Editor
- FMA
- The Fabricator
- FABTECH
- Canadian Metalworking
Categories
- Additive Manufacturing
- Aluminum Welding
- Arc Welding
- Assembly and Joining
- Automation and Robotics
- Bending and Forming
- Consumables
- Cutting and Weld Prep
- Electric Vehicles
- En Español
- Finishing
- Hydroforming
- Laser Cutting
- Laser Welding
- Machining
- Manufacturing Software
- Materials Handling
- Metals/Materials
- Oxyfuel Cutting
- Plasma Cutting
- Power Tools
- Punching and Other Holemaking
- Roll Forming
- Safety
- Sawing
- Shearing
- Shop Management
- Testing and Measuring
- Tube and Pipe Fabrication
- Tube and Pipe Production
- Waterjet Cutting
Industry Directory
Webcasts
Podcasts
FAB 40
Advertise
Subscribe
Account Login
Search
Direct tube forming saves company and customers time, money, and headaches
Flexible cold forming technology tightens several aspects of tubemaking for Dundee Products
- By Lincoln Brunner
- September 15, 2022
- Article
- Tube and Pipe Production
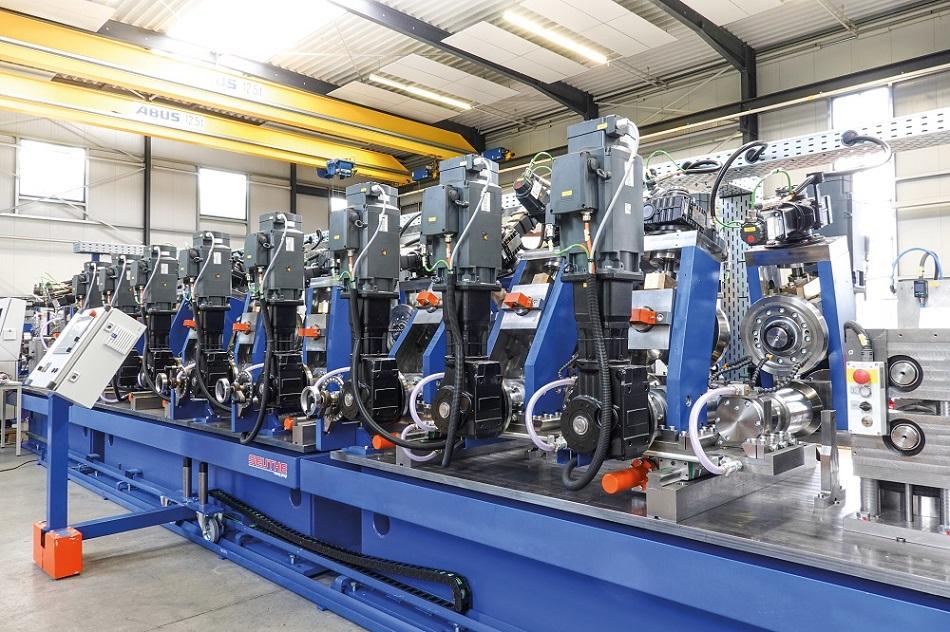
Seuthe introduced its FCF technology about 20 years ago. The company reports that material savings with the FCF can add up to the weight of one of these mills every 20 days.
Efficient production of steel tube has more natural enemies than a zebra in the Serengeti. Tooling changes, tooling wear, strip consistency, and strip availability—among many other factors—constantly threaten the productivity of tube mills.
For a manufacturer like Dundee Products in Dundee, Mich., which makes many varieties of square and rectangular tubing, changeover time alone can mean the difference between a profitable or unprofitable shift.
So, a few years ago, when Dundee was planning to expand its capabilities with a new tube mill, the company considered buying a replica of one of the conventional tube mills it already had. However, when Dundee looked at the work lined up for its new mill—mainly square and rectangular tubing—it learned about the Seuthe Flexible Cold Forming (FCF) 240 and ended its search there.
The FCF is a direct-forming mill, which rolls strip into square and rectangular tubing on an angle from the very first roll pass without using a round mother tube. The result is a nonround tube with a consistent wall profile around the entire diameter of the finished product.
“When we stumbled upon the FCF 240 that uses the universal tooling, that really caught our eye,” said Dundee Plant Manager Brian Yensch.
The universal tooling captured Dundee’s attention because the company manufactures dozens of sizes of round, square, and rectangular tubing for its customers in numerous industries, including automotive, camping, and medical. On one of Dundee’s conventional tube mills, changing from one size of tooling to another typically takes four to eight hours. On the FCF mill, it takes 20 to 30 minutes.
The mill, which is dedicated to square and rectangular tubing, can do this because the settings of each roll pass of the universal tooling are controlled by a PLC-driven servomotor. Those settings (recipes, if you will) are stored at each station for each product rolling off the line. So, the tooling doesn’t change—its positions do.
