted source of information for tube and pipe professionals.
start your free subscription- Stay connected from anywhere
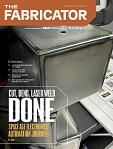
Easily access valuable industry resources now with full access to the digital edition of The Fabricator.
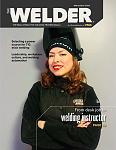
Easily access valuable industry resources now with full access to the digital edition of The Welder.
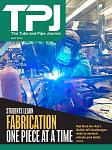
Easily access valuable industry resources now with full access to the digital edition of The Tube and Pipe Journal.
- Podcasting
- Podcast:
- The Fabricator Podcast
- Published:
- 04/16/2024
- Running Time:
- 63:29
In this episode of The Fabricator Podcast, Caleb Chamberlain, co-founder and CEO of OSH Cut, discusses his company’s...
- Trending Articles
Zekelman Industries to invest $120 million in Arkansas expansion
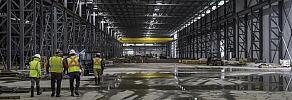
3D laser tube cutting system available in 3, 4, or 5 kW
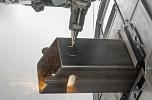
Corrosion-inhibiting coating can be peeled off after use
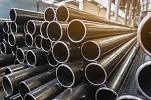
Brushless copper tubing cutter adjusts to ODs up to 2-1/8 in.
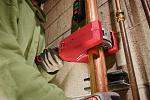
HGG Profiling Equipment names area sales manager
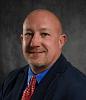
- Industry Events
16th Annual Safety Conference
- April 30 - May 1, 2024
- Elgin,
Pipe and Tube Conference
- May 21 - 22, 2024
- Omaha, NE
World-Class Roll Forming Workshop
- June 5 - 6, 2024
- Louisville, KY
Advanced Laser Application Workshop
- June 25 - 27, 2024
- Novi, MI