- FMA
- The Fabricator
- FABTECH
- Canadian Metalworking
Categories
- Additive Manufacturing
- Aluminum Welding
- Arc Welding
- Assembly and Joining
- Automation and Robotics
- Bending and Forming
- Consumables
- Cutting and Weld Prep
- Electric Vehicles
- En Español
- Finishing
- Hydroforming
- Laser Cutting
- Laser Welding
- Machining
- Manufacturing Software
- Materials Handling
- Metals/Materials
- Oxyfuel Cutting
- Plasma Cutting
- Power Tools
- Punching and Other Holemaking
- Roll Forming
- Safety
- Sawing
- Shearing
- Shop Management
- Testing and Measuring
- Tube and Pipe Fabrication
- Tube and Pipe Production
- Waterjet Cutting
Industry Directory
Webcasts
Podcasts
FAB 40
Advertise
Subscribe
Account Login
Search
Small, mobile tube end forming systems provide alternative to large machines
Small size, portability offer convenience and suit batch or series production
- By Eric Lundin
- October 26, 2021
- Article
- Tube and Pipe Fabrication
End forming machines have come a long way in the last decade or so. The days of loading a single tube by hand and making one hit are on the way out.
Modern end formers are equipped with CNC; provide automatic loading, forming, and unloading; are designed with tooling carousels so they can provide several hits; and often handle two tubes at once for double the productivity. Sensors check for the presence of features or take measurements, helping to determine whether all of the processes were carried out properly and completed. These features assist fabricators short on seasoned staff, making the process more automated and reliable than ever before.
This sort of machine fulfills most of the industry’s needs, but this isn’t the only way to carry out end forming processes. Airmo Inc., which specializes in pressure technologies, developed a line of end forming units based on a compact design, some of which are hand-held. The hydraulic power unit is controlled by a programmable logic controller, but these units dispense with tool carousels, sensors, and other features in favor of mobility. For applications in which it’s more beneficial to bring the machine to the work, rather than the other way around, this type of machine is extremely convenient. For some applications, such as working in confined areas, it can be the only way to get the job done.
The company’s largest series isn’t quite as portable, but still provides end forming mobility for fabricators that need to move machines around from time to time as processes change.
Convenience in Confined Quarters
“For a hand-held end former, heat exchanger assembly is an ideal application,” said CEO Harry Morán. “It allows you to form all of the tubes for the heat exchanger right on the production line.
“You can form both ends of the tube, and you don’t need a separate workstation. You can form the ends, make the U-bends, and start soldering in one smooth process. If you had to set up the end forming process at a separate workstation, you’d have additional material handling and time, adding to the cost of building the unit.”
The company’s 400 series units are small enough to be hand-held, but even at this size, they perform as intended.
“Pinching a tubesheet between two beads forms a gastight seal,” he said. “The assembly doesn’t need a gasket, which could deteriorate over the years. The tool has been proven to create an airtight seal that lasts more than 20 years.”
The machines are suitable for many applications in which space is tight and for which using a traditional end forming machine is difficult, especially when other methods have been tried and abandoned—for example, making an assembly by welding or brazing. If the work area doesn’t provide 360 degrees of unfettered access for welding, brazing, or soldering around a tube or pipe, it might be a candidate for a portable end former.
Hand-held, Supported, and Mobile End Formers
The company’s model 400 uses a hydraulic ram to force the die over the OD or into the ID to compress or expand the tube end. Models M and M6 are available in this style and also the finger style. Also known as segmented tooling, the finger-style process uses a series of tools in segments around a central point. When the tube is inserted into the end forming head, the segments either expand the tube from the ID or compress it from the OD.
Although the company’s designs are more compact than traditional end formers, they aren’t limited in what they can do, providing the same sorts of expansions, reductions, flares, beads, and other end forms that full-sized machines make.
“They can accomplish any shape, as long as physics allows it,” Morán said.
