Contributing Writer
- FMA
- The Fabricator
- FABTECH
- Canadian Metalworking
Categories
- Additive Manufacturing
- Aluminum Welding
- Arc Welding
- Assembly and Joining
- Automation and Robotics
- Bending and Forming
- Consumables
- Cutting and Weld Prep
- Electric Vehicles
- En Español
- Finishing
- Hydroforming
- Laser Cutting
- Laser Welding
- Machining
- Manufacturing Software
- Materials Handling
- Metals/Materials
- Oxyfuel Cutting
- Plasma Cutting
- Power Tools
- Punching and Other Holemaking
- Roll Forming
- Safety
- Sawing
- Shearing
- Shop Management
- Testing and Measuring
- Tube and Pipe Fabrication
- Tube and Pipe Production
- Waterjet Cutting
Industry Directory
Webcasts
Podcasts
FAB 40
Advertise
Subscribe
Account Login
Search
Starting a portable GTAW business (Part III)
Dos and don'ts
- By Phil Evans
- August 8, 2006
- Article
- Arc Welding
![]() |
Photo by Jason Gies, project engineer, Amer Industrial Technologies, Inc., 302-765-3900, www.amerindustrial.com. |
Editor’s note: This is one installment in a four-part series. Part I discusses equipment selection and skill evaluation. Part II focuses on the potential customer base and the welding repair needs of specific segments. It also offers pricing tips for various jobs. Part III lists dos and don’ts for any business with many tips specifically for welders. Part IV discusses specifics for welding stainless steel and aluminum.
Dos for Business
- If you plan to work for a state department of transportation or other government agency, get job facts and requirements before you quote. Usually a printed job description and requirements are available.
- Treat every customer like he is your only customer. More repeat business will come from his recommendations than any other single source. But use your head; don't let him push you too hard or take advantage of your business or skills.
- Do the job right the first time or not at all. There is no such thing as a rush weld job. Plus, doing a re-repair free means your original charge was cut in half, right?
- Drive within the law. That $150 speeding ticket will take the profit right out of that $200 job.
- If someone asks you to repair a part someone else has failed to repair two or three times before, be cautious. Ask questions: Who did the previous weld repairs? Why did the repair fail? How is the part used or abused? All of those previous welds will have to come out before you do your job. Time is money – establish that understanding right from the start. A quoted $30 job that takes six
hours is only $5 an hour, simple math. Sometimes your gut feeling is very valuable.
- Be cautious about customers who insist they want only a quick, temporary fix and that they'll fix it properly later. In most cases, your fix will be it until it faults the next time. A quick fix could cost you in the long run — can you afford it?
- Don't be afraid to tell a customer No. You know your technical skills better than anyone.
Don'ts for Business
- Don't go to the job site in old, torn, burned clothes. Your first impression does count. Looking dirty and destitute could change the customer's mind before you even open your mouth. Also, don't use profanity or crude, derogatory, disrespectful language. You never know who the customer is. Remember: You're looking for repeat business.
- Don't make promises you can't keep.
- Don't say you can weld everything. Visually size up and evaluate every job. Know what the customer expects.
- Never quote a job over the phone.
Dos For Safety
- Evaluate the work area for possible fire hazards. When your helmet's down and you're welding, a spark can start an uncontrollable brush fire. Find out if that open coffee can with a liquid in it contains water or gasoline. Cardboard, paper, wood, fertilizer, insulation, rubber, and plastics all burn well at elevated welding temperatures. You are responsible for what happens, even after you're
gone. If the environment is questionable, don't hesitate to hook up a couple of 50-foot garden hoses with nozzles.
- Go to Goodwill or a similar store and buy five or six old towels and a couple of old blankets. They can be lightly wet down to cover floors, furniture, carpeting, and cushioned boat seats, for example, that hot metal can damage. They cost a fraction of what heat blankets cost.
- For early morning work, use an electric heat gun or light propane torch to dry the morning dew before starting work.
- If the weld repair is on stainless steel hydraulic pipe or tube, remove the tube from the system. Clean and purge it internally with argon before you weld. If you can't remove the tube, pass up the job. Hydraulic lines that can't be purged are burned on the interior, and the structural integrity will be damaged. Also, hydraulic fluids can be flammable at welding temperatures; some are explosive.
Dos for Welding
- When welding aluminum or stainless steel, it's important to clean it first. A 3-inch stainless steel cup wire wheel on an electric angle grinder is best, 0.020-in. wire size.
- Always keep your welding machine under cover when it's not in use. The sun can damage it as much as rain or snow.
- GTAW dockside will require some type of wind break. Even a 2-MPH breeze is enough to blow away your shielding gas. Blue tarps or old blankets and some duct tape will take care of that problem.
