- FMA
- The Fabricator
- FABTECH
- Canadian Metalworking
Our Publications
Categories
- Additive Manufacturing
- Aluminum Welding
- Arc Welding
- Assembly and Joining
- Automation and Robotics
- Bending and Forming
- Consumables
- Cutting and Weld Prep
- Electric Vehicles
- En Español
- Finishing
- Hydroforming
- Laser Cutting
- Laser Welding
- Machining
- Manufacturing Software
- Materials Handling
- Metals/Materials
- Oxyfuel Cutting
- Plasma Cutting
- Power Tools
- Punching and Other Holemaking
- Roll Forming
- Safety
- Sawing
- Shearing
- Shop Management
- Testing and Measuring
- Tube and Pipe Fabrication
- Tube and Pipe Production
- Waterjet Cutting
Industry Directory
Webcasts
Podcasts
FAB 40
Advertise
Subscribe
Account Login
Search
Bending and Forming - Page 7
-
- From The Fabricator
Precision Metalforming Association acquires STAMPING Journal magazine, related assets
- May 5, 2023
- News Release
Precision Metalforming Association (PMA) has acquired STAMPING Journal magazine and its related assets from the Fabricators and Manufacturers Association, International (FMA).
-
- From The Fabricator
A manufacturer's disciplined approach to troubleshooting component problems
- By Bill Frahm
- May 5, 2023
- Article
A press shop experiences many types of failure. The right approach to troubleshooting can give employees better skills for the process and prevent more failures in the first place.
-
- From The Fabricator
Spirol acquires Ford Aerospace
- May 3, 2023
- News Release
Spirol, a global manufacturer of engineered fasteners, installation machines, and parts feeding equipment, has announced that Ford Aerospace Ltd., South Shields, U.K., will be joining the Spirol group of companies.
-
- From The Fabricator
AGS Automotive Systems expands manufacturing operations
- May 3, 2023
- News Release
Tier 1 auto supplier AGS Automotive Systems plans to expand its operations in Sterling Heights, Mich.
-
- From The Fabricator
Hear from experts at Manufacturing in an EV World Conference
- By Kate Bachman
- May 3, 2023
- Blog Post
The 2023 Manufacturing in an EV World Conference features experts and panel discussions on how electric vehicle production is shaping the future of metal forming.
-
- From The Fabricator
O’Neal Manufacturing Services installs largest TRUMPF press brake in U.S.
- May 1, 2023
- News Release
O'Neal Manufacturing Services (OMS), a supplier of fabricated metal components and welded assemblies, recently installed a TRUMPF TruBend 8010 press brake in its Pittsburgh fabrication center.
-
- From The Fabricator
Stamping Die Essentials: Draw reduction calculations
- By Art Hedrick
- Apr 28, 2023
- Article
In this sixth article on die design and construction fundamentals, Art Hedrick explains the calculations needed to perform a draw reduction.
-
- From The Fabricator
Boschert CombiLaser 4020 handles 6- by 12-ft. sheets
- Apr 27, 2023
- Product Release
Boschert has announced the availability of its new CombiLaser 4020 combination forming, punching, and laser cutting machine, which accommodates sheets up to 6 by 12 ft.
-
- From The Fabricator
Clow Stamping names director of manufacturing
- Apr 24, 2023
- News Release
Clow Stamping Co. has announced the promotion of Joe Goble to director of manufacturing.
-
- From The Fabricator
Coe ships coil line to Eaton Corp.
- Apr 24, 2023
- News Release
Coe Press Equipment, Sterling Heights, Mich., has shipped and installed a 48-in. coil processing line to the Highland, Ill., facility of Eaton Corp.
-
- From The Fabricator
Etna Products acquires metalworking fluids line from JTM Products
- Apr 20, 2023
- News Release
Etna Products, a Chagrin Falls, Ohio, developer and producer of lubricants for drawing and stamping of nonferrous materials, has acquired the metalworking fluids line of JTM Products, Solon, Ohio.
-
- From The Fabricator
Bump bending and air forming sheet metal on the press brake
- By Steve Benson
- Apr 20, 2023
- Article
Press brake guru Steve Benson answers questions about air forming and bump bending, including the many variables involved in each application.
-
- From The Fabricator
Ask the Expert: How can metal stampers achieve ever-tightening dimensional tolerance requirements?
- By Thomas Vacca
- Apr 20, 2023
- Article
It is possible to stamp to tight tolerances, as long as metal forming shops have the right tool frame, guide system, lead strip piloting, and strip progression clamping and use design for manufacturability with each tool.
-
- From The Fabricator
All Fabrication Machinery named distributor for MC Machinery/Mitsubishi Laser
- Apr 19, 2023
- News Release
All Fabrication Machinery Inc., Calgary, Alta., has joined the MC Machinery Systems/Mitsubishi Laser distribution network.
-
- From The Fabricator
AP&T offers factory-rebuilt presses
- Apr 19, 2023
- Product Release
AP&T is offering factory-rebuilt presses—older machines that its facility in Tranemo, Sweden, has fully rebuilt and upgraded to meet current performance and safety requirements
subscribe now
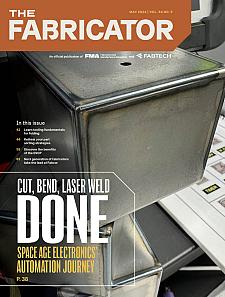
The Fabricator is North America's leading magazine for the metal forming and fabricating industry. The magazine delivers the news, technical articles, and case histories that enable fabricators to do their jobs more efficiently. The Fabricator has served the industry since 1970.
start your free subscription- Podcasting
- Podcast:
- The Fabricator Podcast
- Published:
- 04/16/2024
- Running Time:
- 63:29
In this episode of The Fabricator Podcast, Caleb Chamberlain, co-founder and CEO of OSH Cut, discusses his company’s...
- Trending Articles
Capturing, recording equipment inspection data for FMEA
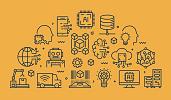
Tips for creating sheet metal tubes with perforations
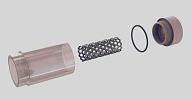
Are two heads better than one in fiber laser cutting?
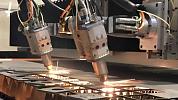
Supporting the metal fabricating industry through FMA
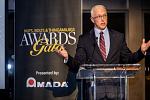
Zekelman Industries to invest $120 million in Arkansas expansion
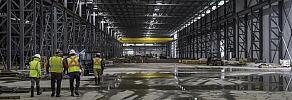
- Industry Events
16th Annual Safety Conference
- April 30 - May 1, 2024
- Elgin,
Pipe and Tube Conference
- May 21 - 22, 2024
- Omaha, NE
World-Class Roll Forming Workshop
- June 5 - 6, 2024
- Louisville, KY
Advanced Laser Application Workshop
- June 25 - 27, 2024
- Novi, MI
- Upcoming Webcasts
Navigating Change: The Manufacturer’s Guide to Change Management with ERP Implementation
- May 16, 2024
- Sponsored
- Presented By: ECI Software Solutions, M1