- FMA
- The Fabricator
- FABTECH
- Canadian Metalworking
Categories
- Additive Manufacturing
- Aluminum Welding
- Arc Welding
- Assembly and Joining
- Automation and Robotics
- Bending and Forming
- Consumables
- Cutting and Weld Prep
- Electric Vehicles
- En Español
- Finishing
- Hydroforming
- Laser Cutting
- Laser Welding
- Machining
- Manufacturing Software
- Materials Handling
- Metals/Materials
- Oxyfuel Cutting
- Plasma Cutting
- Power Tools
- Punching and Other Holemaking
- Roll Forming
- Safety
- Sawing
- Shearing
- Shop Management
- Testing and Measuring
- Tube and Pipe Fabrication
- Tube and Pipe Production
- Waterjet Cutting
Industry Directory
Webcasts
Podcasts
FAB 40
Advertise
Subscribe
Account Login
Search
Rewriting the rules for electrical safety
Beware of the potential for arc flash
- By Eric Lundin
- March 31, 2020
- Article
- Tube and Pipe Fabrication
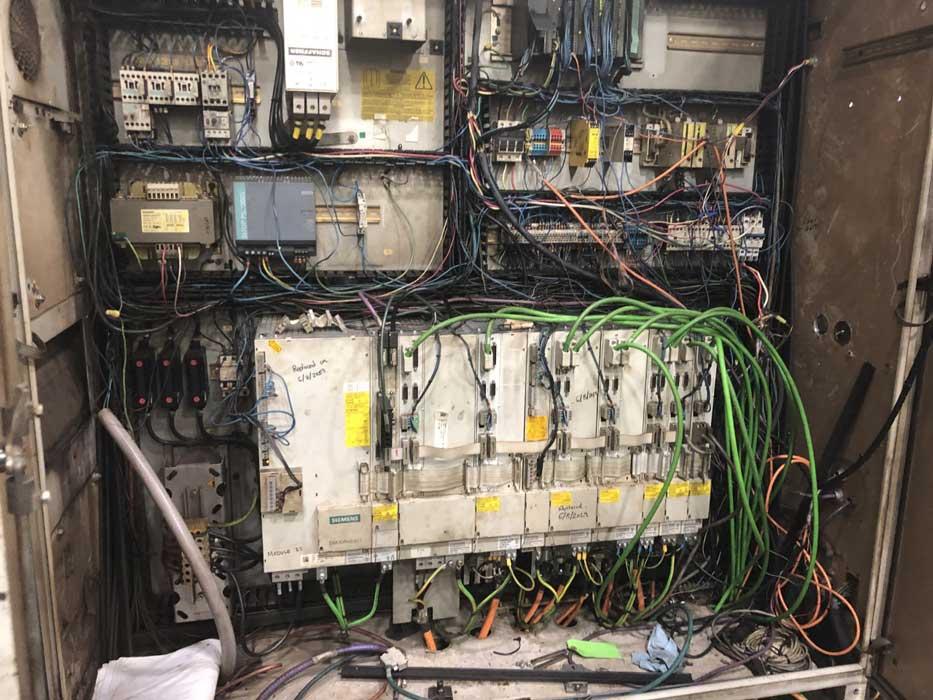
Just a glance at an electrical panel in an industrial setting is enough to see a few hazards. The discoloration on the doors, which should be nearly white, indicates the presence of oil and dust, both of which contribute to the likelihood of a fire or an explosion. The proximity of high and low voltage means that working on low-voltage circuits is risky. This cabinet has a high potential for an arc flash.
Anyone who has worked around machinery for very long can spot a machine’s hazards a mile away. Hot surfaces, belts and pulleys, sharp blades, clamps or jaws that open and close, electrical power—it would be difficult to find an industrial machine that doesn’t have at least a couple of hazards lurking somewhere in the works.
Thankfully, the many advances in safety technology have made today’s workplace much safer than in the past. Whether the hazards are eliminated at the design stage, mitigated with guarding, or alleviated with interlocks, workers today tend to suffer far fewer injuries, and in far less severity, than workers did in the past. National Safety Council data indicates that the total number of recordable incidents per 100 workers in private industry decreased from 5.3 to 2.8 from 2002 to 2018.
