- FMA
- The Fabricator
- FABTECH
- Canadian Metalworking
Categories
- Additive Manufacturing
- Aluminum Welding
- Arc Welding
- Assembly and Joining
- Automation and Robotics
- Bending and Forming
- Consumables
- Cutting and Weld Prep
- Electric Vehicles
- En Español
- Finishing
- Hydroforming
- Laser Cutting
- Laser Welding
- Machining
- Manufacturing Software
- Materials Handling
- Metals/Materials
- Oxyfuel Cutting
- Plasma Cutting
- Power Tools
- Punching and Other Holemaking
- Roll Forming
- Safety
- Sawing
- Shearing
- Shop Management
- Testing and Measuring
- Tube and Pipe Fabrication
- Tube and Pipe Production
- Waterjet Cutting
Industry Directory
Webcasts
Podcasts
FAB 40
Advertise
Subscribe
Account Login
Search
Tips for maximizing tube, pipe mill efficiency (Part II)
Eliminating bottlenecks, speeding up changeovers are key to enhancing a mill’s productivity, uptime
- By Eric Lundin
- November 2, 2021
- Article
- Tube and Pipe Production
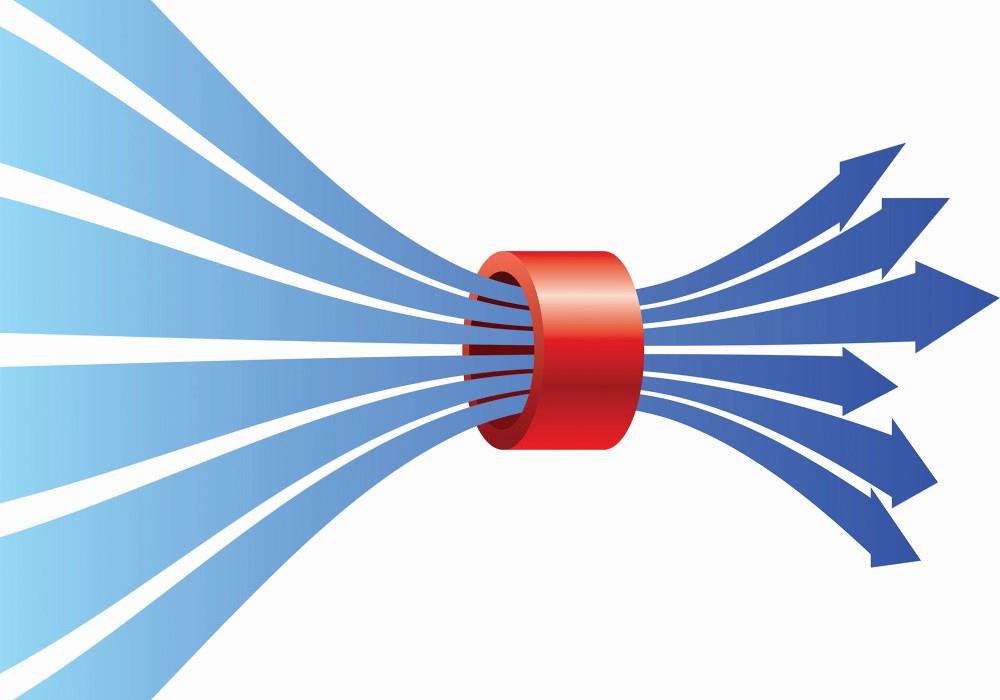
Everyone in every processing industry wants maximum uptime and maximum yield, but when raw materials are expensive and scarce, these concerns are especially acute. Getty Images
Editor’s note: This is the second installment in a two-part series on optimizing tube or pipe mill operations. Read the first part here.
Finding, Reducing, Eliminating Bottlenecks
The pace at which the strip moves through the mill, from one station to the next—breakdown, forming, welding, sizing, and straightening—sets the pace for everything else. The mill’s reference speed is the maximum speed at which it makes a properly formed tube with a robust, durable weld.“The limitations often are in the entry and exit areas,” said Nelson Abbey, director of Abbey Products at Fives Bronx Inc. Efficient mill operations can be hampered by material handling and coil joining at the entry end; cutting the product to length and getting tubulars off the mill likewise tend to impose limits at the exit end.
Getting the Coil Into the Mill. If the coils are long, butt welding the outgoing coil to the incoming coil might take place every 15 or 20 min., and the operator gets a break between each one, Abbey said. If the coils are short and take only 5 min. or so to work their way through the mill, the end-joining process is likely to be the mill’s productivity limit. Longer coils mean less frequent mill stoppages and put less stress on the operator, he said.
