Graduate Research Associate
- FMA
- The Fabricator
- FABTECH
- Canadian Metalworking
Categories
- Additive Manufacturing
- Aluminum Welding
- Arc Welding
- Assembly and Joining
- Automation and Robotics
- Bending and Forming
- Consumables
- Cutting and Weld Prep
- Electric Vehicles
- En Español
- Finishing
- Hydroforming
- Laser Cutting
- Laser Welding
- Machining
- Manufacturing Software
- Materials Handling
- Metals/Materials
- Oxyfuel Cutting
- Plasma Cutting
- Power Tools
- Punching and Other Holemaking
- Roll Forming
- Safety
- Sawing
- Shearing
- Shop Management
- Testing and Measuring
- Tube and Pipe Fabrication
- Tube and Pipe Production
- Waterjet Cutting
Industry Directory
Webcasts
Podcasts
FAB 40
Advertise
Subscribe
Account Login
Search
R&D Update: Exploring the benefits of servo technology in the pressroom
Five case studies show how different methods help improve blanking results on servo presses
- By Berk Aykas, David Diaz-Infante, Dr., and Taylan Altan, Ph.D.
- March 28, 2019
- Article
- Bending and Forming
The use of servo technology can help to improve various sheet metal forming processes. A servo press allows precise control of the ram’s speed and position, while a servo cushion allows adjustment of the blank holder force (BHF) during the stroke. These characteristics give users a number of options for their processes (see “The effects of servo press motion and servo cushions on stamping results,” STAMPING Journal®, May/June 2017).
Researchers at the Center for Precision Forming (CPF) at The Ohio State University have conducted a series of experiments using servo technology in collaboration with AIDA-America, Shiloh Industries, IRMCO, and Hyson. In the experiments, using a 300-ton servo press and a 100-ton servo cushion, the researchers employed methods such as variable BHF, cushion pulsation, and attach/detach (see Figure 1) to improve drawability of the material, reduce springback, and maintain adequate edge quality during blanking without sacrificing productivity.
Case 1: Drawing of a Nonsymmetrical Part
Complex-phase steel (CP800) with 1.4-millimeter thickness was used to draw a 500- by 300-mm part up to a 65-mm depth. The high strength of this material caused wrinkles on the flange, even with a 400-kN BHF. A higher BHF of 500 kN led to a press overload.
To solve this problem, the researchers used a variable BHF, calculated via finite element simulations. By increasing the BHF just enough to prevent wrinkling along the stroke, they were able to form the part while maintaining the press and cushion force limits shown in Figure 2.
Case 2: Cushion Pulsation
Using a 1.0-mm 1008 steel, the researchers drew an 80- by 100-mm part to a 60-mm depth with an average speed of 90 mm per second. Initially they used a constant BHF of 85 kN, but that caused fracturing. By alternating the BHF between 85 and 20 kN with five pulses per second, they were able to form the part successfully (see Figure 3).
Cushion pulsation did not work for the same geometry in 1.0-mm aluminum Al 6205. This technique is limited by the response time in the cushion systems, as higher pulsation frequencies will lead to inaccuracies on the applied forces.
Case 3: Attach/Detach
The same geometry used for cushion pulsation was formed using a 1.0-mm-thick stainless steel SS304. On one hand, fracture was observed on this part when formed in one continuous 70-mm stroke at approximately 72 mm/sec., average speed. On the other hand, the part was successfully drawn up to the 70 mm when it was formed in two steps. Initially the part was drawn up to a 30-mm depth, later the upper die was retracted 5 mm, and finally the remaining 40 mm was formed.
Case 4: Springback Control
The researchers conducted a hat-shape bending operation, drawing a 720- by 120-mm blank of 1.2-mm-thick Al 5182-O to a 70-mm depth (see “Reducing springback in hat-shape bending with variable BHF using a servo-hydraulic cushion,” STAMPING Journal, March/April 2018). Increasing the BHF toward the end of the forming stroke helped stretch the part wall, which reduced bending stresses on this area and significantly decreased the springback (see Figure 4).
Similar results can be achieved by using a “stake bead” that allows stretching of the material toward the end of the forming stroke. Nevertheless, the use of a servo cushion allows a greater flexibility in adjusting the required force to every material and process.
Case 5: Edge Quality Control
Using a 200-ton AIDA servo press, the researchers blanked different advanced high-strength steels. They blanked the sheets at two different speeds (at tool/blank contact): 19.5 mm/sec. and 195 mm/sec. Visual inspection of the blanked perimeter, using a portable USB microscope, showed nonuniform cutting clearances, which confirmed that higher speeds led to tool misalignments due to the tool impact (see Figure 5).
