- FMA
- The Fabricator
- FABTECH
- Canadian Metalworking
Our Publications
Categories
- Additive Manufacturing
- Aluminum Welding
- Arc Welding
- Assembly and Joining
- Automation and Robotics
- Bending and Forming
- Consumables
- Cutting and Weld Prep
- Electric Vehicles
- En Español
- Finishing
- Hydroforming
- Laser Cutting
- Laser Welding
- Machining
- Manufacturing Software
- Materials Handling
- Metals/Materials
- Oxyfuel Cutting
- Plasma Cutting
- Power Tools
- Punching and Other Holemaking
- Roll Forming
- Safety
- Sawing
- Shearing
- Shop Management
- Testing and Measuring
- Tube and Pipe Fabrication
- Tube and Pipe Production
- Waterjet Cutting
Industry Directory
Webcasts
Podcasts
FAB 40
Advertise
Subscribe
Account Login
Search
Bending and Forming - Page 84
-
- From The Fabricator
Feintool earns GM Supplier Quality Excellence Award
- Feb 8, 2019
- News Release
Cincinnati-based Feintool U.S. has been awarded the General Motors (GM) Supplier Quality Excellence Award for the second consecutive year. The award recognizes Feintool’s achieving zero parts per million defects. Feintool makes fineblanked and forming parts for GM, including automatic...
-
- From The Fabricator
Specialty Strip & Oscillating adds 24-in. slitter for ribbon-wound steel coils
- Feb 8, 2019
- News Release
Specialty Strip & Oscillating Inc., Masury, Ohio, has added a 24-in. slitter machine that can cut metal as narrow as 1/4 in. It helps the company manufacture ribbon-wound coils that can have tempers, tolerances, edges, and finishes to customer specifications, weighing up to 5,000 lbs. The company...
-
- From The Fabricator
Nidec Press & Automation acquires SYS-DPA
- Feb 6, 2019
- News Release
Nidec Press & Automation (NPA) has announced the acquisition of a Germany-based provider of high-speed metal forming automation machinery and technology. Systeme and Steuerungen (SYS) and its subsidiary Die Peripherie Anlagen (DPA) join the NPA group of companies. Their products include high-speed...
-
- From The Fabricator
Dallas Industries delivers feed line to Tennessee Industrial Specialties
- Feb 5, 2019
- News Release
Dallas Industries™, Troy, Mich., a manufacturer of coil handling and press feeding equipment and controls for the stamping industry, has delivered a model DRFHDS-636 UnderLoop SpaceSaver™ servo feed line to Tennessee Industrial Specialties Inc., Sugar Springs, Tenn., a manufacturer of steel...
-
- From The Fabricator
SEYI America announces staff additions
- Feb 5, 2019
- News Release
SEYI-America Inc., a press manufacturer based in Tullahoma, Tenn., and Irvine, Calif., has announced the appointments of three new staff members. Scott Braito has been named director of sales for North America. David Brittain has been hired as senior regional sales manager for the Midwest, and...
-
- From The Fabricator
Get to know a metal fabrication guru
- By Tim Heston
- Feb 4, 2019
- Blog Post
Software can't do everything. In this business, it pays to get to know a sheet metal guru.
-
- From The Fabricator
What you need to know about tandem press brakes
- By Chris Robinson
- Feb 4, 2019
- Article
This overview of tandem press brakes can help fabricators understand what these dual setups can deliver.
-
- From The Fabricator
Demystifying aluminum extrusion bending
- By Craig Barnshaw
- Feb 2, 2019
- Article
Bending aluminum extrusions can be extremely challenging. But with the right design considerations, it doesn’t have to be.
-
- From The Fabricator
Industrial Innovations adds RDI Equipment to sales network
- Jan 30, 2019
- News Release
Industrial Innovations, Grandville, Mich., has added RDI Equipment Sales & Service, Barrie, Ont., as a representative of its metal forming and stamping equipment in Canada. Industrial Innovations manufactures industrial lubrication equipment for the metalworking industry and provides automated...
