- FMA
- The Fabricator
- FABTECH
- Canadian Metalworking
Categories
- Additive Manufacturing
- Aluminum Welding
- Arc Welding
- Assembly and Joining
- Automation and Robotics
- Bending and Forming
- Consumables
- Cutting and Weld Prep
- Electric Vehicles
- En Español
- Finishing
- Hydroforming
- Laser Cutting
- Laser Welding
- Machining
- Manufacturing Software
- Materials Handling
- Metals/Materials
- Oxyfuel Cutting
- Plasma Cutting
- Power Tools
- Punching and Other Holemaking
- Roll Forming
- Safety
- Sawing
- Shearing
- Shop Management
- Testing and Measuring
- Tube and Pipe Fabrication
- Tube and Pipe Production
- Waterjet Cutting
Industry Directory
Webcasts
Podcasts
FAB 40
Advertise
Subscribe
Account Login
Search
Combilift celebrates 20 years, opens new facility, introduces three new models
- May 2, 2018
- News Release
- Materials Handling
“We have employed an additional 230 people since we announced our plans for this factory in 2015, and the combination of this state-of-the-art production plant and the growing skilled workforce will allow us to double production within the next five years,” said Managing Director Martin McVicar.
The company doesn’t focus solely on designing and manufacturing material handling equipment. It sees its role as something more comprehensive.
“The three keys are customer safety, storage capability, and efficiency,” said Anthony Rooney, sales director for the U.S., U.K., and Ireland. By spending 7 percent of revenue on research and development, the company doesn’t merely maintain its expertise, but expands it from year to year.
One example concerning safety is a tilt table the company uses to test the stability of actual loads. Another is an optional overload warning device, Combi Safe-lift, that it plans to incorporate as a standard feature on its counterbalanced lift trucks in the future. Whether the load is too heavy, off-center, or too high, the system can detect the problem. Providing more than detection and warning, the system is sophisticated enough to provide three status levels, displayed for the operator as green, yellow, and red corresponding to normal, warning, and shutdown.
“A strain gauge on the mast tells when the mast is overloaded to prevent the truck from tipping over,” Rooney said.
Introduced on April 30, the company’s high-capacity powered pallet truck, COMBi-HC-PPT, illustrated another one of its safety innovations. The machine is similar to a traditional walk-behind fork truck. As the name implies, the operator walks behind the truck, using the tiller at the rear for steering. Anyone who has ever worked an entry-level job in a warehouse or similar industrial environment knows that large, heavy loads can be problematic. When moving forward, it’s difficult to see the route, so the operator often needs a spotter, and sometimes two; when moving backward, the operator can get caught between the truck and something stationary, like a column or a wall, which is hazardous at best. Combilift’s patented adjustable tiller, available on all four of its walk-behind models, differentiates these models from conventional walk-behind machines.
The tiller can swing 90 degrees to the left or right so that the operator isn’t in line with the load. This allows him to view the truck’s path from one side, acting as both operator and spotter. The unit is equipped with a front-facing camera and a camera display on the tiller, providing the operator a wide-angle front view, which eliminates the need for the second spotter. A bigger advantage is in safety; when the tiller is 90 degrees from the usual position, the operator cannot get between the load and anything stationary, eliminating the crushing hazard.
Another product introduced at the open house that reflects the focus of Combilift’s products—designs that support optimized storage capacity—is a new style of order picker. To meet the needs of warehouses that maximize storage space by using high bays and narrow aisles, the Combi OP is equipped with a platform that can extend to 232 inches high, yet it’s relatively narrow at 56.5 in. wide and has a turning radius that is 60 percent of the vehicle’s length.
The platform measures nearly 35.5 in. wide by 125.5 in. long, allowing the operator to pick long items, and it has a carrying capacity of 1,100 pounds. Guide rollers prevent contact with the storage racks.
Anyone interested in taking the hassle out of loading truckloads of product might be interested in another item launched at the open house: the company’s slip-sheet loader, which eliminates the need to move products into the truck one pallet-load at a time.The unit comprises a conveyor table that has width and length that correspond to those of the truck’s bed. A sheet of steel, a slip sheet, sits on top the conveyor. After building up a truckload of material on the slip sheet—loading material from the left or right side—and securing it, the operator extends the table, feeding the load into the truck. The operator then closes the gate and retracts the slip sheet; the gate blocks the load, keeping it in the truck, while the sheet slips out from underneath it.
While the company’s stated goal, doubling production over the next five years, sounds ambitious, it’s not unreasonable to think Combilift can achieve it. From its beginnings in producing lift trucks, the firm branched out to develop its line of pallet jacks a few years ago and introduced a large vehicle, the Straddle Carrier, that can load or unload a 40-ft. shipping container or similar load—timber, line pipe, or construction products, for example—from a semi trailer in minutes. A related product is its mobile gantry, a crane on wheels. It handles thousands of pounds and is useful by itself for heavy loads like steel coil, or used in tandem for long loads, such as wind turbine blades and aircraft wings.
—Eric Lundin, editor
Related Companies
subscribe now
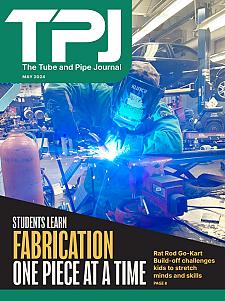
The Tube and Pipe Journal became the first magazine dedicated to serving the metal tube and pipe industry in 1990. Today, it remains the only North American publication devoted to this industry, and it has become the most trusted source of information for tube and pipe professionals.
start your free subscription- Stay connected from anywhere
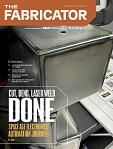
Easily access valuable industry resources now with full access to the digital edition of The Fabricator.
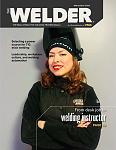
Easily access valuable industry resources now with full access to the digital edition of The Welder.
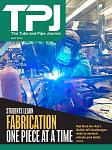
Easily access valuable industry resources now with full access to the digital edition of The Tube and Pipe Journal.
- Podcasting
- Podcast:
- The Fabricator Podcast
- Published:
- 04/16/2024
- Running Time:
- 63:29
In this episode of The Fabricator Podcast, Caleb Chamberlain, co-founder and CEO of OSH Cut, discusses his company’s...
- Trending Articles
Zekelman Industries to invest $120 million in Arkansas expansion
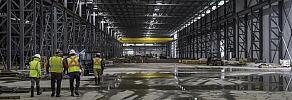
3D laser tube cutting system available in 3, 4, or 5 kW
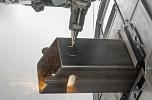
Corrosion-inhibiting coating can be peeled off after use
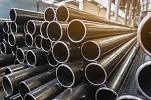
Brushless copper tubing cutter adjusts to ODs up to 2-1/8 in.
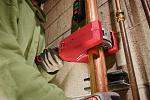
HGG Profiling Equipment names area sales manager
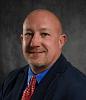
- Industry Events
16th Annual Safety Conference
- April 30 - May 1, 2024
- Elgin,
Pipe and Tube Conference
- May 21 - 22, 2024
- Omaha, NE
World-Class Roll Forming Workshop
- June 5 - 6, 2024
- Louisville, KY
Advanced Laser Application Workshop
- June 25 - 27, 2024
- Novi, MI