Regional Sales Manager
- FMA
- The Fabricator
- FABTECH
- Canadian Metalworking
Categories
- Additive Manufacturing
- Aluminum Welding
- Arc Welding
- Assembly and Joining
- Automation and Robotics
- Bending and Forming
- Consumables
- Cutting and Weld Prep
- Electric Vehicles
- En Español
- Finishing
- Hydroforming
- Laser Cutting
- Laser Welding
- Machining
- Manufacturing Software
- Materials Handling
- Metals/Materials
- Oxyfuel Cutting
- Plasma Cutting
- Power Tools
- Punching and Other Holemaking
- Roll Forming
- Safety
- Sawing
- Shearing
- Shop Management
- Testing and Measuring
- Tube and Pipe Fabrication
- Tube and Pipe Production
- Waterjet Cutting
Industry Directory
Webcasts
Podcasts
FAB 40
Advertise
Subscribe
Account Login
Search
Trends in hydraulic tube production during times of shortages, Part I
Pandemic-related supply chain problems opened the door to reshoring hydraulic pressure line tubing
- By Wynn H. Kearns
- February 22, 2022
- Article
- Tube and Pipe Production
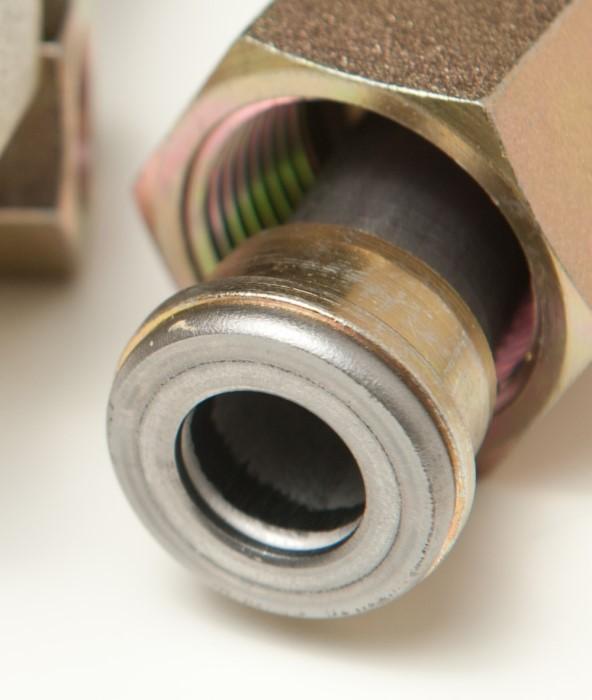
Conventional hydraulic pressure lines use a single-flare end and usually are made to SAE-J525 or ASTM-A513-T5, materials that are difficult to procure from domestic sources. OEMs seeking domestic suppliers could substitute tubing made to specification SAE-J356A and sealed with an O-ring face seal, shown here. Tru-Line Manufacturing.
Editor’s note: This article is the first in a two-part series about the market for and production of fluid-carrying lines for high-pressure applications. Part I discusses the state of the domestic and foreign supply bases of conventional products. Part II discusses the details of a less conventional product for this market.
The COVID-19 pandemic has caused an unexpected shift in many industries, including the steel tubing supply chain and the processes for making tube. From late 2019 until present, the tube market has experienced changes that have been extremely disruptive to both factory and logistical operations. And one long-simmering problem has been thrust into the limelight.
Labor is much more important now than ever before. The pandemic is a human crisis, and the importance of health has changed the work-life-play balance for most, if not all. The population of skilled workers has been reduced by retirements, the inability for some workers to resume old jobs or find new ones in the same industry, and many other factors. Early in the pandemic, the worker shortage was mainly in health care, retail, and other industries that relied on frontline jobs, while manufacturing personnel were on furlough or with employment hours drastically reduced. Now manufacturers are having trouble recruiting and retaining employees, and this includes experienced tube and pipe mill operators. Tube-making is largely a hands-on, blue-collar job requiring strenuous effort in nonclimate-controlled environments. Wearing additional personal protective equipment (that is to say, a mask) to mitigate infection and adherence to additional rules, such as maintaining a 6-ft. linear distance from others, increases the stress in a job that already has many stress risers.
Steel availability and raw steel cost also have changed during the pandemic period. Steel is the largest component cost for most tubes. As a rule of thumb, steel accounts for 50% of the cost per linear foot of tubing. The price of U.S. domestic cold-rolled steel until Q4 2020 was at a three-year average of about $800/ ton. By late 2021 the prices were off the charts at $2,200 per ton.