However, this doesn’t mean that every hazard has been eliminated. In tube fabrication, a rotary tube bender usually presents two obvious hazards: crushing and entrapment. When the clamp dies close in on the tube, the action produces tremendous force, creating a crushing hazard. A moment later, the rotating motion of the bend die and other tools creates a force that draws the tube into the die set, which has the potential to create an entrapment hazard. Despite the risks, such a machine can be operated thousands of hours without a mishap, a credit to safe work habits.
Regrettably, in some fabrication shops, the safety culture isn’t very modern.
“One of my biggest concerns often comes up when I visit old-school bending shops,” said Jay Robinson, owner and president of RbSA Industrial. “An operator loads the tube, the clamp die advances, and often the operator grabs the tube and gives it a tug to make sure it really is clamped securely. During bending the operator may put his finger on the tube and against the clamp to make sure the tube does not slip during bending.” At this point, the machine is already forming the tube, and if the tube does slip, the clamp pushes open, or the operator’s sleeve gets caught, the operator could get pulled into the machine. The term rotary draw bender couldn’t be more clear: The bending die rotates and draws the tube in to bend it. Anything snagged by the tube likewise can get pulled into the machine, and the outcome could very well be a few broken bones or an amputation. Operators must be completely cognizant of every moving part on the bender—their locations, their statuses, and whether they are staged to activate.
Hydraulic System Risks
Hydraulic benders present additional risks in that hydraulic fluid under pressure can present a danger. Robinson mentioned that a somewhat common hazard in industry concerns fluid leaks. Hydraulic fluid pressurized to 2,000 pounds per square inch (PSI), leaking out through a pinhole in the hydraulic circuit, can exit with a tremendous capability to do damage. Such a situation has been known to penetrate the sole of a safety boot and enter the tissue, resulting in an accident known as hydraulic penetration injury.
“I read about a case in which a hydraulic unit sprung a leak, and a worker nearby responded instinctively, covering the leak with his hand to prevent the fluid from squirting all over the place,” Robinson said. If the hydraulic pressure is very low, the outcome can be little more than skin irritation. However, at 2,000 PSI, the outcome can be much more severe, and in some cases it is fatal.
A related problem concerns routine maintenance or repairs on hydraulic equipment. A review of several incidents from the Occupational Safety and Health Administration’s database illustrates a lack of understanding of hydraulic system principles:
- 1365522.015 – An employee repairing a hydraulic leak on an end loader was working under the raised bucket of the loader when he drained the hydraulic fluid, causing the bucket to fall and fatally crush him.
- 1297381.015 – An employee was replacing a hydraulic valve on a reach stacker. When loosening a hydraulic line at the valve, the line blew off and forced hydraulic fluid into the base of the employee’s thumb. The employee was taken to the hospital where he was kept overnight for treatment.
- 1273087.015 – An employee checking or adjusting a light or hydraulic line connection on a loading machine, while standing between the loader boom and the inside of the driver’s front wheel, was caught between the fallen loader machine boom and the inside of the driver’s side front wheel. He was sprayed with oil from a burst hydraulic line and the boom fell. The employee was hospitalized with a fractured left collar bone, several broken ribs, and a collapsed lung.
Although a hydraulic repair on a tube or pipe bender isn’t likely to result in a fatality, a crushed hand is a possibility if the worker has only a passing familiarity with hydraulic systems.
A lack of a thorough understanding of hydraulics is the salient problem. While the unemployment rate is at record lows and skilled labor becoming harder than ever to find, equipment builders are dealing with the same skills shortage that fabricators are dealing with. If one of your machines needs maintenance, the machine builder might not be able to dispatch a service technician anytime soon, and you might need to rely on your staff or hire a service technician who is low in experience and hasn’t been trained to maintain or repair your specific machines.
If such a technician is needed to do maintenance or troubleshooting regarding the machine’s electrical system, he’s going to face other hazards.
Electricity Under Control
Electrical systems and subsystems used in industry likewise pose substantial hazards. They are similar to those in a residential electrical system, but greater in scope.
In a residential electrical system, most circuits carry 120 V, and most circuits are protected by 15-amp or 20-amp breakers. When powering three incandescent bulbs (60 W each), an old cathode-ray tube television (100 W), and a coffee maker (1,500 W) on a single 15-amp circuit at the same time, the breaker isn’t likely to trip. The circuit can handle 1,800 W (120 V multiplied by 15 amps), and the power consumption is 1,780 W.
