- FMA
- The Fabricator
- FABTECH
- Canadian Metalworking
Categories
- Additive Manufacturing
- Aluminum Welding
- Arc Welding
- Assembly and Joining
- Automation and Robotics
- Bending and Forming
- Consumables
- Cutting and Weld Prep
- Electric Vehicles
- En Español
- Finishing
- Hydroforming
- Laser Cutting
- Laser Welding
- Machining
- Manufacturing Software
- Materials Handling
- Metals/Materials
- Oxyfuel Cutting
- Plasma Cutting
- Power Tools
- Punching and Other Holemaking
- Roll Forming
- Safety
- Sawing
- Shearing
- Shop Management
- Testing and Measuring
- Tube and Pipe Fabrication
- Tube and Pipe Production
- Waterjet Cutting
Industry Directory
Webcasts
Podcasts
FAB 40
Advertise
Subscribe
Account Login
Search
Industry 4.0 tech, power transmission capability transform common pipe
Smart pipe uses sensors, transmitters, power gen for downhole applications
- By Eric Lundin
- March 5, 2021
- Article
- Tube and Pipe Production
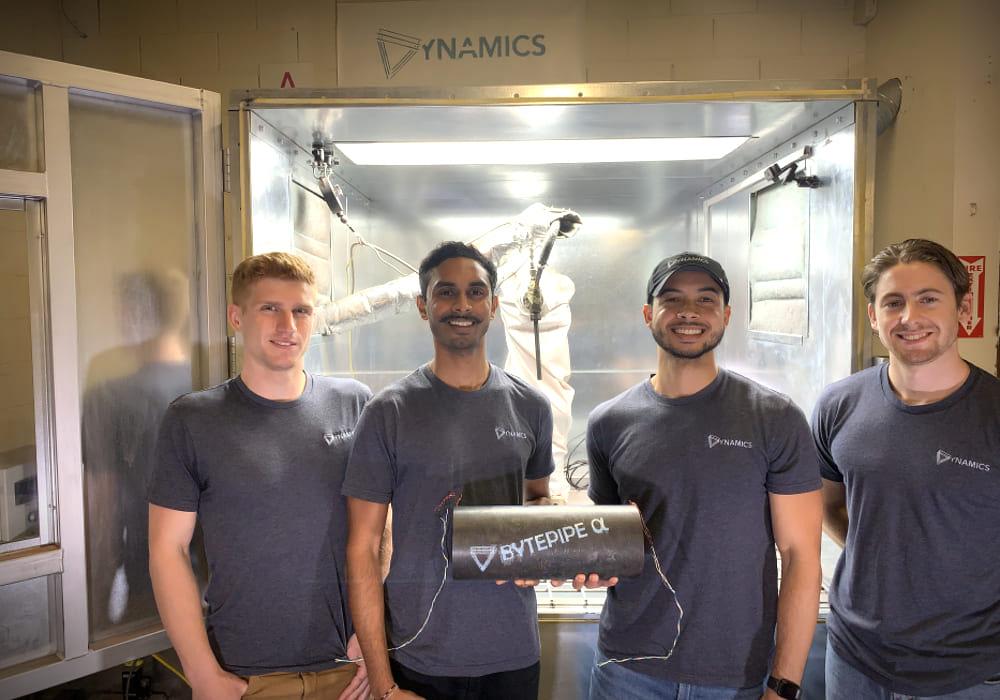
The principals of Tri-D Dynamics Inc. show an example of Bytepipe in front of a robotic workcell used to install the digital componentry: Director of Engineering Ben Nowack and the three cofounders, CEO Deepak Atyam, President Alex Finch, and Vice President of Operations Jesse Lang (l-r).
By definition, a pipe is a vessel through which a fluid flows. Although industry uses many types and styles of pipe for a multitude of applications, the essence of a pipe is that it’s a conduit that permits a flow from one point to another. Few of us would think a pipe could be more than this, but indeed specialized pipe can take on a bigger role.