Given just these two factors that have changed during the pandemic period, how can companies in the tube market react in response? What effect do these changes have on the tubing supply chain, and what useful guidance is available to get the industry out of this crisis?
Get Back to Basics
Many years ago, a veteran tube mill superintendent summarized his company’s role in the industry: “We do only two things here—we make tubing, and we sell it.” This perspective is valuable for any tube-making executive overloaded by too many meetings, too many distractions, too many factors that dilute a company’s core values, or the crisis of the hour (or all of them at once, which is often the case).
It’s important to attain and maintain control by focusing on what is important: the factors that affect making and selling quality tube. If a company’s efforts aren’t focused on these two activities, it’s time to get back to basics.
As the pandemic unfolded, tube demand fell to almost zero in some sectors. Automotive factories and companies in other sectors deemed nonessential were idled. For a period, many in this industry were neither making tubing nor selling it. The tube market continued only for a few essential businesses.
Fortunately, people were going about their business. Some people bought additional freezers to stock up on food items. A bit later the housing market took off, and when people buy a house, they often buy some or many new appliances, so both trends supported demand for small-diameter tubing. The agricultural equipment sector started coming back, with more property owners wanting small tractors or zero-turn mowers. Then automotive markets restarted, although at a slower pace due to the chip shortage and other factors.

Figure 1. SAE-J525 and ASTM-A519 are established, conventional substitutes for SAE-J524 and ASTM-A513T5. The key difference is that SAE-J525 and ASTM-A513T5 are welded rather than seamless. Procurement difficulties such as six-month lead times have created an opportunity for two more tubular products, SAE-J356 (delivered in straight lengths) and SAE-J356A (delivered in coil form), which fulfill many of the same requirements as the other products.
The market has changed, but the guidance is the same. Nothing trumps the focus on making tubing and selling it according to the demands of the market.
Outsourcing
When a manufacturing operation faces higher labor costs and fixed or declining internal resources, the “make it or buy it” question emerges.
Making an as-welded tubing product needs prodigious resources. Slitting wide-band steel in-house is an economic advantage at times, based on the volume and production profiles of the mills. However, in-house slitting can be a liability when considering the labor requirement, capital requirement for tooling, and the cost of wide-band inventory.
One on hand, slitting 2,000 tons a month can lead to holding 5,000 tons of steel raw material in inventory, which ties up a lot of cash. On the other hand, purchasing slit-to-width steel in a just-in-time arrangement uses very little cash. In fact, it actually can delay the cash outlay, considering that the tube producer can negotiate credit terms with the slitting house. Every tube mill is unique in this regard, but it’s safe to say that nearly every tube producer has been affected by the COVID-19 pandemic relative to the availability of skilled labor, the cost of steel, and cash flow.
The same can be said for tube production itself, depending on the circumstances. A company that has an extensive value-add chain might elect to get out of the tube-making business. Rather than make the tubing, then bend it, coat it, and make subassemblies and assemblies, it might make sense to purchase the tubing and focus on the other activities.
Many companies that produce hydraulic assemblies, or automotive fluid-carrying bundles, have captive tube mills. Some of these mills are now liabilities rather than assets. Pandemic-era consumers tend to drive less, and vehicle sales forecasts are way off from pre-pandemic levels. The automotive market is associated with negative words like shutdowns, severe declines, and shortages. None portend much positive change in the supply situation in the near future for automotive OEMs and their suppliers. Noteworthy is the growing presence of electric vehicles in this market which have fewer steel tubing powertrain components.
Captive tube mills typically are built from custom designs. This is an advantage in their intended purpose—making tubing for a specific application—but a disadvantage in economies of scale. As an example, consider a tube mill designed to make a 10-mm-OD product for a known automotive program. That program warrants the setup based on volume. Later, a much smaller program is added for another tube that has the same OD. Time passes, the initial program expires, and the company doesn’t have enough volume to justify the second program. The setup and other costs are simply too high to justify it. In this case, the company should attempt to outsource this item if it can find a capable vendor.
Of course, the calculations don’t stop at the cutoff. Finishing steps such as coating, cutting to length, and packaging add quite a bit of cost. It is often said that the largest hidden cost in making tube is in the handling. Moving tubing off the mill to storage, then retrieving it from storage and loading it onto a table for finish-length cutting, then arranging the tubing into layers to ensure the tubes feed one by one into the cutting machine—all of these steps require labor. This labor cost may escape the attention of the accountants, but it’s right there in the form of an extra forklift operator or additional person in the shipping department.