Most such butt welds serve just one purpose—keeping the two coils joined until the new coil has worked its way through the mill—and the butt weld is discarded after that section goes through the cutoff.
For some applications, the butt weld serves a second purpose. For long lengths of coiled tubing, which can be miles long, the butt welds are a product feature and must be just as durable and leakproof as the longitudinal welds. Although an arc welding process is traditional, laser technology is making inroads relative this application, said Kevin Arnold, Midwest sales manager for IPG Photonics. The benefits are the same as those for making the longitudinal weld with laser technology, especially the minimal heat input and minimal ensuing distortion.
“The lower heat input and smaller heat-affected zone create a more durable weld,” said Mark Wagner, vice president of sales for Guild International. “A hard, brittle weld is prone to breaking as the joint moves through the mill. The tension can be enormous and often is more than enough to break the weld. When using a laser to join the coils, Guild has found that weld breaks are greatly reduced, and that the line can get back up to speed much quicker.”
“Another issue is the weld bead’s thickness,” he said. “Arc welding processes typically leave a thick weld bead. The additional thickness accelerates the wear on the roll tooling and other equipment, like inline tension levelers, so the weld has to be treated with either manual or automatic milling to reduce the weld bead, so the thickness is consistent. Laser welding doesn’t leave a raised weld bead, so it eliminates postweld treatments such as milling.”
The initial process, making the butt weld, also tends to go more quickly with laser welding than arc welding processes, he added.
Make It, Cut It, and Move It Out. When all is nearly said and done on the mill, the focus turns to the cutoff process. Some products simply take more time to cut than others. Even a product that usually is made at a fast rate and is easy to cut—say, a light-wall, small-diameter tube—can slow a mill down if the final cut lengths are short. The saw has to move at the same speed as the tube to make the cut, return to its starting position, then get back up to the mill’s speed to make the next cut. As the cut lengths decrease, the saw’s accelerations have to become increasingly faster to keep up.
Beyond the cutoff, carrying out finishing as part of the production process can create a bottleneck.
“Flushing the chips out of the tube, facing, and bundling them are additional processes that usually slow down a line,” Abbey said. The problem is that these run in different ways, Abbey explained.
“A mill runs most efficiently when it’s running consistently at a constant speed,” he said. “Finishing operations are start-and-stop processes.” On the surface, the difference is the pace of the mill versus the pace of the finishing steps, but it goes deeper.
“Every line stop creates at least one length of scrap,” Abbey said. Another drawback is the time it takes to ramp up the mill. “You don’t press a button and get back to full speed,” he said. “For typical mills, it can take 10 minutes or so.”
Depending on the system’s design, which often is influenced by limited floor space and obstructions such as building columns, such a connected system might just be inherently inefficient. Designing a generous buffering capacity between processes that run at substantially different rates is a good solution, depending on handling complexity. But if it’s impossible to include a buffer, or if the buffer is undersized, a lower overall production rate is inevitable.
It seems counterintuitive to connect a mill to finishing equipment, but indeed many mills are set up in this way. Depending on the product and how fast it runs through the mill, this setup isn’t detrimental to operational efficiency. For example, among mills designed to make products according to American Petroleum Institute specifications, about half of them can be connected to the finishing system with no effect on productivity, Abbey said. However, many such setups would run faster if they were disconnected.
What are the benefits? Such a setup uses less labor power than a disconnected system, and it takes up a smaller footprint than a disconnected setup, so many tube and pipe producers are willing to sacrifice some line speed and possibly lower overall product rates for these benefits.
On some mills, processes such as flushing and bundling are manual, which can be even more detrimental. In some cases, these end-of-mill processes bring the mill speed down by half, Abbey said. It’s a tradeoff—the company makes a smaller capital investment and brings in less revenue—but it can have unintended consequences. The operators become accustomed to the mill’s pace, and even if the company upgrades to automated flushout and bundling, it can have a lot of difficulty with the return on investment. After learning to do the job at 200 ft./min., the operators simply aren’t comfortable operating a mill that runs at twice that pace.
Changeovers
Selecting the right tooling for the job seems like an obvious first step, but mixups do happen. Mounting the wrong tooling—say, substituting tooling with a modified edge break for tooling with a standard edge break—makes it more difficult to make good product, and it compromises the tooling life, said Warren Wheatman, vice president of T&H Lemont’s Tooling Business Unit. The same goes for mounting the tooling correctly. When tools are reconditioned, the company that did the grinding usually provides a set of bearing block shims for proper mounting. In many cases, the shims get misplaced or their purpose isn’t understood and they are discarded. The tooling can’t do its job properly without the shims.Getting the tooling aligned is the next step. Automated tool positioning devices are available, but many tube and pipe producers still rely on manual setups.
