Editor
- FMA
- The Fabricator
- FABTECH
- Canadian Metalworking
Categories
- Additive Manufacturing
- Aluminum Welding
- Arc Welding
- Assembly and Joining
- Automation and Robotics
- Bending and Forming
- Consumables
- Cutting and Weld Prep
- Electric Vehicles
- En Español
- Finishing
- Hydroforming
- Laser Cutting
- Laser Welding
- Machining
- Manufacturing Software
- Materials Handling
- Metals/Materials
- Oxyfuel Cutting
- Plasma Cutting
- Power Tools
- Punching and Other Holemaking
- Roll Forming
- Safety
- Sawing
- Shearing
- Shop Management
- Testing and Measuring
- Tube and Pipe Fabrication
- Tube and Pipe Production
- Waterjet Cutting
Industry Directory
Webcasts
Podcasts
FAB 40
Advertise
Subscribe
Account Login
Search
Investing in America’s tube and pipe industry and false promises of offshoring
New investments signal cautious optimism from tube industry giant Zekelman Industries
- By Lincoln Brunner
- October 25, 2022
- Article
- Tube and Pipe Production
Zekelman Industries is investing hundreds of millions of dollars in the U.S. tube and pipe industry in the belief that the economy will reward those who steward their resources well.
People willing to admit it know: Success often comes from being in the right place at the right time.
Up until recently, building brand-new tubemaking capacity in the U.S. probably would have required importing most of the raw steel to make it. What’s more, most people probably would have considered that good sourcing (even if grudgingly). COVID-19 put that logic to the test as global supply channels dealt with choke points all along the chain—a problem that continues today.
Now, with recent advances in the American steelmaking scene, like Nucor Corp.’s new Brandenburg, Ky., plate mill and U.S. Steel Corp.’s acquisition of Big River Steel, major tube players like Zekelman Industries are eyeing the chance to expand domestic tube production with domestic feedstock.
Zekelman subsidiary Atlas Tube recently cut the ribbon on its second Blytheville, Ark., plant, a $150 million expansion dedicated to jumbo hollow structural sections (HSS) as large as 28-in. OD and 1-in. wall thickness. It also recently began commissioning the mills at its $130 million Wheatland Tube conduit facility in Rochelle, Ill.
At the Rochelle facility, the company is updating its antiquated conduit-making capacity with the latest equipment, company CEO Barry Zekelman told The Tube & Pipe Journal.
“We’re very excited,” Zekelman said of the Wheatland Rochelle plant. “It’s an absolutely state-of-the-art facility—fully automated warehouse, fully automated slitter. The mills are the first of their kind in the world. The two of them will run up to 1,200 feet a minute and have everything completely automated front to back. So, we’re really excited about what we see there in terms of the quality, the speed, the efficiency, and the safety for our teammates.”
As for the Atlas expansion, Zekelman said his company made the investment so it could capitalize on movement in the construction market, particularly in HSS for warehouses. HSS can carry the same loads as solid steel sections with far less material, a boon to expansive structures that often reach 80 to 100 ft. high.
“We wanted to … move into larger sections and heavier walls because of what we saw going on in the construction industry, the trends that were there—these much taller warehouses with automated storage and retrieval systems,” Zekelman said. “Those warehouses need uninterrupted columns that’ll go to the roof to carry much heavier loads.
“The steel [in HSS] can be 30 percent of what a jumbo beam would be,” he said. “In today’s day and age, everyone’s looking at how we’re building these buildings, how efficient they are … to get built, from a mill to a fabricator to a job site. You’re using a lot less weight, so your embodied carbon is a lot less in the building. We’re continually seeing people ask for this—the Amazons, the Lowe’s, all of these companies that are building these buildings.”
Zekelman noted that if his company had made these recent moves five years ago, he would have had to import a lot of the steel for the tubes made at his plants. He didn’t want to do that.
“I wanted to use domestic steel,” said Zekelman, who is Canadian but spoke mainly about his company’s U.S.-based operations. “The mills making the investment gave us the ability to make the investments. It was really welcome [news] to see them invest in the future of what could be made here in America, as well.”
Part of the push for Zekelman was watching, and learning from, the COVID-related supply chain tribulations of companies from all corners of the manufacturing sector. His observations were affirmed by the Federal Reserve Bank of New York in its recently introduced Global Supply Chain Pressure Index (GSCPI). The index uses data from the U.S. transportation and manufacturing industries to track the state of global supply chains.