Focus on Fluid Power Applications
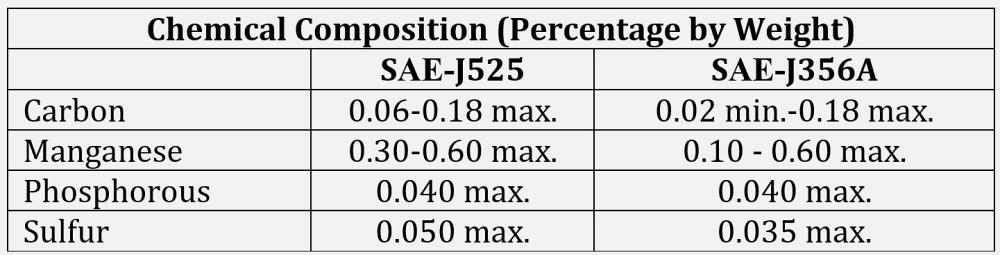
Figure 2. The chemistries for SAE-J525 and SAE-J356A are nearly identical, contributing to the latter’s ability to substitute for the former.
Hydraulic tubing has been around for millennia. Egyptians hammered out copper lines more than 4,000 years ago. Bamboo lines were used in China during the time of the Xia dynasty, approximately 2000 B.C. Later Roman plumbing systems were built from lead conduit tubing, a byproduct of the silver smelting process.
Seamless. Modern seamless steel tube debuted in North America in 1890. The raw material for that process, from 1890 until today, is a solid round billet. Innovation in continuous casting in the 1950s resulted in seamless tubing being converted from ingots to the low-cost steel raw material of the day, the as-cast billet. Hydraulic tubing was then, and is now, made by cold drawing the seamless hollow produced by this process. It is classified by the Society of Automotive Engineers as SAE-J524 and by the American Society for Testing and Materials as ASTM-A519 in the North American market.
Producing seamless hydraulic tubing tends to be a very labor-intensive process, especially for small diameters. It takes a lot of energy and requires a large amount of space.
Welded. In the 1970s the market shifted. After nearly 100 years of dominating the steel tubing market, seamless slipped. It was knocked off its perch by welded tubing, which was found to be suitable for many mechanical applications in the construction and automotive markets. It even claimed some territory on formerly sacred ground, the domain of oil and gas tubing.
Two innovations contributed to this change in the market. One involved continuous slab casting that enabled steel mills to produce high-quality flat strip in high volumes efficiently. The other made high-frequency electric resistance welding a viable process for the tube and pipe industry. The result was a new product: as-welded tubing that performed as well as seamless available at a lower cost than comparable seamless products. Such tube is still made today and classified as SAE-J525 or ASTM-A513-T5 in the North American market. Because the tube is drawn and annealed, it’s a resource-intensive product. These processes aren’t as labor- and capital-intensive as seamless processes, but the costs associated with them are still substantial.
From the 1990s era until the present time, much of the hydraulic line tubing consumed by the domestic market, whether seamless and drawn (SAE-J524) or welded and drawn (SAE-J525), was imported. This was likely a result of a big differential in the cost of labor and steel raw material between the U.S. and exporting countries. These products were available from domestic producers during the last 30 to 40 years, but they were never able to establish themselves as dominant players in this market. The favorable cost of imported products was too high a hurdle to overcome.
Current Market. Over the years, the consumption of the seamless, drawn, and annealed product, J524, withered. It’s still available, and it has a place in the hydraulic line market, but if the welded, drawn, and annealed product, J525, is readily available, OEMs often choose J525.
The pandemic struck and the market shifted yet again. The supply of labor, steel, and logistics throughout the world fell about as quickly as the aforementioned demand for automobiles. So, too, did the supply of imported J525 hydraulic tubing. In light of these events, the domestic market seems to be primed for another market shift. Is it ready for another product, one that is less labor-intensive than welded, drawn, and annealed tubing? One exists, although it’s not commonly used. It’s SAE-J356A, and it meets the requirements of many hydraulic applications (see Figure 1).
Comparison of SAE-J525 and SAE-J356A Welded Tubing
The specifications published by SAE tend to be short and simple in that each defines only one process for making tube. The drawback is that J525 and J356A have considerable overlap in sizes, mechanical properties, and other information, so the specifications tend to sow seeds of confusion. Furthermore, J356A, a coiled product used for small-diameter hydraulic lines, is a variant of J356, a straight-length product primarily for making large-diameter hydraulic line tubes.