“Motorized adjustments with position feedback at each pass can help the setup go much faster, leaving only a small amount of manual tweaking to finalize the setup,” Abbey said. The same goes for the settings of the straightener, he said. The only caveat is that the maintenance staff has to be knowledgeable on how every device works and how everything is wired, and the company has to keep sufficient spares of every critical device in its inventory. Otherwise, just one bad component like an encoder can slow the process substantially, especially if used in an automated quick-change mill.
Does a tube producer need quick-change hardware, electronic positioning devices, and other hardware to reduce its changeover time? No. According to Abbey, good procedures and a motivated crew can cut changeover time nearly in half. He cited one 10-in. mill that had standard equipment and no quick-change features or setup assistance of any sort. While most such mills need five to eight hours for a changeover, one company with a motivated crew equipped with well-documented procedures could get it done in three and a half hours.
If a mill can accommodate rafts—subplates with tooling mountings—it can cut the mill’s downtime by a large amount, frequently up to 75%. It still takes time to do the changeover, so the company still needs the labor to change out the tooling on the raft, but it does so while the mill is still running and making money.
Of course, planning goes into this like it does everything else. Michael Strand, president of T&H Lemont, suggests three rafts per mill. While one raft is on the mill and making money, a second raft can be prepped with tooling for the next run. The rafts themselves have a large number of moving parts, so the third raft can be set aside for a teardown, inspection, and repairs if necessary.
“Threading is also a candidate for improvement on some mills,” Abbey said. “When threading a new strip through the mill, it’s common practice to jog the mill, starting and stopping numerous times. Once threaded, the mill is then typically run for a short distance to check the weld and do sizing adjustments, which generates a substantial amount of scrap. Simple improvements in this area can be obtained by streamlining the steps and by including interlocks with the welder so it can weld and jog at the same time.”
“It would generate less scrap if the company that made the welding power supply would change the controls so the mill could jog the material forward, weld, and scarf simultaneously,” he continued. “On large mills this is a necessity, and it really reduces the amount of scrap generated at each startup.”
Bringing It All Together
The essence of tube or pipe mill efficiency hasn’t changed, but in times like these, it’s more critical than ever. The revenue a mill generates while it’s running is always offset by the losses it incurs when it’s not, but times such as these seem to amplify the losses. Steel prices are higher than normal, and some materials simply aren’t available, so keeping the mill running and minimizing scrap are two considerations that are in sharp focus right now.Best Practices. These industry experts, each of whom has decades of experience in the field, provided informed insights and perspectives regarding best practices:
- “Every changeover involves downtime and scrap, and traditionally these are the two areas where tube and pipe producers can make the biggest gains,” Abbey said. “Every mill supervisor needs to study their changeover procedures.”
“It’s important to perform every maintenance action according to the schedule and document everything,” Strand said. Track every action on the mill, including the number of feet of product made by each set of roll tooling during each run, to stay on top of mill maintenance from a big-picture, years-long perspective.
- “It’s helpful to use a status board or checklists that show each major step described clearly and concisely,” Abbey said. “Whether it is a changeover or a routine maintenance procedure, such as inspecting tooling, using checklists adds to consistency and efficiency,” Abbey said.
Using automated systems and devices to assist with mill setup can keep changeover time to a bare minimum. Abbey cited one special, automated mill that had its changeovers down to a science, relying extensively on such hardware, and it achieved consistent 15-min. changeovers. In that case, it was necessary to keep operator intervention to a minimum.
“Tube and pipe producers need to be careful how they use the mill,” said Stan Green, general manager for SST Forming Roll Inc. “Many of the materials available these days are much harder than common carbon steels, and the steel producers seem to introduce stronger materials all the time,” he said. Using a mill designed for carbon steel with a 50,000-PSI minimum yield strength to process 80,000-PSI material is going to accelerate the wear on every component on the mill and likely will break something—and sooner rather than later.
Inspections, maintenance, alignments, and yield work together, especially with tooling and roll stands.
“The weakest point is the point that moves [out of position],” Green said. He cited a tiny bit of movement, anything more than 0.010 in., as too much movement. “Proper tooling position is important for a consistent process and to maximize yield, but you can’t keep the tooling in the right position if the bearings and shafts are worn,” he said.
Budgetary Matters. Regular maintenance is always important. It’s a critical issue day after day, week after week, month after month, year after year. Following the suggested maintenance schedule for every item isn’t more important when runs are shorter and changeovers are more frequent, but these activities are more likely to be delayed or even overlooked during difficult times.
