- FMA
- The Fabricator
- FABTECH
- Canadian Metalworking
Categories
- Additive Manufacturing
- Aluminum Welding
- Arc Welding
- Assembly and Joining
- Automation and Robotics
- Bending and Forming
- Consumables
- Cutting and Weld Prep
- Electric Vehicles
- En Español
- Finishing
- Hydroforming
- Laser Cutting
- Laser Welding
- Machining
- Manufacturing Software
- Materials Handling
- Metals/Materials
- Oxyfuel Cutting
- Plasma Cutting
- Power Tools
- Punching and Other Holemaking
- Roll Forming
- Safety
- Sawing
- Shearing
- Shop Management
- Testing and Measuring
- Tube and Pipe Fabrication
- Tube and Pipe Production
- Waterjet Cutting
Industry Directory
Webcasts
Podcasts
FAB 40
Advertise
Subscribe
Account Login
Search
Rethinking the split-frame pipe machine concept
Quick-change adjustments reduce setup time, size changeovers
- By Eric Lundin
- Updated January 18, 2019
- February 9, 2019
- Article
- Tube and Pipe Fabrication
Although petroleum can be moved by road, waterway, and rail, it would be an understatement to say that the petroleum industry relies on pipeline for transportation. Approximately 72,000 miles of crude oil pipeline crisscross the U.S., a system that has been in development since 1860 or so. It’s part of the system that processes about 20 million barrels of oil per day in the U.S.
No matter the pipe diameter, installations and repairs require cutting and weld preparations with counterbores (typically called ID transitions in the pipeline market) and flange facing. Machines that mount to the pipe’s exterior are indispensable, providing a platform for tooling that rotates around the pipe’s circumference, removing a bit of material with each pass until the cut or bevel is complete. They perform a cold-cutting process, generating little in the way of heat or sparks—a safety enhancement when working on lines that carry anything potentially flammable, like petroleum.
Although the concept is 70 years old, technology advancements have facilitated the development of larger, sturdier, faster machines than in the past.
Spanning Diameters from 2 to 72 Inches
“E.H. Wachs developed the first traveling cutter in 1948,” said Ron Rohrbacher, U.S. sales manager, referring to the Trav-L-Cutter®, which is still in the company’s product line. Secured in place by a mounting chain that also serves as the drive chain, the unit runs on either pneumatic or hydraulic power to revolve around the pipe as it cuts or bevels.
The company also makes a large number of split-frame unit types in 13 standard sizes from 0.5 to 72 inches. Its small-diameter, split-frame line runs from ½ to 6 in. OD; its modular-design, split-frame products go from 2 to 72 in. OD; and its large-diameter, split-frame series handles sizes from 60 to 120 in. OD.
“With most machines of this type, one of the biggest drawbacks is the time and effort required to change sizes,” Rohrbacher said. “When changing to a smaller size, tool slides need to be moved to get closer to the workpiece and legs are needed to reach further for mounting,” Rohrbacher said. Loosening threaded fasteners was the biggest hurdle.“One machine handles a range of sizes, say 8 to 14 in., but changeover time is downtime,” he said.
The adage time is money is relevant in every industry, but time’s value is exponential when that time is downtime and that downtime concerns large-scale, capital-intensive industries like construction, manufacturing, or power generation. An outage can cost a refinery $500,000 per day. For a nuclear power plant, it can run $1 million per day.
“Often when a powerplant had a scheduled outage, it was common for the utility owner to rent individual machines for each size pipe rather than adapt a machine to different sizes,” Rohrbacher said.
Quick-change Hardware
The company’s redesigned system, christened DynaPrep™, got rid of many of the bolts, exchanging them for quick-change hardware. For example, the operator adjusts to a new pipe size by making two quarter-turns with a wrench, moving the slides to the new position, and making two quarter-turns in the other direction. The slides aren’t limited to pipe sizes, but they have several indexes that are helpful dealing with odd sizes such as casing and valve bodies.
Centering the machine on the pipe and squaring it up aren’t the hassles they used to be. The new design uses graduations on the clamp legs for centering, and the legs are designed to reduce axial motion, making the machine easier to square. If extensions are needed, they simply click into place.
