- FMA
- The Fabricator
- FABTECH
- Canadian Metalworking
Categories
- Additive Manufacturing
- Aluminum Welding
- Arc Welding
- Assembly and Joining
- Automation and Robotics
- Bending and Forming
- Consumables
- Cutting and Weld Prep
- Electric Vehicles
- En Español
- Finishing
- Hydroforming
- Laser Cutting
- Laser Welding
- Machining
- Manufacturing Software
- Materials Handling
- Metals/Materials
- Oxyfuel Cutting
- Plasma Cutting
- Power Tools
- Punching and Other Holemaking
- Roll Forming
- Safety
- Sawing
- Shearing
- Shop Management
- Testing and Measuring
- Tube and Pipe Fabrication
- Tube and Pipe Production
- Waterjet Cutting
Industry Directory
Webcasts
Podcasts
FAB 40
Advertise
Subscribe
Account Login
Search
Dialing in the heat on tube, pipe mills
Webinar provides guidance so tube, pipe producers can maximize weld quality, minimize scrap
- By Eric Lundin
- March 30, 2021
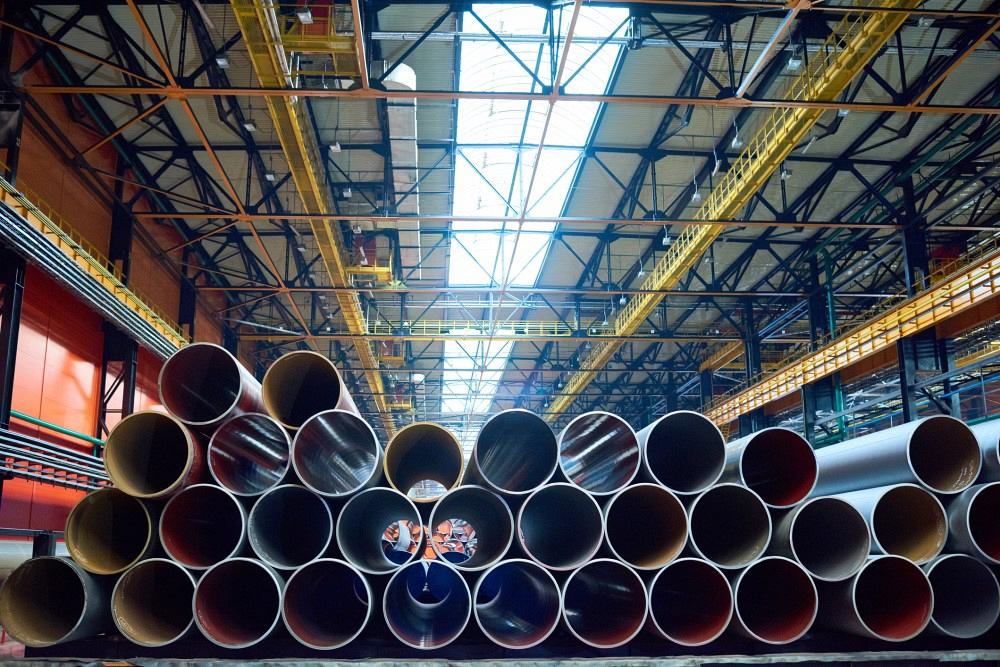
Every tube or pipe application has one thing in common: the need for good, reliable, durable welds. The main process? It’s high-frequency electric resistance welding (HF-ERW). A webinar from Thermaool Corp. covers just that. Getty Images
ASTM-this, SAE-that, API-something else … the number of manufacturing standards that tube and pipe producers must keep up with these days is daunting, and the list keeps growing. Meanwhile, customers keep finding new ways, or at least more creative ways, to abuse the products tube and pipe producers make.
Nobody wants to make yesterday’s products tomorrow, so whether customers are making a structural component for an airplane or a pickup truck or drilling an oil well in some remote location, they need products that are better than ever before. Whether they need more strength from thinner-wall tube, or they’re subjecting pipe to ever-greater pressures, or using pipe products in more corrosive environments, they need tube and pipe products that perform. Structural components have to be stronger and lighter in weight than the materials used in past years, especially in applications that need more fuel efficiency. All of the easy-to-find oil is gone, and with each passing day, drillers are going deeper and getting further from sweet crude and extracting oil from sour deposits, drilling in ever-deeper waters, and so on, so the need for corrosion resistance is as critical as it ever was. For tube and pipe producers, challenges abound.