- Industrial, commercial, and some truck fuel tanks (no personal passenger vehicles) are very expensive: $2,000 to $3,000 with parts and labor. They are weldable with ER4043 filler metal. Have the tank removed from the truck for two reasons: One, today's tractor trailer rigs have high-tech electronics onboard that welding currents and high frequency can damage. Two, the tank should be
thoroughly washed with soap and water or properly purged with straight argon for two to three hours at a 5- to 10-cubic-feet-per-hour flow rate and continually purged while welding. There should be only one entrance and one exit during purging.
- If you're asked to weld on machined parts, make every effort to identify the steel. If the steel has been identified as "free machining" steel (SAE 11xx, 12xx, xxLxx), pass up this job. These steels have elevated amounts of sulfur, phosphorus, or lead to aid in the machinability of the steel but are gross contaminants for a good-quality weld. Other metals that may prove difficult to weld are high-tin or -zinc alloys of copper, galvanized steel, and cast iron.
Don'ts for Welding
- Don't weld trailer hitches on private vehicles. "Good ol' boy Joe" will overload it every time, and if you were the last one to touch it, his insurance company will look for you. Also, sending welding current through newer car and truck frames can damage onboard electronics seriously if you don't take proper precautions. In essence, that $50 hitch could cost you thousands of dollars.
- Don't let the owner of a broken part tell you how to repair it unless you're sure he knows what he's talking about. The repair is your responsibility.
- Don't alter or modify a part's original design beyond its intended use or design with your repair. For example, you might be asked to weld a few brackets on a pontoon to convert a canvas top to a hard top. It's a sure bet someone will use it for a diving platform. After a half-dozen people get up there and it collapses, you will be the scapegoat.
- Don't weld a heat-treated part. If it isn't properly heat-treated after welding, the part will have severe structural integrity problems. Such parts include mower blades, crankshafts, camshafts, pump impellers, high-grade chain hooks, high-grade nuts and bolts, high-strength chain, truck frames, hydraulic cylinder shafts, high-pressure vessels, tire rims, and tool and die steel.
- Don't try to weld over paint, grease, rust, heavy mill scale, or wet metal. Porosity, lack of fusion, lack of penetration, and undercut will result.
- Don't try to plug-weld or finish-weld a repair on a pontoon tube without pulling the vent plug on the top of the tube; almost all pontoon tubes have them. If they don't, you will have to drill a 3/16- or 1/4-in. hole as close as possible to the top of the tube. After you're finished welding, seal the drilled hole with a high-quality silicone caulk. While you're welding, heat causes the pressure inside the tube to increase by about 1 or 2 pounds maximum. As you finish the weld and close things up, the internal pressure will blow out the last of the liquid weld puddle. You never can finish a weld unless you have a vent to allow pressure to escape.
Next time we'll look at tips for welding stainless steel and aluminum.
About the Author
About the Publication
subscribe now
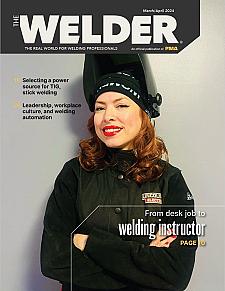
The Welder, formerly known as Practical Welding Today, is a showcase of the real people who make the products we use and work with every day. This magazine has served the welding community in North America well for more than 20 years.
start your free subscription- Stay connected from anywhere
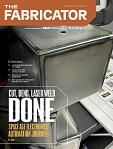
Easily access valuable industry resources now with full access to the digital edition of The Fabricator.
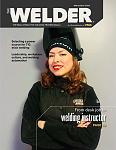
Easily access valuable industry resources now with full access to the digital edition of The Welder.
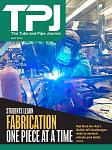
Easily access valuable industry resources now with full access to the digital edition of The Tube and Pipe Journal.
- Podcasting
- Podcast:
- The Fabricator Podcast
- Published:
- 04/16/2024
- Running Time:
- 63:29
In this episode of The Fabricator Podcast, Caleb Chamberlain, co-founder and CEO of OSH Cut, discusses his company’s...
- Trending Articles
Sheffield Forgemasters makes global leap in welding technology
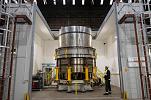
ESAB unveils Texas facility renovation
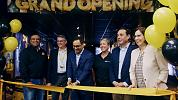
Engine-driven welding machines include integrated air compressors
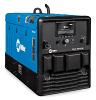
How welders can stay safe during grinding
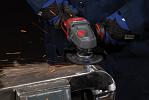
The impact of sine and square waves in aluminum AC welding, Part I
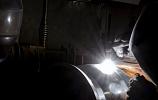
- Industry Events
16th Annual Safety Conference
- April 30 - May 1, 2024
- Elgin,
Pipe and Tube Conference
- May 21 - 22, 2024
- Omaha, NE
World-Class Roll Forming Workshop
- June 5 - 6, 2024
- Louisville, KY
Advanced Laser Application Workshop
- June 25 - 27, 2024
- Novi, MI