Model 400 series machines handle diameters from 0.19- to 1.38-in. OD. Model M, which is a bit bigger than the 400, handles diameters from 0.13- to 3.00-in. OD. The largest is M6, which forms tubes from 3.00 to 6.00-in. OD. Fabricators often use this tool manually, but for long periods of time, it needs a counterbalanced tool holder that can support its weight. Another option is to make a mobile workstation by installing the hydraulic pump inside a mobile cabinet and mounting the end former on top of the cabinet.
As with traditional end formers, cycle times aren’t long. For simple shapes in small diameters of pliable material, the cycle time can be as little as one second; when working heavier-walled material, or when working an alloy that has a lot of springback, the forming cycle time increases accordingly, and might take five or even six seconds, Morán said. All use a common hydraulic power source, a double-acting type—providing power to extend and retract—capable of delivering 3,000 PSI of pressure.
And although the end forming units are compact, they aren’t complex.
“The units are user-friendly,” Morán said.
The company provides a complete set of cutaway drawings for every tool it ships, along with disassembly and assembly instructions. The intention is that the end user swaps out the tooling when necessary and maintains the tool, performing regularly scheduled disassembly, inspection, and repair.
This doesn’t mean that Airmo ships units out and never sees them again. In many cases, a customer needs a unit certified to comply with a specific industry standard. The company certifies the unit on request before shipping it out and recertifies it when the customer requests it.
Direct Contact with the Market
Airmo isn’t a large company—it has just over a dozen employees—and it isn’t bureaucratic, always striving to stay in touch with its customers.
“When you call, you talk to someone at Airmo,” Morán said. The company doesn’t sell its products through any sales representatives and uses just a few vendors who do reselling, which keeps the company close to the market.
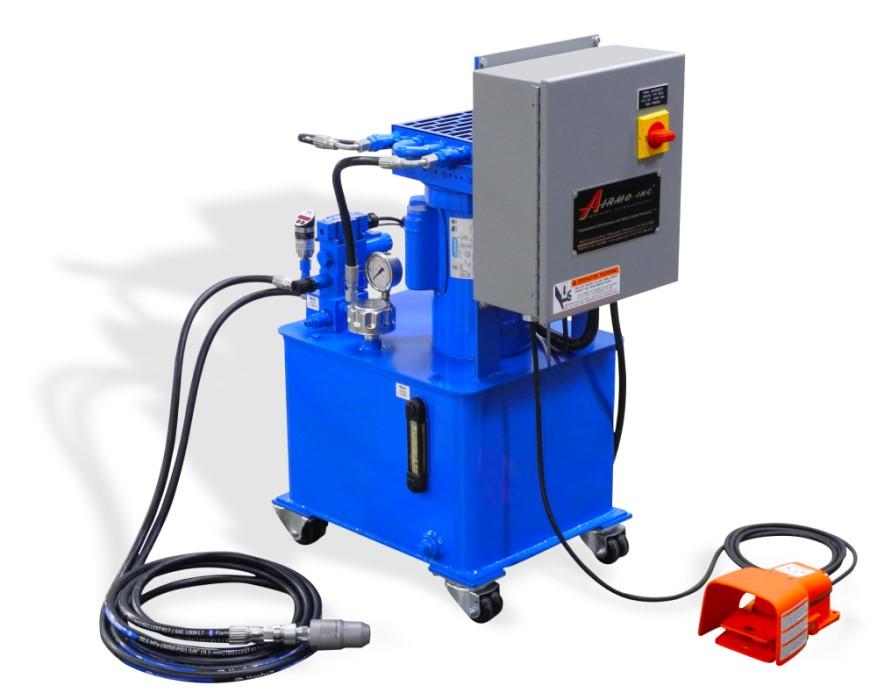
The PLC, foot switch, and tooling rack sum up the convenience of using a compact, mobile end forming system.
“We don’t use a research and development team,” Morán said. “We rely solely on customer input for ideas for new products and die sets.” And while it does make products for common or standard applications, it doesn’t make products that go into inventory. Every machine is made to order and run off at Airmo before being shipped. Building each unit to order puts the company in a position to build entire kits that suit the customer. The company doesn’t have a single, universal catalog of parts, dies, and couplers. Each market—the U.S., Europe, and Japan, for example—has its own industrial standards or specifications, so if Airmo gets an order from a customer in Europe, for example, it supplies a hydraulic power source that runs on 220 V and incorporates connectors with metric threads.
