Founder
- FMA
- The Fabricator
- FABTECH
- Canadian Metalworking
Categories
- Additive Manufacturing
- Aluminum Welding
- Arc Welding
- Assembly and Joining
- Automation and Robotics
- Bending and Forming
- Consumables
- Cutting and Weld Prep
- Electric Vehicles
- En Español
- Finishing
- Hydroforming
- Laser Cutting
- Laser Welding
- Machining
- Manufacturing Software
- Materials Handling
- Metals/Materials
- Oxyfuel Cutting
- Plasma Cutting
- Power Tools
- Punching and Other Holemaking
- Roll Forming
- Safety
- Sawing
- Shearing
- Shop Management
- Testing and Measuring
- Tube and Pipe Fabrication
- Tube and Pipe Production
- Waterjet Cutting
Industry Directory
Webcasts
Podcasts
FAB 40
Advertise
Subscribe
Account Login
Search
Weighing all the tube bending machine options
Shops should look beyond a machine's specs and prioritize the whole operation
- By Jay Robinson
- September 9, 2023
- Article
- Tube and Pipe Fabrication
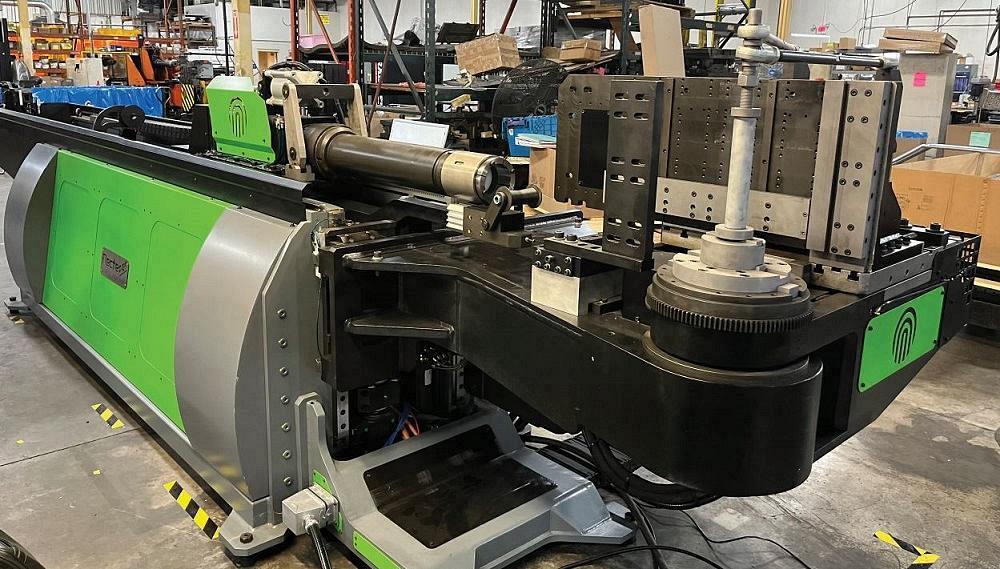
When considering upgrades, repairs, or new tube bending machines, metal fabrication shops should look beyond the equipment's technical capabilities and focus on business as a whole.
Contemplating buying a new CNC tube bender? Here are a few things to consider as you weigh factors like automation, repair, and replacement.
No Cookie-Cutter Solutions
Almost every conversation I’ve had about new CNC tube benders has started with the size of the machine. However, after going through the process with several customers over the past couple of months, I realized how unique the decision-making process can be for each customer.
Most manufacturers specify the size of their machines based on the maximum outside diameter of the tubing. However, this does not necessarily paint a complete picture of the machine’s capability. Bed length, axis speeds, maximum and minimum bending radii, multistack, multiradius, and many other factors should weigh into your decision.
“When we are talking to our customers about new benders, one of the questions we ask is, ‘Can you open up new opportunities by embracing new or different technologies?’” said Mike Thomas, president of Tube Form Solutions. “Adding capabilities like push bending that will allow you to combine traditional rotary draw bending and roll bending for larger bend radii in the same machine set up may allow you to go after bending projects that you could not before.”
Here are some examples of options and benefits:
- Left/right-hand bending - A machine that can bend in both directions may allow manufacture of complicated parts that could not otherwise be made in a single setup. A machine that accomplishes left- and right-hand bending by using a rotary head can effectively double the number of tool stacks that can be on the machine at one time.
- Cutoff - The ability to cut a part to length on the bending machine can allow for multiple parts to be manufactured in one load/unload sequence and can allow for more gripping surface at the clamp. The tube then can be trimmed back near the bending tangent.
- Hole punching/drilling - Adding punching capability can eliminate the need for this as a secondary process. Because the holes are punched during the bending process, their location in reference to the bends is assured.
- Reporting - Some control systems can provide live production and machine status reporting remotely, even troubleshooting data through the Internet of Things. The possibilities of this technology to aid in scheduling production, maintenance, and other activities are nearly endless.
- Multiple tool stacks - The ability to have multiple stacks of tooling on the machine may allow for more production of more complex parts or may allow you to leave multiple tool setups on the machine so changeover from one part to another can be accomplished with very little loss of production time.
Other machine features that may help improve your capability or provide better cycle times include a swing-away wiper, independent bend die rotation, and carriage boost.
Consider Automation
For high-volume production, automating bending processes can provide a rapid return on the additional investment. However, even lower-volume production can sometimes benefit from complete or even partial automation of the bending process, freeing an operator to focus on other tasks such as packaging or assembly.
