Vice President of Engineering
- FMA
- The Fabricator
- FABTECH
- Canadian Metalworking
Categories
- Additive Manufacturing
- Aluminum Welding
- Arc Welding
- Assembly and Joining
- Automation and Robotics
- Bending and Forming
- Consumables
- Cutting and Weld Prep
- Electric Vehicles
- En Español
- Finishing
- Hydroforming
- Laser Cutting
- Laser Welding
- Machining
- Manufacturing Software
- Materials Handling
- Metals/Materials
- Oxyfuel Cutting
- Plasma Cutting
- Power Tools
- Punching and Other Holemaking
- Roll Forming
- Safety
- Sawing
- Shearing
- Shop Management
- Testing and Measuring
- Tube and Pipe Fabrication
- Tube and Pipe Production
- Waterjet Cutting
Industry Directory
Webcasts
Podcasts
FAB 40
Advertise
Subscribe
Account Login
Search
The regrind process for tube mill tooling - Part II
Machining, inspection, and shipping
- By Chris Miller
- June 13, 2006
- Article
- Tube and Pipe Production
Editor's Note: This is the second article in a two-part series on regrinding tube mill tooling. Part I discussed the first two steps of the five-step process: (1) receiving and inspection and (2) analyzing and creating work instructions. Part II discusses (3) machining, (4) final inspection and documentation, and (5) packaging and shipping.
![]() |
Machining
In the regrind shop, the production supervisor reviews the work instructions and regrind charts and determines a "game plan" for each set of tooling. While most follow a standard routing pattern, the work instructions are reviewed for any special circumstances or items that may be specified. All new items required and any items requiring plating are either purchased or sent to production immediately. The new and plated items work themselves back into the regrind process when required. The supervisor reviews the specified delivery date and stages the tooling set for production accordingly.
The first step is face grinding, which usually is performed on a rotary-type surface grinder. All widths are ground on the inside or outside faces as specified and held to the dimensions shown on the regrind chart.
The second operation is to use an ID cylindrical grinder to grind the bores of rolls that have been plated. All of the plated bores are ground to the original print tolerances as specified.
The third operation is to regrind the contours, usually by turning on a CNC lathe using downloaded programs with the specifications shown on the original print or drawing. Each roll is machined to make the actual sizes on the recontoured rolls equal to the after-grind values shown on the regrind chart.
After all rolls of the set have gone through the regrind process, they are reviewed and visually checked. If everything appears to be satisfactory, any neces-sary shims or spacers are brought to their final sizes and the roll contours polished to a high-luster finish either on a lathe or with a special polishing machine. Once the polishing operation is completed, the tooling set proceeds to the final inspection process.
Final Inspection and Documentation
Each roll again is measured on the rim, root, radius, width, and bore, and these values are verified against the after-grind values on the regrind chart. A visual inspection ensures all previous wear, cracks, chip-outs, and inclusions have been eliminated. The actual location of the contour and the amount of runout between the contour and the bore also are checked.
Once all measurements have been veri-fied, the regrind chart is sent back to the regrind engineer for a final review. The regrind engineer takes care of any problems or concerns and then saves the chart in the regrind contractor's file for that tube or pipe producer. He also prints out a copy of the chart, laminates it, and puts the chart, along with a report verifying that the tooling set has passed inspection, into a documentation envelope. The tooling set and documentation envelope now are clear to move on to packaging.
Packaging and Shipping
The packaging operation is not one to be taken lightly. The container must be able to support the weight of the tooling set during shipment. The shipper should place each roll carefully into the shipping container and isolate it to prevent banging, moving, or shifting during shipment, which can result in chips, dents, and marring.
Packing the tooling in mill pass order helps the recipient when unpacking the container. Keeping passes together, reassembling multipiece rolls, and putting any necessary shims and spacers together near the top of the container simplify the customer's unpacking and the mill setup.
The final item to go into the shipping container is the documentation envelope. That way, it is the first thing the tube or pipe producer sees when opening the container. This allows for immediate attention to the regrind charts and any special notes that are necessary when reinstalling the tooling set onto the tube or pipe mill.
Tooling Maintenance Programs
The goal of a comprehensive tooling maintenance program is to achieve adequate roll condition for each production run while maximizing footage run and product quality, minimizing rework cost, and facilitating reordering worn-out tooling in a timely manner.