“We don’t want customers to develop or modify their processes to conform to the capabilities of our products,” he said. It’s the other way around. “We build everything to order.”
This requires close cooperation with its customer base, which has contributed to the company’s cumulative expertise.
The company isn’t limited to units that use 3,000 PSI. This is just a starting point. For heavy-wall applications, it has been known to make units that use 15,000 PSI of hydraulic pressure, which greatly expands the company’s ability to solve challenging forming problems.
Morán acknowledges that Airmo doesn’t solve every problem that comes its way, although he estimates that the company is able to fulfill around 85% of the requests it receives. For the other 15%, it tries to offer advice based on its years of experience in dealing with tube and pipe in many applications. Both a manufacturer and a technical consultant, the company sees its role as that of a problem-solver.
“In some cases, the customer might be able to use another machine, like an off-the-shelf orbital welding machine” Morán said. In this type of situation, Airmo would give the advice and skip the sale.
Time Isn’t Money
The adage “time is money” has many applications, but time often competes with money when fabricators are deciding how to proceed with an end forming project. For a tube that needs two or three operations, they have a choice.
For fabricators with a tight budget but extra time, a single end forming machine can do the job. They just need to swap out the dies to change from one process to the next. Those that are short on time but have a little extra money in the budget should invest in more than one end former and have the second (or even third) die sets installed and ready to go to maximize its throughput.
Having several forming heads also gives a fabricator some breathing room so it can disassemble, inspect, and clean the end formers on a regular basis between jobs.
These guidelines apply to order sizes as well. For a fabricator that deals in long runs, using a single unit and swapping out the tooling is probably the way to go. For short runs, having dedicated units on hand is likely to be the most efficient way, getting around frequent changeovers.
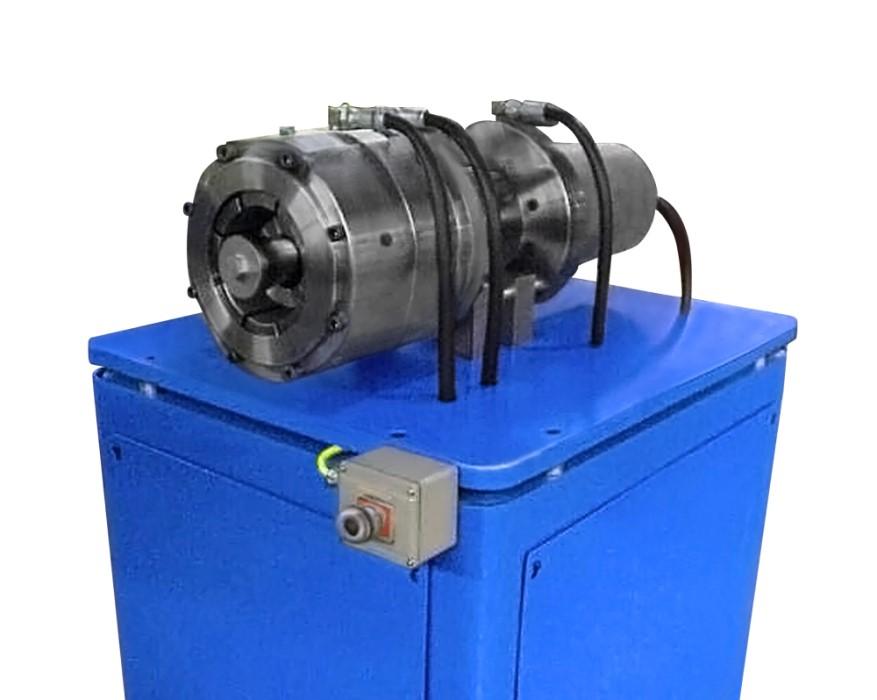
An end former that is too large to be hand-held can still be the centerpiece of a versatile, mobile system when it’s mounted to a cabinet on wheels.