Every tube or pipe application has one thing in common: the need for good, reliable, durable welds. The main process? It’s high-frequency electric resistance welding (HF-ERW), which has been the mainstay welding process for tube and pipe production for many decades. Its ability to heat steel from room temperature to red-hot almost instantly is the key to running a mill fast enough to make tubular products efficiently.
ERW relies on a power supply that causes electrical current to flow through an induction coil that surrounds the tube or pipe. The current in the coil induces a current to flow in the tube or pipe product; its resistance to current flow causes heat to build up. Key process variables are welder output power, the output frequency, the raw material (type and condition), and mill setup. These come together to determine the precise heat input as the coil unspools, moves through the mill, and passes through the coil. The customers are demanding, manufacturing standards are stringent, and the pace of technology is relentless. Keeping up is a matter of making robust welds, and the process window for making a successful weld isn’t getting any larger—in fact, it’s shrinking. To learn about the effects of HF-ERW parameters and mill setup, and how to use this information to reduce costly scrap while achieving a better weld, register for “A Path for a Better HF Weld,” a webinar presented by Sasha Tupalo, a materials engineer with Thermatool.
The webinar is scheduled for Wednesday, May 12, 2021 at 11 a.m. ET (10 a.m. CT). Registration is open.
subscribe now
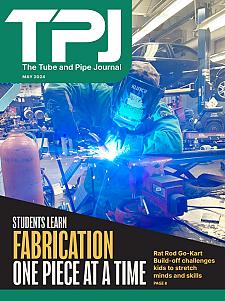
The Tube and Pipe Journal became the first magazine dedicated to serving the metal tube and pipe industry in 1990. Today, it remains the only North American publication devoted to this industry, and it has become the most trusted source of information for tube and pipe professionals.
start your free subscriptionAbout the Author
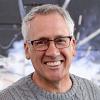
Eric Lundin
2135 Point Blvd
Elgin, IL 60123
815-227-8262
Eric Lundin worked on The Tube & Pipe Journal from 2000 to 2022.
About the Publication
Related Companies
- Stay connected from anywhere
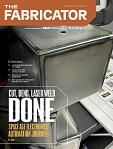
Easily access valuable industry resources now with full access to the digital edition of The Fabricator.
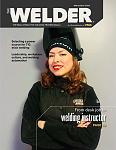
Easily access valuable industry resources now with full access to the digital edition of The Welder.
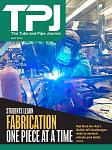
Easily access valuable industry resources now with full access to the digital edition of The Tube and Pipe Journal.
- Podcasting
- Podcast:
- The Fabricator Podcast
- Published:
- 04/16/2024
- Running Time:
- 63:29
In this episode of The Fabricator Podcast, Caleb Chamberlain, co-founder and CEO of OSH Cut, discusses his company’s...
- Trending Articles
Zekelman Industries to invest $120 million in Arkansas expansion
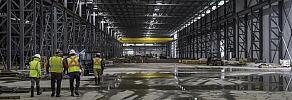
3D laser tube cutting system available in 3, 4, or 5 kW
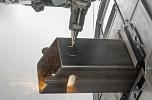
Corrosion-inhibiting coating can be peeled off after use
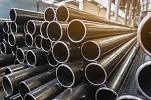
Brushless copper tubing cutter adjusts to ODs up to 2-1/8 in.
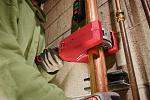
HGG Profiling Equipment names area sales manager
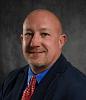
- Industry Events
16th Annual Safety Conference
- April 30 - May 1, 2024
- Elgin,
Pipe and Tube Conference
- May 21 - 22, 2024
- Omaha, NE
World-Class Roll Forming Workshop
- June 5 - 6, 2024
- Louisville, KY
Advanced Laser Application Workshop
- June 25 - 27, 2024
- Novi, MI