“The company’s split-frame machines also offer optional spring-loaded tool slides, which track pipe OD to deliver a uniform prep and land, which is a big advantage when cutting—a pipe under compression has less chance of grabbing a blade,” Rohrbacher said.
“A key component in the drive system is the pinion gear,” he said. While an engineering background and computer simulations can go a long way in determining the stress on any component in any system and help to estimate that component’s service life, Wachs decided to apply a practical test to determine how much stress the drive system could withstand.
“We used a bench test setup that simulated about eight months of wear in just a few weeks to determine just how well it would hold up under normal service conditions,” he said.
Of course, this means that the rest of the machine has to withstand the resultant forces, so it has to be beefed up yet still portable. To handle these opposing design goals, the updated machine uses aluminum for the unit’s fixed ring to reduce its weight, and steel for its rotating ring to increase its strength. The two rings are separated by two sets of bearings in two separate raceways that distribute the loading forces evenly, regardless of the direction of rotation.
Increasing the motor’s power and the force the machine can withstand means the tooling can penetrate deeper on each revolution, reducing the cutting time.
“A 12-in. machine can cut pipe or make a double bevel in about 4½ minutes,” Rohrbacher said.
Just Two Tools
The entire DynaPrep offering, from 6 to 72 in., along with all the accessories, requires just two wrenches. The company elected to use 13 and 19 mm, which interchange with ½- and ¾-in. sizes in the imperial system.
How does all that shake out?
“In a recent demo I was able to take an 8-in. machine from the box, set it up, and perform a cut with double bevel on an 8-in. schedule 40 pipe in 8.5 minutes,” Rohrbacher said.
E.H. Wachs, www.ehwachs.com
About the Author
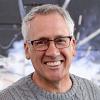
Eric Lundin
2135 Point Blvd
Elgin, IL 60123
815-227-8262
Eric Lundin worked on The Tube & Pipe Journal from 2000 to 2022.
About the Publication
Related Companies
subscribe now
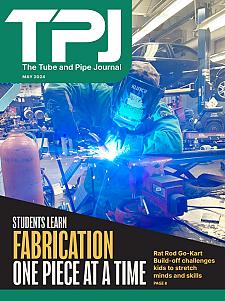
The Tube and Pipe Journal became the first magazine dedicated to serving the metal tube and pipe industry in 1990. Today, it remains the only North American publication devoted to this industry, and it has become the most trusted source of information for tube and pipe professionals.
start your free subscription- Stay connected from anywhere
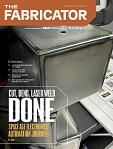
Easily access valuable industry resources now with full access to the digital edition of The Fabricator.
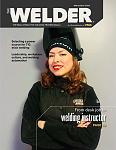
Easily access valuable industry resources now with full access to the digital edition of The Welder.
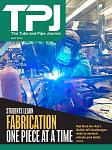
Easily access valuable industry resources now with full access to the digital edition of The Tube and Pipe Journal.
- Podcasting
- Podcast:
- The Fabricator Podcast
- Published:
- 04/16/2024
- Running Time:
- 63:29
In this episode of The Fabricator Podcast, Caleb Chamberlain, co-founder and CEO of OSH Cut, discusses his company’s...
- Trending Articles
Zekelman Industries to invest $120 million in Arkansas expansion
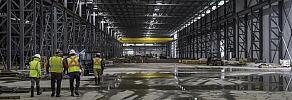
3D laser tube cutting system available in 3, 4, or 5 kW
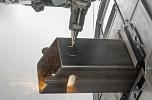
Corrosion-inhibiting coating can be peeled off after use
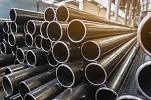
Brushless copper tubing cutter adjusts to ODs up to 2-1/8 in.
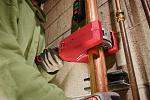
HGG Profiling Equipment names area sales manager
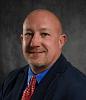
- Industry Events
16th Annual Safety Conference
- April 30 - May 1, 2024
- Elgin,
Pipe and Tube Conference
- May 21 - 22, 2024
- Omaha, NE
World-Class Roll Forming Workshop
- June 5 - 6, 2024
- Louisville, KY
Advanced Laser Application Workshop
- June 25 - 27, 2024
- Novi, MI