-
- From The Fabricator
TCR Integrated Stamping Systems adds staff
- Jan 29, 2019
- News Release
Wisconsin Rapids, Wis.-based TCR Integrated Stamping Systems, a provider of stamping lines, controls, equipment, and safety inspections, has announced several additions to its staff. The company has named Dennis Johnson as mechanical service manager. He has more than 25 years of experience in...
-
- From The Fabricator
AutoForm R8 software helps streamline digital process chain
- Jan 29, 2019
- Product Release
AutoForm Eng. GmbH has introduced its latest software version, AutoForm R8, which the company says can help support users in streamlining the digital process chain. It is suitable for users working with progressive dies, springback compensation, and parts produced from patchwork blanks. Users can...
-
- From The Fabricator
TCR Integrated Stamping Systems expands Wisconsin facility
- Jan 28, 2019
- News Release
TCR Integrated Stamping Systems, a provider of equipment for metal stamping companies, has recently expanded its office and shop space in Wisconsin Rapids, Wis. In addition to doubling its office space and adding square footage to the shop, it also has added trucks, trailers, a Haas CNC mill, and...
-
- From The Fabricator
In pursuit of 100 percent defect-free stampings
- By Kate Bachman
- Jan 25, 2019
- Article
To meet customer demands for defect-free parts, stampers use quality verification devices, such as a check fixture, vision system, CMM, or 3D laser scanner.
-
- From The Fabricator
Die Science: How to perform a draw reduction
- By Art Hedrick
- Jan 25, 2019
- Article
Art Hedrick explains how to determine blank diameter and number of drawing stations when performing a draw reduction.
-
- From The Fabricator
R&D Update: Using double bending tests to estimate edge fracture occurrence
- By Berk Aykas, David Diaz-Infante, Dr., and Taylan Altan, Ph.D.
- Jan 25, 2019
- Article
Researchers at the Center for Precision Forming share the results of FE simulations to determine an adequate sample size and tooling configuration for the double bend test, used to estimate edge fracture in metal forming.
subscribe now
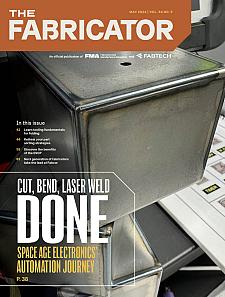
The Fabricator is North America's leading magazine for the metal forming and fabricating industry. The magazine delivers the news, technical articles, and case histories that enable fabricators to do their jobs more efficiently. The Fabricator has served the industry since 1970.
start your free subscription- Podcasting
- Podcast:
- The Fabricator Podcast
- Published:
- 04/16/2024
- Running Time:
- 63:29
In this episode of The Fabricator Podcast, Caleb Chamberlain, co-founder and CEO of OSH Cut, discusses his company’s...
- Trending Articles
Capturing, recording equipment inspection data for FMEA
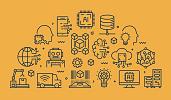
Tips for creating sheet metal tubes with perforations
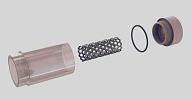
Are two heads better than one in fiber laser cutting?
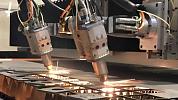
Supporting the metal fabricating industry through FMA
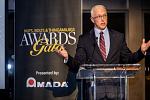
Zekelman Industries to invest $120 million in Arkansas expansion
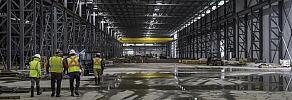
- Industry Events
16th Annual Safety Conference
- April 30 - May 1, 2024
- Elgin,
Pipe and Tube Conference
- May 21 - 22, 2024
- Omaha, NE
World-Class Roll Forming Workshop
- June 5 - 6, 2024
- Louisville, KY
Advanced Laser Application Workshop
- June 25 - 27, 2024
- Novi, MI
- Upcoming Webcasts
Navigating Change: The Manufacturer’s Guide to Change Management with ERP Implementation
- May 16, 2024
- Sponsored
- Presented By: ECI Software Solutions, M1