- FMA
- The Fabricator
- FABTECH
- Canadian Metalworking
Categories
- Additive Manufacturing
- Aluminum Welding
- Arc Welding
- Assembly and Joining
- Automation and Robotics
- Bending and Forming
- Consumables
- Cutting and Weld Prep
- Electric Vehicles
- En Español
- Finishing
- Hydroforming
- Laser Cutting
- Laser Welding
- Machining
- Manufacturing Software
- Materials Handling
- Metals/Materials
- Oxyfuel Cutting
- Plasma Cutting
- Power Tools
- Punching and Other Holemaking
- Roll Forming
- Safety
- Sawing
- Shearing
- Shop Management
- Testing and Measuring
- Tube and Pipe Fabrication
- Tube and Pipe Production
- Waterjet Cutting
Industry Directory
Webcasts
Podcasts
FAB 40
Advertise
Subscribe
Account Login
Search
Workplace hazards never take a vacation – neither should a shop’s safety program
- By Eric Lundin
- July 15, 2021
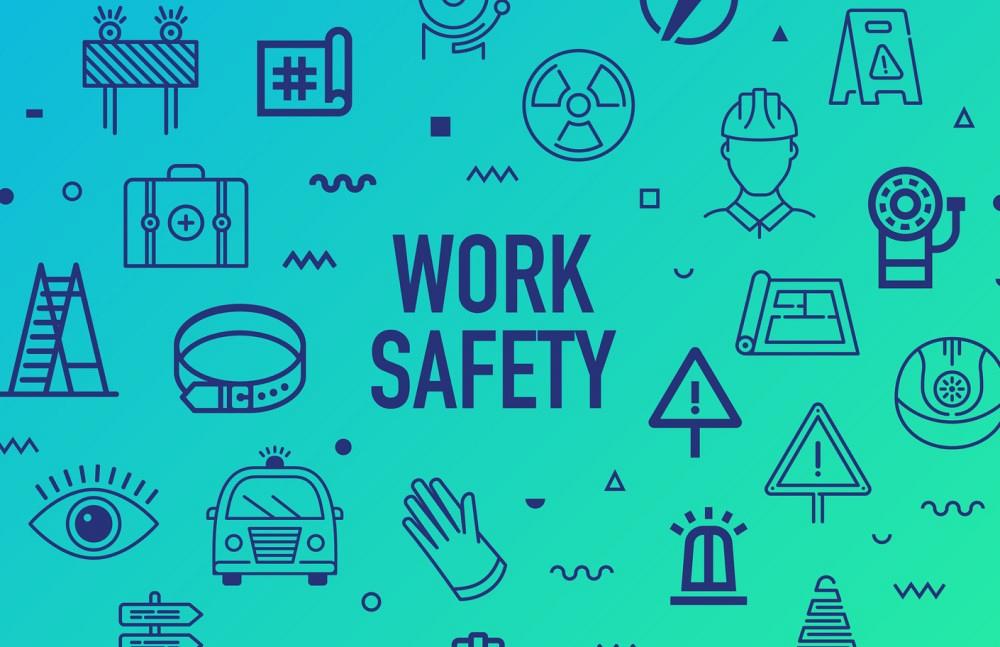
Regardless of the stage of production, any manufacturer that has been ramping up might be relying on workers who had been furloughed, workers new to manufacturing, and temporary help more than usual as industry recovers from the pandemic. This is probably a good time to shake things up in regard to safety briefings. Getty Images
We’re almost a year and a half into the pandemic, and the spread of COVID-19 has changed nearly everything in our lives. Some of the changes have been superficial, like not seeing a movie in a theater in more than a year. Some have been downright tumultuous, like having children attend classes while staying at home. Early on, a few shortages developed. Many stores put a cap on toilet paper purchases, and the shortage of bicycles and adoptable pets threw a few of us for a loop. These were worse than inconveniences, but not nearly as bad as the shortages these days. Right now it seems that every industrial commodity is in short supply, leading to late deliveries and climbing prices.
Business is recovering, and it couldn’t be more clear that the fears of a long, slow recovery were unfounded. No matter how it’s sliced—by nation, region, or industrial sector—recoveries are fast and synchronized. The steep slowdown during the early and middle portion of 2020 was followed by a nearly simultaneous rebound. A combination of factors, such as equipment taken offline and workers furloughed, left supply chains vulnerable—and now they can’t keep up with demand.
