- FMA
- The Fabricator
- FABTECH
- Canadian Metalworking
Categories
- Additive Manufacturing
- Aluminum Welding
- Arc Welding
- Assembly and Joining
- Automation and Robotics
- Bending and Forming
- Consumables
- Cutting and Weld Prep
- Electric Vehicles
- En Español
- Finishing
- Hydroforming
- Laser Cutting
- Laser Welding
- Machining
- Manufacturing Software
- Materials Handling
- Metals/Materials
- Oxyfuel Cutting
- Plasma Cutting
- Power Tools
- Punching and Other Holemaking
- Roll Forming
- Safety
- Sawing
- Shearing
- Shop Management
- Testing and Measuring
- Tube and Pipe Fabrication
- Tube and Pipe Production
- Waterjet Cutting
Industry Directory
Webcasts
Podcasts
FAB 40
Advertise
Subscribe
Account Login
Search
Network of robots monitors large pipe structures using acoustic wave sensors
- November 29, 2023
- News Release
- Tube and Pipe Fabrication
An inspection design method by which mobile robots can inspect large pipe structures has been demonstrated with the successful inspection of multiple defects on a 3-m-long steel pipe using guided acoustic wave sensors.
This approach, developed by a University of Bristol team, was used to review defects including circular holes with different sizes, a crack-like defect, and pits through a designed inspection path to achieve 100% detection coverage for a defined reference defect.
In their study published in NDT and E International, “Pipe inspection using guided acoustic wave sensors integrated with mobile robots,” Jie Zhang, Xudong Niu, and team leaders Anthony J. Croxford and Bruce W. Drinkwater explain how they were able to examine large plate-like structures using a network of independent robots, each carrying sensors capable of both sending and receiving guided acoustic waves, working in pulse-echo mode.
This approach minimizes communication between robots, requires no synchronization, and raises the possibility of on-board processing to lower data transfer costs and hence reduce overall inspection expenses. The inspection was divided into a defect detection and a defect localization stage.
“As the cost of mobile robots has reduced over recent years, it is increasingly possible to deploy multiple robots for a large area inspection,” explained Zhang. “We take the existence of small inspection robots as its starting point and explore how they can be used for generic monitoring of a structure. This requires inspection strategies, methodologies, and assessment procedures that can be integrated with the mobile robots for accurate defect detection and localization that is low cost and efficient.”
The method could be used across other materials, pipe geometries, noise levels, and guided wave modes, allowing the full range of sensor performance parameters, defects sizes and types, and operating modalities to be explored.
subscribe now
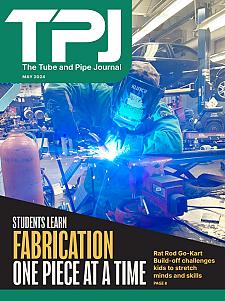
The Tube and Pipe Journal became the first magazine dedicated to serving the metal tube and pipe industry in 1990. Today, it remains the only North American publication devoted to this industry, and it has become the most trusted source of information for tube and pipe professionals.
start your free subscription- Stay connected from anywhere
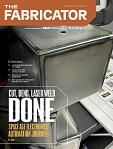
Easily access valuable industry resources now with full access to the digital edition of The Fabricator.
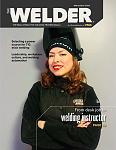
Easily access valuable industry resources now with full access to the digital edition of The Welder.
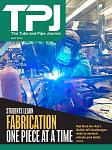
Easily access valuable industry resources now with full access to the digital edition of The Tube and Pipe Journal.
- Podcasting
- Podcast:
- The Fabricator Podcast
- Published:
- 04/16/2024
- Running Time:
- 63:29
In this episode of The Fabricator Podcast, Caleb Chamberlain, co-founder and CEO of OSH Cut, discusses his company’s...
- Trending Articles
Zekelman Industries to invest $120 million in Arkansas expansion
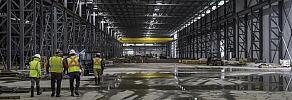
3D laser tube cutting system available in 3, 4, or 5 kW
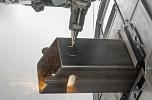
Corrosion-inhibiting coating can be peeled off after use
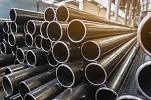
Brushless copper tubing cutter adjusts to ODs up to 2-1/8 in.
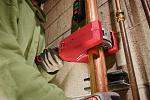
HGG Profiling Equipment names area sales manager
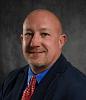
- Industry Events
16th Annual Safety Conference
- April 30 - May 1, 2024
- Elgin,
Pipe and Tube Conference
- May 21 - 22, 2024
- Omaha, NE
World-Class Roll Forming Workshop
- June 5 - 6, 2024
- Louisville, KY
Advanced Laser Application Workshop
- June 25 - 27, 2024
- Novi, MI