Senior Editor
- FMA
- The Fabricator
- FABTECH
- Canadian Metalworking
Categories
- Additive Manufacturing
- Aluminum Welding
- Arc Welding
- Assembly and Joining
- Automation and Robotics
- Bending and Forming
- Consumables
- Cutting and Weld Prep
- Electric Vehicles
- En Español
- Finishing
- Hydroforming
- Laser Cutting
- Laser Welding
- Machining
- Manufacturing Software
- Materials Handling
- Metals/Materials
- Oxyfuel Cutting
- Plasma Cutting
- Power Tools
- Punching and Other Holemaking
- Roll Forming
- Safety
- Sawing
- Shearing
- Shop Management
- Testing and Measuring
- Tube and Pipe Fabrication
- Tube and Pipe Production
- Waterjet Cutting
Industry Directory
Webcasts
Podcasts
FAB 40
Advertise
Subscribe
Account Login
Search
Skills gap, or education gap?
- By Tim Heston
- December 11, 2012
As just one example, The New York Times recently covered several issues that don’t put manufacturing in a favorable light, or at least aren’t flattering to the industry. First there was a series last week that described how large corporations, like Caterpillar, negotiate tax deals with local governments, many of which bend over backward to attract them to the area. The argument goes that large employers build wealth in the community, which in turn funnels back to the government. Over the long term, government officials assume the payback is far greater than the tax breaks. But what if those plants close? The local employer turns from a shining star into an albatross that the community may not be able to shake for years.
Even if the plants don’t close, the wages they pay may not be great. Consider another Times article, this one published in November, about how entry level pay in manufacturing is waning. Reporter Adam Davidson quoted The Boston Consulting Group. This same consultancy that predicted a manufacturing Renaissance recently wrote a report that called into question the skilled labor crisis. “Trying to hire high-skilled workers at rock-bottom rates is not a skills gap,” it said.
“It’s hard not to break out laughing,” Mark Price, a labor economist at the Keystone Research Center, told Davidson. “If there’s a skill shortage, there has to be rises in wages. It’s basic economics.”
This all paints an unfavorable view of manufacturing. Greedy corporations seek out tax breaks. The big plants set up shop and, yes, may support a large network of suppliers, but they and their suppliers don’t pay great starting wages.
Above all else, business owners want certainty. Yes, many manufacturers do have low starting pay, but that’s for the unskilled and inexperienced who present a lot of uncertainty to the employer. Will they make the cut? Can they be trained? Will they fit in? Manufacturers don’t know, so they hire them at a lower-than-average wage, train them, and raise their wages over time. The extremely wide pay range for skilled positions, as reported by the Fabricators & Manufacturers Association’s 2012 wage survey, suggests this trend.
As the Times pointed out, many corporations choose locales with less generous tax breaks because the area may have a more employable work force. Yes, we always hear about the threat of a plant moving overseas to low-cost countries. But as shown in this year’s financial ratio survey from FMA, direct labor costs represent only between 9 and 12 percent of overall sales for the average fabricator. Material is by far the dominant cost (at 30 to 50 percent), and the faster those employees can turn that material into a sellable, quality product, get it into customer hands, and receive payment for it, the more successful the manufacturer can be. Only a smart, engaged work force can make that happen.
Does the metal fabrication industry have companies that don’t pay a fair wage, even to those with skills that merit such wages? Sure. I’ve received e-mails from welders and machine operators who make very good money. And then I’ve received e-mails from those who tell me they have the technical skills yet can’t make a living wage. Reality is messy, and this business has frustrating situations like any other sector does.
What makes manufacturing unique, perhaps, is that the business used to be known for its good starting pay. Manufacturing built the Middle Class. Of course, high schools and secondary vocational schools used to provide a much better technical education, with geometry and trigonometry seen as basic, core requirements.
Now, manufacturing still provides opportunities, but low starting wages aren't attracting talent. Yes, a worker can climb the ranks to make good money, but low starting wages are scaring many away from the business. Look at any comment thread on any article on the skilled labor shortage, like a recent one on 60 Minutes, and you can feel the frustration brewing.