Manufacturers have been dealing with a shortage of available skilled workers for decades, which means that many have been in a continuous state of training new workers for decades. The training covers many topics, of course, not the least critical of which is workplace safety. If your business was ran lukewarm last summer and fall and has been heating up through winter and spring, you might be dealing with the same problem as we cruise into summer.
Summer always tends to be problematic in regard to workplace safety. Whether it’s the distraction of nicer weather, anticipating more recreation on the weekends, daydreaming about an upcoming vacation, getting back into the grind after returning from vacation, the presence of temporary workers filling in, or some combination of all of these, workplace statistics bear this out. To quote an abstract on a report about this topic: “More injuries occur during the summer months than at other times of the year.” For more information, see “The Seasonal Timing of Work‐Related Injuries” by Brooks Pierce.
So this year, if you are relying on workers who have been off for a while, or recruiting even more workers than usual who are new to manufacturing, and relying more on temporary help, this is probably a good time to put a little extra focus on workplace safety.
You’ve probably already done a lot to mitigate or even eliminate workplace hazards, and you might already have a top-notch safety program. Even if you don’t see room for improvement, maybe consider shaking it up a bit: Change the format of your safety briefings, increase the frequency (or change the time of day), throw in a new topic or two—do anything to change it to call more attention to it. And while workplace safety is no laughing matter, maybe even use some humor. Enter “safety fail” into your browser and you’ll see no end to images you can use to spice up your next safety briefing.
subscribe now
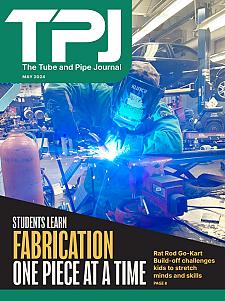
The Tube and Pipe Journal became the first magazine dedicated to serving the metal tube and pipe industry in 1990. Today, it remains the only North American publication devoted to this industry, and it has become the most trusted source of information for tube and pipe professionals.
start your free subscriptionAbout the Author
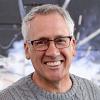
Eric Lundin
2135 Point Blvd
Elgin, IL 60123
815-227-8262
Eric Lundin worked on The Tube & Pipe Journal from 2000 to 2022.
About the Publication
- Stay connected from anywhere
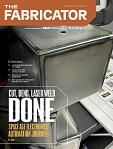
Easily access valuable industry resources now with full access to the digital edition of The Fabricator.
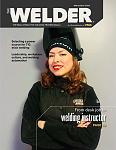
Easily access valuable industry resources now with full access to the digital edition of The Welder.
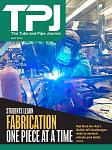
Easily access valuable industry resources now with full access to the digital edition of The Tube and Pipe Journal.
- Podcasting
- Podcast:
- The Fabricator Podcast
- Published:
- 04/16/2024
- Running Time:
- 63:29
In this episode of The Fabricator Podcast, Caleb Chamberlain, co-founder and CEO of OSH Cut, discusses his company’s...
- Trending Articles
Zekelman Industries to invest $120 million in Arkansas expansion
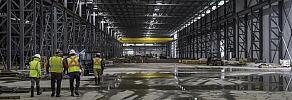
3D laser tube cutting system available in 3, 4, or 5 kW
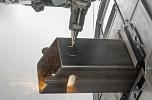
Corrosion-inhibiting coating can be peeled off after use
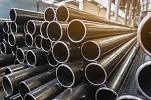
Brushless copper tubing cutter adjusts to ODs up to 2-1/8 in.
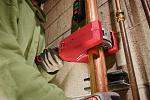
HGG Profiling Equipment names area sales manager
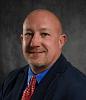
- Industry Events
16th Annual Safety Conference
- April 30 - May 1, 2024
- Elgin,
Pipe and Tube Conference
- May 21 - 22, 2024
- Omaha, NE
World-Class Roll Forming Workshop
- June 5 - 6, 2024
- Louisville, KY
Advanced Laser Application Workshop
- June 25 - 27, 2024
- Novi, MI