- FMA
- The Fabricator
- FABTECH
- Canadian Metalworking
Our Publications
Categories
- Additive Manufacturing
- Aluminum Welding
- Arc Welding
- Assembly and Joining
- Automation and Robotics
- Bending and Forming
- Consumables
- Cutting and Weld Prep
- Electric Vehicles
- En Español
- Finishing
- Hydroforming
- Laser Cutting
- Laser Welding
- Machining
- Manufacturing Software
- Materials Handling
- Metals/Materials
- Oxyfuel Cutting
- Plasma Cutting
- Power Tools
- Punching and Other Holemaking
- Roll Forming
- Safety
- Sawing
- Shearing
- Shop Management
- Testing and Measuring
- Tube and Pipe Fabrication
- Tube and Pipe Production
- Waterjet Cutting
Industry Directory
Webcasts
Podcasts
FAB 40
Advertise
Subscribe
Account Login
Search
More from The Fabricator
-
- From The Fabricator
International Thermal Systems, Snap Logistics send supplies to Houston for hurricane aid
- Sep 6, 2017
- Shop Management
- News Release
International Thermal Systems LLC (ITS), a Milwaukee-based manufacturer of thermal processing industrial ovens, furnaces, and washer systems, teamed up with trucking company Snap Logistics to collect and ship supplies for those affected by Hurricane Harvey. In three days, ITS and Snap Logistics...
-
- From The Welder
Tungsten electrode grinder grinds electrodes longitudinally
- Sep 6, 2017
- Consumables
- Product Release
Huntingdon Fusion Techniques HFT® has re-initiated the manufacturing of the TEG-2 tungsten electrode grinder under the new name of TEG-1000. Available from Cob Industries, the grinder produces repeatable tungsten electrode points, enabling consistent, repeatable arc performance and welding...
-
- From The Fabricator
Morris Group selected to supply 3-D printing technology for Desktop Metal
- Sep 6, 2017
- Shop Management
- News Release
Morris Group Inc., a CNC machine tool supply network based in Windsor, Conn., has been selected by Desktop Metal of Burlington, Mass., as a top-tier, Diamond Partner supplier of its Studio System™ metal 3-D printing systems in 30 states from Maine to Florida to the Dakotas. The metal 3-D printing...
-
- From The Fabricator
Sterling Multi Products sold to IMH Products
- Sep 6, 2017
- Shop Management
- News Release
Sterling Multi Products (SMP), a supplier of metal components in Prophetstown, Ill., has been sold to Indianapolis-based IMH Products Inc. SMP has about 40 employees at its 115,000-sq.-ft. facility. IMH Products supplies metal components for industries such as commercial lighting, defense, tractor...
-
- From The Fabricator
Coldwater Machine Co. to expand in Ohio
- Sep 6, 2017
- Shop Management
- News Release
Coldwater Machine Co., a manufacturer and integrator of assembly automation and special machines, will add 27,500 sq. ft. to its current manufacturing space in Coldwater, Ohio, bringing the facility to 132,500 sq. ft. The addition will double the company’s available assembly areas for turnkey...
-
- From The Fabricator
Honeywell donates $2 million in PPE to aid Hurricane Harvey recovery efforts
- Sep 6, 2017
- Safety
- News Release
Morris Plains, N.J.-based Honeywell has donated about $2 million in personal protective equipment (PPE) to support first responders and emergency personnel in their efforts to assist their communities following the devastation of Hurricane Harvey. The donation includes nearly 100,000 pieces of PPE,...
-
- From The Fabricator
Rockford Systems to host Oct. 17 webinar on press brake safeguarding
- Sep 6, 2017
- Safety
- News Release
Rockford Systems LLC, Rockford, Ill., a provider of machine safeguarding products and services, will host a webinar titled "Safeguarding Press Brakes: Light Curtains vs. Laser AOPD," on Tuesday, Oct. 17, from 10 to 11 a.m. CDT. This free, interactive webinar will take an in-depth look at the...
-
- From The Fabricator
Nonaerosol degreasers offered in industrial-strength formulas
- Sep 6, 2017
- Shop Management
- Product Release
WD-40 Co. has added nonaerosol, industrial-strength cleaner and degreaser products to its WD-40® Specialist® line. The products are designed for use in highly regulated environments for cleaning and degreasing work sites, tools, equipment, and machinery. The low-odor degreasers have a water-based...
-
- From The Fabricator
R&D Update: Warm-forming and magnesium , Part I
- Sep 6, 2017
- Bending and Forming
- Article
Past columns have been devoted to magnesium’s physical and mechanical properties as they relate to the warm-forming process and tool design. It was found that low die corner and punch temperatures improve the limiting draw ratio (LDR), which is the ratio of the initial blank diameter to the punch...
