- FMA
- The Fabricator
- FABTECH
- Canadian Metalworking
Categories
- Additive Manufacturing
- Aluminum Welding
- Arc Welding
- Assembly and Joining
- Automation and Robotics
- Bending and Forming
- Consumables
- Cutting and Weld Prep
- Electric Vehicles
- En Español
- Finishing
- Hydroforming
- Laser Cutting
- Laser Welding
- Machining
- Manufacturing Software
- Materials Handling
- Metals/Materials
- Oxyfuel Cutting
- Plasma Cutting
- Power Tools
- Punching and Other Holemaking
- Roll Forming
- Safety
- Sawing
- Shearing
- Shop Management
- Testing and Measuring
- Tube and Pipe Fabrication
- Tube and Pipe Production
- Waterjet Cutting
Industry Directory
Webcasts
Podcasts
FAB 40
Advertise
Subscribe
Account Login
Search
Take a bite out of processing costs by optimizing the lubricant selection and application process
Cut costs, maximize efficiency by considering upstream and downstream processes
- May 24, 2019
- Article
- Tube and Pipe Fabrication
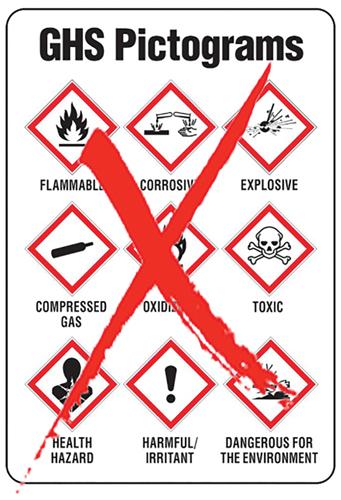
The globally harmonized system (GHS) provides text and pictograms that indicate the various hazards associated with consumer and commercial products. Keep it simple by looking for lubricants that pose no risks or hazards.
Playing lawyer Mitch McDeere in the movie The Firm, Tom Cruise warns FBI agent Wayne Tarrance (played by Ed Harris) that mail fraud isn’t sexy, but the punishment has teeth. Now, what does that have to do with lubrication? Most tube and pipe producers and fabricators wouldn’t give this any thought when trying to find optimal lubricant and application method for a tube forming process, but most should! Lubricant choice doesn’t necessarily provoke a lot of thought or water-cooler conversation in fabrication shops, but it has teeth—it can affect many other factors in the process, including worker safety and processing costs. Using the available data and a proven selection process can help you develop capable, cost-effective forming processes.
Chemistry and Carriers
It is always important to have a basic knowledge of some chemistry and physics to understand why certain lubricants are preferred for specific forming processes. In most cases, all the lubricants have similar additives to control process variables such as microbial growth, material staining, and corrosion. What sets them apart are additives for performance that affect the workpiece and tooling surfaces and the difficulty of the forming process.
In most cases, a lubricant’s viscosity alone can handle the frictional load in the forming process and keep the tool and the workpiece separated. However, as the forming difficulty increases, so do the friction and heat, so a tougher boundary layer is needed. The addition of boundary additives helps create space and reduce friction. When the lubricant’s viscosity and a boundary additive still can’t handle the load, extreme-pressure and temperature additives are used. Coupling these additives with either a synthetic or an oil-based chemistry can help create a very capable lubricant.
The lubricant carrier also can make a difference. Choices include dilutable synthetic and emulsion coolants, straight oils, gels and pastes, a mist to achieve minimum quantity lubricant (MQL), grease, and even wax. Some can be used in several processes depending on the applications, but all can have a specific use and effect in forming tube.
Narrowing Down the Choices
When faced with many options, finding the best choice can be a daunting task. Engaging a reputable lubricant supplier in the process development phase can help you ensure all variables are tailored for the best fit. Consulting a lubricant specialist before and after the design phase will help you increase the options available and perhaps save money in the long run.
To narrow down a broad list of choices, use this time-tested eight-step process:
1. HSE (Health, Safety, and Environment). HSE should always be the first priority. Determine the variables that affect operator health and safety (pH, smoke or fumes, and microbial growth) and look for options that limit operator exposure. With the new globally harmonized labeling and safety data sheet system in place, users have more knowledge than ever before on how a product can be handled. Start by looking for options that have no pictograms or health hazard warning statements.
2. Chemical Restrictions. Restrictions on certain chemicals and additives can come from various sources. At the federal level, the Occupational Health and Safety Administration and the Environmental Protection Agency have the authority to regulate certain chemical parameters. Local authorities can, too. Some corporations have taken up their own initiatives, and these might vary by plant location. Discussing these restrictions with a lubricant supplier in the early stage can help you narrow the list of allowed lubricants and help determine the cost impact.
3. Reconditioning and Waste Treatment. Make sure that any lubricants to be discarded are compatible with current waste treatment methods. Any treatment of effluent from the processes also must be compatible.
4. Effect on Material, Tooling, and Equipment. Any potential lubricant reactions or interactions require investigation before any forming trials begin. These include how the workpieces, tooling, and equipment react to lubricant exposure. In most cases, you can determine the effect rather quickly from a laboratory test or from existing data.