In an industrial setting, it’s a completely different ballgame. Many of the electrical circuits for industry supply multiples of the voltages of home wiring levels, such as 240 or 480 V. At 480 V, an all-electric tube bender capable of bending 3-1/2-in.-OD tubing can draw up to 150 amps, Robinson said. Because such circuits often supply voltage in three phases, the effective current is greater, equivalent to about 1.75 times the current in a single-phase circuit, so the power—the result of multiplying the voltage by the current—is greater by an order of magnitude than any amount in a residence:
480 V x 150 amps x 1.75 = 126,000 W
In both cases, at home and in an industrial setting, as long as everything works as it should, all is well. If a problem occurs—say, a short circuit—and the current increases to the capacity of the circuit breaker, the circuit breaker opens and current stops flowing. This prevents a circuit from overheating and causing a fire; it also is intended to prevent an electric shock.
Note that, although an industrial circuit has much more voltage, current, and power than a residential circuit, a common residential circuit is still a force to be reckoned with. First, it has the potential to melt metal; a mere 24 V is enough for welding. Second, 15 amps is more than enough to electrocute a person, by a long shot. Just 40 milliamps, or 40 thousandths of an amp (0.040 amps), can stop a heart.
Electricity Out of Control
The industrial circuit is hazardous in a way that a residential circuit is not. The amount of power is so vast that when something goes wrong, an arc can develop—that is, rather than flowing through conductors only, the current travels through the air that separates the two conductors.
“The result can be grim,” Robinson said. Grim, as in catastrophic.
Under normal circumstances, the air gap between the conductors is large enough, and the electrical resistance is high enough, that no current flows between them. However, if a screwdriver or some other conductor gets too close and reduces the air gap substantially, the resistance drops. If the electromagnetic fields that surround the conductors ionize the air, the air begins to act like a conductor, making a pathway from the hot side (voltage supply side) to the neutral conductor (the return side) or a ground conductor (a secondary return side). This is similar to a short circuit, but the current travels through the air rather than through a solid. Plasma develops, imparting a tremendous amount of light and heat to everything in the immediate area. Note that the first phenomenon, ionization, is the same natural process that precedes lightning strikes, and that plasma is a state of matter found in the sun. Plasma is so hot that it strips electrons off of atoms.
A plasma arc generates such intense amounts of light—infrared, visible, and ultraviolet—that it scorches and often vaporizes nearly anything in its vicinity. The temperature can exceed 30,000 degrees F, generating enough heat to cause metals to vaporize. Before they vaporize, they expand; copper’s volume increases by a factor of more than 60,000 to 1 when it vaporizes. Metals expand so quickly that they explode, sending fragments of shrapnel and vaporized metal in every direction.
Note that the culprit that causes the arc flash isn’t necessarily a tool that doesn’t belong near the conductors. It can be something as innocuous as dust, or something beyond a worker’s control, such as condensation or corrosion. Finally, it can be a tool that doesn’t seem out of place in an electrical cabinet, such as a voltmeter. A few more incidents from OHSA’s database illustrate the severity of this problem, even when the workers involved are engineers and electricians:
- 310603600 – An employee working for a company that installed temporary power for construction sites was installing a meter on an energized electrical panel (480 V). As he was installing the meter, he shorted out a phase conductor to the ground with the metal part of the meter. This caused an arc flash, and he received flash burns on his face and both hands and arms. He was hospitalized for two weeks.
- 202087821 – A maintenance electrician at a manufacturing company was called by production staff about a mill motor that was “single-phasing.” The mill was powered by a three-phase, 480-V power distribution panel that stepped down the incoming 4,160 V. To troubleshoot the fault, he disconnected the power and placed a voltage tester onto a 4,160-V energized lead, which was greatly in excess of the 600 V for which the meter was rated. An arc blast occurred, hurling him away from the disconnect and causing full- and partial-thickness electrothermal burns to his hands, abdomen, and legs, and he was hospitalized.