-
- From The Fabricator
AME, WiM announce collaboration
- Sep 5, 2017
- Shop Management
- News Release
Rolling Meadows, Ill.-based AME has announced that George Saiz, president/CEO, will speak at the 2017 Women in Manufacturing (WiM) Summit, Sept. 13-15 in Hartford, Conn. Saiz will focus on sticking points for successful lean implementation and the three key elements for becoming an extraordinary...
-
- From The Fabricator
IPG, MC Machinery form laser manufacturing partnership
- Sep 5, 2017
- Laser Cutting
- News Release
Fiber laser and amplifier provider IPG Photonics Corp., Oxford, Mass., has entered into an agreement with metalworking and metal fabrication machine manufacturer MC Machinery Systems Inc. (MCM) to offer sales and service of IPG’s industrial laser systems for materials processing applications....
-
- From The Fabricator
Duralar names CTI as provider of hard-coating services
- Sep 5, 2017
- Finishing
- News Release
Duralar Technologies, a Tucson, Ariz., developer of ultrahard metal coatings, has named Phoenix-based Coating Technologies Inc. (CTI) as an authorized provider of Duralar® coating services. Duralar Technologies is the creator of ultrahard coatings that can cover both the internal and external...
-
- From The Fabricator
Meritor acquires Fabco Holdings product portfolio and technologies
- Sep 5, 2017
- Shop Management
- News Release
Troy, Mich.-based Meritor Inc. has acquired the product portfolio and related technologies of Fabco Holdings Inc. and its subsidiaries. With the addition of Fabco's products, Meritor will have an expanded line, including transfer cases, specialty gear boxes, auxiliary transmissions, and power...
-
- From The Fabricator
Double-sided flap disc offered in three grits
- Sep 5, 2017
- Finishing
- Product Release
Forney Industries has introduced what it says is the first double-sided flap disc to the U.S. market. Three varieties are available. The company created a 40/40 grit double-sided flap disc for a coarse finish, a 40/80 grit for coarse-to-fine finish, and 60/120 grit for medium-to-fine finish. The...
-
- From The Fabricator
Die Science: Deep drawing step by step
- By Art Hedrick
- Sep 5, 2017
- Bending and Forming
- Article
Drawing can be defined as a forming process in which the flow of metal into a cavity or over a post is controlled. Perhaps one of the biggest misconceptions about deep drawing is that the metal is stretched into the part geometry. While it’s true that a lot of the parts (including automobile...
subscribe now
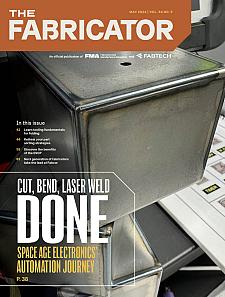
The Fabricator is North America's leading magazine for the metal forming and fabricating industry. The magazine delivers the news, technical articles, and case histories that enable fabricators to do their jobs more efficiently. The Fabricator has served the industry since 1970.
start your free subscription- Podcasting
- Podcast:
- The Fabricator Podcast
- Published:
- 04/16/2024
- Running Time:
- 63:29
In this episode of The Fabricator Podcast, Caleb Chamberlain, co-founder and CEO of OSH Cut, discusses his company’s...
- Trending Articles
Capturing, recording equipment inspection data for FMEA
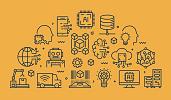
Tips for creating sheet metal tubes with perforations
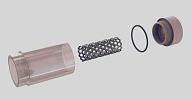
Are two heads better than one in fiber laser cutting?
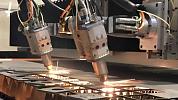
Supporting the metal fabricating industry through FMA
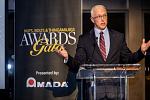
Zekelman Industries to invest $120 million in Arkansas expansion
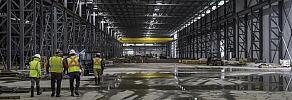
- Industry Events
16th Annual Safety Conference
- April 30 - May 1, 2024
- Elgin,
Pipe and Tube Conference
- May 21 - 22, 2024
- Omaha, NE
World-Class Roll Forming Workshop
- June 5 - 6, 2024
- Louisville, KY
Advanced Laser Application Workshop
- June 25 - 27, 2024
- Novi, MI
- Upcoming Webcasts
Navigating Change: The Manufacturer’s Guide to Change Management with ERP Implementation
- May 16, 2024
- Sponsored
- Presented By: ECI Software Solutions, M1