Changes for fully trained personnel are easy, according to Yensch. The roll stations are organized into three blocks. Each block is assigned a control screen, and adjustments necessary for new products or new types of strip can be changed right there on the panel, with all the rolls in a block moving in or out, up or down, in unison. Operators can even increase or decrease the torque of each servomotor individually.
And, if a motor malfunctions, the problem can be monitored and diagnosed remotely from Seuthe’s offices in Hemer, Germany, without Dundee having to shut down the line.
“This allows us to run if one does not function,” Yensch said. “They were able to log on from Germany, tie in, look into what was going on, and troubleshoot it remotely.”
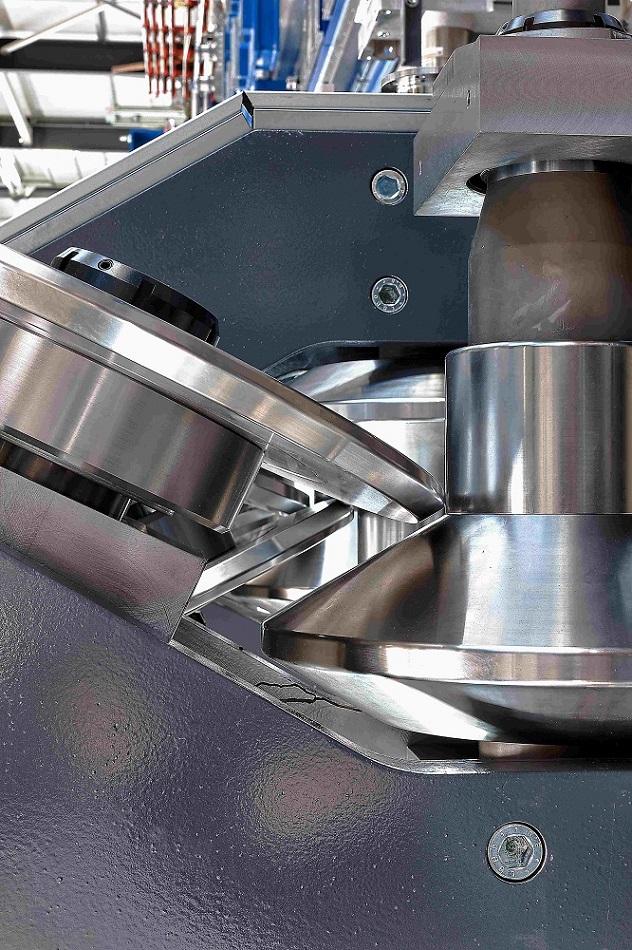
The flexibility of FCF mills lies in the ability to adjust its universal tooling to different product profiles.
And when the line is working properly again, the motors—once they are preset with the parameters of certain products—can switch back and forth with negligible delays in the operation. New product profile sizes can be positioned via integrated calculations and then optimized, Seuthe Project Manager Manfred Imberge noted.
“The servomotors are able to change the position [of the tooling], so we can go exactly to the same position for a different product,” said Imberge, who has worked with the FCF for the past 15 years. “[Dundee] can produce a lot of products with very short changeover times. They don’t have to make the investment in the roller sets.”
Considering how many different products Dundee produces, that savings on tooling sets adds up fast: One set of roll tooling on one of the company’s conventional round tubing mills produces only one size of tube but costs about 65% of one set of FCF tooling—from which Dundee creates about 30 different sizes of tube. In addition, Dundee can regrind the FCF tooling two or three times before a new set is needed. The result of that durability is about 43 million ft. of tubing on the FCF’s current tool set.
“We see a significant amount of footage our of them,” Yensch said.
Dundee Products makes square tubing from 0.75 to 2.5 in. OD. Its rectangular tubing ranges from 0.75 by 1.5 in. to 2 by 3 in. Yensch said that with Dundee’s product mix, slow changeovers really hurt production.
“That’s where it’s so critical to us,” he explained. “Sometimes on this new line, we can do four different profiles in a day and maybe a truckload of each, depending on the gauge. In a 10-hour shift, sometimes we’ll see three to four different jobs.”
In fact, Yensch said, if a customer calls at the end of one product run, the FCF is nimble enough that Dundee operators can break into the schedule, run the special order, and then pick up the original run where they left off with very little interruption.
“It just gives you a lot of flexibility,” Yensch said. “When customers call in a pinch, we’re able to help them out a lot more than we were on another line.”
And with just-in-time production being the rule of things now, customers don’t want to carry a lot of inventory they may not use (and profit from) right away. So it falls on producers like Dundee to respond quickly when those customers call with a gotta-have-it-now order.
“I think there’s always been that rush demand—I don’t see it going away,” Yensch said. “If anything, I see it increasing. Everybody waits until the last minute. They don’t want to make the purchase too soon [and] get stuck with something.”