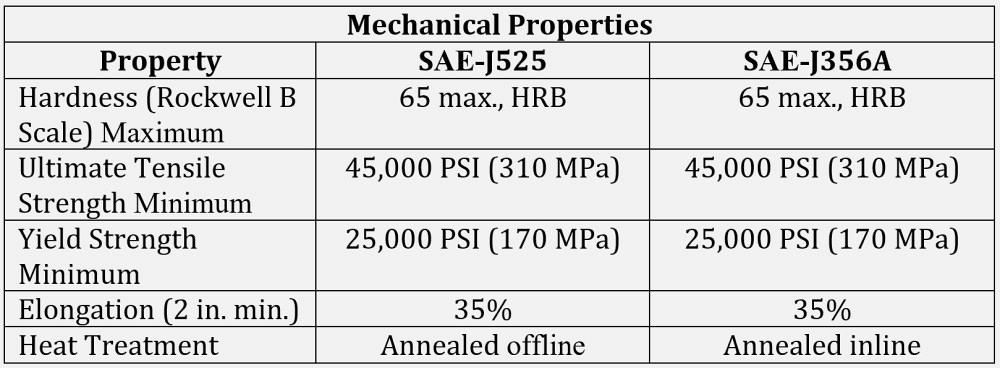
Figure 3. Although welded and cold-drawn tubing is considered by many to be superior to welded and cold-sized tubing, the mechanical properties of the two tubing products are comparable. Note: The imperial values in PSI are soft conversions from the specifications, which are metric values in MPa.
Some engineers regard J525 as superior in high-pressure hydraulic applications, such as those used in heavy equipment. J356A is less well known, but it is also a high-pressure fluid-carrying specification. At times the end forming requirement is the difference: J525 has no ID weld bead and J356A is flash-controlled and has a minor ID weld bead.
The raw materials have similar characteristics (see Figure 2). The very minor differences in the chemical composition relate to the mechanical properties required. To achieve certain mechanical properties, such as the failure strength when stretched, or ultimate tensile strength (UTS), the steel chemistry or the heat treatment is restricted to produce a certain result.
The tubing types have a common similar set of mechanical property parameters, making them interchangeable for many applications (see Figure 3). In other words, if one isn’t available, it’s likely that the other can fulfill the requirement. Nobody needs to reinvent the wheel; the industry already has a robust, balanced set of wheels at its disposal.
About the Author
Wynn H. Kearns
2100 Lexington Road
Evansville, IN 47720
812-424-9028
About the Publication
Related Companies
subscribe now
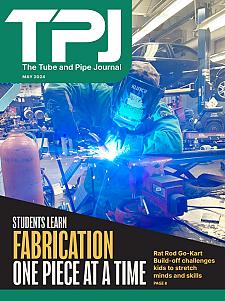
The Tube and Pipe Journal became the first magazine dedicated to serving the metal tube and pipe industry in 1990. Today, it remains the only North American publication devoted to this industry, and it has become the most trusted source of information for tube and pipe professionals.
start your free subscription- Stay connected from anywhere
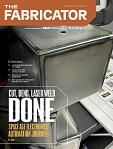
Easily access valuable industry resources now with full access to the digital edition of The Fabricator.
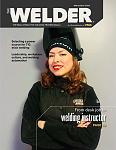
Easily access valuable industry resources now with full access to the digital edition of The Welder.
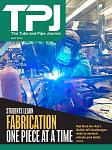
Easily access valuable industry resources now with full access to the digital edition of The Tube and Pipe Journal.
- Podcasting
- Podcast:
- The Fabricator Podcast
- Published:
- 04/16/2024
- Running Time:
- 63:29
In this episode of The Fabricator Podcast, Caleb Chamberlain, co-founder and CEO of OSH Cut, discusses his company’s...
- Trending Articles
Zekelman Industries to invest $120 million in Arkansas expansion
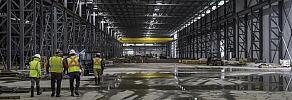
3D laser tube cutting system available in 3, 4, or 5 kW
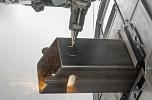
Corrosion-inhibiting coating can be peeled off after use
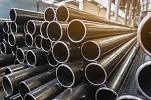
Brushless copper tubing cutter adjusts to ODs up to 2-1/8 in.
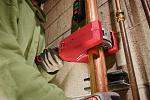
HGG Profiling Equipment names area sales manager
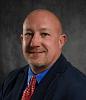
- Industry Events
16th Annual Safety Conference
- April 30 - May 1, 2024
- Elgin,
Pipe and Tube Conference
- May 21 - 22, 2024
- Omaha, NE
World-Class Roll Forming Workshop
- June 5 - 6, 2024
- Louisville, KY
Advanced Laser Application Workshop
- June 25 - 27, 2024
- Novi, MI