The most practical method is to combine good housekeeping practices with visual or micrometer inspections, as well as adequate recordkeeping. This provides useful maintenance information and aids the operator in making faster and more accurate setups on the mill.
New or reground tooling should be set up to the original setup chart specification supplied by the tooling manufacturer, along with regrind shims, if required. The operator then fine-tunes the setup during the initial portion of the production run until the setup is perfect; the remainder of the run then is completed.
The key to quicker setups on future runs is to start up the next run where the last run left off. One of the best ways to do this is to use a roll flange clearance chart. Using feeler gauges or any other appropriate method, the operator can record flange clearance values quickly.
Over time this also provides very good information about the wear condition of the tooling set.
This form also can be used to record footage from each production run, which provides information for a tooling history record. This record documents the purchase date, scrap size, production footage, regrind dates, undersize amounts, and running cost, if desired. This record can be kept for both full and partial sets.
These records should be stored in sepa-rate files that consist of the roll prints, regrind charts, roll flange clearance chart, and the history of production runs for that particular tooling set. The contents of these files can be analyzed when needed to develop and predict future regrind schedules, new tooling schedules, and the cost history of both.
Being proactive generally achieves better results than being reactive. Addressing concerns before they become problems is beneficial to a tube or pipe mill operation. Keeping the tooling sets on clearly labeled racks in a clean and organized fashion results in quicker changeovers. Replacing bad bearings when the rolls come off of the mill eliminates costly, unscheduled maintenance shutdowns during production runs. Inspecting the roll tooling as it is being taken off of the mill can catch a potential future problem that can be repaired before the next production run of that tooling set.
A good tooling maintenance program yields faster tooling setups, faster production runs, less downtime, less scrap, and a higher-quality product coming off the tube or pipe mill.
Chris Miller is vice president of engineering for Addison Machine Engineering Inc., 1301 Industrial St., Reedsburg, WI 53959, 608-524-6454, fax 608-524-6099, www.ameinc.com.
About the Author
Chris Miller
1301 Industrial St.
Reedsburg, WI 53959
608-524-6454
About the Publication
Related Companies
subscribe now
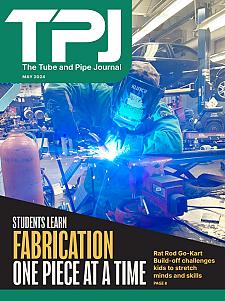
The Tube and Pipe Journal became the first magazine dedicated to serving the metal tube and pipe industry in 1990. Today, it remains the only North American publication devoted to this industry, and it has become the most trusted source of information for tube and pipe professionals.
start your free subscription- Stay connected from anywhere
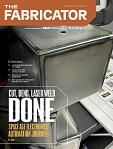
Easily access valuable industry resources now with full access to the digital edition of The Fabricator.
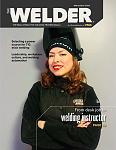
Easily access valuable industry resources now with full access to the digital edition of The Welder.
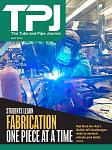
Easily access valuable industry resources now with full access to the digital edition of The Tube and Pipe Journal.
- Podcasting
- Podcast:
- The Fabricator Podcast
- Published:
- 04/16/2024
- Running Time:
- 63:29
In this episode of The Fabricator Podcast, Caleb Chamberlain, co-founder and CEO of OSH Cut, discusses his company’s...
- Trending Articles
Zekelman Industries to invest $120 million in Arkansas expansion
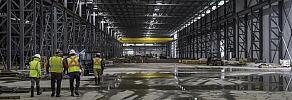
3D laser tube cutting system available in 3, 4, or 5 kW
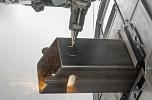
Corrosion-inhibiting coating can be peeled off after use
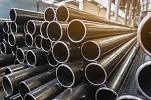
Brushless copper tubing cutter adjusts to ODs up to 2-1/8 in.
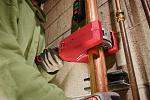
HGG Profiling Equipment names area sales manager
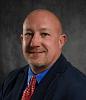
- Industry Events
16th Annual Safety Conference
- April 30 - May 1, 2024
- Elgin,
Pipe and Tube Conference
- May 21 - 22, 2024
- Omaha, NE
World-Class Roll Forming Workshop
- June 5 - 6, 2024
- Louisville, KY
Advanced Laser Application Workshop
- June 25 - 27, 2024
- Novi, MI