- FMA
- The Fabricator
- FABTECH
- Canadian Metalworking
Categories
- Additive Manufacturing
- Aluminum Welding
- Arc Welding
- Assembly and Joining
- Automation and Robotics
- Bending and Forming
- Consumables
- Cutting and Weld Prep
- Electric Vehicles
- En Español
- Finishing
- Hydroforming
- Laser Cutting
- Laser Welding
- Machining
- Manufacturing Software
- Materials Handling
- Metals/Materials
- Oxyfuel Cutting
- Plasma Cutting
- Power Tools
- Punching and Other Holemaking
- Roll Forming
- Safety
- Sawing
- Shearing
- Shop Management
- Testing and Measuring
- Tube and Pipe Fabrication
- Tube and Pipe Production
- Waterjet Cutting
Industry Directory
Webcasts
Podcasts
FAB 40
Advertise
Subscribe
Account Login
Search
Shop strategies for crack-free bending in V-grooved brass sheet metal
Forming against the grain can help prevent brass from cracking
- By Steve Benson
- July 24, 2023
- Article
- Bending and Forming
Question: I’m V-grooving and bending some C385 brass sheet, and it’s cracking. I’m bending parallel to the grain on a large sheet. I’ve done this before and haven’t had this issue. Is there a way to anneal the metal in order to complete this job?
Answer: Yes, you can anneal C385 brass sheet. But before we get to specifics, we’ll review a few basics and how they relate to your application’s material as well as other material types.
First, you say you’re grooving and bending parallel to the grain direction, and that your bends are cracking on the outside of the bend radius. In truth, I’m surprised you haven’t had issues with cracking before. The easiest way to succeed is to bend the parts across the grain—and here is why.
Grain Structure in Sheet Metal
Like most metals, brass undergoes a process called grain structure formation during rolling. The grain structure refers to the arrangement of individual crystalline grains within the material. When brass is rolled into a sheet, the grains elongate and align in the direction of the material’s deformation, the direction of roll. This alignment creates a preferred orientation, commonly referred to as the grain (see Figure 1).
The grain direction in C385 brass sheet can affect its mechanical properties and behavior. For example, the sheet may exhibit different strengths, ductility, or machinability in the direction parallel to the grains compared to processing perpendicular to the grains.
It’s important to consider the grain direction when working with materials that have a grain, especially when forming. When you bend parallel to the grain, it is much easier for those grains to be pulled apart as they’re stretched around the outside surface of the bend.
If the material you are forming has grain structure (that is, the material is anisotropic), that structure will affect the bend angle when bending with or against the grain, as shown in Figure 2. This knowledge is essential when considering its behavior during any bending and forming process.
Anisotropic materials have properties that vary depending on the direction of the grain relative to processing. In the case of C385 brass sheet, the mechanical and physical properties such as strength and ductility depend on the bend’s orientation with respect to the grain direction.
The grain boundaries can affect the material’s response to applied forces. Therefore, when using C385 brass sheet or any other anisotropic material, it’s essential to consider the grain direction and its potential impact on the manufacturing processes.
Along with grain direction, don’t forget about the material thickness. The thicker the material, the more likely it is to exhibit cracking at the bend.