A rethinking of pipe’s capabilities stands to revolutionize the oil and gas industry. The various stages of an oil or gas well’s life cycle–drilling, completion, and production—rely on a large number of tools that must be lowered into the well. Plugs and valves are used to isolate portions of the wellbore; setting tools are needed to put the plugs and valves in their intended locations; pulling tools retrieve plugs; shifting tools open and close valves as needed; swaging tools reform damaged pipe; and probing tools capture and retrieve mud samples. Some downhole tools even assist in operating other downhole tools. Two examples are fishing tools and jars, which are used to recover lost tools and deliver a kinetic energy strike to free a stuck tool, respectively.
Some of the tools are categorized as slickline, meaning they are lowered and retrieved by a cable. Others are wireline tools, meaning they are connected to electrical wire for carrying power or transmitting information.
Is this industry ready to incorporate some Industry 4.0 technologies, along with power transmission capability, into the wall of the pipe? The staff at Tri-D Dynamics thinks so.
Modern Upgrades for an Ancient Concept
Pipes in some form or other have been in use for thousands of years. Among the earliest was clay pipe, used for sanitation systems in the Middle East about 6,000 years ago. Copper pipe was used in Egypt more than 4,000 years ago, and of course Rome was known for its aqueducts and piping systems that supplied water for public baths, sanitation, fountains, and private households.Although formed metal pipe was modernized in the First Industrial Revolution (1760 to 1830 or so), and seamless steel pipe was developed by the Mannesmann brothers shortly thereafter (patented in 1886), pipe’s role didn’t change. In the decades since it has become a much more diverse and capable product, tougher and more corrosion-resistant than ever before, and some advanced thread designs are better than conventional threads at preventing leaks. But pipe is still pipe, and its sole role has been to move fluids.
“Modern pipe has served the needs of industry for more than 100 years,” said Deepak Atyam, president and co-founder of Tri-D Dynamics Inc. “Recently, the needs have changed.”
Needs certainly have changed. The digital revolution has been modernizing industry for decades. Affordable CNC and CAD/CAM systems proliferated in the 1970s and became progressively more sophisticated in the decades the followed. In the 2000s, a combination of sensor technology, Wi-Fi implementation, software capability, and a versatile infrastructure element—the internet—led to the development of Industry 4.0 technologies, which allow manufacturers to digitize nearly everything of value, capture it, and analyze it. Common bar codes, 2D bar codes, and especially RFID tags allow manufacturers to work with newfound ease and near-perfect accuracy to tally materials received, track orders as they move through the shop, and record orders shipped. These capabilities provide management an accurate view of nearly every aspect of production, allowing managers to track raw material levels, measure productivity, respond to a halted machine, and shift resources when necessary. The efficiency gains have been enormous.
Of course these technologies aren’t limited to manufacturing. It’s unlikely that any industry hasn’t adopted aspects of Industry 4.0 at this point.
A key capability is that these systems gather data and supply information continuously. Data-gathering functions don’t need to be started or stopped independently, and the data isn’t downloaded on command. The adjective that describes such systems is smart, indicating self-monitoring, analysis, and reporting.
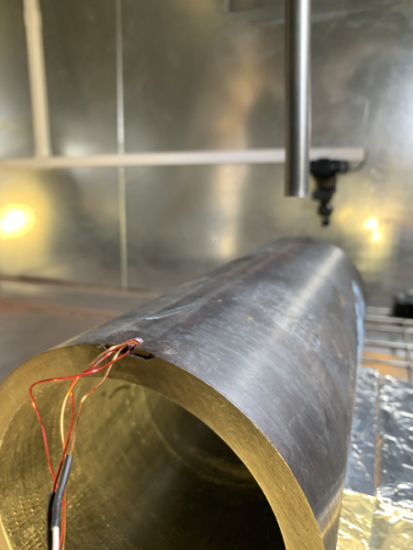
Tri-D Dynamics uses a suite of processes it calls Smart Metal Fusion to seal the pipe wall to protect the components.
As industry has progressed throughout the 2000s era, these new concepts, once optional, have become necessities.
Flying High Before Taking the Plunge. Getting into the nitty-gritty work of oilfield operations isn’t Atyam’s first application of a modern technology. During his student days at the University of California at San Diego, Atyam was part of a team that developed the first rocket engine built by additive manufacturing. The team included two other Tri-D Dynamics co-founders: Alex Finch (company president) and Jesse Lang (vice president of operations).