“When times are good, tube and pipe producers hesitate to stop production for maintenance,” said Michael Strand, president of T&H Lemont. “When times are tough, they don’t want to spend the money.” And although many mills are running full-tilt right now, a sign of good times, some of the business conditions are tough—especially the sky-high cost of raw materials and the less-than-reliable supply chains, fallout from the pandemic.
“More money spent on the raw material and more time spent on changeovers means less money and time for scheduled maintenance,” said Dan Ventura, president of Ventura & Associates. It’s not just a matter of spending money, but spending it wisely. It takes high-quality machinery and consumables to make high-quality products, and better investments can pay off.
“When buying tooling, many tube producers work right off the quotes and make decisions based on price,” Strand said. If it’s not a trustworthy tooling provider, it’s impossible to know if the tooling is made to the right design for your mill, made from the proper alloy, and if it was heat-treated properly.
The same goes for the ferrite used in the impeder, said John Holderman, general manager for EHE Consumables.
Few would go so far as to research something that many would regard as a minute detail, but ferrite varies in grade, which equates to its capacity to do its job. To provide the best use of electrical energy, the ferrite must have three characteristics: low losses, high permeability, and high saturation of flux density. For durability, it needs construction methods and binders that resist heat.
The same goes for everything else on the mill. Frugality is one thing, but taking that too far can mean dedicating disproportionate time and effort on repairs and incurring more downtime than necessary as the equipment ages.
Breaking the Speed Limit. If a company does adhere to every best practice, where can it go from there? For those who are prepared, there is one more boundary to be pushed.
“When everything is dialed in, the operator has one more thing he can do to maximize throughput,” Abbey said. “A motivated operator can run the mill a little faster than he’s accustomed to.” Abbey acknowledges that this means the operator has to work outside of his comfort zone, and this isn’t easy, but this is one last area for productivity gains, and perhaps the only way to find out what the mill really can do.
About the Author
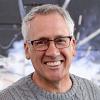
Eric Lundin
2135 Point Blvd
Elgin, IL 60123
815-227-8262
Eric Lundin worked on The Tube & Pipe Journal from 2000 to 2022.
About the Publication
subscribe now
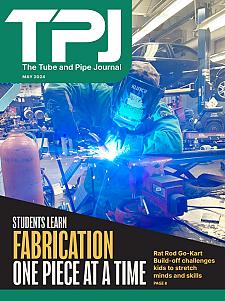
The Tube and Pipe Journal became the first magazine dedicated to serving the metal tube and pipe industry in 1990. Today, it remains the only North American publication devoted to this industry, and it has become the most trusted source of information for tube and pipe professionals.
start your free subscription- Stay connected from anywhere
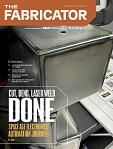
Easily access valuable industry resources now with full access to the digital edition of The Fabricator.
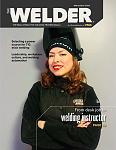
Easily access valuable industry resources now with full access to the digital edition of The Welder.
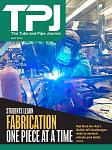
Easily access valuable industry resources now with full access to the digital edition of The Tube and Pipe Journal.
- Podcasting
- Podcast:
- The Fabricator Podcast
- Published:
- 04/16/2024
- Running Time:
- 63:29
In this episode of The Fabricator Podcast, Caleb Chamberlain, co-founder and CEO of OSH Cut, discusses his company’s...
- Trending Articles
Zekelman Industries to invest $120 million in Arkansas expansion
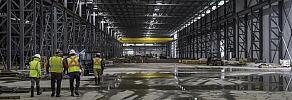
3D laser tube cutting system available in 3, 4, or 5 kW
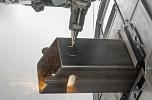
Corrosion-inhibiting coating can be peeled off after use
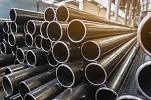
Brushless copper tubing cutter adjusts to ODs up to 2-1/8 in.
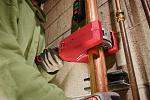
HGG Profiling Equipment names area sales manager
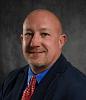
- Industry Events
16th Annual Safety Conference
- April 30 - May 1, 2024
- Elgin,
Pipe and Tube Conference
- May 21 - 22, 2024
- Omaha, NE
World-Class Roll Forming Workshop
- June 5 - 6, 2024
- Louisville, KY
Advanced Laser Application Workshop
- June 25 - 27, 2024
- Novi, MI