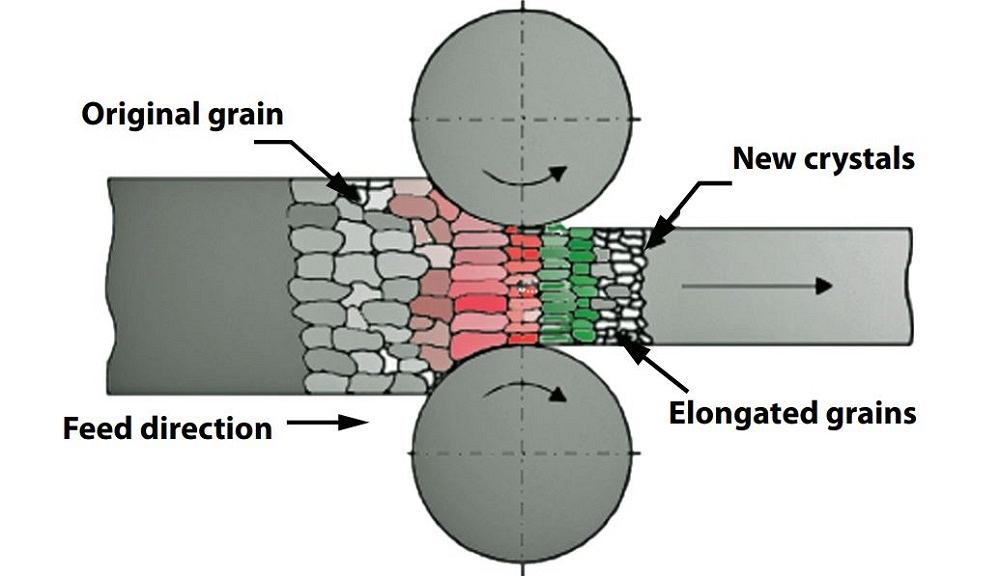
FIGURE 1. When brass is rolled into a sheet, the grains elongate and align in the direction of the material’s deformation.
How to Prevent Cracking
Before anything else, consult with your material supplier about best practices for working with C385 brass sheet or (for that matter) any other metals you’re having issues with. Also, try orienting the bend direction so it’s perpendicular to the grain direction. This can help minimize the stress concentration along the grain boundaries and reduce the risk of cracking.
If you must form C385 brass sheet with the grain, you can try several techniques to avoid cracking. As you mentioned, you can anneal the brass sheet before you form it. Annealing involves heating the material to a specific temperature and then cooling it slowly. This relieves internal stresses and softens the material, making it more ductile and less prone to cracking during forming.
Annealing isn’t your only alternative, though. For instance, be sure to check your tooling. Ensure your forming tools have smooth surfaces and are designed appropriately for working with brass. Also, using a suitable lubricant during forming can help reduce friction and prevent cracking.
Also, avoid applying excessive force. Instead, use a gradual, progressive forming approach. This allows the material to deform more uniformly and reduces the likelihood of cracking.
Don’t bend any sharper on the inside of the bend than necessary. The smaller the inside bend radius, the greater the strain on the bend’s outside surface. However, with the grooving process involved, you are no doubt bending the material very sharp and adding excess stress to the outside of the bend.
If you’re working with complex or critical forms, experiment and practice with scrap or test pieces before working on the final product. This allows you to refine your forming techniques and minimize the chances of cracking.
You also could consider prebending the material slightly before the final bend. This involves bending the sheet to a smaller angle than the one desired, releasing the pressure, and then finishing the bend. Prebending helps to elongate the material’s outer fibers and reduce the likelihood of cracking during the final bend.
Annealing Technique
In certain cases, applying heat to the sheet before bending can increase its ductility and make it less prone to cracking. Heat can be applied using a torch or heating element. That said, remember to carefully evaluate the specific requirements and constraints of your bending application and choose the techniques that are most suitable. If you wish to anneal your C385 brass, consider the following to achieve the best results:
- Clean the brass sheet - Before annealing, ensure that the brass sheet is free from any contaminants, such as oils, dirt, or oxidation. Use a suitable solvent or degreasing agent, followed by a rinsing and thorough drying.
- Heat to the correct temperature - The annealing temperature for C385 brass is typically in the range of 1,112 degrees F to 1,292 degrees F. It’s essential to use a reliable and accurate temperature measurement device, such as a pyrometer, to monitor the temperature when heating. Heat the brass sheet evenly and slowly to the desired annealing temperature.