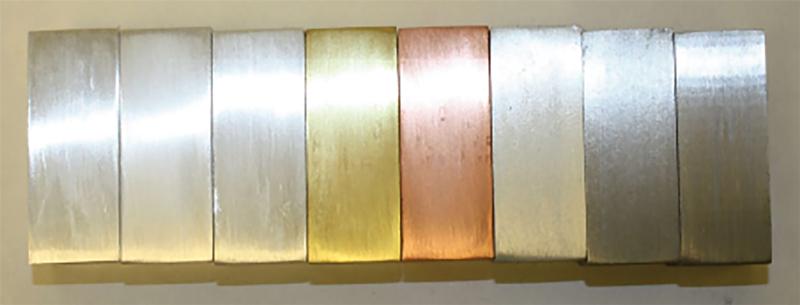
To test for material stains, submerge a sample halfway into a lubricant for a period of time and then compare the two halves.
Stain testing, a process in which half of a panel is submerged in the lubricant and monitored over time, is a simple method. A stack stain test shows the interaction of lubricant trapped between two like substrates such as bundled tubes.
Water quality in tube mills plays an enormous role. In coolant systems, the lubricant is 90 to 95 percent water, so if the water is bad, the coolant is going to be bad as well, and the process will suffer. Emulsion stability, hard water stability, foam tendency (when applicable), tramp oil rejection, corrosion protection, and cleanability are all areas with quick tests that can help preclude or rank lubricant options. You also can obtain pretrial performance using friction testing equipment.
5. Application. Application is something that is best discussed in the design phase. At one end of the spectrum are welded tube and pipe mills, which always run with a coolant, narrowing down the carrier choice substantially. At the other end are tube forming operations; the application process can be manual or automatic, the latter including spray, injection, roll-on, and flood.
6. Secondary Processing. When tubulars are bent or formed, certain lubricant residues can be left on the inside or the outside surfaces. You need to determine the effect of those residues to downstream processes such as washing, painting, welding, and packaging. How much residue can be left on the product for processing or shipment?
7. Tool Life and Quality. Many users like to jump to this section first. Why fiddle with the other steps if it won’t make the part in the first place? And they are right! However, it’s more time-consuming and disheartening to go through a trial and realize that you can’t use something that worked so well because it contains a hazardous ingredient, or the residue has to be washed and there is no provision in the process for that step. In the end, the tube needs to be formed based on the operation, so you need to discuss all the steps with the lubrication specialist and end user to keep a reasonable expectation for success. Always perform small trials followed by full production runs to gauge the full effect on the process.
8. Cost Effectiveness. The previous seven steps will give you a good idea of the cost and potential value the lubricant will bring to the process. Weighing the different cost-generating areas will help you determine whether a premium product is worth the higher upfront cost relative to less costly alternatives. The key is to look at the entire cost of the process, not just the price per gallon. Remember, lubricant isn’t sexy, but it has teeth. The cost of lubricant is typically 0.5 percent of the total manufacturing cost, but it can have a major effect on the total process.
Typical Operations and Products
In tube producing and fabricating, the mill consumes the most lubricant, but that’s just the beginning. From the mill, tube and pipe products go just about everywhere, and they are stored in environments that vary from relatively benign (hot, dry environments) to relatively aggressive (coastal areas with humid environments characterized by salty air). And then they go through any number of forming operations. To choose the best lubricant and application method, you need to understand how the tube or pipe is produced, where it will be stored, and how aggressive the forming operations will be.
Making Welded Tube. Welded tube mills normally run recirculating coolants diluted 5 to 15 percent with water. This provides the best combination of lubricity in the rolling area, cooling after welding and scarfing, subsequent cold rolling, and in many cases, cut to length. These coolants can be fully synthetic, semisynthetic, or soluble oil. Most are in the first two categories and contain less than 30 percent oil. Newer coolant technology offers additive-free biostability, which prolongs sump life and decreases maintenance.
If you maintain the pH and concentration levels and remove tramp oil continuously, you can make the sump last one or even two years. Some lubricant providers even offer products that continually clean the mill as they circulate.
If the coolant residue cannot provide ample long-term corrosion protection, add a rust preventive. You can apply a water-displacing rust inhibitor to the finished tube through a spray box to isolate it from the mill coolant so the two don’t mix. If you need a heavier duty cutoff lube, make sure it is compatible with the mill coolant and the rust inhibitor.