“Even if you are not ready to build out a fully automated production cell right away, when considering a new tubing bender, give some weight to a machine whose mechanical design and control system will make it easier to automate in the future,” suggested Universal Tool and Engineering Owner Jamie Abraham.
Tooling
If you are already bending tubing, you know that a new machine may be a huge initial investment—but the bigger value may be in the tooling you already own. Buying a new machine from a manufacturer that does not use the same tool mounts as your existing tooling may create a need for a larger investment than intended.
Specific machine capabilities may make it possible to adapt the machine to existing tools. Specifically, multistack capabilities can allow more flexibility in adding adapters to the project so you can use your existing tooling. A machine with servo capability for the vertical movement of the tube relative to the bend die provides maximum flexibility to use existing tools with the new machine.
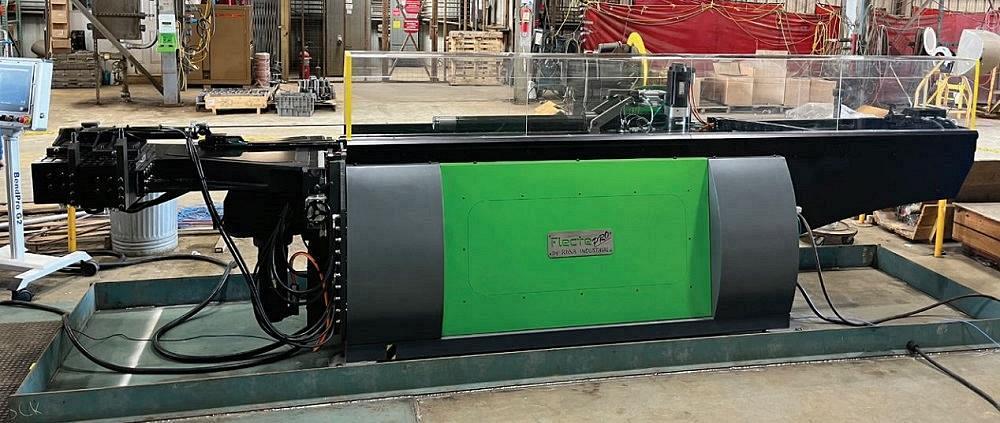
The decision to repair or replace a tube bending machine must incorporate a broader spate of factors than machine size or capacity. You have to consider your entire business.
New or Used
Buying a used or refurbished tube bender may make more sense than buying new.
If you are already forming tubes, finding an immediately available machine that works with your existing tooling won’t just increase your production capacity, it will provide redundancy when one of your production machines inevitably breaks down. Pre-owned machines can provide years of reliable service at a much lower initial cost—and often a better decision-to-delivery timeline.
Repair or Replace
We often work with customers who are struggling with the decision between repairing existing equipment or replacing it with new. Here are few benefits of new machines:
- Warranties
- More efficiency and lower operating costs (generally)
- Reduced maintenance cost and loss of production
- Improved accuracy
The Dollars and Cents
Finally, how you finance a machine can have a positive impact on the bottom line.
Borrowing may preserve cash for ongoing operations, or a lease may allow you to count every payment as an operating expense rather than just the interest. Work closely with your accountant and financial institution to come up with a finance plan that works for you.
About the Author
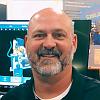
About the Publication
Related Companies
subscribe now
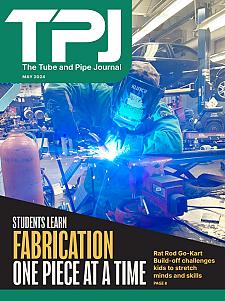
The Tube and Pipe Journal became the first magazine dedicated to serving the metal tube and pipe industry in 1990. Today, it remains the only North American publication devoted to this industry, and it has become the most trusted source of information for tube and pipe professionals.
start your free subscription- Stay connected from anywhere
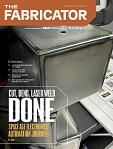
Easily access valuable industry resources now with full access to the digital edition of The Fabricator.
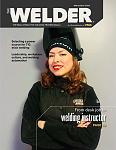
Easily access valuable industry resources now with full access to the digital edition of The Welder.
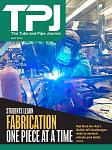
Easily access valuable industry resources now with full access to the digital edition of The Tube and Pipe Journal.
- Podcasting
- Podcast:
- The Fabricator Podcast
- Published:
- 04/16/2024
- Running Time:
- 63:29
In this episode of The Fabricator Podcast, Caleb Chamberlain, co-founder and CEO of OSH Cut, discusses his company’s...
- Trending Articles
Zekelman Industries to invest $120 million in Arkansas expansion
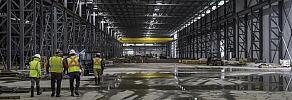
3D laser tube cutting system available in 3, 4, or 5 kW
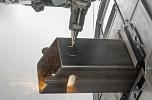
Corrosion-inhibiting coating can be peeled off after use
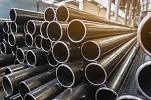
Brushless copper tubing cutter adjusts to ODs up to 2-1/8 in.
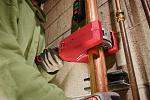
HGG Profiling Equipment names area sales manager
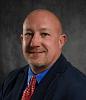
- Industry Events
16th Annual Safety Conference
- April 30 - May 1, 2024
- Elgin,
Pipe and Tube Conference
- May 21 - 22, 2024
- Omaha, NE
World-Class Roll Forming Workshop
- June 5 - 6, 2024
- Louisville, KY
Advanced Laser Application Workshop
- June 25 - 27, 2024
- Novi, MI