Another aspect of material-consciousness addressed by the FCF is conservation of strip going into the mill.
Because the FCF is a direct forming mill, it forgoes round mother tubes altogether, precluding the inevitable corner thickening endemic to virtually all tubing created by conventional means. That direct forming means that a given size of tube—say, a 2- by 2-in. square—can be formed from a narrower strip than one would need when forming from a round mother tube. For makers of tube like Dundee that produce tens of millions of feet of tubing per year, the savings can total hundreds of thousands or even millions of dollars annually, according to Seuthe.
For example, Dundee used to produce 2-in. square tubing on a conventional mill with strip that was 7.814 in. wide. With the FCF, Dundee uses 7.569-in. strip to produce the same product. That’s almost a quarter inch of strip, multiplied by millions of feet per year, in Dundee’s case. And while Dundee’s customers purchase the steel that it processes on the FCF and its other mills, the savings is so significant that, according to Seuthe’s calculations, a tube mill running three shifts can save the equivalent of the FCF’s weight in steel about every three weeks.
“Every 20 days,” Imberge said. “It’s possible.”
The team at Dundee noted that the ease of use on the FCF makes them wish they could get universal tooling on round tubing mills.
“Just seeing how fast it is to run the material through the mill instead of … fighting it through each pass, it seems almost effortless,” Yensch said.
And while the material savings and changeover time on the mill have impressed Dundee, the quality of the tubing coming off the mill has pleased them just as much.“The quality is really good,” said Brent LeBlanc, quality manager at Dundee. “A lot of the tube on … the conventional mills that we have, we use up a lot of the tolerance. This [FCF] out here, when you set the mill to where you want it and get all your adjustments … you can get it all the way down, pretty much right on, plus or minus a thousandth.
“The corner radiuses are always really good—really tight. It’s very impressive. I love the mill.”
Dundee Products, Seuthe:About the Author
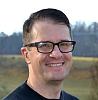
Lincoln Brunner
2135 Point Blvd.
Elgin, IL 60123
(815)-227-8243
Lincoln Brunner is editor of The Tube & Pipe Journal. This is his second stint at TPJ, where he served as an editor for two years before helping launch thefabricator.com as FMA's first web content manager. After that very rewarding experience, he worked for 17 years as an international journalist and communications director in the nonprofit sector. He is a published author and has written extensively about all facets of the metal fabrication industry.
About the Publication
Related Companies
subscribe now
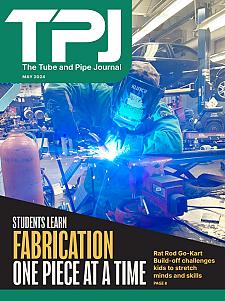
The Tube and Pipe Journal became the first magazine dedicated to serving the metal tube and pipe industry in 1990. Today, it remains the only North American publication devoted to this industry, and it has become the most trusted source of information for tube and pipe professionals.
start your free subscription- Stay connected from anywhere
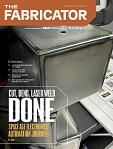
Easily access valuable industry resources now with full access to the digital edition of The Fabricator.
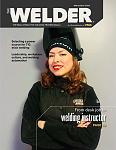
Easily access valuable industry resources now with full access to the digital edition of The Welder.
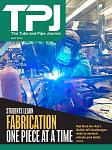
Easily access valuable industry resources now with full access to the digital edition of The Tube and Pipe Journal.
- Podcasting
- Podcast:
- The Fabricator Podcast
- Published:
- 04/16/2024
- Running Time:
- 63:29
In this episode of The Fabricator Podcast, Caleb Chamberlain, co-founder and CEO of OSH Cut, discusses his company’s...
- Trending Articles
Zekelman Industries to invest $120 million in Arkansas expansion
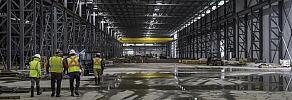
3D laser tube cutting system available in 3, 4, or 5 kW
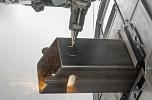
Corrosion-inhibiting coating can be peeled off after use
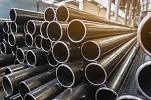
Brushless copper tubing cutter adjusts to ODs up to 2-1/8 in.
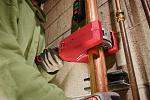
HGG Profiling Equipment names area sales manager
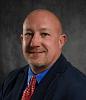
- Industry Events
16th Annual Safety Conference
- April 30 - May 1, 2024
- Elgin,
Pipe and Tube Conference
- May 21 - 22, 2024
- Omaha, NE
World-Class Roll Forming Workshop
- June 5 - 6, 2024
- Louisville, KY
Advanced Laser Application Workshop
- June 25 - 27, 2024
- Novi, MI