Long on Experience, Long on Knowledge
The world moves at a fast pace, and the pace seems to be accelerating all the time. Product life cycles certainly aren’t as long as they were in the past, are they? Believe it or not, some manufactured products still last for decades. Because Airmo is small, it’s nimble, and it can supply parts for machines that probably would be obsolete if they had been produced by a large manufacturer.
“In May of 2020 we got a call from a customer who needed new collets for one of our end formers,” Morán said. “They were for a tool we sold in 1955.” Airmo still had the prints on hand and it was able to ship new collets in short order.
Products that have extremely long lives can be problematic for other reasons. For example, if a tubular component is made from an unusual alloy that is hard to find, and a supplier discontinues it, the fabricator might find itself in a jam. A different supplier might have a similar material with slightly different forming characteristics, or the company might need to substitute an entirely different material. In such cases, Airmo’s expertise in metallurgy can help. The solution might be a new tool set or merely a new forming procedure.
“Every alloy has its own forming characteristics and its own springback characteristics,” Morán said. “Even if one tooling set can form two alloys, the forming process isn’t necessarily identical. One metal might need a slower forming process or longer dwell time than the other to compensate for differences in how they form.”
In this sort of situation, the company draws on its reservoir of forming knowledge, some of which is book smarts and some of which is based on hands-on experience accumulated over the 75 years since it was founded.
“We have 6,000 customers,” Morán said. “Each one is unique. Each one takes a different approach to solving a forming challenge. But it’s all end forming, so each one accomplishes the same thing in a different way.”
About the Author
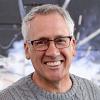
Eric Lundin
2135 Point Blvd
Elgin, IL 60123
815-227-8262
Eric Lundin worked on The Tube & Pipe Journal from 2000 to 2022.
About the Publication
Related Companies
subscribe now
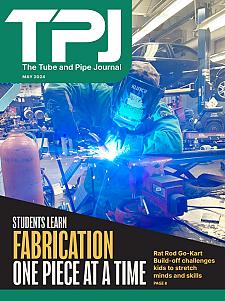
The Tube and Pipe Journal became the first magazine dedicated to serving the metal tube and pipe industry in 1990. Today, it remains the only North American publication devoted to this industry, and it has become the most trusted source of information for tube and pipe professionals.
start your free subscription- Stay connected from anywhere
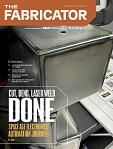
Easily access valuable industry resources now with full access to the digital edition of The Fabricator.
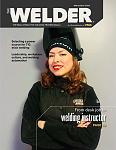
Easily access valuable industry resources now with full access to the digital edition of The Welder.
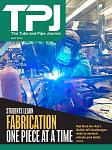
Easily access valuable industry resources now with full access to the digital edition of The Tube and Pipe Journal.
- Podcasting
- Podcast:
- The Fabricator Podcast
- Published:
- 04/16/2024
- Running Time:
- 63:29
In this episode of The Fabricator Podcast, Caleb Chamberlain, co-founder and CEO of OSH Cut, discusses his company’s...
- Trending Articles
Zekelman Industries to invest $120 million in Arkansas expansion
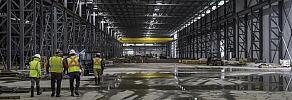
3D laser tube cutting system available in 3, 4, or 5 kW
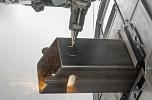
Corrosion-inhibiting coating can be peeled off after use
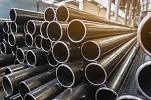
Brushless copper tubing cutter adjusts to ODs up to 2-1/8 in.
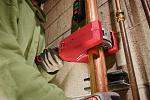
HGG Profiling Equipment names area sales manager
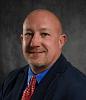
- Industry Events
16th Annual Safety Conference
- April 30 - May 1, 2024
- Elgin,
Pipe and Tube Conference
- May 21 - 22, 2024
- Omaha, NE
World-Class Roll Forming Workshop
- June 5 - 6, 2024
- Louisville, KY
Advanced Laser Application Workshop
- June 25 - 27, 2024
- Novi, MI