- FMA
- The Fabricator
- FABTECH
- Canadian Metalworking
Our Publications
Categories
- Additive Manufacturing
- Aluminum Welding
- Arc Welding
- Assembly and Joining
- Automation and Robotics
- Bending and Forming
- Consumables
- Cutting and Weld Prep
- Electric Vehicles
- En Español
- Finishing
- Hydroforming
- Laser Cutting
- Laser Welding
- Machining
- Manufacturing Software
- Materials Handling
- Metals/Materials
- Oxyfuel Cutting
- Plasma Cutting
- Power Tools
- Punching and Other Holemaking
- Roll Forming
- Safety
- Sawing
- Shearing
- Shop Management
- Testing and Measuring
- Tube and Pipe Fabrication
- Tube and Pipe Production
- Waterjet Cutting
Industry Directory
Webcasts
Podcasts
FAB 40
Advertise
Subscribe
Account Login
Search
Bending and Forming - Page 28
-
- From The Fabricator
Amsted Automotive Group’s MVT unit produces first powertrain components
- Feb 3, 2022
- News Release
Amsted Automotive Group’s MVT business unit has produced the first metal formed products manufactured under the MVT joint venture.
-
- From The Fabricator
How stampers can achieve near-perfect part quality with ERP software
Manual documentation, outdated documents, postproduction inspections, and no traceability result in high scrap rates, poor control, customer rejects, and recurring quality problems for metal stamping operations. A robust quality module in ERP software can remove those obstacles.
-
- From The Fabricator
Benchmaster to serve as West Coast dealer for Amada Press Systems America
- Feb 1, 2022
- News Release
Press manufacturer Benchmaster Inc., Riverside, Calif., has announced a dealer representative agreement with Amada Press Systems America.
-
- From The Fabricator
Okay Industries appoints business development executive
- Feb 1, 2022
- News Release
Okay Industries, New Britain, Conn., a contract manufacturer of components and subassemblies for global medical device OEMs, has named Joshua Chaffee as a business development executive.
-
- From The Fabricator
How metal fabricators take on their own challenges
Some of a job shop’s best work is fabricating products that help to resolve its own challenges.
-
- From The Fabricator
Approaches for improving press feed operations
- By John Kwiatkowski and Tom Brokie
- Jan 27, 2022
- Article
The most common complaints heard in the pressroom are the lack of trained workers, supply chain holdups, and a struggle to gain efficiencies. The good news is that there are many ways to improve the performance of a press feed without breaking the bank.
-
- From The Fabricator
Sigma Electric rebrands to Sigma Engineered Solutions
- Jan 26, 2022
- News Release
In recognition of its growing line of products and services, Sigma Electric is changing its name to Sigma Engineered Solutions.
-
- From The Fabricator
AIDA’s NSX mechanical press reaches speeds up to 300 SPM for high-volume production
- Jan 26, 2022
- Product Release
AIDA-America offers the 110-metric-ton NSX mechanical stamping press.
-
- From The Fabricator
Macrodyne increases European manufacturing capabilities through Dunkes acquisition
- Jan 21, 2022
- News Release
Toronto-based hydraulic press manufacturer Macrodyne Technologies Inc. has acquired Dunkes GmbH, a German press manufacturer.
-
- From The Fabricator
Why the right tooling matters for an old press brake
- By Steve Benson
- Jan 21, 2022
- Article
If your shop is having trouble setting up an old press brake, you might want take a look at your tooling, writes bending guru Steve Benson.
-
- From The Fabricator
Ascent hydraulic presses from Beckwood designed for cost efficiency
- Jan 21, 2022
- Product Release
Beckwood Press Co. has launched the Ascent line of standard hydraulic presses. Models are available from 30 to 500 tons in 21 different frame sizes.
-
- From The Fabricator
Okay Industries names strategic accounts manager
- Jan 20, 2022
- News Release
Okay Industries Inc., New Britain, Conn., a contract manufacturer of components and subassemblies for global medical device OEMs, has promoted Danielle Koonz to strategic accounts manager.
-
- From The Fabricator
Three new employees hired at AIDA-America
- Jan 19, 2022
- News Release
AIDA-America, metal stamping press manufacturer in Dayton, Ohio, has hired three staff members.
-
- From The Fabricator
New Year’s resolution in metalforming: Dream, visualize, and execute
- By Bill Frahm
- Jan 11, 2022
- Article
Metal forming companies can use visualization as a tool to overcome production and business challenges while simultaneously fostering employee growth.
-
- From The Fabricator
Volvo Cars invests in new press hardening furnaces from AP&T
- Jan 7, 2022
- News Release
Volvo Car Body Components in Olofström, Sweden, has ordered two new multilayer furnaces from AP&T for the production of press-hardened automotive components.
subscribe now
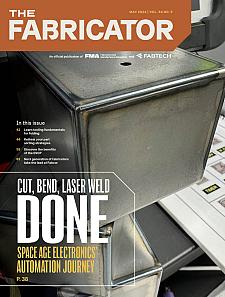
The Fabricator is North America's leading magazine for the metal forming and fabricating industry. The magazine delivers the news, technical articles, and case histories that enable fabricators to do their jobs more efficiently. The Fabricator has served the industry since 1970.
start your free subscription- Podcasting
- Podcast:
- The Fabricator Podcast
- Published:
- 04/16/2024
- Running Time:
- 63:29
In this episode of The Fabricator Podcast, Caleb Chamberlain, co-founder and CEO of OSH Cut, discusses his company’s...
- Trending Articles
Capturing, recording equipment inspection data for FMEA
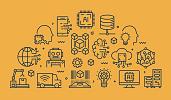
Tips for creating sheet metal tubes with perforations
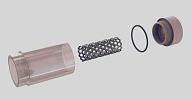
Are two heads better than one in fiber laser cutting?
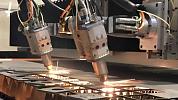
Supporting the metal fabricating industry through FMA
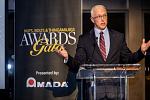
Zekelman Industries to invest $120 million in Arkansas expansion
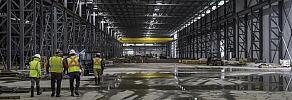
- Industry Events
16th Annual Safety Conference
- April 30 - May 1, 2024
- Elgin,
Pipe and Tube Conference
- May 21 - 22, 2024
- Omaha, NE
World-Class Roll Forming Workshop
- June 5 - 6, 2024
- Louisville, KY
Advanced Laser Application Workshop
- June 25 - 27, 2024
- Novi, MI
- Upcoming Webcasts
Navigating Change: The Manufacturer’s Guide to Change Management with ERP Implementation
- May 16, 2024
- Sponsored
- Presented By: ECI Software Solutions, M1