- FMA
- The Fabricator
- FABTECH
- Canadian Metalworking
Categories
- Additive Manufacturing
- Aluminum Welding
- Arc Welding
- Assembly and Joining
- Automation and Robotics
- Bending and Forming
- Consumables
- Cutting and Weld Prep
- Electric Vehicles
- En Español
- Finishing
- Hydroforming
- Laser Cutting
- Laser Welding
- Machining
- Manufacturing Software
- Materials Handling
- Metals/Materials
- Oxyfuel Cutting
- Plasma Cutting
- Power Tools
- Punching and Other Holemaking
- Roll Forming
- Safety
- Sawing
- Shearing
- Shop Management
- Testing and Measuring
- Tube and Pipe Fabrication
- Tube and Pipe Production
- Waterjet Cutting
Industry Directory
Webcasts
Podcasts
FAB 40
Advertise
Subscribe
Account Login
Search
AMBA all-in-one machine manufactures complex-shaped tube
- January 31, 2018
- Product Release
- Tube and Pipe Production
Aachener Maschinenbau GmbH (AMBA) offers new all-in-one machines for producing cold-formed tubes. These machines are the first in the world to produce tubes with varying cross sections in just one continuous cycle, the manufacturer says.
According to the company, the first tube manufacturer to use one of these machines has increased the production rate by a factor of 10 while reducing the costs of production. In this application, the machine makes shafts for car seats. Over their length, these shafts feature six sections of three different diameters. The seven-stage cold-forming process, finish rolling, and marking are performed fully automatically by one machine. The tubes leave the machine ready to be installed, requiring no additional machining.
All process steps, from the automatic feeding of the input stock out of a high-capacity storage system to the finished tube ready to be installed, are automated. This reduces the need for human intervention and allows for lower tooling costs and the elimination of metal chip scrap.
The cold-forming process imparts better tensile strength properties to the tube than hot forming, the company says, and the finished tube has a consistent wall thickness over its entire length, even at the transitions between different cross sections.
While the cold-formed tubes produced on the all-in-one machines have thinner walls than hot-formed tubes, they generally have the same mechanical properties. The machines can make tubes with diameters up to nearly 2 in.
subscribe now
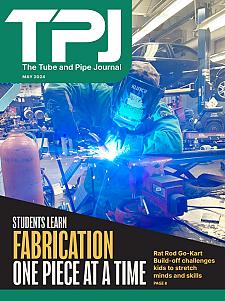
The Tube and Pipe Journal became the first magazine dedicated to serving the metal tube and pipe industry in 1990. Today, it remains the only North American publication devoted to this industry, and it has become the most trusted source of information for tube and pipe professionals.
start your free subscription- Stay connected from anywhere
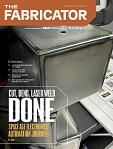
Easily access valuable industry resources now with full access to the digital edition of The Fabricator.
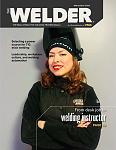
Easily access valuable industry resources now with full access to the digital edition of The Welder.
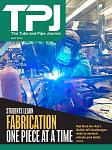
Easily access valuable industry resources now with full access to the digital edition of The Tube and Pipe Journal.
- Podcasting
- Podcast:
- The Fabricator Podcast
- Published:
- 04/16/2024
- Running Time:
- 63:29
In this episode of The Fabricator Podcast, Caleb Chamberlain, co-founder and CEO of OSH Cut, discusses his company’s...
- Trending Articles
Zekelman Industries to invest $120 million in Arkansas expansion
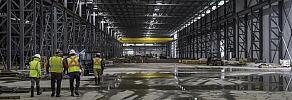
3D laser tube cutting system available in 3, 4, or 5 kW
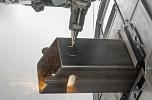
Corrosion-inhibiting coating can be peeled off after use
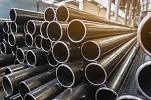
Brushless copper tubing cutter adjusts to ODs up to 2-1/8 in.
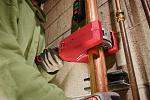
HGG Profiling Equipment names area sales manager
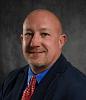
- Industry Events
16th Annual Safety Conference
- April 30 - May 1, 2024
- Elgin,
Pipe and Tube Conference
- May 21 - 22, 2024
- Omaha, NE
World-Class Roll Forming Workshop
- June 5 - 6, 2024
- Louisville, KY
Advanced Laser Application Workshop
- June 25 - 27, 2024
- Novi, MI