Editor
- FMA
- The Fabricator
- FABTECH
- Canadian Metalworking
Categories
- Additive Manufacturing
- Aluminum Welding
- Arc Welding
- Assembly and Joining
- Automation and Robotics
- Bending and Forming
- Consumables
- Cutting and Weld Prep
- Electric Vehicles
- En Español
- Finishing
- Hydroforming
- Laser Cutting
- Laser Welding
- Machining
- Manufacturing Software
- Materials Handling
- Metals/Materials
- Oxyfuel Cutting
- Plasma Cutting
- Power Tools
- Punching and Other Holemaking
- Roll Forming
- Safety
- Sawing
- Shearing
- Shop Management
- Testing and Measuring
- Tube and Pipe Fabrication
- Tube and Pipe Production
- Waterjet Cutting
Industry Directory
Webcasts
Podcasts
FAB 40
Advertise
Subscribe
Account Login
Search
New generation requires new ways of doing business
- By Lincoln Brunner
- November 11, 2023
As the machinery of their industry hummed nearby, a small group of tube and pipe business leaders agreed: To survive, the U.S. tube and pipe industry must drastically change how it attracts and develops its people.
How to do that remains a matter of serious debate for serious reasons, not least of which is the deficit of general tube mill knowledge among incoming workers observed by several members of a Tube and Pipe Association Advisory Board roundtable that TPJ convened at FABTECH 2023 in Chicago.
In fact, what Nuts, Bolts and Thingamajigs, the foundation of Fabricators and Manufacturers Association, is doing for welding education among young people may be just the ticket for the tube and pipe manufacturing sector, according to Phil Meinczinger, chairman of the TPA Advisory Board and business development manager at Magnetic Analysis Corp.
“Most of the people we see, the young ones, have no idea what a tube mill is,” Meinczinger said. “We need to expose them, even from the high school level. We need to [say] to them, ‘You know that tube you’re welding? Where did it come from?’ You know, plant some seeds to get them to think about this.”
Rick Olson, president/COO of Roll Machining Technologies & Solutions, agreed and added that he sees such a lack of general mechanical aptitude among potential hires that if he interviews someone who likes to work on cars, he’s likely to hire that person on the spot.
“Even when you find somebody that may be interested in a tube mill, that problem-solving from a mechanical standpoint—the ability to look at [something] and go, ‘OK, I don’t know how that works, but this went to here, this went to here, so this is kind of how it had to work’—that to me is nonexistent in this day and age,” Olson said. “And it’s a hard thing to teach overnight. So, the ramp up is much longer now.”
Switching the Approach
That on-ramp to the tube and pipe knowledge highway indeed is longer for many Gen Z employees, so the industry might as well get used to it and change with the times, according to consultant and fabrication business owner Lisa Wertzbaugher.
“I think the key is to meet them where they’re at,” said Wertzbaugher, a columnist for this magazine and owner of Wertzbaugher Consulting. “Everything comes to them now. That’s how the world works. We had to go out and find our way—[now] everything comes in.
“We have to understand where they’re strong and see how that offsets where we might have some inefficiencies. But ultimately, having a longer training period is cheaper than turnover. So, I think that is who they are, and we have to adapt more than expect them to.”
Chris Smith, global manager of advanced engineering for Cooper Standard, noted that even though certain new norms like marketing through social media may not resonate with people like him, realities like turnover are forcing him to rethink things.
“That’s what we talked about—since COVID hit, turnover’s killing everyone,” Smith said. “How do we retain people? And if it’s changing work hours or getting them involved with things they enjoy—even though in my mind, maybe Instagram isn’t putting more dollars into the bottom line—maybe it is, because it keeps people there and it gets your name out.”
Olson said adjusting to the general mindset of workers now as opposed to, say, 10 years ago is a regular exercise for him.
“I’ve had to change the way I think about how I manage the new workforce,” Olson said. “In the old days, the more hours you could give them, the more work, the happier they were. I found 10 years ago, I had to make people take time off. Now, I almost have to be OK with the three days a week a guy comes in because that’s all he wants. Normally you would [say], ‘No way.’ But now you have to accept that.
“I find myself constantly having to tell myself that I have to change the way I think—as Lisa said, to bring ourselves to them versus trying to mold them into what we were used to.”
Pat Brunken, vice president tube mills at Addison Machine Engineering, said that the industry indeed does need to strive for better education but encouraged his colleagues to use young workers’ penchant for looking at their phones as a tip to some needed changes.
“We have to be more adept to … get the equipment to that point where the controls are always computer-based—and it’s hard to replace machinery with that,” Brunken said. “The Army and the Air Force [are] starting to make controls like an XBox or a PlayStation. Why aren’t we there now? That attracts smart minds.”
Alex Brueggmann, tooling and innovation manufacturing engineering manager at Atkore Intl., noted that his company and many others rely heavily on OEMs to provide those kinds of innovations.