“Supply chain disruptions have become a major challenge for the global economy since the start of the COVID-19 pandemic,” the New York Fed stated on its website. “The moves in the GSCPI from the beginning of 2022 suggest that although global supply chain pressures have been decreasing, they remain at historically high levels.”
Much of the global supply bottleneck centers on China and its continued COVID-related problems, which have disrupted its exports of many products, notably electronic components. Zekelman, who didn’t specifically name China as a culprit in the current supply conundrum, said that while he’s a firm believer in free trade, he matches that with a belief in fair trade and smart trade.
“I think everyone got exposed to the fact that our supply chain is brutally vulnerable,” he said. “As a country—in many countries—we put all of our eggs in one basket. We got caught, and look what it did.
“So, cheap all of a sudden wasn’t so cheap when you can’t get a microchip to put into a car because you were buying 100 percent of it offshore and that got disrupted,” he added. “It’s irresponsible that anyone would let that happen to their company, and it’s foolish. I think we’ve seen that we have to bring things back here and that it isn’t always about grinding out the last penny.”
Zekelman foresees some rough seas ahead as manufacturers make their way through an economy replete with inflation, interest rate hikes, and personnel challenges.
“We also have to take care of our communities and employ people here and pay them fair wages so that they can make things here,” he said. “I think there’s going to be a big resurgence to making things here.
“I’m cautiously optimistic. I see some red flags and some periods that are going to be quite tough here. You have to continue to invest in … systems that will make you faster and able to deliver your product faster and more efficiently—and provide a workplace that’s attractive for people to go to. This is not going to be easy the next few years. The good stewards and captains that can navigate through it are going to come out way, way on top.”
About the Author
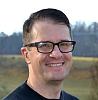
Lincoln Brunner
2135 Point Blvd.
Elgin, IL 60123
(815)-227-8243
Lincoln Brunner is editor of The Tube & Pipe Journal. This is his second stint at TPJ, where he served as an editor for two years before helping launch thefabricator.com as FMA's first web content manager. After that very rewarding experience, he worked for 17 years as an international journalist and communications director in the nonprofit sector. He is a published author and has written extensively about all facets of the metal fabrication industry.
About the Publication
subscribe now
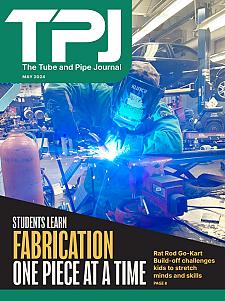
The Tube and Pipe Journal became the first magazine dedicated to serving the metal tube and pipe industry in 1990. Today, it remains the only North American publication devoted to this industry, and it has become the most trusted source of information for tube and pipe professionals.
start your free subscription- Stay connected from anywhere
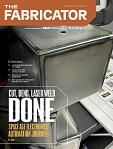
Easily access valuable industry resources now with full access to the digital edition of The Fabricator.
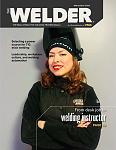
Easily access valuable industry resources now with full access to the digital edition of The Welder.
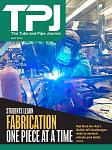
Easily access valuable industry resources now with full access to the digital edition of The Tube and Pipe Journal.
- Podcasting
- Podcast:
- The Fabricator Podcast
- Published:
- 04/16/2024
- Running Time:
- 63:29
In this episode of The Fabricator Podcast, Caleb Chamberlain, co-founder and CEO of OSH Cut, discusses his company’s...
- Trending Articles
Zekelman Industries to invest $120 million in Arkansas expansion
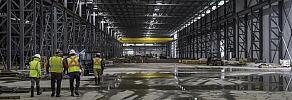
3D laser tube cutting system available in 3, 4, or 5 kW
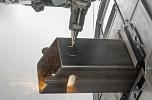
Corrosion-inhibiting coating can be peeled off after use
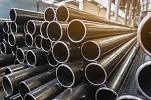
Brushless copper tubing cutter adjusts to ODs up to 2-1/8 in.
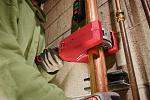
HGG Profiling Equipment names area sales manager
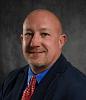
- Industry Events
16th Annual Safety Conference
- April 30 - May 1, 2024
- Elgin,
Pipe and Tube Conference
- May 21 - 22, 2024
- Omaha, NE
World-Class Roll Forming Workshop
- June 5 - 6, 2024
- Louisville, KY
Advanced Laser Application Workshop
- June 25 - 27, 2024
- Novi, MI