- Maintain the temperature - Once the brass sheet reaches the annealing temperature, hold it at that temperature for an appropriate amount of time to allow for complete transformation and stress relief. The duration can vary depending on the thickness of the sheet, but typically ranges from 15 minutes to an hour. This may be difficult to do without an appropriate oven to maintain the temperature.
- Control the cooling - After the desired annealing time and the forming, carefully control the cooling process to avoid thermal shock and sudden temperature changes that can lead to distortion or cracking. Slow cooling is generally recommended to allow the material to reach room temperature gradually in the oven, by turning it off and letting the brass sheet cool inside. Alternatively, you can place it on a thermally insulating material, such as ceramic fiber.
- Inspect your results - Once the brass sheet has cooled to room temperature, you can inspect it for the desired annealing results. Annealing aims to reduce hardness, improve ductility, and relieve internal stresses. The brass should appear softer and more malleable compared to its preannealed state. It’s a good idea to perform mechanical tests or bend a test piece to ensure you’ve achieved the desired properties.
Please note, these best practices provide general guidelines for annealing C385 brass sheet. However, specific parameters, such as heating time and cooling rate, may vary depending on the thickness and the specific requirements of your brass sheet.
Again, consulting with brass sheet suppliers or experts in the field can provide more precise recommendations based on your specific application. Remember that conditions will vary depending on the thickness, grain direction, and your bend requirements. Regardless, by following these guidelines and considering your specific application requirements, you can enhance your chances of successful bending while minimizing the risk of cracking.
About the Author
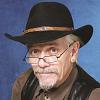
Steve Benson
2952 Doaks Ferry Road N.W.
Salem, OR 97301-4468
503-399-7514
Related Companies
subscribe now
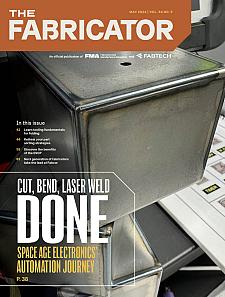
The Fabricator is North America's leading magazine for the metal forming and fabricating industry. The magazine delivers the news, technical articles, and case histories that enable fabricators to do their jobs more efficiently. The Fabricator has served the industry since 1970.
start your free subscription- Stay connected from anywhere
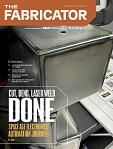
Easily access valuable industry resources now with full access to the digital edition of The Fabricator.
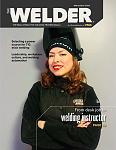
Easily access valuable industry resources now with full access to the digital edition of The Welder.
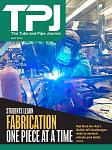
Easily access valuable industry resources now with full access to the digital edition of The Tube and Pipe Journal.
- Podcasting
- Podcast:
- The Fabricator Podcast
- Published:
- 04/16/2024
- Running Time:
- 63:29
In this episode of The Fabricator Podcast, Caleb Chamberlain, co-founder and CEO of OSH Cut, discusses his company’s...
- Trending Articles
Tips for creating sheet metal tubes with perforations
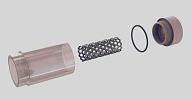
JM Steel triples capacity for solar energy projects at Pennsylvania facility
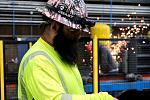
Are two heads better than one in fiber laser cutting?
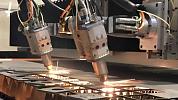
Supporting the metal fabricating industry through FMA
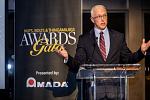
Omco Solar opens second Alabama manufacturing facility
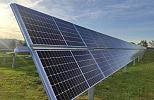
- Industry Events
16th Annual Safety Conference
- April 30 - May 1, 2024
- Elgin,
Pipe and Tube Conference
- May 21 - 22, 2024
- Omaha, NE
World-Class Roll Forming Workshop
- June 5 - 6, 2024
- Louisville, KY
Advanced Laser Application Workshop
- June 25 - 27, 2024
- Novi, MI