- 316574011 – A team of three working in a steel plant—an electrical engineer and two electricians—were troubleshooting a 4,160-V circuit with a meter rated for a maximum of 1,000 V and inadvertently attempted to measure resistance on a live circuit. The ensuing arc flash set one of the workers’ clothing on fire and he sustained burns over 55 percent of his body.
Mitigation
Dealing with the risks associated with vast amounts of electrical power is challenging, but it isn’t difficult to get started on a comprehensive mitigation program.
“This can include having maintenance and other appropriate personnel trained in arc flash safety and providing and enforcing the use of correct personal protective equipment (PPE) if they are required to troubleshoot inside a live panel,” Robinson said, listing the protections for workers who deal with electrical power, but the safety perimeter doesn’t end there. “It’s also necessary to create and enforce a policy of minimum safe distance with temporary physical barriers,” he said. “This prevents any personnel without arc flash PPE from passing through the area while the panel is open and has the potential to be made live.”
A few other resources can provide an orientation to preventing the hazards associated with arc flash:
- “Help Protect Yourself and Your Personnel from the Dangers of Arc Flash,” posted at electrification.us.abb.com/sites/geis/files/ultimatearcflashguide.pdf.
- “Reduce Arc Flash Incidents in 6 Ways” by David G. Loucks, P.E., originally published in Plant Engineering and posted at www.grainger.com/know-how/safety/electrical-hazard-safety/arc-flash-safety/kh-6-ways-reduce-arc-flash-incidents.
- “Five Important Things to Know About Arc Flash PPE Programs” by Scott Francis, posted at ohsonline.com/articles/2019/10/01/five-important-things-to-know-about-arc-flash-ppe-programs.aspx.
RbSA Industrial, www.rbsaindustrial.com
About the Author
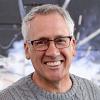
Eric Lundin
2135 Point Blvd
Elgin, IL 60123
815-227-8262
Eric Lundin worked on The Tube & Pipe Journal from 2000 to 2022.
About the Publication
Related Companies
subscribe now
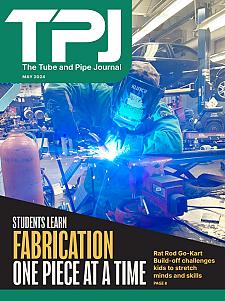
The Tube and Pipe Journal became the first magazine dedicated to serving the metal tube and pipe industry in 1990. Today, it remains the only North American publication devoted to this industry, and it has become the most trusted source of information for tube and pipe professionals.
start your free subscription- Stay connected from anywhere
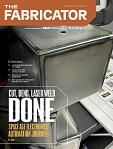
Easily access valuable industry resources now with full access to the digital edition of The Fabricator.
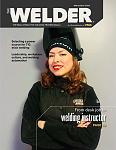
Easily access valuable industry resources now with full access to the digital edition of The Welder.
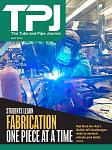
Easily access valuable industry resources now with full access to the digital edition of The Tube and Pipe Journal.
- Podcasting
- Podcast:
- The Fabricator Podcast
- Published:
- 04/16/2024
- Running Time:
- 63:29
In this episode of The Fabricator Podcast, Caleb Chamberlain, co-founder and CEO of OSH Cut, discusses his company’s...
- Trending Articles
Zekelman Industries to invest $120 million in Arkansas expansion
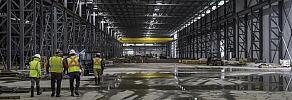
3D laser tube cutting system available in 3, 4, or 5 kW
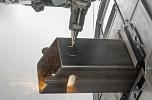
Corrosion-inhibiting coating can be peeled off after use
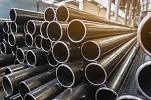
Brushless copper tubing cutter adjusts to ODs up to 2-1/8 in.
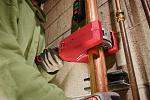
HGG Profiling Equipment names area sales manager
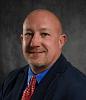
- Industry Events
16th Annual Safety Conference
- April 30 - May 1, 2024
- Elgin,
Pipe and Tube Conference
- May 21 - 22, 2024
- Omaha, NE
World-Class Roll Forming Workshop
- June 5 - 6, 2024
- Louisville, KY
Advanced Laser Application Workshop
- June 25 - 27, 2024
- Novi, MI