“One thing we need to do from the producer side is push back on the OEMs [and say], ‘This is an issue, so we need to team up with you,’” Brueggmann said. “What type of automation are you going to provide to us in the future? How are we going to solve this issue, whether it be packaging machines or visual systems to help with setups, whatever it may be?”
Leaning on New Expertise
And as technology continues to advance, it’s up to business owners to recognize that even if younger employees require longer learning curves, those same employees often are the ones with the better technology skills, according to Wertzbaugher.
“You know, the training period may be longer, and it may take longer for them to learn a certain skill set because we have to move them around,” Wertzbaugher said. “They can’t do the same thing day in, day out. But there’s a lot of advantages, as well. We implemented a new clocking system that was app-based—our younger employees took the lead on all of that.”
Meinczinger recognizes that younger employees want and resonate with technology and welcomes the idea of moving his company that direction.
“Some of the new automation we’re working on—I think that’s where we can attract the young people,” Meinczinger said. “They’re not interested in pushing buttons. They want to work with robotics. They want automation. They want to do something very highly skilled and technical. I think that’s where our company is going. We’re doing a lot more robotic stuff to try to attract the younger talent.”
Reasons for Optimism
Despite the ongoing challenges of finding, keeping, and training that talent, overall tube and pipe business is looking up and should continue to do so, roundtable members said.
“I’m optimistic,” Wertzbaugher said, “just by the sheer amount of work that’s out there. We’ve quoted four times our annual revenue since March. This is a very powerful time for manufacturing domestically right now. I think we are having a moment. We are critical; we are important to the U.S. economy. There’s a major focus with OEMs and our end customers wanting to have suppliers close to them. I think we have an advantage and an opportunity now that has not happened in a very long time.”
Brueggmann couldn’t help but agree.
“As far as optimism on the tube and pipe producers side, we are just busy,” Brueggmann said. “All the producers I talk to, that’s our optimism. That’s a good problem to have—trying to find people, trying to find equipment, trying to automate. So, it’s a good time. We see that going for a while, as far as I’m concerned.”
subscribe now
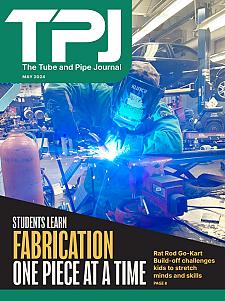
The Tube and Pipe Journal became the first magazine dedicated to serving the metal tube and pipe industry in 1990. Today, it remains the only North American publication devoted to this industry, and it has become the most trusted source of information for tube and pipe professionals.
start your free subscriptionAbout the Author
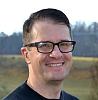
Lincoln Brunner
2135 Point Blvd.
Elgin, IL 60123
(815)-227-8243
Lincoln Brunner is editor of The Tube & Pipe Journal. This is his second stint at TPJ, where he served as an editor for two years before helping launch thefabricator.com as FMA's first web content manager. After that very rewarding experience, he worked for 17 years as an international journalist and communications director in the nonprofit sector. He is a published author and has written extensively about all facets of the metal fabrication industry.
About the Publication
- Stay connected from anywhere
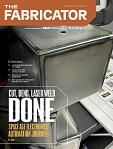
Easily access valuable industry resources now with full access to the digital edition of The Fabricator.
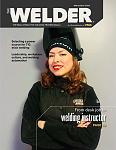
Easily access valuable industry resources now with full access to the digital edition of The Welder.
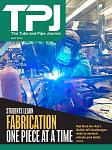
Easily access valuable industry resources now with full access to the digital edition of The Tube and Pipe Journal.
- Podcasting
- Podcast:
- The Fabricator Podcast
- Published:
- 04/16/2024
- Running Time:
- 63:29
In this episode of The Fabricator Podcast, Caleb Chamberlain, co-founder and CEO of OSH Cut, discusses his company’s...
- Trending Articles
Zekelman Industries to invest $120 million in Arkansas expansion
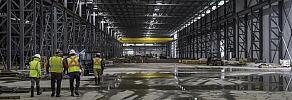
3D laser tube cutting system available in 3, 4, or 5 kW
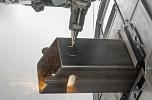
Corrosion-inhibiting coating can be peeled off after use
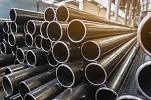
Brushless copper tubing cutter adjusts to ODs up to 2-1/8 in.
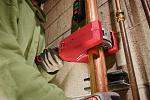
HGG Profiling Equipment names area sales manager
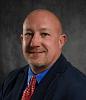
- Industry Events
16th Annual Safety Conference
- April 30 - May 1, 2024
- Elgin,
Pipe and Tube Conference
- May 21 - 22, 2024
- Omaha, NE
World-Class Roll Forming Workshop
- June 5 - 6, 2024
- Louisville, KY
Advanced Laser Application Workshop
- June 25 - 27, 2024
- Novi, MI