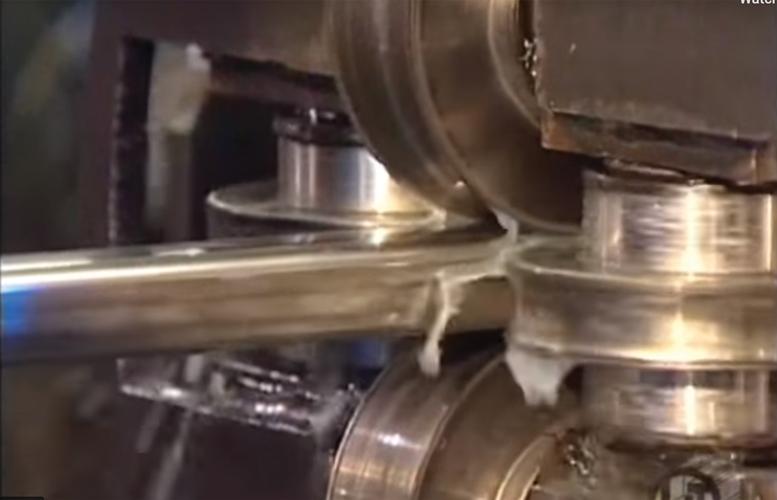
On a welded tube mill, it’s customary to apply a corrosion inhibitor after the cutoff operation. Be sure to keep the corrosion inhibitor separate from the mill coolant if the two chemicals aren’t compatible. Photo courtesy of Roll-Kraft.
Making Seamless Tube. The process of pulling tube through a die to change the OD while using a mandrel on the ID still requires heavy oils and waxes. They provide the needed lubricity and can hang on during the entire forming operation. New application methods have been tried to allow the use of lighter lubricants, which would help with lubricant removal before annealing—often done between successive pulls—but the tubes usually are so long and the reapplication area so remote that these efforts have been hollow, at best.
Bending. For mandrel-based bending, gels and pastes offer high performance for wear tools, and they cling to the tube as it bends. Even with a thin film application, lubricant can be left in the tube after processing. Light-duty bending (such as 1.5D to 3D, where D is the centerline bend radius divided by the tube’s OD) still favors an MQL application of a renewable resource or seed oils. On tougher applications, heavier duty gels, pastes, or compounded straight oils are still necessary and require subsequent wiping or cleaning operations.
Wiper die tooling requires a lighter application of the same lube used for the mandrel, if any. New synthetic fluids are starting to make headway, even on the toughest stainless operations, because they provide increased performance while leaving behind just a thin residue of lubricant that doesn’t interfere with subsequent welding operations.
Forming and Sizing. End forming and sizing operations vary greatly, so they use a variety of lubricants. Some sizing operations need just the lubricant residue from a previous operation, such as bending or the production process. If additional lubricant is required, it’s usually a straight oil applied by flooding the tube or pipe, using a system that recirculates the lube.
Be sure to use the lube that gives the best performance with the lightest application, especially if you apply it by hand; heavy applications require a cleaning operation.
Chris Fletcher is sales and marketing manager for Tower Metalworking Fluids, 4300 S. Tripp Ave., Chicago, IL 60632, 773-927-6161, c.fletcher@towermwf.com, www.towermwf.com.
About the Publication
subscribe now
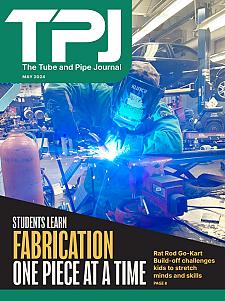
The Tube and Pipe Journal became the first magazine dedicated to serving the metal tube and pipe industry in 1990. Today, it remains the only North American publication devoted to this industry, and it has become the most trusted source of information for tube and pipe professionals.
start your free subscription- Stay connected from anywhere
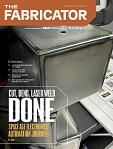
Easily access valuable industry resources now with full access to the digital edition of The Fabricator.
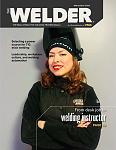
Easily access valuable industry resources now with full access to the digital edition of The Welder.
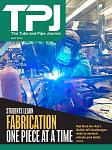
Easily access valuable industry resources now with full access to the digital edition of The Tube and Pipe Journal.
- Podcasting
- Podcast:
- The Fabricator Podcast
- Published:
- 04/16/2024
- Running Time:
- 63:29
In this episode of The Fabricator Podcast, Caleb Chamberlain, co-founder and CEO of OSH Cut, discusses his company’s...
- Trending Articles
Zekelman Industries to invest $120 million in Arkansas expansion
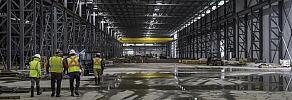
3D laser tube cutting system available in 3, 4, or 5 kW
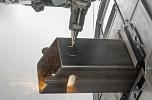
Corrosion-inhibiting coating can be peeled off after use
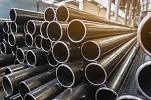
Brushless copper tubing cutter adjusts to ODs up to 2-1/8 in.
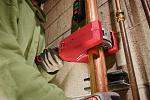
HGG Profiling Equipment names area sales manager
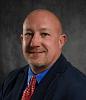
- Industry Events
16th Annual Safety Conference
- April 30 - May 1, 2024
- Elgin,
Pipe and Tube Conference
- May 21 - 22, 2024
- Omaha, NE
World-Class Roll Forming Workshop
- June 5 - 6, 2024
- Louisville, KY
Advanced Laser Application Workshop
- June 25 - 27, 2024
- Novi, MI