I have talked with fabricators in some markets that have pushed their starting wages up significantly to attract experienced talent. The trick: They hire fewer people, but they're far more productive than a larger, inexperienced work force. Crow Corp. in Texas is just one example.
But this doesn't always work. A local area may simply not have the talent. Or if it does have the talent, the people may not fit in with the company culture. I've talked with fabricators who prefer to hire people for the "soft skills" first. Can they work well with others? Can they be cross trained? Will they be an engaged employee, question the status quo, and dream up new and better ways of getting the job done? Jay Manufacturing Oshkosh Inc. is just one example.
Sure, you can easily paint a stark picture of evil employers unwilling to offer better pay to attract talent. But the issue is subtler than that. Someone who's a great welder doesn't automatically make that person a great employee. At the same time, I don't often hear stories of a job shop owner--who paid slave wages to his workers--retiring early and living a life of leisure.
The real problem isn’t that manufacturers are paying entry-level wages similar to Walmart’s and other retail and fast food companies’. The real problem is that both Walmart and manufacturers are drawing from the same labor pool.
As Davidson aptly put it, “The so-called skills gap is really a gap in education, and that affects all of us.”
subscribe now
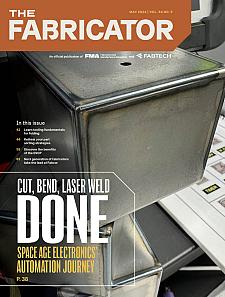
The Fabricator is North America's leading magazine for the metal forming and fabricating industry. The magazine delivers the news, technical articles, and case histories that enable fabricators to do their jobs more efficiently. The Fabricator has served the industry since 1970.
start your free subscriptionAbout the Author
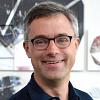
Tim Heston
2135 Point Blvd
Elgin, IL 60123
815-381-1314
Tim Heston, The Fabricator's senior editor, has covered the metal fabrication industry since 1998, starting his career at the American Welding Society's Welding Journal. Since then he has covered the full range of metal fabrication processes, from stamping, bending, and cutting to grinding and polishing. He joined The Fabricator's staff in October 2007.
- Stay connected from anywhere
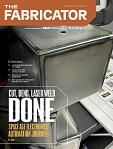
Easily access valuable industry resources now with full access to the digital edition of The Fabricator.
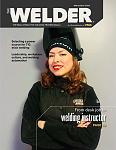
Easily access valuable industry resources now with full access to the digital edition of The Welder.
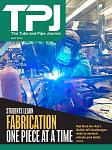
Easily access valuable industry resources now with full access to the digital edition of The Tube and Pipe Journal.
- Podcasting
- Podcast:
- The Fabricator Podcast
- Published:
- 04/16/2024
- Running Time:
- 63:29
In this episode of The Fabricator Podcast, Caleb Chamberlain, co-founder and CEO of OSH Cut, discusses his company’s...
- Trending Articles
Tips for creating sheet metal tubes with perforations
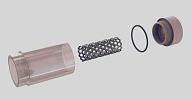
Supporting the metal fabricating industry through FMA
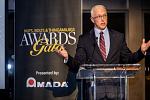
JM Steel triples capacity for solar energy projects at Pennsylvania facility
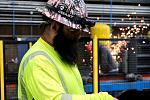
Fabricating favorite childhood memories
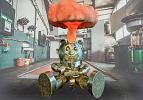
Omco Solar opens second Alabama manufacturing facility
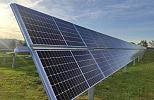
- Industry Events
16th Annual Safety Conference
- April 30 - May 1, 2024
- Elgin,
Pipe and Tube Conference
- May 21 - 22, 2024
- Omaha, NE
World-Class Roll Forming Workshop
- June 5 - 6, 2024
- Louisville, KY
Advanced Laser Application Workshop
- June 25 - 27, 2024
- Novi, MI