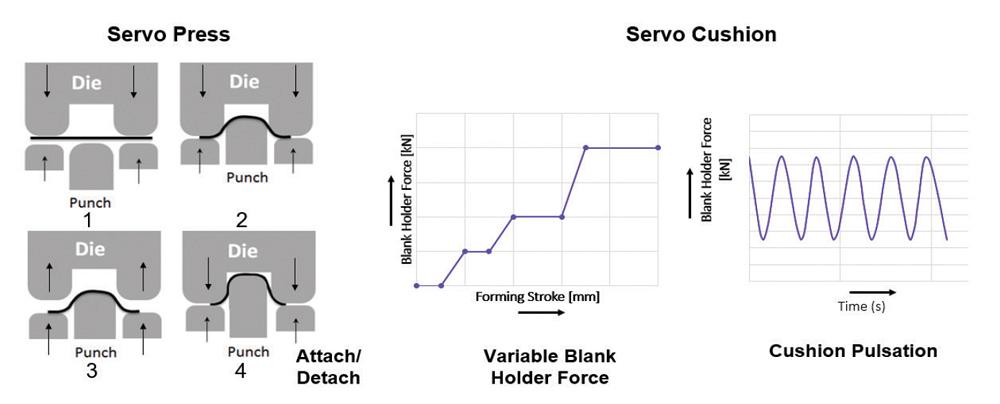
Figure 1
In the Attach/Detach method, after a partial forming, the upper die is retracted to release the part for a few seconds; later it continues the forming process. Variable BHF and cushion pulsation are examples of the variable cushion pressure as a function of time/stroke
A servo press is a good alternative for blanking, not only because of the higher speeds when compared to a mechanical press, but also because of the possibility of reducing the ram speed just before the tool contacts the blank while maximizing the speed on the remaining stroke. This reduction will lead to a decrease on the reverse load and, hence, to a more consistent edge while increasing tool life and decreasing the noise caused by tool impact.
While servo technology helped improve these sheet metal forming processes, in some cases, such as Case 3: Attach/Detach, the phenomenon behind the formability improvement is unclear, so it is difficult to know when and how to apply it. Further research is required to determine how best to apply servo technology in the pressroom.
About the Authors
Berk Aykas
Center for Precision Forming at The Ohio State University
1971 Neil Ave. Room 339 Baker Systems Engineering Building
Columbus, OH 43210
David Diaz-Infante, Dr.
Servo Press Scientist
250 W 5th St.
Minster, OH 45865
o 419 628 2331, d 419 501 1890, m 419 733 7971
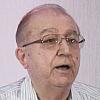
Taylan Altan, Ph.D.
Professor Emeritus and Director - Center for Precision Forming
Related Companies
subscribe now
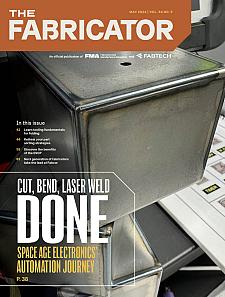
The Fabricator is North America's leading magazine for the metal forming and fabricating industry. The magazine delivers the news, technical articles, and case histories that enable fabricators to do their jobs more efficiently. The Fabricator has served the industry since 1970.
start your free subscription- Stay connected from anywhere
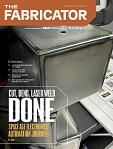
Easily access valuable industry resources now with full access to the digital edition of The Fabricator.
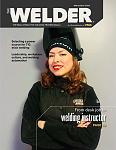
Easily access valuable industry resources now with full access to the digital edition of The Welder.
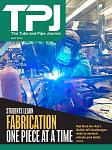
Easily access valuable industry resources now with full access to the digital edition of The Tube and Pipe Journal.
- Podcasting
- Podcast:
- The Fabricator Podcast
- Published:
- 04/16/2024
- Running Time:
- 63:29
In this episode of The Fabricator Podcast, Caleb Chamberlain, co-founder and CEO of OSH Cut, discusses his company’s...
- Trending Articles
Tips for creating sheet metal tubes with perforations
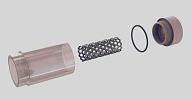
Supporting the metal fabricating industry through FMA
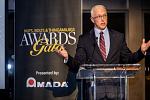
JM Steel triples capacity for solar energy projects at Pennsylvania facility
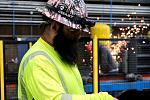
Are two heads better than one in fiber laser cutting?
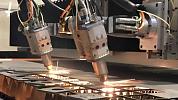
Fabricating favorite childhood memories
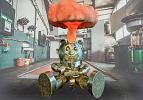
- Industry Events
16th Annual Safety Conference
- April 30 - May 1, 2024
- Elgin,
Pipe and Tube Conference
- May 21 - 22, 2024
- Omaha, NE
World-Class Roll Forming Workshop
- June 5 - 6, 2024
- Louisville, KY
Advanced Laser Application Workshop
- June 25 - 27, 2024
- Novi, MI