The success of this project certainly was a breakthrough moment, but perhaps not unexpected from a group of people who grew up in an environment noted for developing the technologies that the rest of us rely on. California, the founders’ home, is rich in the research and development that comes from the defense industry and Silicon Valley.
The success of the project, and the founders’ collective familiarity with Industry 4.0 technologies, set them off on a quest to develop ways to incorporate digital technology in infrastructure anywhere and everywhere. Their concept isn’t limited to pipe, but the oil and gas industry is an excellent candidate: it needs complex operations, monitored by robust sensors with comprehensive data-gathering capacity, in areas that are impossible to access by workers.
Downhole Operations. “In the three phases of well operations—drilling a borehole, completing the well, and production—the well operator uses monitoring tools to keep an eye on pressures, temperatures, flow rates, and so on,” Finch said. “They also send tools down the hole to do various things, such as injecting chemicals or steam to improve flow, or fracturing a layer of rock to start a flow of oil from a new location,” he said, adding that these are just two of many dozens of activities they carry out. Although some sensors are battery powered, others are wireline sensors.
The industry has a unique communication system. Just as Morse code relies on bursts of current traveling through telegraph lines, the drilling industry relies on pressure pulses that move through soil. Known as mud-pulse telemetry, it’s a classic example of necessity leading to an invention. The downside is that it isn’t very fast. A typical system transfers about 40 bits of information per second at shallow depths; at 35,000 ft., the rate can be as slow as 0.5 bit per second. It works and it’s effective, but in a 5G world with data transfer rates around 300 million bits per second, it appears that the drilling industry stands to benefit from a completely new way of moving information, one that can get well operators the data they need much more quickly than with mud-pulse telemetry.
Why not build sensor, communication, and power transmission capabilities into the wall of the pipe?
Building a Smart Pipe
The foundational element of the smart pipe network concept envisioned by Tri-D is called Bytepipe. It consists of off-the-shelf pipe that Tri-D modifies.After determining a piping system’s digital or power transfer functions, the staff develops the hardware needed to fulfill those functions. It then cuts a groove lengthwise along the pipe to match the hardware’s footprint and installs the hardware.
The company then uses a process it calls Smart Metal Fusion to seal the groove to protect the components. Smart Metal Fusion isn’t a single process but rather a suite of processes, developed in-house based on the staff’s extensive metals background. The fusion techniques include welding, additive manufacturing, and metal spray; the specific process used for a particular application is chosen to correspond with the pipe’s base material and the intended working environment.
“All of the processes have the necessary adhesion, and they contribute to the structural integrity to the pipe,” Finch said.
“We ran thousands of simulations and performed many physical trials to develop the processes,” Atyam said.
Tri-D doesn’t build each system from scratch. It relies on a period of research and development it used to create a plug-and-play system for a variety of sensors types.
While nobody would mistake a length of pipe for a mobile phone, the staff at Tri-D see their work as the basis for additional work, just as third-party developers dreamed up countless apps for the Apple and Android operating systems.
“Like anything else with a digital foundation, it becomes a platform,” Atyam said.
“Conventional pipe has become commoditized,” Finch said. “Digital capability will separate the early adopters from the pack and transform pipe into a value-add product.”
The company has two products in the pipeline that use the Bytepipe electro-mechanical architecture. The most fully featured product is TMC (track, monitor, control), which is scheduled for rollout in 2022. Another product, Tracer, has an identification feature and is slated for rollout first. Similar to affixing an RFID tag to a pallet of raw materials to prevent a mixup with a similar pallet of a different material, Tracer has embedded components that provide an identifying signal to help prevent product mixups and eliminate theft. They teamed up with global steel and pipe distributor Marubeni-Itochu Steel Inc., which has headquarters in Tokyo, to bring this product to market.
Powering Through a New Era of Infrastructure Applications
This concept could be adapted for other uses involving boreholes. A geological project comprising an array of smart pipes has the potential to warn of seismic events and provide detailed information about the magnitude and propagation velocity after one occurs.The construction industry likewise stands to gain from this development. Tube’s use in architecture is growing and is bound to continue to expand. As measured by strength-to-weight ratio, a hollow structural section (HSS) is superior to a conventional building component such as a beam or a channel. Favored for aesthetics as well, a length of HSS is suitable for routing (and hiding) electrical cables, data lines, and possibly plumbing lines. One day power lines and data might flow through the walls of HSS products.
Architectural components in the future might deliver power where it’s needed in all sorts of constructions. Applications might be aesthetic, for example by providing illumination options in a building, or they might concern safety, providing lighting options for bridges and other infrastructure. A third option is utilitarian, providing power for various systems, much like the aforementioned downhole drilling tools.
The key to providing power for a utility application is the quantity, of course. In Tri-D Dynamics’ smart pipe, this doesn’t seem to be a limiting factor.
“We can transfer 1,000 amps between pipe connections,” Atyam said.
Of course the concept isn’t limited to tubular products. For example, if sensor technology were used in bridge construction, it could report changes in loading and vibration activity. Smart gussets or other smart construction materials could have the potential to report structural changes with the aim of preventing a structural failure. When the I-35W Mississippi River bridge near Minneapolis fell into the river in 2007, the immediate cause was a gross overload, but the bridge had been in a state of extreme stress for years; at least one gusset plate had begun to fail as early as 2003. If this had been reported properly, it’s possible that the bridge would have been repaired and 13 lives wouldn’t have been lost.
Bringing digital and power transmission to all infrastructure installations is actually Tri-D Dynamics’ goal. Essentially anything made of metal has the potential to be part of a smart infrastructure.
“Regardless of what it is, when data and power flow through it, new possibilities open up,” Finch said.
About the Author
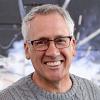
Eric Lundin
2135 Point Blvd
Elgin, IL 60123
815-227-8262
Eric Lundin worked on The Tube & Pipe Journal from 2000 to 2022.
About the Publication
Related Companies
subscribe now
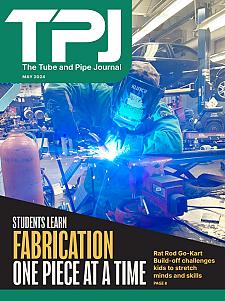
The Tube and Pipe Journal became the first magazine dedicated to serving the metal tube and pipe industry in 1990. Today, it remains the only North American publication devoted to this industry, and it has become the most trusted source of information for tube and pipe professionals.
start your free subscription- Stay connected from anywhere
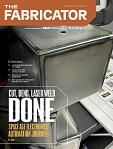
Easily access valuable industry resources now with full access to the digital edition of The Fabricator.
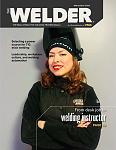
Easily access valuable industry resources now with full access to the digital edition of The Welder.
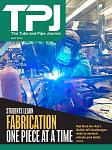
Easily access valuable industry resources now with full access to the digital edition of The Tube and Pipe Journal.
- Podcasting
- Podcast:
- The Fabricator Podcast
- Published:
- 04/16/2024
- Running Time:
- 63:29
In this episode of The Fabricator Podcast, Caleb Chamberlain, co-founder and CEO of OSH Cut, discusses his company’s...
- Trending Articles
Zekelman Industries to invest $120 million in Arkansas expansion
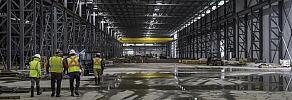
3D laser tube cutting system available in 3, 4, or 5 kW
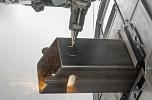
Corrosion-inhibiting coating can be peeled off after use
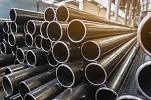
Brushless copper tubing cutter adjusts to ODs up to 2-1/8 in.
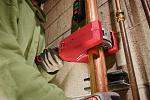
HGG Profiling Equipment names area sales manager
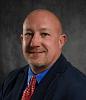
- Industry Events
16th Annual Safety Conference
- April 30 - May 1, 2024
- Elgin,
Pipe and Tube Conference
- May 21 - 22, 2024
- Omaha, NE
World-Class Roll Forming Workshop
- June 5 - 6, 2024
- Louisville, KY
Advanced Laser Application Workshop
- June 25 - 27, 2024
- Novi, MI